基本概念
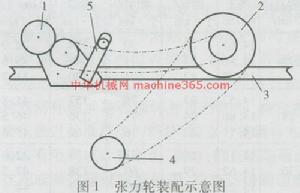
清花流程對梳棉生條棉結的影響
在化纖清梳聯流程中,清花設備的合理選型配置,直接影響生條棉結的高低。因此,在選擇化纖清梳聯流程時,注意開清棉設備的合理配置是提高生條質量的一個重要因素。
0前言
化纖清梳聯流程的配置,有著自己的特殊性。化纖原料蓬鬆,易產生靜電,過多的翻滾和打擊過度都會造成後部棉結的增加。棉結是成紗主要考核指標之一,它直接影響到後部成品的外觀質量。梳棉工序是控制和降低棉結的主要工序,但不是唯一的工序。通過生產實踐我們認為清花工序同樣重要,清花流程及設備的配置。也會影響到梳棉棉結的多少。
1不同流程對棉結的影響
現在介紹兩種生產線比較分析:一條全部是由鄭紡機生產的清梳聯設備,另一條線開清棉設備是德國特呂茨勒的設備,梳棉機配的是FA221B型梳棉機,兩條線的工藝流程分別如下:
兩條線的FA221B型梳棉的主要工藝參數相同:生條定量:27g/5m;出條速度:130m/min;錫林速度:350r/min;刺輥速度:850r/min;蓋板-錫林隔距:14、12、12、12;前固定蓋板-錫林隔距:12;後固定蓋板-錫林隔距:43;錫林-刺輥隔距:7;錫林-道夫隔距:5。以上隔距單位均為1/1000英寸。
2.1梳棉生條棉結測試
取樣方法,每個流程每天測試六台車對比,每台車的生條取五次樣,計算平均值,測試數據見表1。
2.2烏斯特成紗指標對比(見表2)
經過多次取樣對比證明,梳棉機在相同的工藝參數的條件下,清花流程對棉結有較大影響,德國短流程棉結指標明顯優於鄭紡機流程。經分析,化纖原料磨擦係數大,在加工過程中容易引起靜電搓繞形成棉結。所以在生產流程中要特別注意減少原料的翻滾搓擦產生的棉結。在(A)流程中,採用了自動抓包機抓棉,打手速度在1500r/min左右,在抓取原料的過程中,抓棉打手刀片與原料發生摩擦,就會產生棉結,速度越快產生棉結的機會就越多。特別是在前方機台不要花時,抓棉小車就會停留在一個位置,打手刀片反覆在這個位置打擊原料,就更容易造成棉結。流程中的各個機台上的凝棉器,化纖原料在上面摩擦鏇轉,也是增加棉結的一個因素。經觀察,FA017型自動混棉機的角釘帘子,在抓取原料的過程中,原料反覆翻滾,在混棉的同時也容易增加棉結,另外該流程的FA108E型開棉機,開松打手是鋸齒刀片,在開松梳理的過程中刀片截面成矩形,易於掛花,也宜增加棉結。
(B)流程,採用手工餵棉,大大減少了增加棉結的機會,另外混棉機的均棉羅拉和清潔羅拉直徑較大,不易纏繞,流程中也沒有凝棉器的採用,減少了翻滾摩擦造成的棉結增多的機會。VFO型開棉機採用梳針打手,梳針表面光滑,所以產生的棉結機會就大大減少。所以該流程產生棉結的機會低於(A)流程,減少了梳棉機梳理的負擔。這也就是為什麼(B)流程生條棉結低於(A)流程的主要原因。
3結束語
