概念與範疇
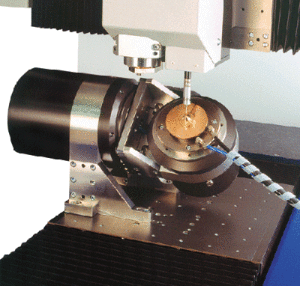
通常,按加工精度劃分,機械加工可分為一般加工、精密加工、超精密加工三個階段。目前,精密加工是指加工精度為1~0.1µm,表面粗糙度為Ra0.1~0.01µm的加工技術,但這個界限是隨著加工技術的進步不斷變化的,今天的精密加工可能就是明天的一般加工。
精密加工所要解決的問題,一是加工精度,包括形位公差、尺寸精度及表面狀況;二是加工效率,有些加工可以取得較好的加工精度,卻難以取得高的加工效率。
分類
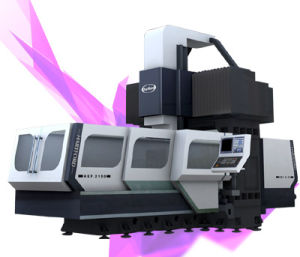
1、傳統的精密加工方法有砂帶磨削、精密切削、珩磨、精密研磨與拋光等。
a.砂帶磨削是用粘有磨料的混紡布為磨具對工件進行加工,屬於塗附磨具磨削加工的範疇,有生產率高、表面質量好、使用範圍廣等特點。
b.精密切削,也稱金剛石刀具切削(SPDT),用高精密的工具機和單晶金剛石刀具進行切削加工,主要用於銅、鋁等不宜磨削加工的軟金屬的精密加工,如計算機用的磁鼓、磁碟及大功率雷射用的金屬反光鏡等,比一般切削加工精度要高1~2個等級。
c.珩磨,用油石砂條組成的珩磨頭,在一定壓力下沿工件表面往復運動,加工後的表面粗糙度可達Ra0.4~0.1µ;m,最好可到Ra0.025µ;m,主要用來加工鑄鐵及鋼,不宜用來加工硬度小、韌性好的有色金屬。
d.精密研磨與拋光通過介於工件和工具間的磨料及加工液,工件及研具作相互機械摩擦,使工件達到所要求的尺寸與精度的加工方法。精密研磨與拋光對於金屬和非金屬工件都可以達到其他加工方法所不能達到的精度和表面粗糙度,被研磨表面的粗糙度Ra≤0.025µ;m加工變質層很小,表面質量高,精密研磨的設備簡單,主要用於平面、圓柱面、齒輪齒面及有密封要求的配偶件的加工,也可用於量規、量塊、噴油嘴、閥體與閥芯的光整加工。
e.拋光是利用機械、化學、電化學的方法對工件表面進行的一種微細加工,主要用來降低工件表面粗糙度,常用的方法有:手工或機械拋光、超音波拋光、化學拋光、電化學拋光及電化學機械複合加工等。手工或機械拋光加工後工件表面粗糙度Ra≤0.05µ;m,可用於平面、柱面、曲面及模具型腔的拋光加工。超音波拋光加工精度0.01~0.02µ;m,表面粗糙度Ra0.1µ;m。化學拋光加工的表面粗糙度一般為Ra≤0.2µ;m。電化學拋光可提高到Ra0.1~0.08µm。
2、精密加工包括微細加工和超微細加工、光整加工等加工技術。
微細加工技術是指製造微小尺寸零件的加工技術;
超微細加工技術是指製造超微小尺寸零件的加工技術,它們是針對積體電路的製造要求而提出的,由於尺寸微小,其精度是用切除尺寸的絕對值來表示,而不是用所加工尺寸與尺寸誤差的比值來表示。
光整加工一般是指降低表面粗糙度和提高表面層力學機械性質的加工方法,不著重於提高加工精度,其典型加工方法有珩磨、研磨、超精加工及無屑加工等。實際上,這些加工方法不僅能提高表面質量,而且可以提高加工精度。精整加工是近年來提出的一個新的名詞術語,它與光整加工是對應的,是指既要降低表面粗糙度和提高表面層力學機械性質,又要提高加工精度(包括尺寸、形狀、位置精度)的加工方法。
3、超精密加工就是在超精密工具機設備上,利用零件與刀具之間產生的具有嚴格約束的相對運動,對材料進行微量切削,以獲得極高形狀精度和表面光潔度的加工過程。當前的超精密加工是指被加工零件的尺寸精度高於0.1μm,表面粗糙度Ra小於0.025μm,以及所用工具機定位精度的解析度和重複性高於0.01μm的加工技術,亦稱之為亞微米級加工技術,且正在向納米級加工技術發展。
現狀與套用
