鑄造分類
為實現上述工藝過程,必須採用離心鑄造機創造使鑄鏇轉的條件。根據鑄型鏇轉軸在空間位置的不同,常用的有立式離心鑄造機和臥式離心鑄造機兩種類型。
臥式離心鑄造機的鑄型是繞水平軸鏇轉的(圖1-1),它主要用來生產長度大於直徑的套類和管類鑄件。
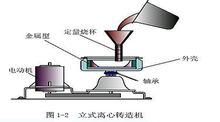
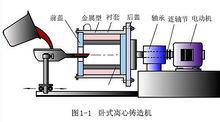
立式離心鑄造機上的鑄型是繞垂直軸鏇轉的(圖1-2),它主要用來生產高度小於直徑的圓環類鑄件,有時也可用此種離心鑄造機澆注異形鑄件。
設計原則
設計離心鑄管機時需要確定幾項參數:澆注時管模的轉速,澆注速度,澆注時間等,並遵循以下四個原則。
1、離心機的下行速度應均勻,保證鑄管壁厚均勻,不同規格的鑄管下行速度不同。
2、澆注不同規格的鑄管時,配用不同容量的扇形包。一套扇形包的傾動機構在一種傾倒速度的條件下,可以傾倒出不同重量的鐵水量。
3、管模的冷卻水量採用閉環控制,根據水的出口和入口溫度控制冷卻水量。
4、離心鑄管模的轉速應保證液態金屬進入管模後立刻成圓筒形,並能得到良好的鑄管內部組織,根據不同規格的鑄管確定不同的轉速。
鑄造特點
臥式離心鑄造的特點是金屬液在離心力的作用下充型和凝固,金屬補縮效果好,鑄件外層組織緻密,非金屬夾雜物少,機械性能好。離心鑄造不用造型、制芯,節省了相關材料及設備投入。鑄造空心鑄件不需澆冒口,金屬利用率可大大提高。因此對某些特定形狀的鑄件來說,離心鑄造是一種節省材料、節省能耗、高效益的工藝,但須特別注意採取有效的安全措施。
臥式離心鑄造可以獲得無縮孔、氣孔、夾渣的鑄件,而且組織細密、機械性能好。當鑄造圓形中空零件時,可以省去型芯。此外,離心鑄造不需要澆注系統,減少了金屬的消耗。但離心鑄造鑄出的筒形零件內孔自由表面粗糙、尺寸誤差大、質量差,有較多氣孔、夾渣,因此需增加加工餘量,而且不適宜澆注容易產生比重偏析的合金及鋁鎂等合金。
發展歷史
1809年,英國人埃爾恰爾特申請了有關臥式離心鑄造和立式離心鑄造的第一個專利。
1849年,英國人安德魯·遜克製作出第一台離心鑄管機,而後生產了長達3.6m、直徑為75mm的離心鑄鐵管。
1857年德國人漢內·貝士麥提出用立式離心鑄造生產輪圈。
1862年英國人惠爾利和鮑韋爾製作出了鑄造輪圈的立式離心鑄造機。
1910年德國人奧托·勃里代發明用移動澆注槽生產金屬型離心鑄管的方法。
1914年巴西人代拉夫得和阿倫斯研究水冷型離心鑄管法成功。1917年美國人莫爾創造了砂型離心鑄管法,1920年開始用於大量生產。
1950年在瑞典開始用塗料金屬型離心鑄造法生產主要用於下水道的小口徑鐵管。
50年代美國離心鑄管公司建立了樹脂砂型離心鑄管法。
30年代以後離心鑄造法逐步推廣套用於生產汽缸套、炮身、鼓輪等鑄件。
在20世紀40年代出現了用離心鑄造法生產雙金屬複合冶金軋輥的工藝。
鑄造工藝
離心機的選擇
如表5-1所示,根據零件尺寸選擇1號臥式三級離心機。
表5-1離心機選擇表
序號 | 最大規格(mm) | 功率(KW) | 最大車速(轉/分) | 形式 |
1 2 3 4 | 300 400 600800 700200 1100600 | 4 10 20 40 | 1150 900 800 700 | 臥式三級 臥式二級 立式二級 立式二級 |
轉速的確定
離心機轉速直接影響鑄件質量,轉速過低使鑄件內圓產生金屬堆積,合金液中的氧化夾雜物不易離出,鑄件產生類渣;轉速過高鑄件容易產生偏析,尤其是鑄件壁厚較大,結晶溫度範圍較寬的合金和合金中成分比重相差較大的元素。如錫、鉛等。通常我們用如下經驗方法來確定。鑄件的直徑小,需要的離心力大,速度靠上限取,反之取較小的轉速。此處鑄件的直徑是指內孔而不是外圓,見表5-2所示。
