封裝技術
把積體電路(或半導體分立器件)晶片包裝、密封在一個外殼內,使其能在所要求的外界環境和工作條件下穩定可靠地工作。封裝一般可分為晶片裝架、引線鍵合和封蓋三個過程。晶片裝架 把積體電路晶片裝配到外殼或引線框架上。一般採用粘結料或合金法使晶片和外殼或引線框架裝配成一個整體。①粘結料粘片:用粘結料把晶片粘結到外殼上,再加熱使粘結料固化。粘結料的種類很多,常用的一種導電膠是環氧樹脂加銀粉末組成。用它把晶片和外殼底座粘結後,加熱到 200℃左右使環氧樹脂固化。加銀粉的作用是提高粘結材料的導熱和導電性能,有利於晶片把熱量經外殼傳布到周圍環境中去;也有利於改進晶片和外殼底座之間的導電性能。銀漿是另一種常用的粘結料,主要成分是銀的氧化物,用於粘結晶片。加熱後,銀的氧化物分解還原成銀並固化。②合金法粘片:在晶片背面和外殼底座之間用金屬材料形成合金,使晶片固定在底座上。
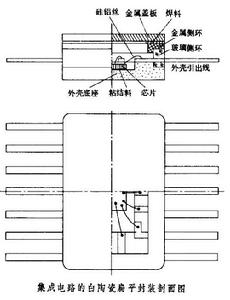
引線鍵合 又稱壓焊,是將外殼引出線與晶片中相對應的部位用金屬細絲連線起來,通常採用超音波壓焊或熱壓焊(金絲球焊)。常用的細絲有矽鋁絲和金絲兩種。矽鋁絲用超音波壓焊在氣密封裝中實現互連;金絲則用球焊或超聲球焊在塑膠封裝中互連(見積體電路焊接工藝)。
封蓋(或封裝成型) 把裝有積體電路或分立器件晶片的外殼(或引線框架)封蓋、密封(或模封成型)。常用的封裝類型有:①金屬圓殼封裝:多用於分立器件(如電晶體)和線性積體電路的封裝。底殼和圓帽由可伐合金製成。封帽是在氮氣保護下通過大電流把圓帽和底殼焊接密封起來;隨後進行氣密性檢漏,以保證器件可靠性。②白陶瓷扁平封裝:把帶有金屬環的白陶瓷扁平外殼和金屬蓋板用焊料進行釺焊密封。焊料常用熔點在 200℃以上的錫合金。封裝後要進行氦質譜細檢漏和氟油加壓粗檢漏。前者檢查細微漏孔,後者檢查較大的漏孔。檢漏合格的器件,具有良好的氣密性和可靠性。③白陶瓷雙列直插式封裝:類似於白陶瓷扁平封裝,通常在氫氣和氮氣保護下的鏈式爐中進行釺焊封裝。也可用平行縫焊機通過大電流加熱的方法把蓋板與外殼焊接。鏈式爐生產效率高、產量大;而平行縫焊機設備簡單、成本低。封裝後要進行檢漏。白陶瓷封裝的密封性好、可靠性高。扁平封裝體積小、重量輕。但雙列直插式封裝在生產過程中便於自動上、下料,適合於自動化大產生。把雙列直插式封裝的電路焊到整機線路板上可採用波峰焊。線路板通過錫鍋上面時與被壓縮空氣吹起的熔融焊錫波峰相接觸即能完成全部焊接,可實現自動化焊接,生產效率高。④低熔玻璃雙列直插式封裝:把塗敷有低熔點玻璃的陶瓷底座和陶瓷蓋板裝架,在通過鏈式爐時,低熔點玻璃把蓋板和裝有晶片的底座熔封成一個整體。這種外殼用的陶瓷和玻璃都是黑色的,故又稱黑陶瓷封裝。這種外殼玻璃的熔封溫度僅四百多度,比一般玻璃的熔化溫度低得多,所以稱低熔玻璃。它的耐酸腐蝕性和可靠性不如白陶瓷外殼好,但成本比白陶瓷外殼低。封裝後的器件也要進行檢漏。⑤塑膠雙列直插式封裝:也叫塑膠模封或塑膠包封,是把粘有晶片並已壓焊好的引線框架置於塑封油壓機的包封模具中。再把經過預熱的塑膠(通常是環氧樹脂或矽酮樹脂)放入加料腔中,在一定的壓力下使塑膠流入加熱的模腔中固化成型完成封裝。常用的油壓機具有幾十到一百多噸的壓力。包封模一次可同時成型幾十到幾百個積體電路或更多的分立器件,生產效率高,適合於自動化生產。包封后的積體電路,要進行後固化、鍍錫或沾錫以及沖筋打彎等工序,但不進行檢漏。⑥塑膠單列直插式封裝:和塑膠雙列直插式封裝類似,只是外形不同。
CPU封裝技術
所謂“封裝技術”是一種將積體電路用絕緣的塑膠或陶瓷材料打包的技術。以CPU為例,實際看到的體積和外觀並不是真正的CPU核心的大小和面貌,而是CPU核心等元件經過封裝後的產品。
