簡介
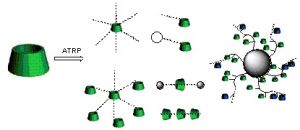
地位
自由基聚合在高分子化學中占有極其重要的地位。是人類開發最早,研究最為透徹的一種聚合反應歷程。目前60%以上的聚合物是通過自由基聚合得到的,如低密度聚乙烯,聚苯乙烯,聚氯乙烯,聚甲基丙烯酸甲酯,聚丙烯腈,聚醋酸乙烯,丁苯橡膠,丁腈橡膠,氯丁橡膠等。
聚合過程
該聚合反應屬鏈式聚合反應,分為鏈引發、鏈增長和鏈終止3個基元反應。
鏈引發
又稱鏈的開始 ,主要反應有兩步:形成活性中心——游離基,進而游離基引發單體。主要的副反應是氧和雜質與初級游離基或活性單體相互作用使聚合反應受阻。一般需要有引發劑進行引發,常用的引發劑有偶氮引發劑、過氧類引發劑和氧化還原引發劑等,偶氮引發劑有偶氮二異丁腈,偶氮二異丁酸二甲酯引發劑,V-50引發劑等,過氧類有BPO等。
鏈增長
是活性單體反覆地和單體分子迅速加成,形成大分子游離基的過程。鏈增長反應能否順利進行,主要決定於單體轉變成的自由基的結構特性、體系中單體的濃度及與活性鏈濃度的比例、雜質含量以及反應溫度等因素。
鏈終止
主要由兩個自由基的相互作用形成,指活性鏈活性的消失,即自由基的消失而形成了聚合物的穩定分子。終止的主要方式是兩個活性鏈自由基的結合和歧化反應的雙基終止,或二者同時存在。
聚合方法
自由基聚合反應在高分子合成工業中是套用最廣泛的化學反應,大多烯類單體的聚合或共聚都採用自由基聚合,所得聚合物都是線型高分子化合物。
按反應體系的物理狀態自由基聚合的實施方法有本體聚合、溶液聚合、懸浮聚合、乳液聚合四種方法 。它們的特點不同,所得產品的形態與用途也不相同。
本體聚合
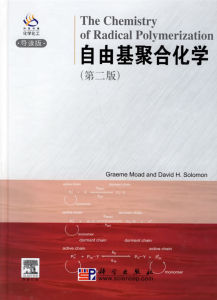
氣態、液態、固態單體均可進行本體聚合,液態單體的本體聚合最重要。
⑴ 本體聚合工藝
針對本體聚合法聚合熱難以散發的問題,工業生產上多採用兩段聚合工藝。第一階段為預聚合,可在較低溫度下進行,轉化率控制在10%~30%,一般在自加速以前,這時體系粘度較低,散熱容易,聚合可以在較大的釜內進行。第二階段繼續進行聚合,在薄層或板狀反應器中進行,或者採用分段聚合,逐步升溫,提高轉化率。由於本體聚合過程反應溫度難以控制恆定,所以產品的分子量分布比較寬。
本體聚合的後處理主要是排除殘存在聚合物中的單體。常採用的方法是將熔融的聚合物在真空中脫除單體和易揮發物, 所用設備為螺桿或真空脫氣機。現在也有用泡沫脫氣法,將聚合物在壓力下加熱使之熔融,然後突然減壓使聚合物呈泡沫狀,有利於單體的逸出。
本體聚合流程方塊圖見圖
⑵ 本體聚合反應器
工業上為解決聚合反應熱的難題,在設計反應器的形狀、大小時要考慮傳熱面積等。
在自由基聚合本體聚合所用的反應器有以下幾種。
① 模型式反應器 主要適宜於本體澆鑄聚合以製備板材、管、棒材等。模型的形狀與尺寸大小根據製品的要求而定,同時要考慮到聚合時的傳熱問題。
② 釜式反應器 帶有攪拌裝置的聚合釜,由於後期物料是高粘度流體多採用螺帶式(如單螺帶或雙螺帶)攪拌釜,操作方式可以是間歇也可是連續操作。也有根據聚合過程中粘度的變化採用數個聚合釜串聯,分段聚合的連續操作方式。