綜上所述,在選擇化纖清梳聯流程時,開清棉設備的合理配置是提高生條質量的一個重要因素,由於化纖無雜質。採用一抓一混一梳的短流程即可,一抓就是一道抓棉機,一混就是一道混棉機,一梳就是一道梳針滾筒開棉機。在清花流程應強調的是開松梳理,不要有過多的打擊,應選用梳理作用柔和的梳針打手為宜,同時選用原料不易翻滾而又能起到混棉作用的多倉混棉機,儘量少用凝棉器,在化纖流程中,基本不存在除雜的問題,採用凝棉器的弊大於利。同時各部氣流要通暢,減少阻塞掛花,都會有效地減少生條棉結,提高成紗質量。如採用國產自動抓包機,打手的速度不宜過快,同時應該提高運轉率,儘可能減少停止抓棉的時間,防止抓包打手反覆打擊該處的原料而造成棉結的產生。
降低清梳聯生條雜質
近幾年國產清梳聯技術進步較快,表現在機械加工精度的提高,單元機型和流程機台配置的改進,控制技術的進步,分梳元件的優選配套和濾塵技術的配合等方面,已被廣大用戶接受並得到迅速推廣,對改善和提高棉紗質量水平起到了積極作用。棉紡織廠工程技術人員在生產中不斷研究並改進工藝,積累了不少經驗,但普遍遇到的突出問題是生條含短絨(≤16mm以下)偏高,而採取降低短絨的措施往往又會影響結雜的清除,特別是棉結。要處理好這一對矛盾,應根據品種需要做好設備選型和流程配置,尤其是開松、梳理元件規格的選擇,工藝上對開松、除雜、減少棉結和排除短絨必須統一考慮,同時還應加強基礎性技術管理工作,才能獲得最佳效果。在實踐中我們通過對“青鋒”牌清梳聯工藝特點進行分析、改進,逐步形成了“連續均勻餵給、薄餵柔和開松、早落少傷纖維、梳理轉移適度、結雜短絨兼顧,氣流參數保證”的清梳聯降低結雜和短絨的生產工藝要點,已被廣泛採用,對於其他機型清梳聯流程也會起到參考作用。
1連續均勻餵給的控制
提高開清單元機台的運轉率,做到連續均勻餵給,這樣在相同產量前提下抓取棉束最小、最勻,開松效果好,棉束表面積增加,雜質易於暴露,有利於排除,同時也為均勻混和創造了條件。
1.1提高抓棉機運轉率
抓棉機多包取用、精細抓棉是短流程的基礎。在加工過程中,隨著原棉逐步開松,雜質逐步減少,但棉結、短絨隨著打擊力度的增大和經過單元機台的增多是逐步增加的。因此現代清梳聯開清部分均採用“一抓一開一混一清”的短流程工藝。一般要求自動抓棉機的運轉率應達到95%,至少也要保持90%以上。它是通過調整主要參數:小車往復速度、抓取輥速度、抓取輥刀片與肋條相關隔距和抓臂每次下降動程來實現的。四個參數選擇是否恰當,不僅影響運轉率的高低,棉束重量的大小,還影響單位時間抓取棉包嘜頭的多少,最終影響除塵雜和均勻混和效果。在通常情況下,抓取輥速度採用1250r/min~1350r/min,不宜過高,否則抓取力大,損傷纖維,近幾年有的廠採用1000r/min;抓取輥刀片與肋條隔距採用負值,抓取浮起於肋條以上的棉層,抓取棉束小,一股採用-2mm~-3mm。二者調整好後平常生產不便於變動,保證產量供應主要靠變動小車往復速度和抓棉下降動程來實現。要提高運轉率,關鍵是操作工應根據棉包密度的變化及時調節(小車速度確定後也不輕易變動,重點是掌握抓臂下降動程)。為了做到多包取用,往復速度以控制在15m/min左右為好。目前生產中碰到的問題是棉包密度差異大,進口棉包密度要比國內棉包大得多,揀“三絲”後各廠打包的密度也不一樣,這對保證自動抓棉機實現精細抓棉造成了困難。例如棉包過松,為了保證供應,有的廠小車往復速度高達18m/min,抓取輥刀片與肋條隔距-5mm~-7mm,抓棉臂每次下降動程也相應較大,致使棉塊體積必然相對較大,對除塵雜和均勻混和均不利。