封裝對於晶片來說是必須的,也是至關重要的。因為晶片必須與外界隔離,以防止空氣中的雜質對晶片電路的腐蝕而造成電氣性能下降。另一方面,封裝後的晶片也更便於安裝和運輸。由於封裝技術的好壞還直接影響到晶片自身性能的發揮和與之連線的PCB(印製電路板)的設計和製造,因此它是至關重要的。封裝也可以說是指安裝半導體積體電路晶片用的外殼,它不僅起著安放、固定、密封、保護晶片和增強導熱性能的作用,而且還是溝通晶片內部世界與外部電路的橋樑——晶片上的接點用導線連線到封裝外殼的引腳上,這些引腳又通過印刷電路板上的導線與其他器件建立連線。因此,對於很多積體電路產品而言,封裝技術都是非常關鍵的一環。
採用的CPU封裝多是用絕緣的塑膠或陶瓷材料包裝起來,能起著密封和提高晶片電熱性能的作用。由於現在處理器晶片的內頻越來越高,功能越來越強,引腳數越來越多,封裝的外形也不斷在改變。封裝時主要考慮的因素:
1、晶片面積與封裝面積之比為提高封裝效率,儘量接近1:1
2、引腳要儘量短以減少延遲,引腳間的距離儘量遠,以保證互不干擾,提高性能
3、基於散熱的要求,封裝越薄越好
作為計算機的重要組成部分,CPU的性能直接影響計算機的整體性能。而CPU製造工藝的最後一步也是最關鍵一步就是CPU的封裝技術,採用不同封裝技術的CPU,在性能上存在較大差距。只有高品質的封裝技術才能生產出完美的CPU產品。
CPU主要封裝技術
DIP技術
DIP封裝(Dual In-line Package),也叫雙列直插式封裝技術,指採用雙列直插形式封裝的積體電路晶片,絕大多數中小規模積體電路均採用這種封裝形式,其引腳數一般不超過100。DIP封裝的CPU晶片有兩排引腳,需要插入到具有DIP結構的晶片插座上。當然,也可以直接插在有相同焊孔數和幾何排列的電路板上進行焊接。DIP封裝的晶片在從晶片插座上插拔時應特別小心,以免損壞管腳。DIP封裝結構形式有:多層陶瓷雙列直插式DIP,單層陶瓷雙列直插式DIP,引線框架式DIP(含玻璃陶瓷封接式,塑膠包封結構式,陶瓷低熔玻璃封裝式)等。
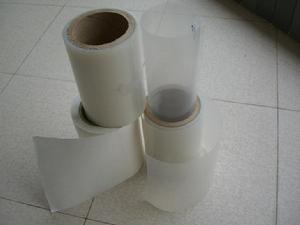
DIP封裝具有以下特點
1、適合在PCB(印刷電路板)上穿孔焊接,操作方便。
2、晶片面積與封裝面積之間的比值較大,故體積也較大。
QFP技術 這種技術的中文含義叫方型扁平式封裝技術(Plastic Quad Flat Pockage),該技術實現的CPU晶片引腳之間距離很小,管腳很細,一般大規模或超大規模積體電路採用這種封裝形式,其引腳數一般都在100以上。該技術封裝CPU時操作方便,可靠性高;而且其封裝外形尺寸較小,寄生參數減小,適合高頻套用;該技術主要適合用SMT表面安裝技術在PCB上安裝布線。
PFP技術 該技術的英文全稱為Plastic Flat Package,中文含義為塑膠扁平組件式封裝。用這種技術封裝的晶片同樣也必須採用SMD技術將晶片與主機板焊接起來。採用SMD安裝的晶片不必在主機板上打孔,一般在主機板表面上有設計好的相應管腳的焊盤。將晶片各腳對準相應的焊盤,即可實現與主機板的焊接。用這種方法焊上去的晶片,如果不用專用工具是很難拆卸下來的。該技術與上面的QFP技術基本相似,只是外觀的封裝形狀不同而已。
PGA技術 該技術也叫插針格線陣列封裝技術(Ceramic Pin Grid Arrau Package),由這種技術封裝的晶片內外有多個方陣形的插針,每個方陣形插針沿晶片的四周間隔一定距離排列,根據管腳數目的多少,可以圍成2~5圈。安裝時,將晶片插入專門的PGA插座。為了使得CPU能夠更方便的安裝和拆卸,從486晶片開始,出現了一種ZIF CPU插座,專門用來滿足PGA封裝的CPU在安裝和拆卸上的要求。該技術一般用於插拔操作比較頻繁的場合之下。
