特性
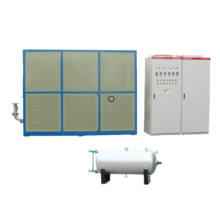
有機熱載體爐是一種以熱傳導液為加熱介質的新型特種鍋爐。具有低壓高溫工作特性。隨著工業生產的發展和科學技術的進步,有機熱載體爐得到了不斷的發展和套用。有機熱載體
爐的工作壓力雖然比較低,但爐內熱傳導液溫度高,且大多具有易燃易爆的特性,一旦在運行中發生泄漏,將會引起火災、爆炸等事故,甚至造成人員傷亡和財產損失。因此,對有機熱載體爐的安全運行和管理,必須高度重視。導熱油電加熱器是一種新型、安全、高效節能,低壓(常壓下或較低壓力)並能提供高溫熱能的特種工業爐,以導熱油為熱載體,通過熱油泵使熱載體循環,將熱量傳遞給用熱設備。
電加熱導熱油爐系統由防爆電加熱器、有機熱載體爐、換熱器(如有)、現場防爆操作箱、熱油泵、膨脹槽等組合成一個撬塊,用戶只僅需接入電源、介質的進出口管道及一些電氣接口即可使用。
功能特點
1、導熱油爐具有低壓、高溫、安全、高效節能的特點。
2、導熱油爐具有完備的運行控制和安全監測裝置,可以精密地控制工作溫度。
3、導熱油爐的結構合理、配套齊全、安裝周期短,運行和維修方便,便於鍋爐布置。
4、由於電加熱有機熱載體爐採用先進的防爆結構,可套用於工廠Ⅱ區防爆,防爆等級可達C級。
工作原理
導熱油爐的也叫有機熱載體爐,俗稱導熱油爐鍋爐,官方名稱為熱油爐。其是以煤、油、氣為燃料,以導熱油爐為循環介質供熱的新型熱能設備,導熱油爐指載熱工質為高溫導熱油爐(也稱熱煤體、熱載體)的新型熱能轉換設備,通常也用“MW”(兆瓦)表示爐的容量,舊單位也用“萬千瓦/時”或“萬大卡/時”,即“104kcal/h”表示,導熱油爐的優勢在於“高溫低壓“、運行平穩而被廣泛運用。
導熱油爐的原理:是以煤、重油、輕油、可燃氣體其他可燃材料為燃料,導熱油爐為熱載體。利用循環油泵強制液相循環,將熱能輸送給用熱設備後,繼而返回重新加熱的直流式特種工業爐。廣泛用於如石化、紡織、印染、塑膠、橡膠、食品加工、木材加工、瀝青加熱、紙箱生產、蔬菜脫水、烤漆、鑄造砂模烘乾等。導熱油爐是一種以熱傳導液為加熱介質的新型特種鍋爐。具有低壓高溫工作特性。隨著工業生產的發展和科學技術的進步,導熱油爐得到了不斷的發展和套用。
由於它具有高溫(320℃以上)低壓(0.3-0.5MPa)的優點,且其供熱溫度可精確控制,因此可取代原蒸汽鍋爐供熱。同時該設備不需要水處理設備並且無蒸汽鍋爐的跑、冒、滴、漏等熱損失,所以其一次性投資省,運行費用低,是一種安全、高效、節能的供熱設備。
導熱油爐鍋爐是基於強制循環的設計思維而開發的直流式特種導熱油爐。封閉循環供熱,與大氣相通,可延長鍋爐的使用壽命,液相輸送熱能,熱損失小,節能效果顯著,環保效果好。由於採用盤管式結構,因此,受熱面充足,使其具有較高的熱效率。
導熱油爐鍋爐,顯著的特點是逆流換熱,燃燒排煙溫度與熱導油出口溫差在30℃以下。導熱油爐其卓越的結構,主要是在較低的壓力下運行,獲取450℃以下的工作溫度,具有低壓高溫的特點。
工作流程
導熱油加熱器是將電加熱器直接插入有機載體(導熱油)中直接加熱,並通過高溫油泵進行強制性液相循環將加熱後的導熱油輸送到用熱設備,再由用熱設備出油口回到熱油爐加熱,形成一個完整的循環加熱系統。導熱油加熱器採用數顯溫控儀控溫,具有超溫報警、低油位報警、超壓力報警功能,它是化工、紡織、印染、食品、塑膠、薄膜等行業中一種高效節能供熱設備,
導熱油加熱器的工作原理和流程。對於導熱油加熱器的原理:我們強調熱量是由浸入導熱油的電加熱元件產生和傳輸的,以導熱油為介質,利用循環泵,強制導熱油進行液相循環,將熱量傳遞給用一個或多種用熱設備,經用熱設備卸載後,重新通過循環泵,回到加熱器,再吸收熱量,傳遞給用熱設備,如此周而復始,實現熱量的連續傳遞,使被加熱物體溫度升高,達到加熱的工藝要求。導熱油加熱器主要運用於:石油及化學工業、油脂工業、合成纖維工業、紡織印染工作、非織造工業、飼料工業、塑膠及橡膠工業、造紙工業等。
導熱油加熱器若出現異常怎么辦
異常1: 當循環泵的電流比正常值低時,導致循環泵的效率和流量下降。
原因:有可能是供熱管線積垢堵塞造成的。
處理:清洗消堵。
異常2:循環泵壓不改變,電流升高而流量卻下降。
原因:有可能是熱傳導液變質,粘度增加造成的。
處理:及時更換或再生導熱油,同時注意排氣。
異常3:循環泵電流值減小,出口泵壓回零,說明泵空轉不供油。
原因:可能是導熱油汽化所致,查明汽化原因採取相應的措施。