在此情況下,有必要適當提高抓取輥速度,因為速度越高,則抓取的棉塊相對越小(棉包密度小,對纖維損傷也相對較小)。反之如遇緊包棉,則可相對縮小刀片與肋條的隔距和抓棉臂每次下降的動程,為了少傷纖維,適當降低抓取輥速度。一般國內外抓取輥配兩檔速度(如立達公司為1335r/min和1.565r/min),而“青鋒”牌FA009型自動抓棉機抓取輥採用變頻調速,同時正式推出2300mm長度的抓臂,使橫向排包增加了25%,(國棉包),既適應各種棉包密度,並可根據不同原料、纖維細度、成熟度等為優選抓取輥速度提供方便,同時由於抓取量的增加(抓臂長度1700mm~2300mm),在供應產量不變的情況下,也為調小抓臂下降動程創造了條件,做到棉束相對較小,有利於排除塵雜和均勻混和。
1.2提高多倉混棉機的運轉率是保證開清流程
機台高運轉率的核心
只有提高多倉混棉機的運轉率,才能保證自動抓棉機高運轉率,實現多包取用、精細抓棉,同時做到均勻送出棉流。“青鋒”牌FA029型多倉混棉機的斜簾、水平帘子均採用變頻調速,斜簾運轉率受FA116型主除雜機棉箱內部壓力感測器和餵棉羅拉控制,調試中可達100%;水平帘子受控於斜帘子速度,只要設定好棉倉壓力範圍(紡棉180Pa~220Pa),就為提高FA009型抓棉機運轉率創造了條件,一般可達95%左右(FA009型機運轉受控於棉倉壓力的變化)。這時,在一定產量下不僅做到抓棉束最小(產量在350kg/h一500kg/h時,棉束重量約在16mg/塊~25mg/塊),而且抓取每個嘜頭次數也相對最多。
1.3主除雜機運轉率必須做到100%
為了控制好生條重量CV值和重量偏差,必須抓好三個重要環節:主除雜機要做到向餵棉箱上管道連續均勻地送棉;上棉箱向下棉箱連續均勻餵棉和配備自調勻整器;“青鋒”牌清梳聯流程配有連續餵棉裝置(FT1301B),做到主除雜機餵棉羅拉運轉率100%,保證了筵棉薄餵入,對主除雜機除塵雜有利。
2開清棉有關工藝與結雜短絨的關係
實踐證明,筵棉含結雜、短絨情況除了和原棉質量密切相關外(特別是棉結),更重要的是取決於開清部分流程機台配置、打手形式及相關工藝參數(如打擊力度,排雜方式)。現代清梳聯開清部分多採用“一抓一開一混一清”短流程配置,如何做到薄餵入,實現柔和開松,減少打擊力度,對多排雜和少產生棉結和短絨尤為重要。連續均勻餵給對開棉機和主除雜機的薄餵人創造了條件,可根據原棉含雜情況合理選擇打手(滾筒)形式和速度,減少打擊力度,既可提高除雜效率,又可少產生棉結和短絨。同時可根據含雜類別,合理分配開、清機台除雜效率。
2.1充分發揮單軸流開棉機除大雜的作用
目前國內開棉機多採用單軸流或雙軸流形式,但普遍認為單軸流優於雙軸流。FA105A型單軸流開棉機的設計特點:(1)棉流在上蓋內部導棉槽的作用下,可繞打手5.5圈(機長1600mm型),開松清除時間長;(2)塵棒分四區可調,塵棒角度的變動既可調整塵棒間隔距,同時也調整打手與塵棒間隔距;(3)棉流在自由狀態下受V形角釘彈打作用,開松除雜作用逐步增加;(4)車肚排雜,打手前側設排微塵和短絨網孔;(5)打手為變頻調速,調整工藝方便。因此FA105型機除雜效率高,一般可達25%以上,有的廠試驗可高達35%,遠遠高於雙軸流開棉機。