PGA封裝具有以下特點:
1.插拔操作更方便,可靠性高;
2.可適應更高的頻率;
3.如採用導熱性良好的陶瓷基板,還可適應高速度、大功率器件要求;
4.由於此封裝具有向外伸出的引腳,一般採用插入式安裝而不宜採用表面安裝;
5.如用陶瓷基板,價格又相對較高,因此多用於較為特殊的用途。它又分為陳列引腳型和表面貼裝型兩種。
BGA技術 BGA技術(Ball Grid Array Package)即球柵陣列封裝技術。該技術的出現便成為CPU、主機板南、北橋晶片等高密度、高性能、多引腳封裝的最佳選擇。但BGA封裝占用基板的面積比較大。雖然該技術的I/O引腳數增多,但引腳之間的距離遠大於QFP,從而提高了組裝成品率。而且該技術採用了可控塌陷晶片法焊接,從而可以改善它的電熱性能。另外該技術的組裝可用共面焊接,從而能大大提高封裝的可靠性;並且由該技術實現的封裝CPU信號傳輸延遲小,適應頻率可以提高很大。
BGA封裝具有以下特點
1.I/O引腳數雖然增多,但引腳之間的距離遠大於QFP封裝方式,提高了成品率
2、雖然BGA的功耗增加,但由於採用的是可控塌陷晶片法焊接,從而可以改善電熱性能
3、信號傳輸延遲小,適應頻率大大提高
4、組裝可用共面焊接,可靠性大大提高
BGA封裝的不足之處:BGA封裝仍與QFP、PGA一樣,占用基板面積過大;塑膠BGA封裝的翹曲問題是其主要缺陷,即錫球的共面性問題。共面性的標準是為了減小翹曲,提高BGA封裝的特性,應研究塑膠、粘片膠和基板材料,並使這些材料最佳化。同時由於基板的成本高,而使其價格很高。
SFF技術 SFF是Small Form Factor的簡稱,英特爾將其稱為小封裝技術。小封裝技術是英特爾在封裝移動處理器過程中採用的一種特殊技術,可以在不影響處理器性能的前提下,將封裝尺寸縮小為普通尺寸的40%左右,從而帶動移動產品內其他組件尺寸一起縮小,最終讓終端產品更加輕薄、小巧、時尚,並且支持更豐富的外觀和材質的設計。
晶片封裝技術發展
從DIP封到BGA封裝
晶片的封裝技術種類實在是多種多樣,諸如DIP,PQFP, TSOP, TSSOP, PGA, BGA, QFP, TQFP, QSOP, SOIC, SOJ, PLCC, WAFERS......一系列名稱看上去都十分繁雜,其實,只要弄清晶片封裝發展的歷程也就不難理解了。晶片的封裝技術已經歷經好幾代的變遷,技術指標一代比一代先進,包括晶片面積與封裝面積之比越來越接近,適用頻率越來越高,耐溫性能越來越好,以及引腳數增多,引腳間距減小,重量減小,可靠性提高,使用更加方便等等,都是看得見的變化。 20世紀70年代時,晶片封裝流行的還是雙列直插封裝,簡稱DIP(Dual ln-line Package)。DIP封裝在當時具有適合PCB(印刷電路板)的穿孔安裝,具有比TO型封裝易於對PCB布線以及操作較為方便等一些特點,其封裝的結構形式也很多,包括多層陶瓷雙列直插式DIP,單層陶瓷雙列直插式DIP,引線框架式DIP等等。但是衡量一個晶片封裝技術先進與否的重要指標是晶片面積與封裝面積之比,這個比值越接近1越好。比如一顆採用40根I / O引腳塑膠雙列直插式封裝(PDIP)的晶片為例,其晶片面積/封裝面積=(3 x3)/(15.24 x 50)=1:86,離l相差很遠。不難看出,這種封裝尺寸遠比晶片大不少,說明封裝效率很低,占去了很多有效安裝面積。
