基本簡介
壓鑄材料、壓鑄機、模具是壓鑄生產的三大要素,缺一不可。所謂壓鑄工藝就是將這三大要素有機地加以綜合運用,使能穩定地有節奏地和高效地生產出外觀、內在質量好的、尺寸符合圖樣或協定規定要求的合格鑄件,甚至優質鑄件的過程。
介紹
壓鑄模具是鑄造液態模鍛的一種方法, 一種在專用的壓鑄模鍛機上完成的工藝。它的基本工藝過程是:金屬液先低速或高速鑄造充型進模具的型腔內,模具有活動的型腔面,它隨著金屬液的冷卻過程加壓鍛造,既消除毛坯的縮孔縮松缺陷,也使毛坯的內部組織達到鍛態的破碎晶粒。毛坯的綜合機械性能得到顯著的提高。
壓鑄模具合金
壓鑄件所採用的合金主要是有色合金,至於黑色金屬(鋼、鐵等)由於模具材料等問題,目前較少使用。而有色合金壓鑄件中又以鋁合金使用較廣泛, 鋅合金次之。 下面簡單介紹一下壓鑄有色金屬的情況。
(1)、壓鑄有色合金的分類 受阻收縮 混合收縮 自由收縮 鉛合金 -----0.2-0.3% 0.3-0.4% 0.4-0.5% 低熔點合金 錫合金 鋅合金--------0.3-0.4% 0.4-0.6% 0.6-0.8% 鋁矽系--0.3-0.5% 0.5-0.7% 0.7-0.9% 壓鑄有色合金 鋁合金 鋁銅系 鋁鎂系---0.5-0.7% 0.7-0.9% 0.9-1.1% 高熔點合金 鋁鋅系 鎂合金----------0.5-0.7% 0.7-0.9% 0.9-1.1% 銅合金
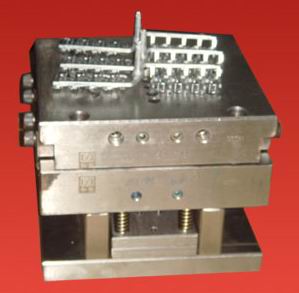
(2)、各類壓鑄合金推薦的澆鑄溫度 合金種類 鑄件平均壁厚≤3mm 鑄件平均壁厚>3mm 結構簡單 結構複雜 結構簡單 結構複雜
鋁合金 鋁矽系 610-650℃ 640-680℃ 600-620℃ 610-650℃
鋁銅系 630-660℃ 660-700℃ 600-640℃ 630-660℃
鋁鎂系 640-680℃ 660-700℃ 640-670℃ 650-690℃
鋁鋅系 590-620℃ 620-660℃ 580-620℃ 600-650℃
鋅合金 420-440℃ 430-450℃ 400-420℃ 420-440℃
鎂合金 640-680℃ 660-700℃ 640-670℃ 650-690℃
銅合金 普通黃銅 910-930℃ 940-980℃ 900-930℃ 900-950℃
矽黃銅 900-920℃ 930-970℃ 910-940℃ 910-940℃
* 註:①澆鑄溫度一般以保溫爐的金屬液的溫度來計量。
②鋅合金的澆鑄溫度不能超過450℃,以免晶粒粗大。
設計過程
1、按照產品使用的材料類別、產品的形狀和精度等各項指標對該產品進行工藝分析,訂出工藝。
2、確定產品在模具型腔中擺放的位置,進行分型面、排溢系統和澆注系統的分析和設計。
3、對各個活動的型芯拼裝方式和固定方式進行設計。
4、抽芯距和力的設計。
5、頂出機構的設計。
6、確定壓鑄機,對模架和冷卻系統設計。
7、核對模具和壓鑄機的相關尺寸,繪製模具及各個部件的工藝圖。
8、設計完成。
常見問題
壓鑄模具表面溫度的控制對生產高質量的壓鑄件來說,是非常重要的。不平均或不適當的壓鑄模具溫度亦會導致鑄件尺寸不穩定,在生產過程中頂出鑄件變形,產生熱壓力、粘模、表面凹陷、內縮孔及熱泡等缺陷。模溫差異較大時,對生產周期中的變數,如填充時間、冷卻時間及噴塗時間等產生不同程度的影響。
1).冷紋:
原因:熔湯前端的溫度太低,相疊時有痕跡.