③ 本體連續聚合釜 連續聚合反應器有管式和塔式反應器兩種。一般的管式反應器為空管,物料在管式反應器中呈層流狀態流動。有的管式反應器在管內裝有固定式混合器。
塔式反應器相當於放大的管式反應器, 無攪拌裝置,物料在塔中呈柱塞狀流動。
溶液聚合
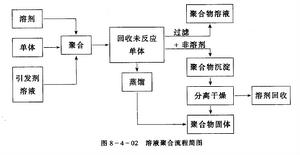
單體和引發劑溶於適當溶劑中進行的聚合方法稱作溶液聚合法。溶液聚合反應生成的聚合物溶解在所用的溶劑中為均相聚合,如聚合物不溶於所用溶劑中而沉澱析出,則為非均相聚合又稱沉澱聚合。
溶液聚合過程中使用溶劑,使體系粘度降低,因此混合和傳熱較易,溫度容易控制,較少凝膠效應,可以避免局部過熱。
另外,由於溶液聚合過程中使用溶劑,體系單體濃度低,聚合速率較慢,設備生產能力與利用率下降。如生產固體產品,則須進行後處理,溶劑的回收費用高,增加生產成本。因此工業上溶液聚合多用於聚合物溶液直接使用的場合,如塗料、膠粘劑、浸漬劑、分散劑、增稠劑等。如果要求得到固體聚合物,則可在溶液中加入與溶劑互溶而與聚合物不溶的其它溶劑使聚合物沉澱析出,再經分離、乾燥而得到固體聚合物。
⑴ 溶劑的選擇
溶液聚合所用溶劑主要是有機溶劑或水。溶劑的選擇在溶液聚合中是很重要的。在自由基溶液聚合中選擇溶劑時要注意:
溶劑對引發劑的誘導分解作用,以及對鏈自由基的鏈轉移反應。
可按聚合產品對分子量的要求,參考CS值來選擇溶劑。
根據溶劑對聚合物溶解性能和聚合產品的用途選擇適當的溶劑。常用的有機溶劑有醇、酯、酮、苯、甲苯等。
離子聚合選用溶劑時首先要考慮到溶劑的溶劑化能力,其次再考慮到鏈轉移反應。
⑵ 溶液聚合工藝
溶液聚合選用有機溶劑時,引發劑為可溶於有機溶劑的過氧化物或偶氮化合物。根據反應溫度和引發劑的半衰期選擇適當的引發劑。
用水作為溶劑時,採用水溶性引發劑,如過硫酸鹽及其氧化-還原體系。
溶液聚合反應溫度在溶劑的回流溫度下進行,所以大多選用低沸點溶劑。為了便於控制聚合反應溫度,溶液聚合通常在釜式反應器中半連續操作。直接使用的聚合物溶液,在結束反應前應儘量減少單體含量,或採用化學方法或蒸餾方法將殘留單體除去。要得到固體物料須經過後處理,即採用蒸發、脫氣擠出、乾燥等脫除溶劑與未反應單體,製得粉狀聚合物。
改變引發劑用量,單體與溶劑的用量比,添加分子量調節劑等方法來控制產物的分子量。
懸浮聚合
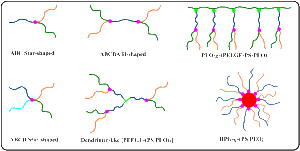
懸浮聚合體系一般有單體、引發劑、水,分散劑四個基本組分組成。不溶於水的單體在強力攪拌作用下,被粉碎分散成小液滴,它是不穩定的,隨著反應的進行,分散的液滴又可能凝結成塊,為防止粘結,體系中必須加入分散劑。
懸浮聚合產物的顆粒粒徑一般在0.05~0.2mm。其形狀、大小隨攪拌強度和分散劑的性質而定。
懸浮聚合法因以水為介質,體系粘度低,傳熱好,溫度易控制。產品分子量及其分布比較穩定。產物是固體微粒,後處理簡單,只需經離心、乾燥即可,因此成本較低。但也存在自動加速效應,使聚合速度不易控制;產品中的分散劑不能徹底清除,影響產品純度。 懸浮聚合法廣泛套用於工業生產。
⑴ 成粒機理與分散作用
① 成粒機理
