定義
以一定能量的粒子(離子或中性原子、分子)轟擊固體表面,使固體近表面的原子或分子獲得足夠大的能量而最終逸出固體表面的工藝。濺射只能在一定的真空狀態下進行。
原理
濺射工藝圖如圖1所示,濺射鍍膜最初出現的是簡單的直流二極濺射,它的優點是裝置簡單,但是直流二極濺射沉積速率低;為了保持自持放電,不能在低氣壓( <0.1 Pa)下進行;不能濺射絕緣材料等缺點限制了其套用。在直流二極濺射裝置中增加一個熱陰極和輔助陽極,就構成直流三極濺射。增加的熱陰極和輔助陽極產生的熱電子增強了濺射氣體原子的電離,這樣使濺射即使在低氣壓下也能進行;另外,還可降低濺射電壓,使濺射在低氣壓,低電壓狀態下進行;同時放電電流也增大,並可獨立控制,不受電壓影響。在熱陰極的前面增加一個電極(柵網狀),構成四極濺射裝置,可使放電趨於穩定。但是這些裝置難以獲得濃度較高的電漿區,沉積速度較低,因而未獲得廣泛的工業套用。
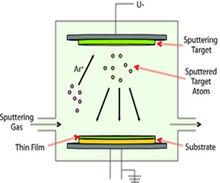
磁控濺射是由二極濺射基礎上發展而來,在靶材表面建立與電場正交磁場,解決了二極濺射沉積速率低,電漿離化率低等問題,成為鍍膜工業主要方法之一。磁控濺射與其它鍍膜技術相比具有如下特點:可製備成靶的材料廣,幾乎所有金屬,合金和陶瓷材料都可以製成靶材;在適當條件下多元靶材共濺射方式,可沉積配比精確恆定的合金;在濺射的放電氣氛中加入氧、 氮或其它活性氣體,可沉積形成靶材物質與氣體分子的化合物薄膜;通過精確地控制濺射鍍膜過程,容易獲得均勻的高精度的膜厚;通過離子濺射靶材料物質由固態直接轉變為等離子態,濺射靶的安裝不受限制,適合於大容積鍍膜室多靶布置設計;濺射鍍膜速度快,膜層緻密,附著性好等特點,很適合於大批量,高效率工業生產 。
濺射用的轟擊粒子通常是帶正電荷的惰性氣體離子,用得最多的是氬離子。氬電離後,氬離子在電場加速下獲得動能轟擊靶極。當氬離子能量低於5電子伏時,僅對靶極最外表層產生作用,主要使靶極表面原來吸附的雜質脫附。當氬離子能量達到靶極原子的結合能(約為靶極材料的升華熱)時,引起靶極表面的原子遷移,產生表面損傷。轟擊粒子的能量超過靶極材料升華熱的四倍時,原子被推出晶格位置成為汽相逸出而產生濺射。對於大多數金屬,濺射閾能約為10~25電子伏。
濺射產額,即單位入射離子轟擊靶極濺出原子的平均數,與入射離子的能量有關。在閾能附近濺射,產額只有10-5~10-4個原子/離子,隨著入射離子能量的增加,濺射產額按指數上升。當離子能量為103~104電子伏時,濺射產額達到一個穩定的極大值;能量超過104電子伏時,由於出現明顯的離子注入現象而導致濺射產額下降。濺射產額還與靶極材料、原子結合能、晶格結構和晶體取向等有關。一般說來,單金屬的濺射產額高於它的合金;在絕緣材料中,非晶體濺射產額最高,單晶其次,複合晶體最低。
濺射工藝主要用於濺射刻蝕和薄膜澱積兩個方面。濺射刻蝕時,被刻蝕的材料置於靶極位置,受氬離子的轟擊進行刻蝕。刻蝕速率與靶極材料的濺射產額、離子流密度和濺射室的真空度等因素有關。濺射刻蝕時,應儘可能從濺射室中除去濺出的靶極原子。常用的方法是引入反應氣體,使之與濺出的靶極原子反應生成揮發性氣體,通過真空系統從濺射室中排出。
澱積薄膜時,濺射源置於靶極,受氬離子轟擊後發生濺射。如果靶材是單質的,則在襯底上生成靶極物質的單質薄膜;若在濺射室內有意識地引入反應氣體,使之與濺出的靶材原子發生化學反應而澱積於襯底,便可形成靶極材料的化合物薄膜。通常,製取化合物或合金薄膜是用化合物或合金靶直接進行濺射而得。在濺射中,濺出的原子是與具有數千電子伏的高能離子交換能量後飛濺出來的,其能量較高,往往比蒸發原子高出1~2個數量級,因而用濺射法形成的薄膜與襯底的粘附性較蒸發為佳。若在濺射時襯底加適當的偏壓,可以兼顧襯底的清潔處理,這對生成薄膜的台階覆蓋也有好處。另外,用濺射法可以製備不能用蒸發工藝製備的高熔點、低蒸氣壓物質膜,便於製備化合物或合金的薄膜。濺射主要有離子束濺射和電漿濺射兩種方法。離子束濺射裝置中,由離子槍提供一定能量的定向離子束轟擊靶極產生濺射(圖1)。離子槍可以兼作襯底的清潔處理(位置1)和對靶極的濺射(位置2)。為避免在絕緣的固體表面產生電荷堆積,可採用荷能中性束的濺射。中性束是荷能正離子在脫離離子槍之前由電子中和所致。離子束濺射廣泛套用於表面分析儀器中,對樣品進行清潔處理或剝層處理。由於束斑大小有限,用於大面積襯底的快速薄膜澱積尚有困難。 電漿濺射也稱輝光放電濺射。產生濺射所需的正離子來源於輝光放電中的等離子區。靶極表面必須是一個高的負電位,正離子被此電場加速後獲得動能轟擊靶極產生濺射,同時不可避免地發生電子對襯底的轟擊。