處理:若是因過濾器堵塞而使循環泵抽空,應立即開旁通清洗過濾器;若是因新增加的熱傳導液含水或水分解的氣體在系統內未排除,則應立即打開放空閥排氣。
異常4:液相熱載體爐出口溫度低,供熱量不足,而排煙的溫度超過300℃。
原因:引風不足使燃燒強度不夠,造成排煙溫度低。
處理:及時吹灰。著重檢查爐後部出渣機水封、除塵器出灰口等處是否封閉好,有無冷風大量漏入。
異常5:過濾器前後壓差增加,泵入口壓力下降時,
原因:可能是濾網阻塞。
處理:開通旁路,將過濾器拆卸清洗。
異常6:爐排停止轉動。
原因:鏈條太松,與鏈輪嚙合不好導致,或者是因鏈輪磨損嚴重,與鏈條連線不良造成的。
處理:調整兩側的調整螺絲,將爐排拉緊,若仍不能正常轉動,則需要調換鏈輪。
異常7:爐排卡住。
原因:爐排片折斷或銷子脫落。煤中有金屬夾雜物將爐排卡住;爐排片拱起;擋渣器(老鷹鐵)尖端下沉,將爐排卡住。
處理:用板手倒轉爐排清除雜物,更換斷裂爐排片後再啟動,如啟動後再卡住,則停止轉動後,詳細檢查原因
原因 :
加熱特點
1、加熱速度快,傳熱效率高,不易結垢。
2、可對油品定量加熱,需要多少加熱多少。
3、油品不會出現局部高溫、炭化,保證了油品質量及加熱器傳熱效率。
4、油罐內出油口溫度最高,保證了倒出油品流動性。
5、避免了反覆對罐內油品進行加熱,保證了油品色度、降低了油品處理的成本。
6、使用壽命長,耐腐蝕、耐高溫、耐高壓、防結垢功能,極大的提高了換熱器整體性能。
7、工藝結構設計先進,保證了油品順利流出及較好的“抽罐底”作用。
8、可實現自動化控制,可根據油品的進出溫度及倒油流量控制蒸汽進給量。
9、結構緊湊,安裝與維修方便,不會因為加熱器的安裝而影響罐體的安全。與U型管換熱器比較,在同等換熱面積情形下:渦流熱膜換熱器的外型尺寸,僅為U型管換熱器外形尺寸的二分之一左右。
10、相對於電加熱方式,更安全,加熱更溫和,對油品品質影響更小。
據【石油化工技術推廣中心】介紹,此新型油罐加熱技術已經獲得多項國家專利,已經在中石油多個油氣儲運單位得到套用。
性能
1、能在較低的運行壓力下<0.5Mpa,獲得較高的工作溫度≤320℃,降低了用熱設備的受壓等級,可提高系統的安全性。
2、加熱均勻柔合,溫度調節採用PID自整定智慧型控制,控溫精度高≤±1℃,可滿足高工藝標準的嚴格要求。
3、體積小,占地少,可安裝在用熱設備附近,不需專設鍋爐房,不需要設專人操作,可降低設備投資及運行費用,回收投資快。
套用行業
石油及化學工業:聚合、縮合、蒸餾、熔融、脫水、強制保溫。
油脂工業:脂肪酸蒸餾、油脂分解、濃縮、酯化、真空臭等反應釜控溫,反應釜加熱。
合成纖維工業:聚合、熔融、紡絲、延伸、乾燥。
紡織印染工作:熱定型輥筒加熱、烘房加熱、熱容染色。
非織造工業:無紡布。
飼料工業:烘乾。
塑膠及橡膠工業:熱壓、壓延、擠壓、硫化成型。
造紙工業:乾燥、波紋紙加工。
木材工業:多合板、纖維板加壓成型、層壓板加熱,熱壓板加熱,油壓機控溫,木材幹燥。
建材工作:石膏板烘乾、瀝青加熱、混凝土構件養護。
機械工業:噴漆、印花烘乾。
食品工業:烘箱加熱,夾層鍋加熱。
空調工業:工業廠房及民用建築採暖。
築路工業:瀝青熔化、保溫。
製藥工業:烘乾。
輕工業:生產油墨、洗衣粉。
.加熱功率計算公式
1.加熱功率計算公式,選型的計算方法特殊的情況需進行計算:
A、求加熱器功率/冷卻功率KW=W×△t×C×S/860×T
W=控溫設備重量或冷卻水(KG)
△t=所需溫度和起始溫度之間的溫差。
C=比熱油(0.5),鋼(0.11),水(1),塑膠(0.45~0.55)
T=加溫至所需溫度的時間(小時)
B、求泵的大小,需了解客戶所需泵浦流量和壓力(揚程)
P(壓力Kg/cm2)=0.1×H(揚程M)×α(傳熱媒體比重,水=1,油=0.7-0.9)
L(媒體所需流量L/min)=Q(控溫設備所需熱量Kcal/H)/C(媒體比熱水=1油=0.45)×△t(循環媒體進出控溫設備的溫差)×α×60
操作使用管理
第一條電加熱導熱油爐的操作人員,應經過電加熱導熱油爐方面知識的培訓,並經當地鍋爐安全監察機構考核發證。
第二條電加熱導熱油爐使用單位,必須制訂電加熱導熱油爐操作規程。操作規程應包括電加熱導熱油爐啟動、運行、停爐、緊急停爐等操作方法和應注意事項。操作人員必須按操作規程進行操作。
第三條電加熱導熱油爐範圍內的管道應採取保溫措施,但法蘭連線處不宜採用包復措施。