懸浮聚合的單體苯乙烯、氯乙烯等在水中溶解度很小,基本與水不相溶,只是浮在水面呈兩層。在攪拌器強烈的剪下作用下,單體液層分散成液滴。
加有分散劑的懸浮聚合體系,當轉化率到20~70%時,液滴進入發粘階段,如果不攪拌仍有粘結成塊的危險,因此在懸浮聚合中,攪拌和分散劑是兩個重要因素。
② 分散劑及其作用
工業生產用的分散劑主要有保護膠類分散劑和無機粉末狀分散劑兩大類。
保護膠類分散劑都是水溶性高分子化合物。有明膠、蛋白質、澱粉、纖維素衍生物、藻酸鈉等天然高分子化合物,部分水解的聚乙烯醇、聚丙烯酸及其鹽、磺化聚苯乙烯、馬來酸酐-苯乙烯共聚物等合成高分子化合物。這類分散劑的作用機理是吸附在液滴表面,形成一層保護膜,起著保護膠體的作用。
碳酸鹽、磷酸鹽、滑石粉、高嶺土等無機粉末狀分散劑的作用機理是細粉末吸附在液滴表面起著機械隔離作用。無機分散劑較適合於高溫聚合。另外,懸浮聚合反應結束以後,無機粉末狀分散劑易用稀酸洗脫,因而所得聚合物所含雜質較少。
分散劑種類的選擇與用量的確定隨聚合物種類和顆粒要求而定。有時在懸浮聚合體系還加入少量的助分散劑,如十二烷基硫酸鈉、聚醚等。分散劑的用量為單體量的0.1%左右,助分散劑量是0.01~0.03%.
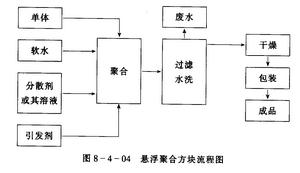
⑵ 懸浮聚合工藝
懸浮聚合法的典型生產工藝過程是將單體、水、引發劑、分散劑等加入反應釜中,加熱,並採取適當的手段使之保持在一定溫度下進行聚合反應,反應結束後回收未反應單體,離心脫水、乾燥得產品。
懸浮聚合所使用的單體或單體混合物應為液體,要求單體純度>99.98%。
在工業生產中,引發劑、分子量調節劑分別加入到反應釜中。引發劑用量為單體量的0.1% ~ 1%。
去離子水、分散劑、助分散劑、pH調節劑等組成水相。水相與單體之比一般在75:25~50:50範圍內。
各種單體的懸浮聚合過程都採用間歇法操作。
乳液聚合
乳液聚合是可用於某些自由基聚合反應的一種獨特的方法,它涉及以乳液形式進行的單體的聚合反應。它是指單體在乳化劑和機械攪拌作用下,在分散介質中分散成乳狀液而進行的聚合反應。乳液聚合體系的組成比較複雜,一般是由單體、分散介質、引發劑、乳化劑四組分組成。經典乳液聚合的單體是油溶性,分散介質通常是水,選用水溶性引發劑。當選用油溶性單體時,則分散介質為有機溶劑,引發劑是油溶性的,這樣的乳液體系稱為反相乳液聚合。
乳液聚合在工業生產上套用廣泛,很多合成樹脂、合成橡膠都是採用乳液聚合方法合成的,因此乳液聚合方法在高分子合成工業中具有重要意義。
乳液聚合法最大的特點是可同時提高聚合速率與分子量,同時還具備以下優點:
① 以水為分散介質,價廉安全。體系粘度低,易傳熱,反應溫度容易控制。
② 聚合速率快,分子量高,可以在較低的溫度下聚合。
③ 適宜於直接使用膠乳的場合,如乳膠漆、粘結劑等的生產。
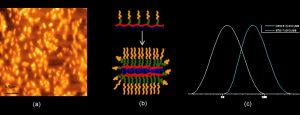
⑴ 乳液聚合機理
① 乳化作用
乳液聚合首先使單體在水中藉助於乳化劑分散成乳液狀態,這種使互不相溶的兩相,即油(單體)-水轉變為相當穩定難以分層的乳液,這個過程稱為乳化。乳化劑在乳液體系能起乳化作用,是因為乳化劑分子是由親水的極性基團和親油的非極性基團構成的。
