讀法
在金屬材料加工、金屬熱處理等學術領域和行業內均讀音:zhàn。淬火應該讀(zhànhuǒ)“蘸火”是淬火工藝的行業術語,起源於工藝處理的方法,因為淬火就是把加熱到一定程度的熱工件蘸一下介質,以達到要求,過去工匠們形象的稱謂淬火為蘸火,淬火工藝套用很廣,讀法也隨之流傳開來。但辭海中並未有說明,只提有淬火(cuìhuǒ)。淬火要求溫度均勻。目的
淬火的目的是使過冷奧氏體進行馬氏體或貝氏體轉變,得到馬氏體或貝氏體組織,然後配合以不同溫度的回火,以大幅提高鋼的強度、硬度、耐磨性、疲勞強度以及韌性等,從而滿足各種機械零件和工具的不同使用要求。也可以通過淬火滿足某些特種鋼材的鐵磁性、耐蝕性等特殊的物理、化學性能。工藝
將金屬工件加熱到某一適當溫度並保持一段時間,隨即浸入淬冷介質中快速冷卻的金屬熱處理工藝。常用的淬冷介質有鹽水、水、礦物油、空氣等。淬火可以提高金屬工件的硬度及耐磨性,因而廣泛用於各種工、模、量具及要求表面耐磨的零件(如齒輪、軋輥、滲碳零件等)。通過淬火與不同溫度的回火配合,可以大幅度提高金屬的強度、韌性及疲勞強度,並可獲得這些性能之間的配合(綜合機械性能)以滿足不同的使用要求。另外淬火還可使一些特殊性能的鋼獲得一定的物理化學性能,如淬火使永磁鋼增強其鐵磁性、不鏽鋼提高其耐蝕性等。淬火工藝主要用於鋼件。常用的鋼在加熱到臨界溫度以上時,原有在室溫下的組織將全部或大部轉變為奧氏體。隨後將鋼浸入水或油中快速冷卻,奧氏體即轉變為馬氏體。與鋼中其他組織相比,馬氏體硬度最高。淬火時的快速冷卻會使工件內部產生內應力,當其大到一定程度時工件便會發生扭曲變形甚至開裂。為此必須選擇合適的冷卻方法。根據冷卻方法,淬火工藝分為單液淬火、雙介質淬火、馬氏體分級淬火和貝氏體等溫淬火4類。工件硬度
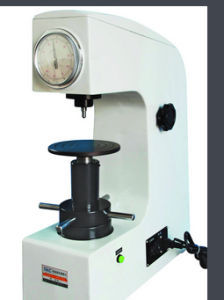
在焊接中碳鋼和某些合金鋼時,熱影響區中可能發生淬火現象而變硬,易形成冷裂紋,這是在焊接過程中要設法防止的。
由於淬火後金屬硬而脆,產生的表面殘餘應力會造成冷裂紋,回火可作為在不影響硬度的基礎上,消除冷裂紋的手段之一。
淬火對厚度、直徑較小的零件使用比較合適,對於過大的零件,淬火深度不夠,滲碳也存在同樣問題,此時應考慮在鋼材中加入鉻等合金來增加強度。
淬火是鋼鐵材料強化的基本手段之一。鋼中馬氏體是鐵基固溶體組織中最硬的相(表1),故鋼件淬火可以獲得高硬度、高強度。但是,馬氏體的脆性很大,加之淬火後鋼件內部有較大的淬火內應力,因而不宜直接套用,必須進行回火。
套用
淬火工藝在現代機械製造工業得到廣泛的套用。機械中重要零件,尤其在汽車、飛機、火箭中套用的鋼件幾乎都經過淬火處理。為滿足各種零件千差萬別的技術要求,發展了各種淬火工藝。如,按接受處理的部位,有整體、局部淬火和表面淬火;按加熱時相變是否完全,有完全淬火和不完全淬火(對於亞共析鋼,該法又稱亞臨界淬火);按冷卻時相變的內容,有分級淬火,等溫淬火和欠速淬火等。工藝過程
包括加熱、保溫、冷卻3個階段。下面以鋼的淬火為例,介紹上述三個階段工藝參數選擇的原則。淬火加熱溫度
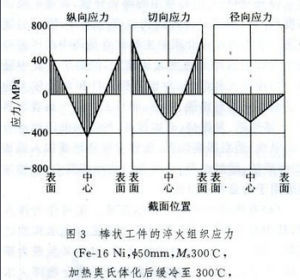
實際生產中,加熱溫度的選擇要根據具體情況加以調整。如亞共析鋼中碳含量為下限,當裝爐量較多,欲增加零件淬硬層深度等時可選用溫度上限;若工件形狀複雜,變形要求嚴格等要採用溫度下限。
淬火保溫
淬火保溫時間由設備加熱方式、零件尺寸、鋼的成分、裝爐量和設備功率等多種因素確定。對整體淬火而言,保溫的目的是使工件內部溫度均勻趨於一致。對各類淬火,其保溫時間最終取決於在要求淬火的區域獲得良好的淬火加熱組織。加熱與保溫是影響淬火質量的重要環節,奧氏體化獲得的組織狀態直接影響淬火後的性能。-般鋼件奧氏體晶粒控制在5~8級。