第四條電加熱導熱油爐在點火升壓過程中,應多次打開鍋爐上的排氣閥,以排淨空氣、水及有機熱載體混合蒸汽。對於氣相爐,當有機熱載體的溫度與壓力符合對應關係後,應停止排氣,進入正常運行。
第五條有機熱載體必須經過脫水後方可使用。不同的有機熱載體不宜混合使用。需要混合使用時,混用前應由有機熱載體生產單位提供混用條件和要求。
第六條使用中的有機熱載體每年應對其殘碳、酸值、粘度、閃點進行分析,當有兩項分析不合格或熱載體分解成份的含量超過10%時,應更換熱載體或對熱載體進行再生。
第七條電加熱導熱油爐受熱面應定期進行檢查和清洗,應將檢查和清洗情況存入鍋爐技術檔案。
第八條電加熱導熱油爐安裝或重大修理後,在投入運行前應由使用單位和安裝或修理單位進行1.5倍工作壓力的液壓試驗,對於氣相爐應按第15條進行氣密性試驗。合格後才能投入運行。液壓試驗與氣密試驗時,當地鍋爐安全監察機構應派人參加。
第九條鍋爐房應有有效的防火和滅火措施法
導熱油加熱器調試步驟
調試:
調試是進一步考證安裝質量、系統工作性能和熟悉操作要領,保證正常運行的重要工作,應有管理人員、技術人員、操作人員共同參加,在設備初次啟動後的運行中,應對設備工況進行測定和記錄,以保證今後系統的正常運行。調試工作分冷態和熱態兩個步驟進行。
1.冷態調試:
①目的:
檢查各單元設備的運轉正常與否。
檢查冷態條件下的系統運行正常與否。
使操作工作熟悉和掌握操作要領。
②要求:
所有電機轉向正確,設備負荷正常,動作正確連續運行2小時以上。
循環油泵在水壓試驗前應進行冷態調試。
做好調試運行記錄,及時排除可能出現的故障。做好調試前的一切準備工作。
③冷態調試步驟:
檢查所有設備及管線安裝是否符合圖紙要求。
檢查系統試壓沖掃是否符合要求。
檢查電器系統及控制儀表是否裝妥。
熱油泵軸承箱及其它傳動機構根據要求注入潤清油或潤滑脂。
將各運動機構單機試運轉,檢查運轉方向是否正確,聲音是否正常。
調節系統各個閥門,為注油、試車做好準備。
注油泵向高位膨脹槽注油。
啟動熱油循環泵。
觀察熱油循環泵進出口壓力、爐本體壓降及進出口油溫,排煙溫度等儀表的工作顯示是否正常。
冷態運行連續四小時以上,如無異常現象,方可進行熱態調試。
2.熱態調試
熱態調試應包括用熱設備在內的運行操作,請按表一進行。
⑴.初升溫階段:
啟動熱油循環泵,進行冷爐點火。冷爐點火後,以每10℃/時的升溫速度進行升溫。直到90~95℃。因冷爐時油的粘度大,受熱面管內流速較低,管壁油膜較厚,傳熱條件差,容易使局部油膜溫度過高。
⑵.脫水階段:
90~110℃範圍內是驅趕系統內殘存水份和有機熱載體所含微量水份階段。升溫速度控制在0~5℃/時的範圍內,此時間的長短視脫水情況而定。當高位膨脹槽放空管處排氣量較大,底部有水擊聲,管道振動加劇,各處壓力表指針擺動幅度較大時。必須停止升溫,保持恆溫狀態,必要時可打開爐門減弱燃燒。
這個階段的長短視殘存水份的多少和熱載體的質量而定。決不能盲目加快升溫脫水速度,因一旦系統內水份劇烈蒸發汽化,體積將膨脹1000餘倍,不僅引起“突沸”,使油位急劇膨脹大量噴出,而且可能使受壓元件破裂釀成事故。
⑶.再升溫階段:
當有機熱載體爐和管道中響聲變小,熱油循環泵不再出現抽空現象(泵出口壓力降至0.1MPa以下,有沉重的喘氣聲)時,可以5℃/時的速度再升溫,但不能超過120℃,直到放空管不在有汽體排除為止。
⑷.脫輕組分(脫氣)階段:
脫水過程完成後,以30℃/時的速度再升溫,但仍應注意可能會有殘餘水份蒸發,隨時停止升溫。當溫度達到210~230℃時要停下來,這時主要脫去熱載體中的輕組分。在液相供熱的熱載體中的輕組分以氣相存在,會造成“氣阻”使熱油循環泵壓力不穩,流量下降或中斷。
脫輕組分過程的長短視殘熱載體的質量而定。當放空管不在有氣體排出,熱油循環泵壓力穩定,即可以0~10℃/時的速度再升溫。
⑸.再升溫階段:
從210直到熱載體工作溫度是在脫氣結束後以40℃/時的速度再升溫,,這時候應全面考察各檢測儀表的指示、動作是否靈敏、準確。各配套輔機、附屬設備工作是否正常。全面檢查熱載體爐和整個供熱系統工作是否正常。
3.注意事項:
①.壓差不穩定時,不得投入使用。
②.停爐時,油溫應降至80℃以下時,熱油循環泵方可停運。
③.高溫狀態時要確保導熱油循環良好。
④.正常工作時,高位槽內導熱油保持高液位,貯油槽內導熱油應處於低液位。
⑤.應按規定對各機械潤滑點注油。
⑥.出油溫度不得超過導熱油的允許工作溫度。
⑦.不同品種導熱油一般不得混用。
⑧.冷爐點火必須先開熱油循環泵後再點火,