到了80年代出現的記憶體第二代封裝技術以TSOP為代表,它很快為業界所普遍採用,到目前為止還保持著記憶體封裝的主流地位。TSOP是英文Thin Small Outline Package的縮寫,意即薄型小尺寸封裝。TSOP記憶體封裝技術的一個典型特徵就是在封裝晶片的周圍做出引腳,如SDRAM記憶體的積體電路兩側都有引腳,SGRAM記憶體的積體電路四面都有引腳。TSOP適合用SMT技術(表面安裝技術)在PCB(印製電路板)上安裝布線。TSOP封裝外形尺寸時,寄生參數(電流大幅度變化時,引起輸出電壓擾動) 減小,適合高頻套用,操作比較方便,可靠性也比較高。改進的TSOP技術目前廣泛套用於SDRAM記憶體的製造上,不少知名記憶體製造商如三星、現代、Kingston等目前都在採用這項技術進行記憶體封裝。
20世紀90年代隨著集成技術的進步、設備的改進和深亞微米技術的使用,LSI、VLSI、ULSI相繼出現,晶片集成度不斷提高,I / O引腳數急劇增加,功耗也隨之增大,對積體電路封裝的要求也更加嚴格。為滿足發展的需要,在原有封裝方式的基礎上,又增添了新的方式一一球柵陣列封裝,簡稱BGA(Ball Grid Array Package)。BGA封裝技術已經在筆記本電腦的記憶體、主機板晶片組等大規模積體電路的封裝領域得到了廣泛的套用。比如我們所熟知的Intel BX、VIA MVP3晶片組以及SODIMM等都是採用這一封裝技術的產品。
BGA 封裝技術有這樣一些特點:I / O引腳數雖然增多,但引腳間距並不小,從而提高了組裝成品率;雖然它的功耗增加,但BGA能用可控塌陷晶片法焊接,從而可以改善它的電熱性能;厚度和重量都較以前的封裝技術有所減少;寄生參數減小,信號傳輸延遲小,使用頻率大大提高;組裝可用共面焊接,可靠性高。不過BGA封裝仍然存在著占用基板面積較大的問題。
隨著以CPU為主的計算機系統性能的總體大幅度提升趨勢,人們對於記憶體的品質和性能要求也日趨苛刻。為此,人們要求記憶體封裝更加緊緻,以適應大容量的記憶體晶片,同時也要求記憶體封裝的散熱性能更好,以適應越來越快的核心頻率。毫無疑問的是,進展不太大的TSOP等記憶體封裝技術也越來越不適用於高頻、高速的新一代記憶體的封裝需求,新的記憶體封裝技術也應運而生了。 採用BGA新技術封裝的記憶體,可以使所有計算機中的DRAM記憶體在體積不變的情況下記憶體容量提高兩到三倍,BGA與TSOP相比,具有更小的體積,更好的散熱性能和電性能。BGA封裝技術使每平方英寸的存儲量有了很大提升,採用BGA封裝技術的記憶體產品在相同容量下,體積只有TSOP封裝的三分之一;另外,與傳統TSOP封裝方式相比,BGA封裝方式有更加快速和有效的散熱途徑。
封裝的作用
封裝(Package)對於晶片來說是必須的,也是至關重要的。封裝也可以說是指安裝半導體集成電路晶片用的外殼,它不僅起著保護晶片和增強導熱性能的作用,而且還是溝通晶片內部世界與外部電路的橋樑和規格通用功能的作用。封裝的主要作用有:
(1)物理保護。因為晶片必須與外界隔離,以防止空氣中的雜質對晶片電路的腐蝕而造成電氣性能下降,保護晶片表面以及連線引線等,使相當柔嫩的晶片在電氣或熱物理等方面免受外力損害及外部環境的影響;同時通過封裝使晶片的熱膨脹係數與框架或基板的熱膨脹係數相匹配,這樣就能緩解由於熱等外部環境的變化而產生的應力以及由於晶片發熱而產生的應力,從而可防止晶片損壞失效。基於散熱的要求,封裝越薄越好,當晶片功耗大於2W時,在封裝上需要增加散熱片或熱沉片,以增強其散熱冷卻功能;5~1OW時必須採取強制冷卻手段。另一方面,封裝後的晶片也更便於安裝和運輸。
