發展歷史
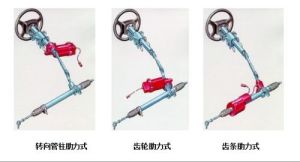
裝配機械式轉向系統的汽車,在泊車和低速行駛時 駕駛員的轉向操縱負擔過於沉重,為了解決這個問題,美國 GM公司在20世紀50年代率先在轎車上採用了液壓助力轉向系統。但是,液壓助力轉向系統無法兼顧車輛低速時的轉向輕便性和高速時的轉向穩定性,因此在1983年日本 Koyo公司推出了具備車速 感應功能的電控液壓助力轉向系統。這種新型的轉向系統可以隨著車速的升高提供逐漸減小的轉向助力,但是結構複雜、造價較高,而且無法克服液壓系統自身所具有的許多缺點,是一種介於液壓助力轉向和電動助力轉向之間的過渡產品。到了1988年,日本 Suzuki公司首先在小型轎車Cervo上配備了Koyo公司研發的轉向柱助力式電動助力轉向系統;1990年,日本 Honda公司也在運動型轎車NSX上採用了自主研發的齒條助力式電動助力轉向系統,從此揭開了電動助力轉向在汽車上套用的歷史。
種類及優缺點
我們常見的助力轉向有 機械液壓助力、 電子液壓助力、 電動助力三種。機械液壓助力
機械液壓助力是我們最常見的一種助力方式,它誕生於1902年,由英國人Frederick W. Lanchester發明,而最早的商品化套用則推遲到了半個世紀之後,1951年克萊斯勒把成熟的液壓轉向助力系統套用在了Imperial車繫上。由於技術成熟可靠,而且成本低廉,得以被廣泛普及。 機械液壓助力系統的主要組成部分有液壓泵、油管、壓力流體控制閥、V型傳動皮帶、儲油罐等等。這種助力方式是將一部分發動機動力輸出轉化成液壓泵壓力,對轉向系統施加輔助作用力,從而使輪胎轉向。
電子液壓助力
由於機械液壓助力需要大幅消耗發動機動力,所以人們在機械液壓助力的基礎上進行改進,開發出了更節省能耗的電子液壓助力轉向系統。 這套系統的轉向油泵不再由發動機直接驅動,而是由電動機來驅動,並且在之前的基礎上加裝了電控系統,使得轉向輔助力的大小不光與轉向角度有關,還與車速相關。機械結構上增加了液壓反應裝置和液流分配閥,新增的電控系統包括車速感測器、電磁閥、轉向ECU等。
電動助力
EPS就是英文Electric Power Steering的縮寫,即電動助力轉向系統。電動助力轉向系統是汽車轉向系統的發展方向。該系統由電動助力機直接提供轉向助力,省去了液壓動力轉向系統所必需的動力轉向油泵、軟管、液壓油、傳送帶和裝於發動機上的皮帶輪,既節省能量,又保護了環境。另外,還具有調整簡單、裝配靈活以及在多種狀況下都能提供轉向助力的特點。正是有了這些優點,電動助力轉向系統作為一種新的轉向技術,將挑戰大家都非常熟知的、已具有50多年歷史的液壓轉向系統。
駕駛員在操縱方向盤進行轉向時,轉矩感測器檢測到轉向盤的轉向以及轉矩的大小,將電壓信號輸送到電子控制單元,電子控制單元根據轉矩感測器檢測到的轉矩電壓信號、轉動方向和車速信號等,向電動機控制器發出指令,使電動機輸出相應大小和方向的轉向助力轉矩,從而產生輔助動力。汽車不轉向時,電子控制單元不向電動機控制器發出指令,電動機不工作。
優勢優點
相比傳統液壓動力轉向系統,電動助力轉向系統具有以下優點:
1、只在轉向時電機才提供助力,可以顯著降低燃油消耗