⑨.點火升溫過程中脫去的水分以水蒸汽形態經膨脹管進入膨脹槽,其中一部分以氣體從排空管排出,另一部分凝成水分沉入槽底,要避免這部分水分再次進入循環系統,在升溫過程中應定期打開膨脹槽底部排污管,放出冷凝水。
⑩.當熱載體升溫到200℃以上時,應對熱載體爐和整個供熱系統進行全面檢查,並對所有的聯結螺栓進行一次熱緊,消除因膨脹不均引起的泄漏。
六.壓力試驗:
在整個供熱系統全部按標準安裝完畢後進行試壓,液相熱載體爐以1.5倍的工作壓力試壓,使用試驗介質不可以用水,因為水壓試驗不易將水排淨,形成安全運行隱患。試壓時氣溫應大於5℃以上,在試驗壓力下保持20分鐘,在降至工作壓力時檢查各聯結部位有否泄露現象,若有應及時整修完畢後重新做壓力試驗。
七.煮爐:
⑴.煮爐的目的是在有機熱載體爐內加入NaOH和Na3Po4.12H2O進行化學處理,採用鹼性煮爐,使金屬表面形成護膜,保把管內油污、鐵鏽除去以減少有機熱載體的脫水時間。,用磷酸三鈉(Na3PO4.12H2O)和氫氧化鈉(NaOH)配製成溶液後加入爐內煮沸1-2天。
⑵.藥品應溶解成溶液後方可加入爐內,配製和加入藥液時,應採取安全措施。
⑶.用專用清洗液YDJ配製以0.5-0.7%的氫氧化銷加入爐內煮沸1-2天,待爐冷卻至70℃以下時從排污閥排出,並用清水沖洗乾淨。煮爐合格後沖洗乾淨後再用壓縮空氣將鍋內管道內滯留水分吹乾。
⑷.煮爐後應符合下列要求:
①盤管、出、回油集管內壁應無油污。
②擦去附著物後金屬表面應無銹斑。
煮爐工作應可在烘爐後期同時進行。
八.升火與升溫:
有機熱載體爐具備投入運行條件後才可點火升溫,點火升溫必須嚴格按操作規程進行。
1、點火前的準備:
⑴、熱載體爐內殘存水分已放盡吹乾,爐內無雜物所有孔類已密閉,使用填料符合熱載體介質要求。
⑵、所有安全附屬檔案的保護裝置已安裝驗收合格。
2、介質化驗及冷態循環:
⑴、有機熱載體爐內所使用的熱載體必須是合格品,使用溫度必與供熱條件一致。鍋爐出口溫度至少比熱載體允許使用溫度低30-40℃,否則會發生分解變,提前失效。
該爐選擇的有機熱載體為“YD-320”型,在20℃時的其性能參數如下:
①.密度1022kg/m3:②.粘度20厘沲:
③.導熱係數0.4342KJ/m.h℃:④.比熱1.7899KJ/Kg℃:
⑤.普郎特數229.5:⑥.酸值0.02mgKOH/g:⑦.殘碳≤0.05w%:
⑧.膠質53mg/100ml:⑨.總硫含量0.15%:
⑩.最高允許油膜溫度330℃:⑾.外觀為淡黃色透明液體:
⑿.毒性為低毒:⒀.閃點≥110℃:
⑵、裝油:將化驗合格的熱載體用注油泵往鍋爐內注油,在注油泵向系統注油時,應再檢一遍爐體內所有供熱系統的閥門同時逐一打開排污閥排除空氣,直至有油流時關閉,當高位膨脹槽液位計出現油時停止注油然後啟動循環泵進行冷油循環。
⑶、冷油循環:冷油循環的目的是試驗整個供熱系統是否有阻現象,設備閥門等處有無滲漏。每台油泵要輪轉流啟動冷油在系統內循環不少於6小時。
⑷、清洗過濾器:冷油循環中系統內一些金屬物及雜質沉積物等隨著冷油在油泵前的過濾器中截流,冷循環結束後拆開過濾器徹底清掃。
點火升溫及脫水:
點火升溫及脫水過程參照熱態調試章節
運行指標和調節,有機熱載體使用時,其出口溫度低於製造提供的最高使用溫度20-40℃其調節指標主要靠近出口溫度,當進出口溫差減小時(回油溫度高)應相應減弱燃燒。當回溫降低時應強化燃燒。任何時候決不能盲目提高出口溫度的方法來增加供熱量。當出口溫度超溫起溫儀表報警時應及時停爐清洗。
安全要點
導熱油爐的主要危險是火災。導熱油一旦從導熱油爐供熱系統泄漏,由於自身溫度很高,又接觸火焰或接近火焰,就會被點燃或自燃,造成火災。另外,導熱油爐也會因導熱油帶水等原因,而發生爆炸事故。防範導熱油爐事故必須從設備和介質兩方面同時著手,一是使設備具有足夠的強度和嚴密性,不破不漏;二是使導熱油在受熱中不過熱,不變質,正常流動與換熱。主要有:
1、導熱油的供貨單位應提供導熱油的理化性能數據且應符合國家標準要求。導熱油在使用中應每年化驗一次,發現問題及時更換或再生。
2、導熱油爐在啟動中應充分排放空氣、水蒸汽和輕組分。在運行中應維持導熱油足夠高的流速,防止斷電停泵,以免導熱油過熱結焦或積碳。過濾器應定期清理。
3、導熱油爐及供熱系統的安全裝置應齊全完好,超溫、超壓保護裝置應靈敏可靠。
防爆知識