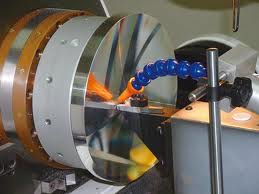
1.精密成型加工的發展現狀與套用
精密鑄造成形、精密模壓成形、塑性加工、薄板精密成形技術在工業已開發國家受到高度重視,並投入大量資金優先發展。70年代美國空軍主持制訂“鍛造工藝現代化計畫”,目的是使鍛造這一重要工藝實現現代化,更多地使用CAD/CAM,使新鍛件的製造周期減少75%。1992年,美國國防部提出了“軍用關鍵技術清單”,其中包含了等壓成型工藝、數控計算機控制鏇壓、塑變和剪下成形機械、超塑成型/擴散連線工藝、液壓延伸成型工藝等精密塑性成型工藝。國外近年來還發展了以航空航天產品為套用對象的“大型模鍛件的鍛造及葉片精鍛工藝”、“快速凝固粉末層壓工藝”、“大型複雜結構件強力鏇壓成型工藝”、“難變形材料超塑成形工藝”、“先進材料(如金屬基複合材料、陶瓷基複合材料等)成形工藝”等。我國的超塑成形技術在航天航空及機械行業也有套用,如航天工業中的衛星部件、飛彈和火箭氣瓶等,採用超塑成形法製造偵察衛星的欽合金回收艙。與此同時,還基本上掌握了鋅、銅、鋁、欽合金的超塑成形工藝,最小成形厚度可達0.3mm,形狀也較複雜。此外,國外已廣泛套用精密模壓成形技術製造武器。常用的精密模壓成形技術,如閉塞式鍛造、採用分流原理的精密成形及等溫成形等國外已用於軍工生產。目前,精密模壓技術在我國套用還較少,精度也較差,國外精度為±0.05—0.10mm,我國為±0.1—0.25mm。
2.孔加工技術的發展現狀及套用
近年來,汽車、模具零部件、金屬加工大都採用以CNC工具機為中心的生產形態,進行孔加工時,也大都採用加工中心、CNC電加工工具機等先進設備,高速、高精度鑽削加工已提上議事日程。無論哪個領域的孔加工,實現高精度和高速化都是取得用戶訂單的重要競爭手段。
近年來,隨著高速銑削的出現,以銑削刀具為中心的切削加工正在進入高速高精度化的加工時期。在孔加工作業中,目前仍大量使用高速鋼麻花鑽,但各企業之間在孔加工精度和加工效率方面已逐漸拉開了差距。高速切削鑽頭的材料以陶瓷塗層硬質合金為主,如MAZAK公司和森精機製作所在加工鑄鐵時,即採用了陶瓷塗層鑽頭。在加工鋁合金等有色材料時,可採用金剛石塗層硬質合金鑽頭、DLC塗層硬質合金鑽頭或帶金剛石燒結體刀齒的鑽頭。高速高精度孔加工除採用CNC切削方式對孔進行精密加工外,還可採用鏜削和鉸削等方式對孔進行高精度加工。隨著加工中心主軸的高速化,已可採用鏜削工具對孔進行高速精密加工。
隨著IT相關產業的發展,近年來,光學和電子工業所用裝置的零部件產品的需求急速增長,這種增長刺激了微細形狀及高精度加工技術的迅速發展。其中,微細孔加工技術的開發套用尤其引人注目。微細孔加工早已在印刷電路板等加工中加以套用,包括鋼材在內的多種被加工材料,均可用鑽頭進行小直徑加工。目前,小直徑孔加工中,利用鑽頭切削的直徑最小可至φ50μm左右。小於φ50μm的孔則多採用電加工來完成。為了抑制毛刺的產生,許多研究者提出可採用超音波振動切削的方式。目前,正在探索一種套用範圍廣而且工藝合理的超音波振動切削模式,其中包括研究工具機的適應特性等內容。隨著這些問題的順利解決,今後可望更好地實現直徑更小的微小深孔加工,加工精度會更高。
3.特種熱處理的發展現狀與套用
特種熱處理工藝是國防工業系統關鍵製造技術之一。真空熱處理以其特有的無污梁、無氧化、工件變形小和適用範圍廣等優點,廣泛用於航空航天結構件處理,如齒輪結構件表面滲碳或滲氮,飛彈和太空飛行器各種合金或鋼件的去應力、增強或增韌處理等。典型結構如:儀表零件、傳動結構、燃料貯箱、發動機殼體等;美國熱處理爐約有50%以上為真空熱處理爐。真空熱處理爐已廣泛採用了計算機控制,目前已發展到真空化學熱處理和真空氣淬熱處理,包括高壓真空氣淬、高流率真空氣淬和高壓高流率真空氣淬技術等。另外,雷射熱處理技術在國外已廣泛用於航空、航天、電子、儀表等領域,如各種複雜表面件、微型構件、需局部強化處理構件、微型電子器件、大規模積體電路的生產和修補、精密光學元件、精密測量元件等。