如何發揮單軸流開棉機的作用,工藝上應注意兩點:
(1)掌握好四點壓力。棉流人口處靜壓一般應掌握在+50Pa-+150Pa,不能過大,否則受氣流衝擊入口處塵棒間落白花;出口處靜壓一般掌握在-50Pa~-200Pa,不能過低,否則會回收短絨和塵雜;排雜口應保證落物順利排出,一般靜壓不低於-800Pa;排微塵口靜壓一般控制在100Pa~-200Pa,不宜過低,否則網眼易被短絨糊死。
2)調節好四區塵棒角度。塵棒安裝如圖1所示,打手與塵棒間隔距是隨著塵棒安裝角度增加而縮小,塵棒間隔距是隨著角度增加而增大。理論上棉流進入工作區應是隨著逐步開松而逐步增大打手至塵棒間隔距,而塵棒間隔距則隨之相應縮小,即塵棒角度第一區至第四區應逐步減小。但實際上第一區角度要視落雜和是否落白花而選擇,主要發揮第二、三區落大雜的功能,塵棒角度可適當調大,第四區則為了防止塵雜、短絨回收,角度應調小。打手速度一般採用500r/min-600r/min(如原棉含雜率在2.5%以上,打手速度可以適當提高,塵棒角度也要調整),如某廠在生產CJ14.5tex紗時,原棉含雜率1.02%,打手速度為590r/min,塵棒角度為18°、12°、6°、3°,除雜效率達到34%~36%。
θ-塵棒安裝角;α-塵棒間隔距;b-打手與塵捧間隔距;c-塵棒間頂面距。
FA116型主除雜機為開清工序流程中的精細分梳開松點,它採用梳棉機後車肚工藝,餵棉羅拉包覆鋸條與給棉板隔距可調至1.2mm,將棉層均勻地餵給傳送輥,這是流程中唯一的握持打擊點。傳送輥和主除雜輥鋸條均屬Hollingsworth公司專利產品,前者縱密小(0.99齒/25.4mm),橫密大(24.19齒/25.4mm),工作角65°,對分梳有利且便於轉移,附有除塵刀清潔器,排除大雜、微塵和短絨;後者也是縱密小(2.48齒/25.4mm),橫密大(18.14齒/25.4mm),齒密45齒/(25.4mm)2,工作角55°,有利於對棉束的進一步分解。附有三把除塵刀,兩塊分梳板,起到交替分梳和除雜的作用。主除雜輥與傳送輥表面線速比設計為3.2:1,即調節主除雜輥速度時,傳送輥速度也按比例進行變動,速比大有利於棉束的轉移。過去由於過分突出該機的除雜作用(一般除雜效率可達50%以上),主除雜輥速度比較高,傳送輥速度也隨著增加。餵棉羅拉速度受控於梳棉上棉箱管道內部靜壓和梳棉機開台的變化,如後部產量沒有變化,則餵入量一定,這樣雖然主除雜輥與傳送輥間自由分梳仍保持較高的轉移率,但傳送輥與給棉羅拉間卻增加了打擊力度,分梳度也增加,帶來的問題是棉結隨著速度的增加而上升。有生產廠做過試驗:當主除雜輥速度由930r/min增加到1850r/min時,單機除雜效率由50.2%增加到68.5%,但棉結卻從61粒/g增至103粒/g,同時短絨率也由降低0.5%變為增加0.7%。