表5-2離心機轉速表
形式 | 直徑(mm) | 轉速(r/min) |
臥式 | 50~100 100~200 200~400 400~600 | 800~1300 950~1100 750~950 600~750 |
立式 | 600~800 800~1100 | 600~700 500~600 |
零件內徑是130mm,選取轉速950~1100r/min。
澆注溫度
澆注溫度是保證合格鑄件的主要參數之一。本次設計為管狀零件,金屬液充型時遇到阻力較小,又有離心壓力或離心力加強金屬液的充型性,故離心鑄造是的澆注溫度可比重力澆注低5℃~10℃。澆注溫度過高鑄件外圓容易產生氣孔,澆口部位將產生縮孔。澆注溫度過低鑄件外圓產生冷隔、皺皮,鑄件內部產生夾層、壁厚不均、內圓堆積金屬等缺陷。45鋼的熔化溫度1460℃~1467℃,出鋼溫度1560℃~1580℃,澆注溫度1500℃~1550℃。
澆注速度
離心機因採用金屬型模具,冷卻速度較快,採用快速澆注能獲得優質鑄件。由零件
參數得質量為kg。根據表5-3,選取包孔直徑30mm,澆注時間0.5s。
表5-3鋼液澆注重量速度平均值
包孔直徑 | 澆注重量速度 | 備註 |
30 35 40 45 50 | 10 20 27 42 55 | 包孔直徑:mm,澆注重量速度:kg/s |
澆注系統
離心鑄造澆注系統應滿足下列要求:(1)澆注長度長、直徑大的鑄件時,澆注系統應使金屬液能較快的均勻的鋪在鑄型內表上。(2)儘可能減少金屬液飛濺。(3)鑄型內的澆道應能使金屬液順利流入型腔。(4)澆注終了,澆杯和澆注槽內應不留金屬和熔渣,如果有熔渣也應該易於清理。
離心鑄造的澆口沒有手工鑄造的要求嚴格,但澆口位置不當也會使鑄件產生缺陷,突出的缺陷有,縱向壁厚不均,澆口近的地方過厚,遠離澆口的地方很薄,鑄件兩頭產生氧化夾雜物,特別是臥式離心機。因此對直徑小而長的鑄件,儘量將澆口伸進金屬模1/3~1/2處較為理想;直徑大而短的鑄件,澆口伸進金屬模的深度約1/3~1/2處即可。澆口的深度確定之後,還必須調整澆口方向,澆口方向不能朝上順著離心機的鏇轉方向,也不能直頂著離心機的鏇轉方向。合適的澆口方向始終與離心機的鏇轉方向形成一個15°左右的夾角,最大不得超過30°,能有效地保證鑄件質量。本次設計選擇伸進金屬模1/3處。選擇管式澆注杯。
鑄型轉動時間
當金屬液注入金屬模後,要有足夠的時間使液態金屬轉變為固態金屬,整個轉變過程是在離心機鏇轉過程中進行的,不可以停機。若是過早停機,鑄件將會產生凸瘤和不圓現象。最簡單的辦法是觀察鑄件顏色,呈暗紅色時停機、取件。一般轉動時間取10s。
缺陷分析及注意事項
缺陷分析
離心鑄造合金鋼管常出現的缺陷有:充型不完整,表面氣孔,鋼管表層夾砂,裂紋,試壓滲漏,夾渣與渣痕,表面局部針刺。
1、裂紋。鋼管裂紋有縱裂和橫裂。縱裂紋主要是由於合金在凝固時轉速過高,往往伴隨離心機振動較大時出現,生產中縱裂紋出現不多。
實際中橫裂紋較多見,裂紋多靠管子一端,裂紋有時穿透管壁,嚴重者管子一出型就斷開了。
2、試壓滲漏。鋼管在試壓時,在表面出現大面積滲漏,呈現一片片泅水現象,造成報廢。
3、充型不完整。在離心鑄造鋼管中充型不完整常有兩種情況:一種是外型缺澆,管子未達到足夠的長度;另一種是管子壁厚不均,在管子澆注的彼端壁較薄。此缺陷常發生於壁厚在8mm以下的薄壁鋼管中,特別是長徑比大的管子(L/D>15,L管長;D管徑)。
4、表面氣孔。在鋼管表面局部存在氣孔,直徑為0.2mm~2 mm,深0.5mm~2mm,氣孔分布的密度約為2~12個/ cm³ 。呈現出很均勻的一片片的氣孔。
5、鋼管表層夾砂。在鋼管表面局部出現粗糙麻面並稍有凸起,粗糙麻面有清晰的周邊輪廓。嚴重時成為環帶狀夾砂。當去掉粗糙的鋼表層後可見存在其中的薄塗料層即夾砂。夾砂部位經過1mm~2mm的加工即可去除。但它嚴重影響鑄皮質量,如是非加工的鋼管就很可能報廢。這種缺陷多出現於掛塗料的鋼管。