淬火冷卻
要使鋼中高溫相——奧氏體在冷卻過程中轉變成低溫亞穩相——馬氏體,冷卻速度必須大於鋼的臨界冷卻速度。工件在冷金屬材料加工卻過程中,金屬材料加工表面與心部的冷卻速度有-定差異,如果這種差異足夠大,則可能造成大於臨界冷卻速度部分轉變成馬氏體,而小於臨界冷卻速度的心部不能轉變成馬氏體的情況。為保證整個截面上都轉變為馬氏體需要選用冷卻能力足夠強的淬火介質,以保證工件心部有足夠高的冷卻速度。但是冷卻速度大,工件內部由於熱脹冷縮不均勻造成內應力,可能使工件變形或開裂。因而要考慮上述兩種矛盾因素,合理選擇淬火介質和冷卻方式。冷卻階段不僅零件獲得合理的組織,達到所需要的性能,而且要保持零件的尺寸和形狀精度,是淬火工藝過程的關鍵環節。
方式
單介質淬火
工件在一種介質中冷卻,如水淬、油淬。優點是操作簡單,易於實現機械化,套用廣泛。缺點是在水中淬火應力大,工件容易變形開裂;在油中淬火,冷卻速度小,淬透直徑小,大型工件不易淬透。雙介質淬火
工件先在較強冷卻能力介質中冷卻到300℃左右,再在一種冷卻能力較弱的介質中冷卻,如:先水淬後油淬,可有效減少馬氏體轉變的內應力,減小工件變形開裂的傾向,可用於形狀複雜、截面不均勻的工件淬火。雙液淬火的缺點是難以掌握雙液轉換的時刻,轉換過早容易淬不硬,轉換過遲又容易淬裂。為了克服這一缺點,發展了分級淬火法。分級淬火
工件在低溫鹽浴或鹼浴爐中淬火,鹽浴或鹼浴的溫度在Ms點附近,工件在這一溫度停留2min~5min,然後取出空冷,這種冷卻方式叫分級淬火。分級冷卻的目的,是為了使工件內外溫度較為均勻,同時進行馬氏體轉變,可以大大減小淬火應力,防止變形開裂。分級溫度以前都定在略高於Ms點,工件內外溫度均勻以後進入馬氏體區。改進為在略低於Ms點的溫度分級。實踐表明,在Ms點以下分級的效果更好。例如,高碳鋼模具在160℃的鹼浴中分級淬火,既能淬硬,變形又小,所以套用很廣泛。等溫淬火
工件在等溫鹽浴中淬火,鹽浴溫度在貝氏體區的下部(稍高於Ms),工件等溫停留較長時間,直到貝氏體轉變結束,取出空冷。等溫淬火用於中碳以上的鋼,目的是為了獲得下貝氏體,以提高強度、硬度、韌性和耐磨性。低碳鋼一般不採用等溫淬火。表面淬火
表面淬火是將鋼件的表面層淬透到一定的深度,而心部分仍保持未淬火狀態的一種局部淬火的方法。表面淬火時通過快速加熱,使剛件表面很快到淬火的溫度,在熱量來不及穿到工件心部就立即冷卻,實現局部淬火。感應淬火
感應加熱就是利用電磁感應在工件內產生渦流而將工件進行加熱。鋼鐵整體熱處理大致有退火、正火、淬火和回火四種基本工藝。退火
將工件加熱到適當溫度,根據材料和工件尺寸採用不同的保溫時間,然後進行緩慢冷卻(冷卻速度最慢)目的是使金屬內部組織達到或接近平衡狀態,獲得良好的工藝性能和使用性能,或者為進一步淬火作組織準備。正火
將工件加熱到適宜的溫度後在空氣中冷卻,正火的效果同退火相似,只是得到的組織更細,常用於改善材料的切削性能,也有時用於對一些要求不高的零件作為最終熱處理。回火
為了降低鋼件的脆性,將淬火後的鋼件在高於室溫而低於710℃的某一適當溫度進行長時間的保溫,再進行冷卻,這種工藝稱為回火。淬火
工件加熱奧氏體化後以適當方式冷卻獲得馬氏體或貝氏體組織的熱處理工藝。最常見的有水冷淬火、油冷淬火、空冷淬火等。退火、正火、淬火、回火是整體熱處理中的“四把火”,其中的淬火與回火關係密切,常常配合使用,缺一不可。淬火冷卻、淬冷
工件淬火周期中的冷卻部分。局部淬火
僅對工件需要硬化的局部進行的淬火。氣冷淬火