近幾年,各生產企業普遍重視棉結和短絨的產生,只要筵棉含雜率控制在0.8%~1.0%以內(錫萊分析機檢測)或棉結增長率在80%以內,最多不超過100%(AFIS檢測),則應儘量減小開清部分打擊力度,以減少棉結和短絨的增加。如FA116型主除雜機或FA109型三刺輥清棉機,速度都有大幅度降低。在環錠紡生產中、細號紗時,一般原棉含雜率多在1.5%~2.0%,對主除雜輥的速度多數採用500r/min~650r/min,但如遇含雜率較少時,則可採用更低的速度。如某廠生產CJ14.6tex紗,原棉含雜率為1.0%~1.2%,主除雜輥速度降為320r/min,經AFIS儀器檢測:輸人主除雜機筵棉棉結為244粒/g,輸出筵棉棉結為270.3粒/g,增加10.8%;輸入筵棉帶籽殼棉結為16.5粒/g,輸出筵棉帶籽殼棉結為25.75粒/g,增加56.1%;輸入筵棉塵雜127粒/g,輸出筵棉塵雜69.5粒/g,減少45.3%,輸入筵棉短絨率(<16mm)9.85%(重量法)、26.9%(根數法),輸出筵棉短絨率9.8%(重量法)、25.8%(根數法),分別減少了0.5%(重量法)和4.1%(根數法)。實踐表明,根據原棉含雜情況可降低主除雜輥速度,棉結增長幅度小(帶籽殼棉結增長幅度大,可能是棉籽破碎造成,這時應檢查FA105A型機落大雜情況),短絨率不增而塵雜去除率仍很高,這正是薄餵為輕打創造了條件。
為了控制棉結和短絨的增長,少傷纖維,在原棉含雜1.5%以內,且總產量不太高的情況下,主除雜輥鋸齒改為針輥,實行以梳代打,柔和開松,進一步清除塵雜,此舉已取得一定效果,目前正逐步擴大試驗,已有11條線在生產。
3梳棉工藝參數與結雜短絨的關係
在清梳聯流程中,梳棉機是去除棉結和雜質的主要設備,但它既排除短絨,同時也產生短絨。纖維在梳理過程中要考慮梳理度、梳理強度和轉移率,因為只有三者配置恰當,纖維才能獲得充分梳理,損傷少,均勻混和且及時轉移。因此我們在制定梳棉工藝時,要根據成紗質量特殊要求,參考原棉條件,特別是纖維細度、成熟度和含雜類形,掌握“梳理轉移適度,結雜短絨兼顧”的原則,正確處理好去除棉結雜質和少產生短絨的關係。
3.1做好梳理件七配套工作
生條質量的關鍵取決於針布的選型配套和工藝參數的設定,而做好梳理件七配套是前提。“青鋒”牌清梳聯在梳棉機七配套工作中體現了高產高質的要求:(1)刺輥-分梳板-後固定蓋板-迴轉蓋板-前固定蓋板-錫林,針布齒密逐步增加,分梳能力逐步增強;(2)採用了矮、淺、尖、薄、密、小的新型錫林針布,提高了分梳能力;(3)道夫採用大齒深、小工作角、彎背的新型針布,有利於纖維向道夫凝聚和轉移;(4)與之配套的新型蓋板針布(稀密型);(5)採用耐磨度較高的進口針布或國產合金鋼針布。目前梳理件有國內外各種規格可供用戶選擇。
3.2生條定量的確定
生條定量是確定梳棉機產量的主要條件之一。清梳聯和梳理元件、附加梳理件的進步,為提高梳棉機產量創造了條件。現代高產梳棉機主要是提高了出條速度,生條定量加重只有少量變化。這主要是因為生條定量加大一方面會受到後工序牽伸分配的限制(特別是生產較細紗號時),另一方面會加大錫林針布負荷,影響分梳效果。多數製造廠家推薦生條定量範圍多為3.6g/m~6.5g/m,而實際生產中多採用3.6g/m-4.5g/m(轉杯紡紗可適當提高),這是比較合適的。定量也不能太輕,否則會相應增加分梳強度,造成短絨增加。定量確定後,要合理選擇錫林速度和出條速度,這就是前面提到的要掌握“梳理轉移適度、結雜短絨兼顧”的原則。
高產梳棉機生條定量