6、夾渣與渣痕。
夾渣,有時管子表面並未見有夾渣,經試壓發現局部小面積滲漏,經剖破檢驗發現在漏水處管壁中存在夾渣,某廠生產鎂罐筒曾出現過此現象。
渣痕,有時在鋼管的內表面存在小凹陷,大小、深淺不等。在薄壁鋼管中凹陷處使壁厚減薄較多。由於鋼管內表面存留較大塊浮渣,待其脫落後便顯出凹陷,所以是渣痕。渣物的密度比鋼液小時在離心力作用下浮到內表面,但由於渣物本身的重力使其沉入鋼液一定深度,從而形成渣痕。
7、表面局部針刺。在靠近鋼管的一端有時會出現針刺。針刺的直徑為0.5mm~1 mm,高為2mm~3mm,每平方厘米內1根左右。這種現象常發生在塗料層較厚的情況下。
注意事項
生產離心鑄件的生產操作控制工藝技術參數在設定時,特別要注意以下八個要點。
(1)對低碳鋼鑄件,澆注時要提高砂箱內的真空度
砂箱應採用雙層箱壁真空室結構,澆注時抽真空能加速熱分解物逸出塗層到型腔外,從而減少模樣熱分解產物的濃度和與鋼水的接觸時間,降低或避免鑄鋼件出現滲碳、積碳現象。型砂粒度在20/40目時,澆注鑄鋼件時負壓以0.03~0.06MPa為宜。如果負壓度過大,將會引起鑄件粘砂及其它缺陷發生。
(2)選擇適宜的密度進行模樣製作
在保證模樣製作技術要求和鑄件澆注時不出現因模樣質量引起的其他缺陷的前提下,模樣的密度越小、泡沫塑膠質量越少,對減少鑄件的滲碳積碳現象就越好。
選擇含碳量低的泡沫塑膠或預發珠粒製作模樣
(3)選用含碳量低或無碳粘接劑
應採用消失模鑄造模樣專用膠進行模樣的粘接組合,不要使用含碳量高的低質普通膠粘接。在模樣粘接時,在保證膠的粘接溫度及粘接強度的同時,要儘量減少粘接劑用量,從而降低粘接劑的熱分解產物。
(4)採用底注式澆注系統
對低碳鋼鑄件,澆注時應儘可能採用底注式澆注方式,使鋼水充型流動平穩,模樣熱分解產物能順利進入集渣腔或冒口中,從而降低和減少模樣熱分解產物中液相和固相的接觸反應時間,降低和消除增碳機率。低碳鋼鑄件一般不宜使用雨淋式澆注系統,易使鑄件增碳、滲碳、積碳的工況和條件增大,導致鑄件產生嚴重缺陷。
(5)中頻爐熔煉,嚴格控制碳鋼配料計算和實際配料、選料、投料操作
因配料計算是保證熔煉出成份合格的鋼水及含有最少氣體與夾雜而鑄出優質鑄鋼件產品的關鍵所在。而配料、選料、投料的準確與否,是鑄造出產品質量合格與否的根本保證。因此,對回爐廢鋼必須建立嚴格的分檢制度。特別是必須將合金鋼廢料和材質不清楚的廢料挑除,保證熔煉配料材質的成份符合鑄造工藝技術參數的要求,是生產離心鑄件操作控制中的第一要務。
(6)選擇確定合理的澆注系統
在進行澆注系統設計時,要儘可能在澆注過程中具有加速模樣氣化的作用,儘量減少及錯開其熱分解產物中液相與固相接觸和反應的時間,從而減少或避免鑄件的滲碳現象發生。
(7)選擇並確定鑄件適宜的澆注溫度和澆注速度
因相同的鑄件如澆注工藝不同,在相同溫度澆注鋼液時,實際充型溫度是完全不相同的。如澆注溫度提高,澆注速度也提高,將造成模樣熱分解加快而不易完全氣化,使熱分解產物在液相中的含量增加,同時因鋼液與模樣的間隙較小,液相中的熱分解物常被擠出間隙後,被擠到模樣塗料層和金屬液之間,或鋼液流動的冷角、死角,造成接觸面增加,碳濃度增加,滲碳量也將增大。同時特別要注意,如澆注工藝不合理,鋼液澆注溫度過高且澆注速度太快,將會造成冒氣、反噴等生產事故。
(8)在模樣上塗料過程中添加防滲碳材料
在塗料配製過程中加入某些抗增碳的催化劑,如鹼金屬鹽、石灰石粉等,澆注後使塗料層中能分解出足夠量的CO、CO2氣體進行吸碳,從而防止鑄件滲碳;或在塗料中加入氧化劑,促使模樣熱分解後的C、H2氣體轉變為中性氣體,從而減少模樣熱分解後形成的C與H向鑄件內滲入,避免造成鑄件增碳或氫脆現象。