改善方法:
1.檢查壁厚是否太薄(設計或製造) ,較薄的區域應直接充填.
2.檢查形狀是否不易充填;距離太遠、封閉區域(如鰭片(fin) 、凸起) 、被阻擋區域、圓角太小等均不易充填.並注意是否有肋點或冷點.
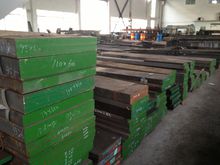
3.縮短充填時間.縮短充填時間的方法:…
4.改變充填模式.
5.提高模溫的方法:…
6.提高熔湯溫度.
7.檢查合金成分.
8.加大逃氣道可能有用.
9.加真空裝置可能有用.
2).裂痕:
原因:1.收縮應力.
2.頂出或整緣時受力裂開.
改善方式:
1.加大圓角.
2.檢查是否有熱點.
3.增壓時間改變(冷室機).
4.增加或縮短合模時間.
5.增加拔模角.
6.增加頂出銷.
7.檢查模具是否有錯位、變形.
8.檢查合金成分.
3).氣孔:
原因:1.空氣夾雜在熔湯中.
2.氣體的來源:熔解時、在料管中、在模具中、離型劑.
改善方法:
1.適當的慢速.
2.檢查流道轉彎是否圓滑,截面積是否漸減.
3.檢查逃氣道面積是否夠大,是否有被阻塞,位置是否位於最後充填的地方.
4.檢查離型劑是否噴太多,模溫是否太低.
5.使用真空.
4).空蝕:
原因:因壓力突然減小,使熔湯中的氣體忽然膨脹,衝擊模具,造成模具損傷.
改善方法:
流道截面積勿急遽變化.
5).縮孔:
原因:當金屬由液態凝固為固態時所占的空間變小,若無金屬補充便會形成縮孔.通常發生在較慢凝固處.
改善方法:
1.增加壓力.
2.改變模具溫度.局部冷卻、噴離型劑、降低模溫、.有時只是改變縮孔位置,而非消縮孔.
6).脫皮:
原因:1.充填模式不良,造成熔湯重疊.
2.模具變形,造成熔湯重疊.
3.夾雜氧化層.
改善方法:
1.提早切換為高速.
2.縮短充填時間.
3.改變充填模式,澆口位置,澆口速度.
4.檢查模具強度是否足夠.
5.檢查銷模裝置是否良好.
6.檢查是否夾雜氧化層.
7).波紋:
原因:第一層熔湯在表面急遽冷卻,第二層熔湯流過未能將第一層熔解,卻又有足夠的融合,造成組織不同.
改善方法:
1.改善充填模式.
2.縮短充填時間.
8).流動不良產生的孔:
原因:熔湯流動太慢、或是太冷、或是充填模式不良,因此在凝固的金屬接合處有孔.
改善方法:
1.同改善冷紋方法.
2.檢查熔湯溫度是否穩定.
3.檢查模具溫充是否穩定.
9).在分模面的孔:
原因:可能是縮孔或是氣孔.
改善方法:
1.若是縮孔,減小澆口厚度或是溢流井進口厚度.
2.冷卻澆口.
3.若是氣孔,注意排氣或卷氣問題.
10).毛邊:
原因:1.鎖模力不足.
2.模具合模不良.
3.模具強度不足.
4.熔湯溫度太高.
11).縮陷:
原因:縮孔發生在壓件表面下面.
改善方法:
1.同改善縮孔的方法.
2.局部冷卻.
3.加熱另一邊.
12).積碳:
原因:離型劑或其他雜質積附在模具上.
改善方法:
1.減小離型劑噴灑量.
2.升高模溫.
3.選擇適合的離型劑.
4.使用軟水稀釋離型劑.