4.數控電火花加工新工藝的套用
a.標準化夾具
數控電火花加工為保證極高的重複定位精度且不降低加工效率,採用快速裝夾的標準化夾具。標準化夾具,是一種快速精密定位的工藝方法,它的使用大大減少了數控電火花加工過程中的裝夾定位時間,有效地提升了企業的競爭力。目前有瑞士的EROWA和瑞典的3R裝置可實現快速精密定位。
b.混粉加工方法
在放電加工液內混入粉末添加劑,以高速獲得光澤面的加工方法稱之為混粉加工。該方法主要套用於複雜模具型腔,尤其是不便於進行拋光作業的複雜曲面的精密加工。可降低零件表面粗糙度值,省去手工拋光工序,提高零件的使用性能(如壽命、耐磨性、耐腐蝕性、脫模性等)。混粉加工技術的發展,使精密型腔模具鏡面加工成為現實。
c.搖動加工方法
電火花加工複雜型腔時,可根據被加工部位的搖動圖形、搖動量的形狀及精度的要求,選用電極不斷搖動的方法,獲得側面與底面更均勻的表面粗糙度,更容易控制加工尺寸,實現小間隙放電條件下的穩定加工。
d.多軸聯動加工方法
近年來,隨著模具工業和IT技術的發展,多軸聯動電火花加工技術取得了長足的進步。模具企業採用多軸聯動的方法來提高加工性能,如清角部位在加工可行的情況下採用X、Y、Z三軸聯動的方法,即斜向加工,避免了因加工部位面積小而發生放電不穩定的現象。模具潛伏式膠口的加工通過對電極斜度裝夾定位的設計,也可進行斜向多軸聯動加工。採用多軸迴轉系統與多種直線運動協調組合成多種複合運動方式,可適應不同種類工件的加工要求,擴大數控電火花加工的加工範圍,提高其在精密加工方面的比較優勢和技術效益。
發展趨勢
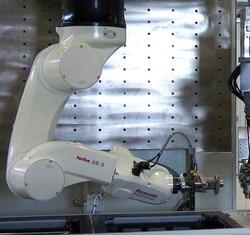
面向21世紀的精密加工技術的發展趨勢體現在以下幾個方面:
a.精密化
精密加工的核心主要體現在對尺寸精度、仿形精度、表面質量的要求。當前精密電火花加工的精度已有全面提高,尺寸加工要求可達±2-3μm、底面拐角R值可小於0.03mm,最佳加工表面粗糙度可低於Ra0.3μm。通過採用一系列先進加工技術和工藝方法,可達到鏡面加工效果且能夠成功地完成微型接外掛程式、IC塑封、手機、CD盒等高精密模具部位的電火花加工。
b.智慧型化
智慧型化是而向21世紀製造技術的發展趨勢之一。智慧型製造技術(IMT)是將人工智慧融入製造過程的各個環節,通過模擬人類專家的智慧型活動,取代或延伸製造系統中的部分腦力勞動,在製造過程中系統能自動監測其運行狀態,在受到外界干擾或內部激勵能自動調整其參數,以達到最佳狀態和具備自組織能力。新型數控電火花工具機採用了模糊控制技術和專家系統智慧型控制技術。模糊控制技術是由計算機監測來判定電火花加工間隙的狀態,在保持穩定電弧的範圍內自動選擇使加工效率達到最高的加工條件;自動監控加工過程,實現最穩定的加工過程的控制技術。採用人機對話方式的專家系統,根據加工的條件、要求,合理輸入設定值後便能自動創建加工程式,選用最佳加工條件組合來進行加工。線上自動監測、調整加工過程,實現加工過程的最最佳化控制。專家系統在檢測加工條件時,只要輸入加工形狀、電極與工件材質、加工位置、目標粗糙度值、電極縮放量、搖動方式、錐度值等指標,就可自動推算並配置最佳加工條件。專家系統智慧型技術的套用使工具機操作更容易,對操作人員的技術水平要求更低。