(2)電氣連線。封裝的尺寸調整(間距變換)功能可由晶片的極細引線間距,調整到實裝基板的尺寸間距,從而便於實裝操作。例如從以亞微米(目前已達到0.1 3μm以下)為特徵尺寸的晶片,到以10μm為單位的晶片焊點,再到以100μm為單位的外部引腳,最後劍以毫米為單位的印刷電路板,都是通過封裝米實現的。封裝在這裡起著由小到大、由難到易、由複雜到簡單的變換作用,從而可使操作費用及材料費用降低,而且能提高工作效率和可靠性,特別是通過實現布線長度和阻抗配比儘可能地降低連線電阻,寄生電容和電感來保證正確的信號波形和傳輸速度。
(3)標準規格化。規格通用功能是指封裝的尺寸、形狀、引腳數量、間距、長度等有標準規格,既便於加工,又便於與印刷電路板相配合,相關的生產線及生產設備都具有通用性。這對於封裝用戶、電路板廠家、半導體廠家都很方便,而且便於標準化。相比之下,裸晶片實裝及倒裝目前尚不具備這方面的優勢。由於組裝技術的好壞還直接影響到晶片自身性能的發揮和與之連線的印刷電路板(PCB)的設計和製造,對於很多積體電路產品而言,組裝技術都是非常關鍵的一環。
記憶體的封裝技術
如今計算機的“心”奔騰不止,以百兆為單位的高速提升讓我們不得不感嘆CPU技術的成熟和完善。不過,光有一顆速急力猛的芯好像還遠遠不夠,為了讓計算機真正快速地跑起來,整個內外系統都需要齊齊跟進,而記憶體則一向是一個關注焦點。作為計算機的“運作機艙”,記憶體的性能直接影響計算機的整體表現,重要性是不言而喻的。與CPU一樣,記憶體的製造工藝同樣對其性能高低具有決定意義,而在記憶體製造工藝流程上的最後一步也是最關鍵一步就是記憶體的封裝技術。採用不同封裝技術的記憶體條,在性能上也會存在較大差距。從DIP、TSOP到BGA,不斷發展的封裝技術使得記憶體向著高頻、高速的目標繼續邁進,而NORCENT Micro-CSP等新型技術的出現,則意味著記憶體封裝已經進入到CSP時代。
記憶體封裝,“品質”外衣
我們所使用的每一條記憶體,其實是由數量龐大的積體電路組合而成,只不過這些電路,都是需要最後打包完成,這類將積體電路打包的技術就是所謂的封裝技術。封裝也可以說是指安裝半導體積體電路晶片用的外殼,它不僅起著安放、固定、密封、保護晶片和增強導熱性能的作用,而且還是溝通晶片內部世界與外部電路的橋樑——晶片上的接點用導線連線到封裝外殼的引腳上,這些引腳又通過印刷電路板上的導線與其他器件建立連線。因此,對於很多積體電路產品而言,封裝技術都是非常關鍵的一環。
在我們的計算機里,CPU需要嚴格地封裝,記憶體條也同樣不可怠慢,對於常見的記憶體條而言,我們實際看到的體積和外觀並不是真正的記憶體的大小和面貌,那一個一個整齊排列的小黑塊即記憶體晶片經過打包封裝後的成果。對於記憶體這樣以晶片為主的產品來說,封裝技術不僅保證晶片與外界隔離,防止空氣中的雜質對晶片電路的腐蝕而造成電學性能下降;而且封裝技術的好壞還直接關係到與晶片連線的PCB(印製電路板)的設計和製造,從而對晶片自身性能的表現和發揮產生深刻的影響。 如此而言,封裝技術好比記憶體的一件外衣,而記憶體品質在這裡則是典型的“以貌取人”,越“高檔”的外衣身價也就越高了。如同微處理器一樣,記憶體條的技術也是不斷地更新。人們手中記憶體條上的顆粒模樣漸漸在變,變得比以前更小、更精緻。變化不僅在表面上,而且這些新型的晶片在適用頻率和電氣特性上比老前輩又有了長足的進步。這一結晶應歸功新型的記憶體晶片封裝技術所帶來的成果。
LED封裝技術