乳化劑溶於水的過程中,在乳化劑濃度很低時,乳化劑以分子狀態溶解於水中,當濃度達到一定值後,乳化劑分子形成膠束,乳化劑開始形成膠束時的濃度為臨界膠束濃度,簡稱CMC,此時的濃度約為0.01~ 0.03%。在大多數乳液聚合中,乳化劑的濃度(約2~3%)總超過CMC值1~3個數量級,所以大部分乳化劑處於膠束狀態。膠束的數目和大小取決於乳化劑的量。在典型的乳液聚合中,膠束的濃度為1017~1018個/cm3。
乳化劑的作用是降低表面張力,使單體分散成細小的液滴;在液滴表面形成保護層,防止凝聚,使乳液保持穩定;增溶作用,使部分單體溶於膠束內。這三方面總合起來就是乳化作用。
乳化劑有陽離子型、陰離子型、兩性型和非離子型四類。用於乳液聚合的大多是陰離子型和非離子型的乳化劑。
極性基團是陰離子的為陰離子乳化劑,如十二烷基硫酸鈉(C12H25SO4Na)、松香皂等。它在鹼性溶液中比較穩定。
非離子乳化劑在水中不能離解為正、負離子,其典型代表是環氧乙烷聚合物,或環氧乙烷和環氧丙烷嵌段共聚物、聚乙烯醇等是具有非離子型特性的乳化劑。在乳液聚合過程中不能單獨使用,常用作輔助乳化劑,加入少量,可改善乳液穩定性、乳膠粒的粒徑和粒徑分布。
② 聚合機理
乳液聚合機理也經鏈引發、 鏈增長、鏈終止反應。在乳液聚合過程中,聚合體系的基本組分分別以不同的狀態存在,其變化情況是:
1)聚合過程相態變化
聚合反應開始前,單體與乳化劑分別以下列三種相態:a. 水相中,極少量的單體和少量的乳化劑,大部分引發劑;b. 單體液滴,由大部分單體分散成的液滴,表面吸附著乳化劑分子,形成穩定的乳液;c. 膠束,大部分乳化劑分子聚集而成,一般每個膠束由50~100個乳化劑分子組成,其中一部分為含有單體的增溶膠束。
在水相中的引發劑分解產生的自由基擴散進入膠束內,引發膠束中溶有的單體進行聚 合。隨著聚合的進行,水相單體不斷進入膠束,補充消耗的單體,單體液滴中的單體又溶解到水相,形成一個動態平衡。由此可見膠束是進行乳液聚合的反應場所,單體液滴是提供單體的倉庫。
在聚合反應初期,反應體系中存在有三種粒子,即單體液滴、發生聚合反應的膠束―稱作乳膠粒和沒有反應的膠束。隨反應進行,膠束數減少,直至消失,乳膠粒數逐漸增加到穩定。反應進入聚合中期,乳膠粒數穩定,單體液滴數減少。到反應後期,單體液滴全部消失,乳膠粒不斷增大,體系中只有聚合物乳膠粒。這就是在聚合過程中體系組成的變化。
2) 成核機理
膠束進行聚合後形成聚合物乳膠粒的過程,又稱為成核作用。
乳液聚合粒子成核作用的機理由兩個同步過程進行。一是自由基(包括引發劑分解生成的初級自由基和溶液聚合的短鏈自由基)由水相擴散進入膠束,引發增長,這個過程為膠束成核。另一個過程是溶液聚合生成的短鏈自由基在水相中沉澱出來,沉澱粒子從水相和單體液滴上吸附了乳化劑分子而變得穩定,接著又擴散入單體,形成與膠束成核同樣的粒子,這個過程叫均相成核。膠束成核作用和均相成核作用的相對程度將隨著單體的水溶解度和表面活性劑的濃度而變化。單體較高的水溶性和低的表面活性劑濃度有利於均相成核;水溶性低的單體和高的表面活性劑濃度則有利於膠束成核。對有一定水溶性的醋酸乙烯酯,均相成核作用是粒子形成的主要機理,而對親油性較強的苯乙烯,主要是膠束成核機理。