c.自動化
自動化技術的成功套用,不但提高了效率,保證了產品質量,還可以代替人去完成危險場合的工作。對於批量較大的生產自動化,可通過工具機自動化改裝、套用自動工具機、專用組合工具機、自動生產線來完成。小批量生產自動化可通過NC,MC,CAM,FMS,CIM,IMS等來完成。在末來的自動化技術實施過程中,將更加重視人在自動化系統中的作用。同時自動化開始面向中小型企業,以經濟實用為出發點,滿足不斷發展的產品多樣化和個性化需要。數控電火花工具機具備的自動測量找正、自動定位、多工件的連續加工等功能已較好地發揮了它的自動化性能。自動操作過程不需人工干預,可以提高加工精度、效率。目前最先進的數控電火花工具機在配有電極庫和標準電極夾具的情況下,只要在加工前將電極裝入刀庫,編制好加工程式,整個電火花加工過程便能日以赴繼地自動運轉,幾乎無需人工操作。工具機的自動化運轉降低了操作人員的勞動強度、提高生產效率。
d.高效化
現代加工的要求為數控電火花加工技術提供了最佳的加工模式,即要求在保證加工精度的前提下大幅提高粗、精加工效率。如手機外殼、家電製品、電器用品、電子儀表等領域,都要求減少輔助時間(如編程時間、電極與工件定位時間等),同時又要降低粗糙度,從原來的Ra0.8μm改進到Ra0.25μm,使放電後不必再進行手工拋光處理。這不但縮短了加工時間且省卻後處理的麻煩,同時提升了模具品質,使用粉末加工設備可達到要求。這就需要增強工具機的自動編程功能,配置電極與工件定位的夾具、裝置。若在大工件的粗加工中選用石墨電極材料也是提高加工效率的好方法。
e.信息化
信息、物質和能源是製造系統的三要素。隨著計算機、自動化與通訊網路技術紅製造系統中的套用,信息的作用越來越重要。產品製造過程中的信息投入,己成為決定產品成本的主要因素。製造過程的實質是對製造過程中各種信息資源的採集、輸入、加工和處理過程,最終形成的產品可看作是信息的物質表現,因此可以把信息看作是一種產業,包括在製造之中。為此一些企業開始利用網路技術、計算機聯網、信息高速公路、衛星傳遞數據等實現異地生產。使生產分散網路化,以適應21世紀高柔性生產的需要。
f.柔性化
隨著科學技術的飛速發展和人民生活水平不斷提高,促使產品更新換代的速度不斷加快,這就要求現代企業必須具備一定的生產柔性來滿足市場多變的需要。所謂柔性,是指一個製造系統適應各種生產條件變化的能力,它與系統方案、人員和設備有關。系統方案的柔性是指加工不同零件的自由度。人員柔性是指操作人員能保證加工任務,完成數量和時間要求的適應能力。設備柔性是指工具機能在短期內適應新零件的加工能力。柔性製造自動化的形式很多,如美國提出的敏捷製造(AM)其主線就是高柔性生產。上海同濟大學張曙教授提出的獨立製造島(AMI)也是高柔性生產模式。
g.集成化
集成的作用是將原來獨立運行的多個單元系統集成一個能協調工作的和功能更強的新系統。集成不是簡單的連線,是經過統一規劃設計,分析原單元系統的作用和相互關係並進行最佳化重組而實現的。集成化的目的是實現製造企業的功能集成,功能集成要藉助現代管理技術、計算機技術、自動化技術和信息技術實現技術集成,同時還要強調人的集成,由於系統中不可能沒有人,系統運行的效果與企業經營思想、運行機制、管理模式都與人有關,在技術上集成的同時,還應強調管理與人的集成。集成化生產將成為面向21世紀占主導的生產方式。
超精密加工
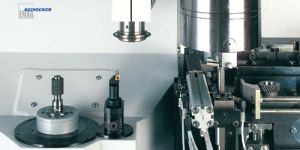