LED封裝技術大都是在分立器件封裝技術基礎上發展與演變而來的,但卻有很大的特殊性。一般情況下,分立器件的管芯被密封在封裝體內,封裝的作用主要是保護管芯和完成電氣互連。而LED封裝則是完成輸出電信號,保護管芯正常工作、輸出可見光的功能,既有電參數,又有光參數的設計及技術要求,無法簡單地將分立器件的封裝用於LED。
LED的核心發光部分是P型半導體和N型半導體構成的PN結管芯。當注入PN結的少數載流子與多數載流子複合時,就會發出可見光、紫外線光或者紅外線光。但PN結區發出的光子是非定向的,即向各個方向發射有相同的幾率。因此,並不是管芯產生的所有光都可以釋放出來,這主要取決於半導體材料質量、管芯結構和幾何形狀、封裝內部結構與包封材料,套用要求提高LED的內、外部量子效率。常規Φ5mm型LED封裝是將邊長0.25mm的正方形管芯粘結或燒結在引線架上,管芯的正極通過球形接觸點與金絲鍵合為內引線與一條管腳相連,負極通過發射杯和引線架的另一管腳相連,然後其頂部用環氧樹脂包封。反射杯的作用是收集管芯側面、界面發出的光,向期望的方向角內發射。頂部包封的環氧樹脂做成一定形狀,有這樣幾種作用:保護管芯等不受外界侵蝕;採用不同的形狀和材料性質(摻或不摻散色劑),起透鏡或漫射透鏡功能,控制光的發散角;管芯折射率與空氣折射率相關太大,致使管芯內部的全反射臨界角很小,其有源層產生的光只有小部分被取出,大部分易在管芯內部經多次反射而被吸收,易發生全反射導致過多光的損失。選用相應折射率的環氧樹脂做過渡,提高管芯的光出射效率。用作構成管殼的環氧樹脂須具有耐濕性、絕緣性、機械強度,對管芯發出光的折射率和透射率高。選擇不同折射率的封裝材料,封裝幾何形狀對光子逸出效率的影響是不同的,發光強度的角分布也與管芯結構、光輸出方式、封裝透鏡所用材料和形狀有關。若採用尖形樹脂透鏡,可使光集中到LED的軸線方向,相應的視角較小;如果頂部的樹脂透鏡為圓形或平面型,其相應視角將增大。
一般情況下,LED的發光波長隨溫度變化為0.2 -0.3nm/℃,光譜寬度隨之增加,影響顏色鮮艷度。另外,當正向電流流經PN結,發熱性損耗使結區產生溫升。在室溫附近,溫度每升高1℃,LED的發光強度會相應地減少1%左右,封裝散熱時保持色純度與發光強度非常重要。以往採用減少其驅動電流的辦法,降低結溫,多數LED的驅動電流限制在20mA左右。但是,LED的光輸出會隨著電流的增大而增加。目前,很多功率型LED的驅動電流可以達到70mA、100mA甚至1A級,需要改進封裝結構。全新的LED封裝設計理念和低熱阻封裝結構及技術,改善了熱特性。例如,採用大面積晶片倒裝結構,選用導熱性能好的銀膠,增大金屬支架的表面積,焊料凸點的矽載體直接裝在熱沉上等方法。此外,在套用設計中,PCB線路板等的熱設計、導熱性能也十分重要。
生產工藝
1.工藝:
a)清洗:採用超音波清洗PCB或LED支架,並烘乾。
b)裝架:在LED管芯(大圓片)底部電極備上銀膠後進行擴張,將擴張後的管芯(大圓片)安置在刺晶台上,在顯微鏡下用刺晶筆將管芯一個一個安裝在PCB或LED支架相應的焊盤上,隨後進行燒結使銀膠固化。
c)壓焊:用鋁絲或金絲焊機將電極連線到LED管芯上,以作電流注入的引線。LED直接安裝在PCB上的,一般採用鋁絲焊機。(製作白光TOP-LED需要金線焊機)
d)封裝:通過點膠,用環氧將LED管芯和焊線保護起來。在PCB板上點膠,對固化後膠體形狀有嚴格要求,這直接關係到背光源成品的出光亮度。這道工序還將承擔點螢光粉(白光LED)的任務。
e)焊接:如果背光源是採用SMD-LED或其它已封裝的LED,則在裝配工藝之前,需要將LED焊接到PCB板上。
f)切膜:用沖床模切背光源所需的各種擴散膜、反光膜等。
g)裝配:根據圖紙要求,將背光源的各種材料手工安裝正確的位置。