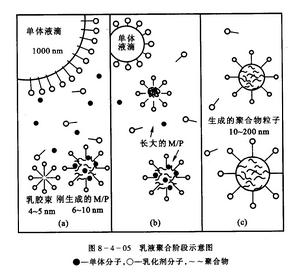
3) 聚合過程
典型的乳液聚合根據乳膠粒數的變化可將聚合過程分為三階段,即聚合物乳膠粒子形成階段;聚合物乳膠粒子與單體液滴共存階段和單體液滴消失、聚合物乳膠粒子內單體聚合階段。三個階段變化示意如圖。
第Ⅰ階段 — 乳膠粒生成期,即成核期。從開始引發直到膠束消失,整個階段聚合速率遞增。轉化率可達2~15%。。
第Ⅱ階段 — 恆速階段。自膠束消失開始到單體液滴消失止。膠束消失,乳膠粒數恆定,體積增大,單體液滴消失,乳液聚合速度恆定。轉化率達50%。
第Ⅲ階段 — 降速期。單體液滴消失後,乳膠粒內繼續進行引發、增長、終止,直到乳膠粒內單體完全轉化。乳膠粒數不變,體積增大,最後粒徑可達500~2000 Å。
聚合速率隨乳膠粒內單體濃度的減少而下降。
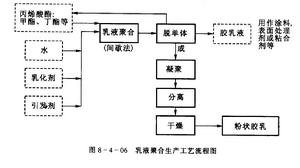
⑵ 乳液聚合工藝
乳液聚合法是高分子合成工業的重要生產方法之一,主要生產合成橡膠、合成樹脂、粘合劑和塗料用膠乳等。工業上用乳液聚合方法生產的產品有固體塊狀物,固體粉狀物和流體狀膠乳。如丁苯橡膠、氯丁橡膠、聚氯乙烯糊用樹脂及丙烯酸酯類膠乳。
乳液聚合法的生產簡單工藝流程如圖。
在乳液聚合工藝配方中除以上組分外,還加入緩衝劑,分子量調節劑,電介質,鏈終止劑,防老劑等添加劑。
乳液聚合過程是按配方分別向聚合釜內投入水、單體、乳化劑及其它助劑,然後升溫反應。根據向聚合釜加料方式,可分為間歇操作、半連續操作和連續操作,都在帶有攪拌裝置的聚合釜內進行反應。間歇操作、半連續操作在單釜內進行聚合反應,而連續操作則採用多釜串聯的方式進行聚合反應,通常由4~12個釜組成一組生產線。
膠乳用作塗料、粘合劑等就可直接使用,不必再處理;必要時須調整含固量,可採用稀釋或濃縮的方法。如要得到粉狀膠乳,可採用噴霧乾燥的方式。將膠乳連續送入噴霧乾燥塔,噴入熱空氣與霧化的膠乳接觸,經乾燥成為粉狀顆粒。
另外還可用凝聚法進行後處理,簡單的方法是在膠乳中加入破乳劑將聚合物分離出後,再進行洗滌、乾燥即得分散性的膠乳粉末。凝聚法因能去除大部分乳化劑,產物純度高於噴霧乾燥法。
⑶ 乳液聚合的發展
近幾年內典型的乳液聚合法在理論上獲得了很大進展,由Harkins,Smith和Ewart等人建立了乳液聚合機理和動力學模型,同時也有很多學者提出了殼層或核-殼層模型等一些有參考價值的理論。同時在乳液聚合技術方面也在不斷發展和創新,出現了許多新的乳液聚合方法,如水溶性單體的反相乳液聚合,核殼乳液聚合,無皂乳液聚合,乳液定向聚合,乳液輻射聚合,乳液接枝共聚合及種子乳液聚合等,為乳液聚合技術領域提供了豐富的新內容,使乳液聚合在高分子合成工業套用更為廣泛。採用無皂乳液聚合法可以得到粒子規整的單分散聚合物,核殼乳液聚合法可以通過調整核、殼兩部分得化學組成、分子量及玻璃化溫度來達到產物所需的性能要求。這些為開發性能優越的新產品提供了更多的渠道。