導熱油爐的工作壓力雖然比較低,但爐內熱傳導液溫度高,且大多具有易燃易爆的特性,一旦在運行中發生泄漏,將會引起火災、爆炸等事故,甚至造成人員傷亡和財產損失。因此,對有機熱載體爐的安全運行和管理,必須高度重視。有機熱載體爐的工作壓力雖然比較低,氣導熱油爐但爐內熱傳導液溫度高,且大多具有易燃易爆的特性,在幾乎常壓的條件下,可以獲得很高的操作溫度。即可以大大降低高溫加熱系統的操作壓力和安全要求,提高了系統和設備的可靠性。由於它具有高溫(320℃以上)低壓(0.3-0.5MPa)的優點,且其供熱溫度可精確控制,因此可取代原蒸汽鍋爐供熱。
導熱油加熱爐供熱溫度可達350℃,熔鹽爐供熱溫度可達530℃。節約水資源:可替代水資源貧缺的地區以水為介質的蒸汽鍋爐供熱,且在寒冷地區不易凍結。因為燃油燃氣導熱油爐燃燒後均不產生燃料灰渣,故燃油燃氣導熱油爐無須排渣舉措措施。噴入爐內的油氣假如與空氣在一定範圍內混合或熄滅,就輕易爆炸。導熱油爐的導熱油與另一類高溫傳熱介質熔鹽相比,在操作溫度為400℃以上時,熔鹽較導熱油在傳熱介質的價格及使用壽命方面具有絕對的優勢,但在其它方面均處於明顯劣勢,尤其是在系統操作的複雜性方面。
爐管排列採用即不窩氣,又不存水的結構,並加裝頂盤管與同類設備相比節能5%左右.使用中阻力小、流速大、壓力穩;安全耐用。燃油燃氣導熱油爐均需採用自動化的燃燒與控制系統。燃油燃氣導熱油爐結構緊湊,小型的導熱油爐本體及其透風、給水、控制與輔助設備均設定在一個底盤上,大中型的也可組裝出廠。
化學清洗
化學清洗有以下好處:
1、有效清除管壁上固化或半固化油垢。
2、有效清除導熱油裂解碳化形成的中、高溫積炭。
3、防止導熱油老化失效,提高傳熱效率,降低能耗,節約運行成本。一般情況下可節約能源5%以上。
4、防止爐體管道局部失效,延長使用壽命。
5、保證產品質量和生產任務。
導熱油爐清洗劑主要通過鹼、有機溶劑與表面活性劑(簡稱SAA)這3種基本成分的組合,並加入絡合劑、氧化劑、緩蝕劑、吸附劑與防沉積劑等其他助劑,再通過加溫、機械沖刷等作用,最終達到清除系統中焦垢的目的。清洗劑清焦作用是通過表面活性劑的增溶、濕潤、吸附、乳化和分散來實現的。以下是奇聯導熱油爐專家綜合了國內外的導熱油爐化學清洗技術列出的幾個方案:
①鹼洗和酸洗兩步法工藝:排出導熱油→蒸汽吹掃滯油→鹼性清洗劑→水沖洗→酸洗→鈍化→完畢。原理:鹼性水基清洗劑對油質中溫積炭處理效果良好,但處理後試件內壁仍殘留有緻密石墨化高溫積炭層,因此須經過進一步的酸洗除去,以避免殘留碳層影響導熱油質量及傳熱效果。鹼洗、酸洗兩步法清洗工藝用於熱媒爐及管道積炭,具有清洗率高、清洗溫度較低、無毒、清洗成本低的優點。該法雖能清除垢層,但工藝繁多,存在著酸鹼腐蝕,縮短機器壽命,會造成二次污染,並且要在導熱油爐停車的情況下進行,影響生產。
②溶解清洗法工藝:排出導熱油→蒸汽吹掃滯油→有機溶劑清洗液(有機溶劑+SAA+助劑)清洗→鈍化。原理:由於焦炭垢是一種以有機物為主的成分複雜的混合污垢,與金屬表面的粘附主要是范德華力的物理吸附,採用“溶解洗滌法”,將焦油溶於有機溶劑中,隨有機物的溶解而自然除去。該清洗劑的清洗能力相當強,受溫度影響不是很大。該清洗劑清洗後經澄清過濾處理,再添加適量表面活性劑和助劑可重複使用。殘渣可摻入煤中燃燒,既降低成本又減少環境污染。但該清洗劑具揮發性,安全性低,成本高。
③複合清洗劑清洗法工藝:排出導熱油→蒸汽吹掃滯油→清洗液循環清洗。原理:複合清洗劑主要由數種表面活性劑在助洗劑的協同作用下首先在油垢表面吸附使其潤濕、膨脹而後清洗劑滲透到油垢間隙使油污物在複合清洗劑作用下逐漸捲縮成膠束不斷乳化經泵連續循環沖刷可使分散乳化的油污物脫離傳熱表面。此清洗劑既能有效破碎、分散積炭也能高效地溶解有機碳氫化合物工藝簡單基本對設備無腐蝕。但此法會造成二次污染且須在停車的情況下進行清洗影響生產。
④有機添加劑清洗法工藝:只需在運行著的導熱油中加入添加劑就可使積炭剝落再經澄清過濾處理除油渣。原理:此添加劑利用相似相溶原理洗脫焦油垢或使焦油垢降解防止導熱油的變質。此法在不停車的情況下進行清洗添加劑能耐260℃以上的高溫溶於導熱油不影響導熱油的物性用量不能超過導熱油的千分之一。使用時導熱油爐與管道不用降溫不影響生產。此法工藝簡單節約成本除去油渣後的導熱油可再利用不污染環境是化學清洗法清洗導熱油管道的趨勢。
應急措施
導熱油在加熱系統中進行加熱循環,一旦發生故障,必定要影響生產,甚至發生事故,因此必須及時分析發生故障的原因,並儘快排除故障,恢復系統循環及生產。
導熱油系統易發生的故障及應急處理方法
1、膨脹槽溢油