二極濺射是最簡單的電漿濺射裝置。兩個平行板電極間加上一個直流高電壓:陰極為靶極,陽極為襯底。為使這種自持輝光放電保持穩定,除兩極板間須保持一定電壓外,極板間距和氣體壓強的大小也很重要。在兩極板間距為數厘米的正常濺射間距下,放電氣壓一般高達10帕。在這樣的氣壓下,粒子的平均自由程很短,對濺射不利。為保持更低氣壓下的濺射,可採用非自持放電,常用的是熱電子激發法。直流四極濺射就是在原有的二極濺射設備上附加一對熱燈絲和陽極組成的。從燈絲髮出的強大電子流在流向陽極的途中,使處於低氣壓的氬氣分子大量電離,從而提供足夠的離子。這可使濺射在10-1~10-2帕的低氣壓下進行。外加磁場可使電子電離氣體的效率增加。
對於絕緣體靶的濺射,必須採用高頻濺射方法。在靶極上施加高頻電壓,氣體擊穿後電漿中的電子和離子將在靶極高頻電場的作用下交替地向靶極遷移。電子的遷移率比離子高得多。頻率很高時,離子向靶極的遷移就會跟不上高頻信號的頻率變化。因為靶是絕緣的,靶極迴路淨電流必須保持為零。為此,必須在靶極表面維持一個負電勢,用以抑制電子向靶極的遷移,同時加速正離子的遷移,使流向靶極的電子數與離子數相等。正是這一負電勢加速氬離子,使絕緣靶的濺射得到維持。為使這一負電勢保持足夠的數值,靶上的高頻電壓的頻率必須足夠高。頻率過高,高頻損耗增大且難於匹配。常用的頻率約為13.56兆赫。
電漿濺射突出的問題是濺射速率低、襯底溫度升高。從靶極發出的濺射原子流為E=Sj+。式中S為濺射產額,j+為轟擊靶極的離子流密度。在S確定以後,提高濺射速率必須增加離子流密度。另外,降低襯底溫升,必須防止高能二次電子對襯底的轟擊。磁控濺射能解決這兩個問題。磁控濺射利用高頻磁控管的原理,在濺射室中引入一個與電場方向正交的磁場。在此磁場的控制下,電子局限於靶極附近並沿螺鏇形軌道運動,大大提高電子對氬原子的電離效率,增加轟擊靶極的離子流密度j+,實現快速的大電流濺射。同時,又能避免電子直接向襯底加速,降低襯底的溫升。磁控濺射有直流和高頻兩類。按結構又有同軸型、平面型和S槍等多種類型。圖2為一平面型磁控濺射裝置,圖中虛線表示磁場方向。靶極上出現不均勻侵蝕,會使磁控濺射靶材利用率降低。 離子鍍膜法將真空蒸發和濺射工藝相結合,利用濺射對襯底作清潔處理,用蒸發的方法鍍膜。襯底置於陰極,它與蒸發源之間加數百伏以至數千伏的高壓電,放電氣壓為10~10-2帕。蒸發源通過熱絲加熱進行蒸發,部分蒸發分子與放電氣體分子成一定比例,在強電場作用下激發電離並加速向襯底轟擊,而大部分中性蒸發分子不經加速而到達襯底。用此法製造薄膜,澱積速率比濺射法為高,與襯底的粘附力又比蒸發法為強。
分類
近年來具有代表性的濺射方法 有:
平衡磁控濺射
平衡磁控濺射即傳統的磁控濺射,是在陰極靶材背後放置芯部與外環磁場強度相等或相近的永磁體或電磁線圈,在靶材表面形成與電場方向垂直的磁場。沉積室充入一定量的工作氣體,通常為Ar,在高壓作用下Ar原了電離成為Ar+離子和電子,產生輝光放電,Ar+離子經電場加速轟擊靶材,濺射出靶材原子、離子和二次電子等。電子在相互垂直的電磁場的作用下,以擺線方式運動,被束縛在靶材表面,延長了其在電漿中的運動軌跡,增加其參與氣體分子碰撞和電離的過程,電離出更多的離子,提高了氣體的離化率,在較低的氣體壓力下也可維持放電,因而磁控濺射既降低濺射過程中的氣體壓力,也同時提高了濺射的效率和沉積速率。
非平衡濺射
1985年,Window和Savvides首先引入了非平衡磁控濺射的概念。不久,多種不同形式的非平衡磁場設計相繼出現,磁場有邊緣強,也有中部強,導致濺射靶表面磁場的“非平衡”。磁控濺射靶的非平衡磁場不僅有通過改變內外磁體的大小和強度的永磁體獲得,也有由兩組電磁線圈產生,或採用電磁線圈與永磁體混合結構,還有在陰極和基體之間增加附加的螺線管,用來改變陰極和基體之間的磁場,並以它來控制沉積過程中離子和原子的比例。
非平衡磁控濺射離子轟擊在鍍膜前可以起到清洗工件的氧化層和其他雜質,活化工件表面的作用,同時在工件表面上形成偽擴散層,有助於提高膜層與工件表面之間的結合力。在鍍膜過程中,載能的帶電粒子轟擊作用可達到膜層的改性目的。比如,離子轟擊傾向於從膜層上剝離結合較鬆散的和凸出部位的粒子,切斷膜層結晶態或凝聚態的優勢生長,從而生更緻密,結合力更強,更均勻的膜層,並可以較低的溫度下鍍出性能優良的鍍層。
參考書目
G.K. Wehner,G.S.Anderson and L.Maisse,Handbook of Thin Film Technology, McGraw-Hill, New York,1970.