傳統的液壓助力轉向系統有發動機帶動轉向油泵,不管轉向或者不轉向都要消耗發動機部分動力。而電動助力轉向系統只是在轉向時才由電機提供助力,不轉向時不消耗能量。因此,電動助力轉向系統可以降低車輛的燃油消耗。
與液壓助力轉向系統對比試驗表明:在不轉向時,電動助力轉向可以降低燃油消耗2.5%;在轉向時,可以降低5.5%。
2、轉向助力大小可以通過 軟體調整,能夠兼顧低速時的轉向輕便性和高速時的操縱穩定性,回正性能好。傳統的液壓助力轉向系統所提供的轉向助力大小不能隨車速的提高而改變。這樣就使得車輛雖然在低速時具有良好的轉向輕便性,但是在高速行駛時轉向盤太輕,產生轉向“發飄”的現象,駕駛員缺少顯著的“路感”,降低了高速行駛時的車輛穩定性和駕駛員的安全感。
電動助力轉向系統提供的助力大小可以通過軟體方便的調整。在低速時,電動助力轉向系統可以提供較大的轉向助力,提供車輛的轉向輕便性;隨著車速的提高,電動助力轉向系統提供的轉向助力可以逐漸減小,轉向時駕駛員所需提供的轉向力將逐漸增大,這樣駕駛員就感受到明顯的“路感”,提高了車輛穩定性。
電動助力轉向系統還可以施加一定的附加回正力矩或阻尼力矩,使得低速時轉向盤能夠精確的回到中間位置,而且可以抑制高速回正過程中轉向盤的振盪和超調,兼顧了車輛高、低速時的回正性能。
3、結構緊湊,質量輕,生產線裝配好,易於維護保養
電動助力轉向系統取消了液壓轉向油泵、油缸、液壓 管路、油罐等部件,而且電機及減速機構可以和轉向柱、 轉向器做成一個整體,使得整個轉向系統結構緊湊,質量輕,在生產線上的裝配性好,節省裝配時間,易於維護保養。
4、通過程式的設定,電動助力轉向系統容易與不同車型匹配,可以縮短生產和開發的周期。
由於電動助力轉向系統具有上述多項優點,因此近年來獲得了越來越廣泛的套用。
電動助力轉向系統是在機械式轉向系統的基礎上,加裝了電機及減速機構、轉矩轉角感測器、 車速感測器和ECU 電控單元而成。
工作原理
電助力轉向系統的工作原理如下:首先, 轉矩感測器測出駕駛員施加在 轉向盤上的操縱力矩,車速感測器測出車輛當前的行駛速度,然後將這兩個信號傳遞給ECU;ECU根據內置的控制策略,計算出理想的目標助力力矩,轉化為電流指令給電機;然後,電機產生的助力力矩經減速機構放大作用在機械式轉向系統上,和駕駛員的操縱力矩一起克服轉向阻力矩,實現車輛的轉向。關鍵技術
電動助力轉向系統的關鍵技術主要包括硬體和軟體兩個方面。硬體技術主要涉及 感測器、 電機和 ECU。感測器是整個系統的信號源,其精度和可靠性十分重要。電機是整個系統的執行器,電機性能好壞決定了系統的表現。ECU是整個系統的運算中心,因此ECU的性能和可靠性至關重要。
軟體技術主要包括控制策略和故障診斷與保護程式兩個部分。控制策略用來決定電機的目標電流,並跟蹤該電流,使得電機輸出相應的助力矩。故障診斷與保護程式用來監控系統的運行,並在必要時發出警報和實施一定的保護措施。
工作過程