超精密加工是指亞微米級(尺寸誤差為0.3~0.03µm,表面粗糙度為Ra0.03~0.005µm)和納米級(精度誤差為0.03µm,表面粗糙度小於Ra0.005µm)精度的加工。實現這些加工所採取的工藝方法和技術措施,則稱為超精加工技術。加之測量技術、環境保障和材料等問題,人們把這種技術總稱為超精工程。超精密加工主要包括三個領域:超精密切削加工如金剛石刀具的超精密切削,可加工各種鏡面。它已成功地解決了用於雷射核聚變系統和天體望遠鏡的大型拋物面鏡的加工。超精密磨削和研磨加工如高密度硬磁碟的塗層表面加工和大規模積體電路基片的加工。超精密特種加工如大規模積體電路晶片上的圖形是用電子束、離子束刻蝕的方法加工,線寬可達0.1µm。如用掃描隧道電子顯微鏡(STM)加工,線寬可達2~5nm。
a.超精密切削
超精密切削以SPDT技術開始,該技術以空氣軸承主軸、氣動滑板、高剛性、高精度工具、反饋控制和環境溫度控制為支撐,可獲得納米級表面粗糙度。多採用金剛石刀具銑削,廣泛用於銅的平面和非球面光學元件、有機玻璃、塑膠製品(如照相機的塑膠鏡片、隱形眼鏡鏡片等)、陶瓷及複合材料的加工等。未來的發展趨勢是利用鍍膜技術來改善金剛石刀具在加工硬化鋼材時的磨耗。此外,MEMS組件等微小零件的加工需要微小刀具,目前微小刀具的尺寸約可達50~100μm,但如果加工幾何特徵在亞微米甚至納米級,刀具直徑必須再縮小,其發展趨勢是利用納米材料如納米碳管來製作超小刀徑的車刀或銑刀。
b.超精密磨削
超精密磨削是在一般精密磨削基礎上發展起來的一種鏡面磨削方法,其關鍵技術是金剛石砂輪的修整,使磨粒具有微刃性和等高性。超精密磨削的加工對象主要是脆硬的金屬材料、半導體材料、陶瓷、玻璃等。磨削後,被加工表面留下大量極微細的磨削痕跡,殘留高度極小,加上微刃的滑擠、摩擦、拋光作用,可獲得高精度和低表面粗糙度的加工表面,當前超精密磨削能加工出圓度0.01μm、尺寸精度0.1μm和表面粗糙度為Ra0.005μm的圓柱形零件。
c.超精密研磨
超精密研磨包括機械研磨、化學機械研磨、浮動研磨、彈性發射加工以及磁力研磨等加工方法。超精密研磨的關鍵條件是幾乎無振動的研磨運動、精密的溫度控制、潔淨的環境以及細小而均勻的研磨劑。超精密研磨加工出的球面度達0.025μm,表面粗糙度Ra達0.003μm。
d.超精密特種加工
超精密特種加工主要包括雷射束加工、電子束加工、離子束加工、微細電火花加工、精細電解加工及電解研磨、超聲電解加工、超聲電解研磨、超聲電火花等複合加工。雷射、電子束加工可實現打孔、精密切割、成形切割、刻蝕、光刻曝光、加工雷射防偽標誌;離子束加工可實現原子、分子級的切削加工;利用微細放電加工可以實現極微細的金屬材料的去除,可加工微細軸、孔、窄縫平面及曲面;精細電解加工可實現納米級精度,且表面不會產生加工應力,常用於鏡面拋光、鏡面減薄以及一些需要無應力加工的場合。
超精密加工技術在國際上處於領先地位的國家有美國、英國和日本。這些國家的超精密加工技術不僅總體成套水平高,而且商品化的程度也非常高。美國50年代未發展了金剛石刀具的超精密切削技術,稱為“SPDT技術”(SinglePointDia-mondTurning)或“微英寸技術”(1微英寸=0.025μm),並發展了相應的空氣軸承主軸的超精密工具機,用於加工雷射核聚變反射鏡、戰術飛彈及載人飛船用球面、非球面大型零件等。英國克蘭菲爾德技術學院所屬的克蘭菲爾德精密工程研究所(簡稱CUPE)是英國超精密加工技術水平的獨特代表。如CUPE生產的Nanocentre(納米加工中心)既可進行超精密車削,又帶有磨頭,也可進行超精密磨削,加工工件的形狀精度可達0.1μm,表面粗糙度Ra<10nm。日本對超精密加工技術的研究相對於美、英來說起步較晚,但是當今世界上超精密加工技術發展最快的國家。