h)測試:檢查背光源光電參數及出光均勻性是否良好。
包裝:將成品按要求包裝、入庫。
封裝工藝
1.LED的封裝的任務
是將外引線連線到LED晶片的電極上,同時保護好LED晶片,並且起到提高光取出效率的作用。關鍵工序有裝架、壓焊、封裝。
2.LED封裝形式 LED封裝形式可以說是五花八門,主要根據不同的套用場合採用相應的外形尺寸,散熱對策和出光效果。LED按封裝形式分類有Lamp-LED、TOP-LED、Side-LED、SMD-LED、High-Power-LED等。
3.LED封裝工藝流程
4.封裝工藝說明
(1)晶片檢驗
鏡檢:材料表面是否有機械損傷及麻點麻坑(lockhill)晶片尺寸及電極大小是否符合工藝要求,電極圖案是否完整。
(2)擴片
由於LED晶片在劃片後依然排列緊密間距很小(約0.1mm),不利於後工序的操作。我們採用擴片機對黏結晶片的膜進行擴張,是LED晶片的間距拉伸到約0.6mm。也可以採用手工擴張,但很容易造成晶片掉落浪費等不良問題。
(3)點膠
在LED支架的相應位置點上銀膠或絕緣膠。(對於GaAs、SiC導電襯底,具有背面電極的紅光、黃光、黃綠晶片,採用銀膠。對於藍寶石絕緣襯底的藍光、綠光LED晶片,採用絕緣膠來固定晶片。)工藝難點在於點膠量的控制,在膠體高度、點膠位置均有詳細的工藝要求。由於銀膠和絕緣膠在貯存和使用均有嚴格的要求,銀膠的醒料、攪拌、使用時間都是工藝上必須注意的事項。
(4)備膠
和點膠相反,備膠是用備膠機先把銀膠塗在LED背面電極上,然後把背部帶銀膠的LED安裝在LED支架上。備膠的效率遠高於點膠,但不是所有產品均適用備膠工藝。
(5)手工刺片
將擴張後LED晶片(備膠或未備膠)安置在刺片台的夾具上,LED支架放在夾具底下,在顯微鏡下用針將LED晶片一個一個刺到相應的位置上。手工刺片和自動裝架相比有一個好處,便於隨時更換不同的晶片,適用於需要安裝多種晶片的產品.
(6)自動裝架
自動裝架其實是結合了沾膠(點膠)和安裝晶片兩大步驟,先在LED支架上點上銀膠(絕緣膠),然後用真空吸嘴將LED晶片吸起移動位置,再安置在相應的支架位置上。自動裝架在工藝上主要要熟悉設備操作編程,同時對設備的沾膠及安裝精度進行調整。在吸嘴的選用上儘量選用膠木吸嘴,防止對LED晶片表面的損傷,特別是蘭、綠色晶片必須用膠木的。因為鋼嘴會劃傷晶片表面的電流擴散層。
(7)燒結
燒結的目的是使銀膠固化,燒結要求對溫度進行監控,防止批次性不良。銀膠燒結的溫度一般控制在150℃,燒結時間2小時。根據實際情況可以調整到170℃,1小時。絕緣膠一般150℃,1小時。銀膠燒結烘箱的必須按工藝要求隔2小時(或1小時)打開更換燒結的產品,中間不得隨意打開。燒結烘箱不得再其他用途,防止污染。
(8)壓焊
壓焊的目的將電極引到LED晶片上,完成產品內外引線的連線工作。LED的壓焊工藝有金絲球焊和鋁絲壓焊兩種。先在LED晶片電極上壓上第一點,再將鋁絲拉到相應的支架上方,壓上第二點後扯斷鋁絲。金絲球焊過程則在壓第一點前先燒個球,其餘過程類似。壓焊是LED封裝技術中的關鍵環節,工藝上主要需要監控的是壓焊金絲(鋁絲)拱絲形狀,焊點形狀,拉力。對壓焊工藝的深入研究涉及到多方面的問題,如金(鋁)絲材料、超聲功率、壓焊壓力、劈刀(鋼嘴)選用、劈刀(鋼嘴)運動軌跡等等
LED的封裝主要有點膠、灌封、模壓三種。
基本上工藝控制的難點是氣泡、多缺料、黑點。設計上主要是對材料的選型,選用結合良好的環氧和支架。手動點膠封裝對操作水平要求很高(特別是白光LED),主要難點是對點膠量的控制,因為環氧在使用過程中會變稠。白光LED的點膠還存在螢光粉沉澱導致出光色差的問題。