膨脹槽是導熱油加熱系統中的重要設備之一,其主要功能是克服導熱油因加熱溫度升高體積膨脹及系統超壓的安全裝置,也起著補充壓頭、平衡系統、排放殘餘水分及低沸點物等作用。因此,當加熱循環系統內導熱油壓力超過它與膨脹槽的壓力差時,系統中的油汽混合物就會衝出膨脹槽,造成溢油現象,而溢油很可能引起火災的危險和燙傷生產人員。
所以說,引起溢油的根本原因是系統中的油溫劇變而發生油位的急劇上升,油壓也隨之急劇升高,使系統失去平衡。下面幾種情況可能發生溢油現象:
①開車時脫水升溫速度過快,由此引起水蒸汽及低沸點揮發物大量衝擊膨脹槽造成溢油。
防止的辦法:嚴格按升溫曲線的要求進行升溫,並根據壓力波動及排汽的情況調整升溫速度;
②多台用熱設備頻繁交替使用,當溫度高的導熱油急速大量流入低溫系統並與冷油接觸,冷油吸熱後低沸點組分大量汽化蒸發,同時體積發生較大的膨脹引起溢油。
解決的辦法:當低溫用熱設備投入運行時,閥門應慢慢打開而逐步加大,使冷熱油的熱交換逐步平衡就可避免溢油;
③因熱油泵發生故障或是系統漏油,或因突然停電造成系統循環中斷,這時,因爐膛中溫度很高,瞬間油溫隨之迅速上升,使原來導熱油中沸點較高不易揮發的組分也大量汽化蒸發,這股汽和油的混合物急速直衝膨脹槽而造成溢油。
解決的辦法:迅速停止加熱,立即打開膨脹槽通往熱油爐的匯油閥,使高位膨脹槽的導熱油徐徐流過爐膛中的爐管並流入低位貯油槽。與此同時,應迅速排除故障使系統恢復正常循環。
2、熱油系統中電流及泵壓波動幅度較大,高位膨脹槽的底部及熱油管道發出汽錘聲。這是因為導熱油中有水分汽化蒸發造成,查出原因及時排除水分或更換新油。
3、導熱油系統壓差不穩發生的異常與處理:
①系統中過濾器堵塞產生阻力,應清洗過濾器;
②導熱油流量下降,熱油泵故障或系統管道堵塞,應分別檢查並予以排除;
③導熱油長期運行後低沸點組分汽化蒸發或漏油,使系統中的循環油量不足,應堵漏或添加新油新
④導熱油變質,粘度上升,流量下降,要進行必要的添加或更
⑤熱油爐進出口溫度差超過規定值,而油溫又達不到工藝要求:
(a)熱油系統及導熱油中水分及低沸沸點易揮發物質未脫淨,只要脫淨後溫度就會上去;
(b)熱油輸送管線太長,保溫又不好,應加強保溫措施或更換性能好的保溫材料;
(c)超負荷運行應對用熱設備進行調整;
(d)導熱油裂解或氧化變質,粘度、膠質、殘炭增加,流動性變差,熱效率下降,應取樣測試技術指標變化情況添加或更換新導熱油。
設計和計算
一、電加熱的設計和計算,通常按以下三 部分進行:
1、計算從初始狀態按要求在規定的時間內加熱至設定溫度所需要的功率。
2、計算維持介質溫度不便的前提下,實際工作中所需要的功率。
3、加熱器型號和數量的選擇,總功率取以上兩種功率的最大值,並考慮1.2係數。
公式:1、初始維持加熱所需要的功率Kw=(C1M1△T+C2M2△T)/863/H+P/2
P最終溫度下容器的散熱量單位:千瓦
H為初始溫度加熱至最終所需要的時間單位:小時
M1、M2分別為容器和介質的質量,單位:千克
C1、C2分別為容器和介質的比熱,單位:千卡/(千克℃)
△T為最終溫度和初始溫度之差,單位:℃。
2、維持介質溫度所需要的功率:Kw=C2M3△T/863+P
M3為每小時增加的介質單位:千克/小時。
二、為了方便人們的設計,以下提供了一些速算公式
1、靜止水、油加熱所需功率(不考慮容器熱耗)Kw=CM△T/863/H
C:比熱千卡/(千克.℃)
M:質量千克△T
H:時間:小時。
2、流動的水、油加熱所需功率(不考慮容器熱耗)Kw=CF△T/14
C:比熱千卡/(千克.℃)
M:流量千克/分△
T:溫差℃。
3、通道式空氣加熱(常壓)Kw=F△T/40
M:流量米3/分
△T:溫差℃
40:係數千瓦.分(米3/分)
Vout=Vin(Tout+273)/(Tin+273)
Vin,Vout:通道進出口流速
Tin,Tou:通道進出口溫度℃。
功率計算方法
模溫機選型的計算方法特殊的情況需進行計算:
A、求加熱器功率或冷凍功率 KW=W×△t×C×S/860×T
W=模具重量或冷卻水 KG
△t=所需溫度和起始溫度之間的溫差。
C= 比熱 油(0.5),鋼(0.11),水(1),塑膠(0.45~0.55)
T=加溫至所需溫度的時間(小時)
B、求泵的大小
需了解客戶所需泵浦流量和壓力(揚程)
P(壓力Kg/cm2)=0.1×H(揚程M)×α(傳熱媒體比重,水=1,油=0.7-0.9)
L(媒體所需流量L/min)=Q(模具所需熱量Kcal/H)/C(媒體比熱水=1 油=0.45)×△t(循環媒體進出模具的溫差)×α×60