北京工具機研究所是國內進行超精密加工技術研究的主要單位之一,研製出了多種不同類型的超精密工具機、部件和相關的高精度測試儀器等,如精度達0.025μm的精密軸承、JCS—027超精密車床、JCS—031超精密銑床、JCS—035超精密車床、超精密車床數控系統、複印機感光鼓加工工具機、紅外大功率雷射反射鏡、超精密振動-位移測微儀等,達到了國內領先、國際先進水平。哈爾濱工業大學在金剛石超精密切削、金剛石刀具晶體定向和刃磨、金剛石微粉砂輪電解線上修整技術等方面進行了卓有成效的研究。清華大學在積體電路超精密加工設備、磁碟加工及檢測設備、微位移工作檯、超精密砂帶磨削和研拋、金剛石微粉砂輪超精密磨削、非圓截面超精密切削等方面進行了深入研究,並有相應產品問世。我國超精密加工技術與美日相比,還有不小差距,特別是在大型光學和非金屬材料的超精加工方面,在超精加工的效率和自動化技術方面差距尤為明顯。
超精密加工發展趨勢
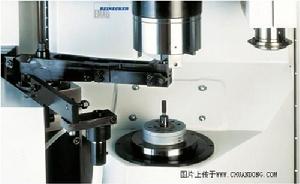
將向高精度、高效率、大型化、微型化、智慧型化、工藝整合化、線上加工檢測一體化、綠色化等方向發展。
a.高精度、高效率。
隨著科學技術的不斷進步,對精度、效率、質量的要求愈來愈高,高精度與高效率成為超精密加工永恆的主題。超精密切削、磨削技術能有效提高加工效率,CMP、EEM技術能夠保證加工精度,而半固著磨粒加工方法及電解磁力研磨、磁流變磨料流加工等複合加工方法由於能兼顧效率與精度的加工方法,成為超精密加工的趨勢。
b.大型化、微型化。
由於航天航空等技術的發展,大型光電子器件要求大型超精密加工設備,如美國研製的加工直徑為2.4~4m的大型光學器件超精密加工工具機。同時隨著微型機械電子、光電信息等領域的發展,超精密加工技術向微型化發展,如微型感測器,微型驅動元件和動力裝置、微型航空太空飛行器件等都需要微型超精密加工設備。
c.智慧型化。
以智慧型化設備降低加工結果對人工經驗的依賴性一直是製造領域追求的目標。加工設備的智慧型化程度直接關係到加工的穩定性與加工效率,這一點在超精密加工中體現更為明顯。
d.工藝整合化。
當今企業間的競爭趨於白熱化,高生產效率越來越成為企業賴以生存的條件。在這樣的背景下,出現了“以磨代研”甚至“以磨代拋”的呼聲。另一方面,使用一台設備完成多種加工(如車削、鑽削、銑削、磨削、光整)的趨勢越來越明顯。
e.線上加工檢測一體化。
由於超精密加工的精度很高,必須發展線上加工檢測一體化技術才能保證產品質量和提高生產率。同時由於加工設備本身的精度有時很難滿足要求,採用線上檢測、工況監控和誤差補償的方法可以提高精度,保證加工質量的要求。
f.綠色化。
磨料加工是超精密加工的主要手段,磨料本身的製造、磨料在加工中的消耗、加工中造成的能源及材料的消耗、以及加工中大量使用的加工液等對環境造成了極大的負擔。我國是磨料、磨具產量及消耗的第一大國,大幅提高磨削加工的綠色化程度已成為當務之急已開發國家以及中國的台灣地區均對半導體生產廠家的廢液、廢氣排量及標準實施嚴格管制,為此,各國研究人員對CMP加工產生的廢液、廢氣回收處理展開了研究。綠色化的超精密加工技術在降低環境負擔的同時,提高了自身的生命力。
發展策略
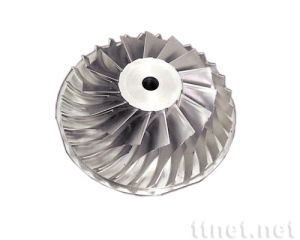
精密和超精密加工經過數十年的努力,日趨成熟,不論是超精密工具機、金剛石工具,還是超精密加工工藝已形成了一整套完整的超精密製造技術系統,為推動機械製造向更高層次發展奠定了基礎,現在正在向納米級精度或毫微米精度邁進,其前景十分令人鼓舞。隨著科學技術的飛速發展和市場競爭日益激烈,越來越多的製造業開始將大量的人力、財力和物力投入先進的製造技術和先進的製造模式的研究和實施策略之中。
