原理
銅轉爐銅鋶吹煉的目的是通過銅鋶和空氣中的氧氣進行劇烈的自熱反應,將CuS氧化成金屬銅,是一個典型的間隙式生產過程。該過程通常分為兩個階段:造渣期和造銅期。造渣期的主要目的是除去銅鋶中的鐵元素,生成主要含CuS的白鋶;造銅期的主要目的是除去其中的硫元素,生成含銅98%以上的粗銅。
吹煉(converting)鼓風將液態杭氧化除去毓中的鐵和硫,產出粗金屬或金屬富集物的火法冶金過程。銅的吹煉過程一般分為兩周期,第一周期是FeS的氧化造渣產出白銅銑(CuZS),第二周期是CuZS的氧化得到粗銅。一般稱第一周期為造渣期,第二周期為造銅期。鎳梳的吹煉只有第一周期,產出高鎳銑(NiSZ),不繼續吹煉得粗鎳而另行處理。吹煉過程一般在臥式轉爐(P一S轉爐)(見銅毓吹煉)中進行,為周期性作業。
先進控制在銅鋶吹煉造渣期終點判斷的套用
研究背景
銅鋶吹煉終點判斷是利用吹煉過程信息,分別推斷最佳造渣期倒渣時機和造銅期出銅時機。吹煉終點是吹煉過程各影響因素的綜合體現,準確判斷各周期終點既是整個吹煉過程的重點也是難點。在工業實踐中仍靠操作工經驗觀察火焰顏色,取樣檢查熔體試樣顏色和形狀,化驗分析組分存在情況來判斷終點。這極其依賴操作工經驗,難以規範化、標準化,無法利用計算機取代人的判斷過程;化學分析造成滯後,而可能錯過終點導致過吹現象。這些缺點造成實現計算機線上終點判斷困難,極大限制了銅鋶吹煉的自動化水平。為提高綜合生產率,國內外企業積極探索銅鋶吹煉終點的判斷策略,並取得諸多成果:分析SO2濃度變化趨勢輔助判斷造銅期終點;張雲生等人套用信息集成並行進行吹煉過程操作和終點控制 ,開啟了國內銅鋶吹煉終點計算機判斷的新進程;梅熾教授等套用BP神經網路開發轉爐吹煉過程智慧型決策與終點預報系統 ,為研究先進控制在銅鋶吹煉終點判斷的套用提供了重要參考。模型預測控制(MPC)是套用較成熟的一種先進控制技術 ,對描述和處理多變數複雜過程工業控制問題有它獨到的優越性。套用MPC建立銅鋶吹煉終點判斷模型具有簡單、直觀、易懂易用的優點,且在終點判斷中僅用到簡單的矩陣計算,不需要在龐大的解空間中尋找最優解,免去繁瑣的推理匹配過程,大大提高了判斷速度。所以MPC是研究和模擬銅鋶吹煉終點的理想工具,對於判斷的準確性具有顯著的作用。鑒於此,研究基於MPC的銅鋶吹煉造渣期終點的動態矩陣控制(DMC)以實現造渣期終點判斷的自動控制,並利用MATLAB進行系統仿真驗證該方案的可行性。
銅鋶吹煉造渣期終點的DMC模型
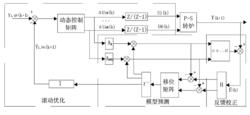
DMC是套用最廣的一種MPC算法,它突破了傳統控制模式:以對象在單位階躍信號作用下的時間回響為基礎,通過採集對象的輸入、輸出信號序列來確定控制量的時間序列,並預測系統未來輸出,突破傳統控制中對模型結構的嚴格要求;它採用滾動式的有限時域最佳化策略,將系統未來輸出與期望軌跡線上比較反覆最佳化局部目標,顧及了畸變、模型失配和干擾引起的不確定性;此外,滾動最佳化還能方便地處理過程被控變數和操縱變數中的各種約束條件。推導P-S轉爐造渣期吹煉終點控制系統的預測模型方程、反饋校正方程及最優控制律,進而建立其DMC預測控制模型。
DMC模型研究結果