2.冷凍機容量選擇
A、Q(冷凍量Kcal/H)=Q1+Q2
Q1(原料帶入模具的熱量Kcal/H)=W(每小時射入模具中原料的重量KG)×C×(T1-T2)×S(安全係數1.5~2) T1 原料在料管中的溫度;T2 成品取出模具時的溫度 ;Q2 熱澆道所產生的熱量Kcal/H
B、速算法(有熱澆道不適用)
1RT=7~8 OZ 1OZ=28.3g(含安全係數)
1RT=3024Kcal/H=12000BTU/H=3.751KW
1KW=860 Kcal/H 1 Kcal=3.97BTU
3、冷卻水塔選用=A+B
A、射出成型機用
冷卻水塔RT=射出機馬力(HP)×0.75KW×860Kcal×0.4÷3024
B、冷凍機用
冷卻水塔RT=冷凍機冷噸(HP)×1.25
選擇模具溫度控制器時,
以下各點是主要的考慮因素;
1.泵的大小和能力。
2.內部喉管的尺寸。
3.加熱能力。
4.冷卻能力。
5.控制形式。
從已知的每周期所需散熱量我們可以很容易計算冷卻液需要容積流速,其後再得出所需的正確冷卻能力,模溫控制器的製造商大都提供計算最低的泵流速公式。表4.1在選擇泵時是很有用,它準確地列出了不同塑膠的散熱能力。
以下決定泵所需要提供最低流速的經驗法則:
若模腔表面各處的溫差是5℃時,
0.75gal/min/kW @5℃溫差或是
3.4151/min/kW @5℃溫差
若模腔表面各處的溫差是1℃,則所需的最低流速需要按比例乘大五倍即是3.75gal/min/kW 或是 17.031/min/kW。為了獲得產品質量的穩定性,很多注塑公司都應該把模腔表面的溫差控制在1-2℃, 可 是 實 際 上其中很多的注塑廠商可能並不知道這溫差的重要性或是認為溫差的最佳範圍是5-8℃。
計算冷卻液所需的容積流速,應使用以下的程式:
1.先計算栽一塑膠/模具組合的所城要排走的熱量:若
以前述的PC杯模為例,則實際需要散去的熱量是:
一模件毛重(g)/冷卻時間(s)=208/12=17.333g/s
PC的散熱率是=368J/g或是368kJ/kg
所以每周期需要散去的熱量=368×17.33/1,000=6.377kW
2.再計算冷卻所需的容積流速:
按照上述的經驗法則若模腔表面的溫差是5℃時,流速=6.377×0.75=4.78gal/min或是=6.377×3.41=21.751/min 若模腔表現的溫差是1℃則流速=4.78×5=23.9gal/min或是=21.75×5=108.731/min
3.泵流速的規定
為了得到良好的散熱效果,泵的流速能力應較計算的結果最少大10%,所以需使用27gal/min或是120/min的泵。
4.泵壓力的規定;
一般模溫控制器的操作壓力在2-5bar(29-72.5psi),由於在壓力不足的情況下會影響冷卻液的容積流速(流動的阻力產生壓力損失),所以泵的壓力愈高,流速愈穩定。
對於冷卻管道很細小的模具(例如管道直徑是6mm/0. 236in),泵的壓力便需要有10bar(145psi)才可提供足夠的散熱速度(即是冷卻液速度)。
大體上冷卻液的容積液速要求愈高,管道的直徑愈少則所需要的泵輸出壓力愈大。所以在一般套用模溫控制器的壓力應超過了3bar(43.5psi). B、加熱能力
圖4.8是典型的加熱計算表,提供了就模具重所需要的加熱量。圖4.8的計算用法下:
1.縱軸代表著模具的重量。
2.橫軸代表著模具升溫至所需溫度的熱量,單位是kW/hr。
3. 37℃-121℃的各溫度斜線提供了模具重量和模溫控制器的發熱能力在相應溫度下的關係。
例如我們可以從圖查知:
1.把重量500kg的模具升溫至50℃所 需的加熱能力是3.3kW/hr。
2.把重700kg的模具升溫至65℃所需的別熱能力是6.5kW/hr。
總的來說,加熱能力愈強,則所需的升溫時間,便相應地減少了(加熱能力雙倍,升溫時間減少)。往往就是因為模溫控制器的能力太低,引致模具不能達到最佳的溫度狀態。欲想知道模溫控制器實際表現,我們可以比較它的實際的和計算的模具升溫時間。
加熱功率 | 加熱器尺寸 | 膨脹槽 尺寸 |
6~18KW | Φ150*1200 | Φ300*400 |
18~30KW | Φ150*1400 | Φ300*400 |
36KW | Φ200*1400 | Φ400*500 |
45KW | Φ200*1400 | Φ400*500 |