1.整合、創新思想的運用
精密、超精密加工技術是發展科技的重要手段,所以受到世界各國的廣泛重視,因此也就不斷地獲得新的成果,但是因為它的要求都處在精度的極限,傳統的、單一的技術往往很難突破,必須綜合地運用信息化技術,通過綜合、分析,加以整合、重組,進一步滿足更高的要求。
精密加工技術是一項系統工程,它集工具機、工具、計量、數控、材料、環境控制等成果於一體,針對不同的加工對象,不同的設計要求,綜合地加以利用。超精密加工技術也都是在其有關的各項技術支撐的條件下,逐步發展起來的,同時又往往取各項技術的嶄新成果來加以充實、提高。超精密加工技術每前進一步,都離不開創新,這是由超精密加工技術所處的位置決定的,因為這門技術始終處在發展的前沿。面對飛速發展的需求就決定了它必須創新。
2.先進的製造模式套用
製造模式是指企業體制、經營、管理、生產組織和技術系統的形態和運作模式。
a.敏捷製造
美國通用汽車公司與里海大學於1988年提出了敏捷製造(AM),AM是在不可預測的持續變化的競爭環境中取得繁榮成長,並具有能對客戶需求的產品和服務驅動市場作出迅速回響的生產模式。AM的特徵是:
①企業間聯作集成。充分發揮各企業的長處,針對限定市場的目標要求共同合作完成任務。
②具有高度的製造柔性。製造柔性是指製造企業對市場要求迅速轉產和能實現產品多品種變批量的快速製造。
③充分發揮人的作用,不斷提高企業職工素質和教育水平,最佳化人機功能分配。
b.虛擬製造
虛擬製造(VM)是國際上提出的新概念。VM與AM聯繫密切。VM的特徵是:當市場新的機遇出現時,組織幾個有關公司聯作,把不同的公司,不同地點的工廠或車間重新組織協調工作。在運行之前必須分析組合是否最優,能否協調運行,以及投產後的效益和風險進行評估,這種聯作公司稱虛擬公司。虛擬公司通過虛擬製造系統運行。因此研究開發虛擬製造技術(VMT)和虛擬製造系統(VMS)意義重大,美國稱AM為2l世紀製造業發展戰略。
c.集成製造
美國哈林頓博士在《計算機和集成製造》一書中提出計算機和集成製造(CIM)的概念。集成製造的核心內容是:製造企業從市場預測、產品設計、加工製造、經營管理克至售後服務是一個不可分割的整體,需要統籌考慮。整個製造過程的實質是信息採集、傳遞和加工過程,最終生產的產品可看作是信息的物質表現。集成是CIM的核心,這種集成不僅是物的集成,更主要的是以信息集成為特徵的技術集成和功能集成,計算機是集成的工具,計算機和輔助各單元技術是集成的基礎,信息交換是橋樑,信息共享是關鍵。集成的目的在於製造企業組織結構和運行方式的合理化和最最佳化,以提高今業對市場變化的動態回響速度,並追求最高整體效益和長期效益。
d.智慧型製造
智慧型製造(IM)是美國出版研究IM和IMS書籍中首先提出的。它的特徵是:在製造工業的各個環節的高度柔性與高度集成的方式,通過計算機和模擬人類專家的智慧型活動,進行分析、判斷、推理、構思和決策,旨在取代或延伸製造環境中人的部分腦力勞動,並對人類專家的製造智慧型進行收集、存儲、完善、共享、繼承與發展。製造智慧型的目的是:通過集成知識工程、製造軟體系統、機器人視覺和機器人控制對製造工人的技能與人類專家知識進行建模,以使智慧型機器能夠在沒有人干預的情況下進行小批量生產。
e.綠色製造
綠色製造又稱環境意識製造和面向環境的製造等。即綜合考慮環境影響和資源消耗的現代製造模式。其目標是使得產品從設計、製造、包裝、運輸、使用到報廢處理的全生命周期中,廢棄物和有害排放物最小,對環境的負面影響最小,對健康無害,資源利用率最高,使企業經濟效益和社會效益更高。