專指在真空中加熱和在高速循環的負壓、常壓或高壓的中性和惰性氣體中進行的淬火冷卻。表面淬火僅對工件表層進行的淬火,其中包括感應淬火、接觸電阻加熱淬火、火焰淬火、雷射淬火、電子束淬火等。風冷淬火
以強迫流動的空氣或壓縮空氣作為冷卻介質的淬火冷卻。鹽水淬火
以鹽類的水溶液作為冷卻介質的淬火冷卻。有機聚合物水溶液淬火
以有機高分子聚合物的水溶液作為冷卻介質的淬火冷卻。噴液淬火
用噴射液流作為冷卻介質的淬火冷卻。噴霧冷卻
工件在水和空氣混合噴射的霧中進行的淬火冷卻。熱浴冷卻
工件在熔鹽、熔鹼、熔融金屬或高溫油等熱浴中進行的淬火冷卻,如鹽浴淬火、鉛浴淬火、鹼浴淬火等。雙介質淬火、雙液淬火
工件加熱奧氏體化後先浸入冷卻能力強的介質,在組織即將發生馬氏體轉變時立即轉入冷卻能力弱的介質中冷卻。加壓淬火、模壓淬火
工件加熱奧氏體化後再特定夾具夾持下進行的淬火冷卻,其目的在於減少淬火冷卻畸變。透淬
工件從表面至心部全部硬化的淬火。貝氏體等溫淬火、等溫淬火
工件加熱奧氏體化後快冷卻到貝氏體轉變溫度區間等溫保持,使奧氏體變成貝氏體的淬火。馬氏體分級淬火、分級淬火
工件加熱奧氏體化後浸入溫度稍高或稍低於M1點的鹼浴或鹽浴中保持適當時間、在工件整體達到介質溫度後取出空冷以獲得馬氏體的淬火。亞溫淬火
亞共析鋼製工件在Ac1-Ac3溫度區間奧氏體化後淬火冷卻,獲得馬氏體及鐵素體組織的淬火。直接淬火
工件滲入碳後直接淬火冷卻的工藝。兩次淬火
工件滲碳冷卻後,先高於Ac3的溫度奧氏體化並淬冷以細化心部組織,隨即在略髙於Ac3的溫度奧氏體化以細化滲層組織的淬火。自冷淬火
工件局部或表層快速加熱奧氏體化後,加熱區的熱量自行向未加熱區傳到,從而使奧氏體化區迅速冷卻的淬火。軋輥感應器
一、確定軋輥淬火感應器內孔直徑工頻感應器內孔直徑D工=D1+25mm,中頻感應器內孔直徑D中=D1+50mm,式中D1為軋輥輥身直徑。工頻、中頻感應器內孔直徑是根據軋輥淬硬層和淬火所需功率確定,軋輥表面與感應器間距過大則功率損失大,過小則對感應器製造、安裝誤差比較敏感,容易引起軋輥表面硬度不均。實際生產中,為了儘量減少軋輥淬火感應器的製造數量,降低生產成本.提高現有感應器的利用率,一個規格的軋輥選用感應器直徑可在±3mm的範圍內浮動。這樣淬火時軋輥與感應器之間的間距就不總是一個常數,熱處理工程師應按照具體的間距值對淬火工藝進行適當調整。相應地改變輸入功率及軋輥淬火進給速率。
二、軋輥淬火感應器選用的紫銅板規格
根據感應器通過的電流、提供的功率及基本的強度校核。採用寬165mm、厚10mm的紫銅板製造感應器本體。紫銅板長度計算式為:
L=(D+10)π-56(mm);
式中:L一紫銅板長度;
D一軋輥輥身直徑(mm);
10mm—銅板厚度(mm);
56mm—導電彎板、雲母片厚度之和(mm);
三、軋輥淬火感應器的冷卻措施
軋輥淬火過程中軋輥表面溫度很高,一般為870~900℃之間,有的軋輥要達到940℃,而且軋輥淬火合理的進給速率很低為0.5~0.7mm/s。淬火一支軋輥至少需要1h。
設備長時間連續工作,軋輥表面的高溫對感應器強度、耐用度都有重大影響。因此必須對軋輥淬火感應器採取冷卻措施。在感應器本體的外圓表面焊上4紫銅冷卻水扁管,內通循環冷卻水,保證生產過程中感應器不變熱升溫。
四、軋輥淬火感應器的絕緣措施
軋輥淬火感應器的絕緣措施必須穩妥,採用足夠厚度的雲母片、電木來絕緣並用2000V電壓做耐壓試驗而不被擊穿。雲母片厚度10mm,電木絕緣套壁厚3mm。電木墊圈厚度為5mm。導電彎板與變壓器的結合面表面粗糙度應達R1.6,需要拋光處理,搬運、安裝過程中避免磕碰,表面禁止有凹坑出現.否則生產中易引起電弧。