針對現代銅冶金工業銅鋶吹煉工序“定終點”難的問題,介紹了如何套用先進控制技術——DMC實現銅鋶吹煉造渣期終點判斷的自動控制,並藉助MATLAB系統仿真檢驗了這種控制策略的效果,證實了設計方案的可行性,為進一步深入研究銅鋶吹煉造銅期吹煉終點控制推進實現吹煉全過程的自動控制提供了實驗參考。存在的問題是研究僅以銅鋶品位及銅鋶量這兩種主要因素對被控變數的影響實施仿真進行效果說明,而轉爐吹煉銅鋶過程中轉爐工況不穩定、各物料投入產出波動、轉爐工操作規範與否、造渣期冷料量、渣量、渣中鐵矽比、渣含銅等因素均會對吹煉所需風量造成影響。所以,具體實施時應充分考慮各方面因素的綜合影響,對模型和調節參數作進一步修正,以使系統的性能達到最佳。
PS轉爐吹煉造渣期冷量及其影響因素的研究
研究背景
銅鋶吹煉是火法煉銅工藝的關鍵工序之一。全世界約85%的冰銅採用Peirce-Smith(PS)轉爐吹煉。PS轉爐吹煉為間歇式熔池反應過程,是具有非線性、強耦合的非封閉系統。將熔煉過程得到的銅鋶送至PS轉爐進行吹煉,在此過程中鼓入空氣或富氧空氣、添加熔劑以維持反應進行,同時投放冷料吸收剩餘熱量,最終形成粗銅。吹煉過程分為兩個階段:即FeS發生系列氧化造渣反應產出大量爐渣(稱為造渣期),和CuS發生系列氧化反應產出粗銅(稱為造銅期)。
吹煉造渣期反應為放熱反應,反應所放出的熱量不僅能滿足維持反應溫度的需求(通常為1523±10K範圍內),還能產生大量剩餘熱量(即冷量)。因此,在反應過程中需要加入冷料來平衡冷量,以維持穩定的反應溫度,增加粗銅產量。該過程中的剩餘熱量大小對冷料的添加和轉爐的壽命等參數影響很大。因此,準確計算該過程中的冷量,將為添加冷料、增加銅產量、降低產品能耗提供依據,實現銅吹煉過程節能降耗。由於準確測量生產數據難度大、技術環境不穩定等因素,難以根據經驗的方法得到準確的冷量值。
國內外研究者建立了銅鋶吹煉過程的靜態計算模型。基於Brinkly平衡法建立了鋶、氣、渣三相平衡計算模型,該模型在實際生產中得到運用;運用吉布斯自由能最小熱力學平衡計算法得到了吹煉期間轉爐內銅鋶溫度的變化情況;根據元素守恆原理計算出吹煉過程的理論耗氧量和全息氧率;從熱力學原理角度建立富氧吹煉的節能模型和熱經濟模型;利用傳熱原理合理假設建立了冷料熔化速率和熔化時間的動力學模型。然而,上述靜態模型不能滿足對生產過程進行實時調度的需要。基於物料守恆、能量守恆和反應動力學原理,建立了銅鋶吹煉造渣期的動態模型。利用正交試驗和方差分析的方法,對影響冷量的主要生產因素進行顯著性分析。該研究實時反映生產中物質和能量的實時變化,為實現最佳化能量利用和實時監測提供依據。
造渣期冷量計算動態模型
為建立描述造渣期過程物料平衡和能量平衡的動態模型,對模型做出以下假設:
(1)進入轉爐吹煉的銅鋶主要由FeS和CuS組成,忽略其它微量元素如鋅、鈷、鉛、砷、錫等的影響;
(2)吹煉過程中,假設鼓入轉爐中的空氣只由氧氣、氮氣兩種氣體組成,其它成分忽略不計。普通空氣中氧氣、氮氣體積比為21:79,富氧空氣中氧氣、氮氣體積比為a:(1-a);
(3)轉爐內物料的總體積基本不變,PS轉爐反應系統可近似為恆容系統;
(4)吹煉過程中,投放固體冷料吸收冷量的過程為物理熔化過程。
研究結論
(1)各能量分項的累計值變化如下:反應初始階段,反應熱Q(反應)增加速度快,反應進行到後期,趨於穩定;白銅鋶和爐渣造成的熱損失Q(白銅鋶)、Q(爐渣)也隨反應的進行先增加後趨於穩定;鼓風帶走的熱量Q(鼓風)將持續增加;Q(冷量)隨反應的進行先增加後略有下降。
(2)在實際生產條件範圍內,增加造渣期富氧率、降低冰銅品位或減小鼓風速度,將導致生成的冷量增加。
(3)富氧率、冰銅品位、鼓風速度等主要控制因素對於冷量生成量都是顯著的影響因素,但其重要程度不同,由高到低分別為:冰銅品位、鼓風速度、富氧率。