54KW | Φ150*1400*2段 | Φ400*500 |
60KW | Φ200*1400*2段 | Φ400*500 |
72KW | Φ200*1400*2段 | Φ400*500 |
81KW | Φ200*1400*2段 | Φ500*600 |
90KW | Φ250*1500*2段 | Φ500*600 |
100KW | Φ250*1600*2段 | Φ600*700 |
120KW | Φ300*1600*2段 | Φ600*700 |
140KW | Φ300*1600*2段 | Φ700*800 |
160KW | Φ300*1800*2段 | Φ700*800 |
180KW | Φ300*1800*2段 | Φ700*800 |
200KW | Φ300*1800*2段 | Φ700*800 |
240KW | Φ300*1800*2段 | Φ700*800 |
260KW | Φ300*1800*2段 | Φ700*800 |
280KW | Φ350*1800*2段 | Φ700*800 |
300KW | Φ350*1800*2段 | Φ800*1000 |
320KW | Φ350*1800*2段 | Φ800*1000 |
340KW | Φ350*1800*2段 | Φ800*1000 |
360KW | Φ350*1800*2段 | Φ800*1000 |
380KW | Φ350*1800*2段 | Φ800*1000 |
400KW | Φ350*1800*2段 | Φ800*1000 |
450KW | Φ400*1800*2段 | Φ1000*1200 |
500KW | Φ350*1800*3段 | Φ1000*1200 |
600KW | Φ350*1800*3段 | Φ1000*1200 |
700KW | Φ350*1800*3段 | Φ1000*1200 |
800KW | Φ400*1800*3段 | Φ1000*1200 |
900KW | Φ400*1800*3段 | Φ1000*1200 |
1000KW | Φ450*1800*3段 | Φ1000*1200 |
選型方法
反應釜導熱油加熱器溫度控制機,反應釜導熱油加熱器設備的選型參數:
1、反應釜的大小;
2、反應釜的重量;
3、反應釜夾套或盤管的容積;
4、反應釜內的物料的參數:密度、比熱、粘度等
5、反應釜內物料所需要達到的溫度,及加熱到這個溫度的時間要求;
6、反應釜夾套的進出口是多大;
7、是否需要製冷或防爆;
8、反應釜的圖紙是否可以提供;
9、反應釜工作的工藝要求;
10 反應釜夾套或盤管能承受的多少壓力;
11 反應釜導熱油加熱器距離反應釜多遠,連結管徑的大小;
反應釜的導熱油加熱器機器基本參數:
機型 | Model | 單位Unit | AEOT-30 | AEOT-40 | AEOT-75 | AEOT-75 | AEOT-100 |
溫控範圍 | Controlrange | ℃ | 350℃ | ||||
電源 | Power | AC3相380V50HZ | |||||
溫控精度 | Temp.control accuracy | KW | PID±1℃ | ||||
加熱能量 | Heating capacity | KW | 18 | 36 | 48 | 60 | 72 |
泵浦功率 | Pump power | KW | 2.2 | 3 | 5.5 | 5.5 | 7.5 |
最大電力消耗 | Powersupply | KW | 26.5 | 39 | 53.5 | 65.5 | 79.5 |
泵浦流量/ 揚程 | Pump folw/Head | M3/H/M | 10/28 | 10.5/30 | 18/40 | 18/40 | 30/48 |
膨脹油箱 | Expansion tank capacity | L | 50 | 50 | 100 | 100 | 150 |
循環油配管 | Circulation oil pipe | DN | DN40 | DN40 | DN50 | DN50 | DN65 |
外型尺寸 | LxWxH | M | 1.6*0.6*1.4 | 1.6*0.6*1.4 | 1.6*0.6*1.4 | 1.7*0.6*1.4 | 1.8*0.7*1.4 |
重量 | Weight | KG | 220 | 240 | 350 | 480 | 600 |