(10)灌膠封裝
Lamp-LED的封裝採用灌封的形式。灌封的過程是先在LED成型模腔內注入液態環氧,然後插入壓焊好的LED支架,放入烘箱讓環氧固化後,將LED從模腔中脫出即成型。
(11)模壓封裝
將壓焊好的LED支架放入模具中,將上下兩副模具用液壓機合模並抽真空,將固態環氧放入注膠道的入口加熱用液壓頂桿壓入模具膠道中,環氧順著膠道進入各個LED成型槽中並固化。 (12)固化與後固化
固化是指封裝環氧的固化,一般環氧固化條件在135℃,1小時。模壓封裝一般在150℃,4分鐘。
(13)後固化
後固化是為了讓環氧充分固化,同時對LED進行熱老化。後固化對於提高環氧與支架(PCB)的粘接強度非常重要。一般條件為120℃,4小時。
(14)切筋和劃片
由於LED在生產中是連在一起的(不是單個),Lamp封裝LED採用切筋切斷LED支架的連筋。SMD-LED則是在一片PCB板上,需要劃片機來完成分離工作。
(15)測試
測試LED的光電參數、檢驗外形尺寸,同時根據客戶要求對LED產品進行分選。
(16)包裝
將成品進行計數包裝。超高亮LED需要防靜電包裝。
LED單晶片封裝
LED在過去的30多年裡,取得飛速發展。第一批產品出現在1968年,工作電流20mA的LED的光通量只有千分之幾流明,相應的發光效率為0.1lm/W,而且只有一種光色為650nm的紅色光。70年代初該技術進步很快,發光效率達到1lm/W,顏色也擴大到紅色、綠色和黃色。伴隨著新材料的發明和光效的提高,單個LED光源的功率和光通量也在迅速增加。原先,一般LED的驅動電流僅為20mA。到了20世紀90年代,一種代號為“食人魚”的LED光源的驅動電流增加到50-70mA,而新型大功率LED的驅動電流達到300—500mA。特別是1998年白光LED的開發成功,使得LED套用從單純的標識顯示功能向照明功能邁出了實質性的一步。圖2-1到圖2-4描述了LED的發展歷程。圖2-1普通LED主要用於指示燈圖2-2高亮度LED主要用於照明燈圖2-3食人魚LED圖2-4大功率LEDA功率型LED封裝技術現狀 功率型LED分為功率LED和瓦(W)級功率LED兩種。功率LED的輸入功率小於1W(幾十毫瓦功率LED除外);W級功率LED的輸入功率等於或大於1W。[3]
半導體封裝技術
半導體器件有許多封裝形式,按封裝的外形、尺寸、結構分類可分為引腳插入型、表面貼裝型和高級封裝三類。從DIP、SOP、QFP、PGA、BGA到CSP再到SIP,技術指標一代比一代先進。總體說來,半導體封裝經歷了三次重大革新:第一次是在20世紀80年代從引腳插入式封裝到表面貼片封裝,它極大地提高了印刷電路板上的組裝密度;第二次是在20世紀90年代球型矩陣封裝的出現,滿足了市場對高引腳的需求,改善了半導體器件的性能;晶片級封裝、系統封裝等是現在第三次革新的產物,其目的就是將封裝面積減到最小。
國內外比較
我國封裝技術與國外封裝技術的差距所在
(1)封裝技術人才嚴重短缺、缺少製程式改善工具的培訓及持續提高培訓的經費及手段。
(2)先進的封裝設備、封裝材料及其產業鏈滯後,配套不拿且質量不穩定。
(3)封裝技術研發能力不足,生產工藝程式設計不周傘,可操作性差,執行能力弱。
(4)封裝設備維護保養能力欠偉,缺少有經驗的維修工程師,且可靠性實驗設備不齊全,失效分析(FA)能力不足。
(5)國內封裝企業除個別企業外,普遍規模較小,從事低端產品生產的居多,可持續發展能力低,缺乏向高檔發展的技術和資金。
(6)缺少團隊精神,缺乏流程整合、持續改善、精細管理的精神,缺少現代企業管理的機制和理念。