13).冒泡:
原因:氣體卷在鑄件的表面下面.
改善方式:
1.減少卷氣(同氣孔).
2.冷卻或防低模溫.
14).粘模:
原因:1.鋅積附在模具表面.
2.熔湯衝擊模具,造成模面損壞.
改善方法:
1.降低模具溫度.
2.降低劃面粗糙度.
3.加大拔模角.
4.鍍膜.
5.改變充填模式.
6.降低澆口速度
最新技術
各種壓鑄模具表面處理新技術不斷湧現,但總的來說可以分為以下三個大類:
(1)傳統熱處理工藝的改進技術;
(2)表面改性技術,包括表面熱擴滲處理、表面相變強化、電火花強化技術等;
(3)塗鍍技術,包括化學鍍等。
壓鑄模具是模具中的一個大類。隨著我國汽車機車工業的迅速發展,壓鑄行業迎來了發展的新時期,同時,也對壓鑄模具的綜合力學性能、壽命等提出了更高的要求。國際模協秘書長羅百輝認為,要滿足不斷提高的使用性能需求僅僅依靠新型模具材料的套用仍然很難滿足,必須將各種表面處理技術套用到壓鑄模具的表面處理當中才能達到對壓鑄模具高效率、高精度和高壽命的要求。在各種模具中,壓鑄模具的工作條件是較為苛刻的。壓力鑄造是使熔融金屬在高壓、高速下充滿模具型腔而壓鑄成型,在工作過程中反覆與熾熱金屬接觸,因此要求壓鑄模具有較高的耐熱疲勞、導熱性耐磨性、耐蝕性、衝擊韌性、紅硬性、良好的脫模性等。因此,對壓鑄模具的表面處理技術要求較高。
1、傳統熱處理工藝的改進技術
傳統的壓鑄模具熱處理工藝是淬火-回火,以後又發展了表面處理技術。由於可作為壓鑄模具的材料多種多樣,同樣的表面處理技術和工藝套用在不同的材料上會產生不同的效果。史可夫提出針對模具基材和表面處理技術的基材預處理技術,在傳統工藝的基礎上,對不同的模具材料提出適合的加工工藝,從而改善模具性能,提高模具壽命。熱處理技術改進的另一個發展方向,是將傳統的熱處理工藝與先進的表面處理工藝相結合,提高壓鑄模具的使用壽命。如將化學熱處理的方法碳氮共滲,與常規淬火、回火工藝相結合的NQN(即碳氮共滲-淬火-碳氮共滲複合強化,不但得到較高的表面硬度,而且有效硬化層深度增加、滲層硬度梯度分布合理、回火穩定性和耐蝕性提高,從而使得壓鑄模具在獲得良好心部性能的同時,表面質量和性能大幅提高。
2、表面改性技術
表面熱擴滲技術
這一類型中包括有滲碳、滲氮、滲硼以及碳氮共滲、硫碳氮共滲等。
滲碳和碳氮共滲
滲碳工藝套用於冷、熱作和塑膠模具表面強化中,都能提高模具壽命。如3Cr2W8V鋼製的壓鑄模具,先滲碳、再經1140~1150℃淬火,550℃回火兩次,表面硬度可達HRC56~61,使壓鑄有色金屬及其合金的模具壽命提高1.8~3.0倍。進行滲碳處理時,主要的工藝方法有固體粉末滲碳、氣體滲碳、以及真空滲碳、離子滲碳和在滲碳氣氛中加入氮元素形成的碳氮共滲等。其中,真空滲碳和離子滲碳則是近20年來發展起來的技術,該技術具有滲速快、滲層均勻、碳濃度梯度平緩以及工件變形小等特點,將會在模具表面尤其是精密模具表面處理中發揮越來越重要的作用。
滲氮及有關的低溫熱擴滲技術
這一類型中包括滲氮、離子滲氮、碳氮共滲、氧氮共滲、硫氮共滲以及硫碳氮、氧氮硫三元共滲等方法。這些方法處理工藝簡便、適應性強、擴滲溫度較低一般為480~600℃、工件變形小,尤其適應精密模具的表面強化,而且氮化層硬度高、耐磨性好,有較好的抗粘模性能。
3Cr2W8V鋼壓鑄模具,經調質、520~540℃氮化後,使用壽命較不氮化的模具提高2~3倍。美國用H13鋼製作的壓鑄模具,不少都要進行氮化處理,且以滲氮代替一次回火,表面硬度高達HRC65~70,而模具心部硬度較低、韌性好,從而獲得優良的綜合力學性能。氮化工藝是壓鑄模具表面處理常用的工藝,但當氮化層出現薄而脆的白亮層時,無法抵抗交變熱應力的作用,極易產生微裂紋,降低熱疲勞抗力。因此,在氮化過程中,要嚴格控制工藝,避免脆性層的產生。國外提出採用二次和多次滲氮工藝。採用反覆滲氮的辦法可以分解容易在服役過程中產生微裂紋的氮化物白亮層,增加滲氮層厚度,並同時使模具表面存在很厚的殘餘應力層,使模具的壽命得以明顯提高。此外還有採用鹽浴碳氮共滲和鹽浴硫氮碳共滲等方法。這些工藝在國外套用較為廣泛,在國內較少見。如TFI+ABI工藝,是在鹽浴氮碳共滲後再於鹼性氧化性鹽浴中浸漬。工件表面發生氧化,呈黑色,其耐磨性、耐蝕性、耐熱性均得到了改善。經此方法處理的鋁合金壓鑄模具壽命提高數百小時。再如法國開發的硫氮碳共滲後進行氮化處理的oxynit工藝,套用於有色金屬壓鑄模具則更具特點。