從紡紗過程牽伸角度來說,生條定量加重對成紗最終質量是不利的,故生條定量不能過重,這也是今後高產梳棉機研製和使用過程中要始終遵循的基本原則。
有利於錫林針面負荷減輕和道夫轉移率提高
根據鮑爾佐諾夫Nawaz,P.Grosberg[11,12,13]等人的研究,道夫速度提高時,轉移率是提高的,(由於當代高產梳棉機工藝和製造水平的提高,如道夫針布,採用新齒型和特殊處理方法使纖維的轉移比傳統梳棉機有較大程度的提高)。錫林上纖維密度降低,負荷下降,自由纖維量減少,這是因為道夫速度增加相當於道夫針齒與錫林上纖維接觸幾率增加,因而有利於纖維轉移,另外,道夫針布上纖維負荷減輕(因為生條定量減輕)也使錫林針布上纖維所受到壓力減輕,這將促使錫林針布上纖維負荷上浮,纖維密度下降,纖維容易轉移。同時,因錫林負荷減輕,蓋板花重量也減輕[14],因而將會提高梳棉機(錫林蓋板區)的分梳能力,故有利於分梳質量提高[3],這就是現代高產梳棉機採用快速,生條定量變化不大的另一原因。
但生條定量也不可過輕,生條定量過輕,就意味著道夫速度過快,這樣根據分析,其自由纖維量將變得太少,因為當代高產梳棉機分梳能力都較強,故纖維受到一次分梳強度增加,因而會造成纖維損傷而導致短絨增加,有關試驗表明[4]當在C4梳棉機採用3.4g/m輕定量(已經低於C4梳棉機生條定量範圍)時,其短絨要高於4.5g/m定量情況。這證實過輕定量的確會造成纖維損傷,故當代高產梳棉機不宜使用太輕的定量。另外,定量過輕,會使棉網抱合力差,棉網飄動,也不利於棉網形成與棉條高速輸出,為了增加棉條的強力,當代高產梳棉機,都採取適當增加生條重量的技術措施,這也是高產梳棉機生條定量緩慢增加一個很重要的原因。
高速剝棉系統的完善
根據以上分析,梳棉機要想高產,必須採取以提高道夫速度這個措施入手,但是當輸出速度提高后,由於棉網飄動、涌頭等而導致棉條斷頭,因而國內外高產梳棉機都在研製高速導棉裝置,以加強對棉條輸送強力,提高棉條穩定輸送能力,據測試[15],在DK2機上不採用導棉裝置,儘管採用較高定量(以加強棉網強力),但當採用道夫38r/min時,半小時有5次斷頭,而採用導棉裝置道夫50r/min時,半小時無一次斷頭,可見採用導棉裝置的確可提高輸出速度,保證棉條正常快速輸送。如今世界各主要梳棉機公司都採用導棉裝置來保證條子高速輸出[16]。
C4採用棉網一切向輸送帶的方式進行棉網輸送,其速度可達300m/min。MK5、FA203等採用雙皮圈導棉。DK903採用是可減少條子斷頭的纖維網引導組件—WEBSPEED。還加有任選的橫向輸送條子系統transverseslivertakeoffsystem以保證在加工極短纖維時,條子能順利輸送。
結論
根據以上分析,我們可以得出如下結論
1)高產梳棉機的發展歷程顯示,生條定量只是略有增加。
2)生條定量變化不大原因是,①紡紗過程中牽伸倍數限制,②有利於錫林針面負荷減輕和道夫轉移率提高。③高速剝棉系統進一步完善。
3)根據高產梳棉機實際發展情況建議生條定量做如下劃分,將4g/m以下定義為輕定量
4-5.2g/m為中定量
5.2g/m以上為重定量。
4)在高產梳棉機製造和使用過程中,快速和生條採用中定量是我們應遵循的基本工藝原則。