電動助力轉向系統(EPS)作為傳統液壓系統的替代產品已經進入汽車製造領域。與先前的預測相反,EPS不僅適用於小型汽車,而且某些12V中型汽車也適於安裝電動系統。 EPS系統包含下列組件:轉矩感測器,檢測轉向輪的運動情況和車輛的運動情況;電控單元,根據轉矩感測器提供的信號計算助力的大小; 電機,根據電控單元輸出值生成轉動力;減速齒輪,提高電機產生的轉動力,並將其傳送至轉向機構。其它車輛系統控制算法輸入信息是由汽車CAN匯流排提供的(例如轉向角和汽車速度等等)。 電機驅動還需要其它信息,例如電機轉子位置(電機感測器提供)和相電流(電流感測器提供)。 電機由四個 MOSFET控制。由於微控制器無法直接驅動MOSFET的大型柵電容,因此需要採用驅動IC形式的接口。出於安全考慮,完整的電機控制系統必須實施監控。將電機控制系統集成在PCB上,通常包含一個繼電器,該繼電器可作為主開關使用,在檢測出故障的情況下,斷開電機與電控單元。微控器(μC)必須控制EPS系統的直流有刷電機。微控器根據轉矩感測器提供的轉向輪所需轉矩信息,形成一個電流控制迴路。為了提高系統的安全水平,該微控器應有一個板載振盪器,這樣即使在外部振盪器出現故障的情況下,亦可確保微控器的性能,同時還應具備片上 看門狗。英飛凌公司的XC886集成了所有重要的微控器組件,其它安全特性可通過軟體實現,如果必須執行iec61508等行業安全標準規範,就不得不完成各種診斷和自檢任務,因而會增加微控器的工作負荷。目前不同客戶採用的轉矩感測器與轉子位置感測器差別很大。他們採用不同的測量原理,如分解器、 電磁共振器、基於感測器的集成巨磁阻(IGMR)。
功率級的作用是開關電機電流。該功率級具有兩個功能:驅動IC控制和保護MOSFET,MOSFET本身又可負責開關電流。MOSFET和分區(例如驅動IC與MOSFET結合在一個器件或多個器件內)由電機功率決定。
微控器的PWM輸出連線埠提供的驅動電流和電壓太低,無法直接與MOSFET柵極實現連線。驅動IC的作用是提供充足的電流,為MOSFET的柵極進行充電和放電,使其在20kHz的條件下正常實現開關,同時保證為高低側MOSFET提供高柵源電壓Vgs,確保獲得低導通電阻。如果高側MOSFET處於開通狀態,源極電位就接近電池電平。要想使MOSFET到達標稱導通電阻,柵源電壓需高於8V。MOSFET完全導通所需的最理想的電壓是10V或以上,因此所需的柵極電位就比電池電壓高出10V。電荷泵是確保該功能最大程度降低MOSFET功耗(即使低電池電壓條件下)的電路。圖2說明,英飛凌驅動IC即使在8V電池電壓條件下,其低高側MOSFET的柵源電壓也可達到11V。這將確保在低電池電壓條件下,獲得低功耗和高系統效率。
電荷泵設計的其它關鍵特性是可以根據不同PWM模式的要求,實現極低(低至1%)和極高的占空比(高至100%)。驅動IC的另一個重要功能是檢測短路情況,避免損壞MOSFET。受影響的MOSFET將關閉,診斷結果提交給微控器。電流水平可實現調節。
MOSFET通常套用在一個多半橋拓撲結構內,由驅動IC控制。根據ISO7637規定,在12V電網中,電池電壓通常可高達16V。在選擇MOSFET電壓級別時,必須針對二極體恢復過程中所出現的感應瞬變現象提供足夠的安全邊際(Ls x dl/dt,Ls代表雜散電感,dl/dt代表開關時的電流斜率)。在低dl/dt和低雜散電感的系統中,可使用30V MOSFET,但通常最好使用40V的MOSFET,可提供更高的安全邊際。最新的40V MOSFET技術採用D2PAK(TO263)封裝在2mm和180A條件下,以及採用較小的DPAK(TO252)裝封在低於4mm和90A的條件,可提供極低的導通電阻,使EPS系統設計具備極高的功率密度和效率。