壓鑄模具專業英語
landed plunger mold 有肩柱塞式模具
burnishing die 擠光模
landed positive mold 有肩全壓式模具
button die 鑲入式圓形凹模
loading shoe mold 料套式模具
center-gated mold 中心澆口式模具
loose detail mold 活零件模具
chill mold 冷硬用鑄模
loose mold 活動式模具
clod hobbing 冷擠壓制模
louvering die 百葉窗沖切模
composite dies 複合模具
manifold die 分歧管模具
counter punch 反凸模
modular mold 組合式模具
double stack mold 雙層模具
multi-cavity mold 多模穴模具
electroformedmold 電鑄成形模
multi-gate mold 複式澆口模具
expander die 擴徑模
offswt bending die 雙摺冷彎模具
extrusion die 擠出模
palletizing die 疊層模
family mold 反套製品模具
plaster mold 石膏模
blank through dies 漏件式落料模
porous mold 通氣性模具
duplicated cavity plate 復板模
positive mold 全壓式模具
fantail die 扇尾形模具
pressure die 壓緊模
fishtail die 魚尾形模具
profile die 輪廓模
flash mold 溢料式模具
progressive die 順序模
gypsum mold 石膏鑄模
protable mold 手提式模具
hot-runner mold 熱流道模具
prototype mold 雛形試驗模具
ingot mold 鋼錠模
punching die 落料模
lancing die 切口模
raising(embossing) 壓花起伏成形
re-entrant mold 倒角式模具
sectional die 拼合模
runless injection mold 無流道冷料模具
sectional die 對合模具
segment mold 組合模
semi-positive mold 半全壓式模具
shaper 定型模套
single cavity mold 單腔模具
solid forging die 整體鍛模
split forging die 拼合鍛模
split mold 雙並式模具
sprueless mold 無注道殘料模具
squeezing die 擠壓模
stretch form die 拉伸成形模
sweeping mold 平刮鑄模
swing die 振動模具
three plates mold 三片式模具
trimming die 切邊模
unit mold 單元式模具
universal mold 通用模具
unscrewing mold 退扣式模具
yoke type die 軛型模
壓鑄模具管理
一、目的 為使模具的驗收、保管、維護、盤點、轉移、報廢等作業做合理的管制特訂本程式。
二、範圍 2.1 凡本公司自行設計開發的零組件所用的模具均屬之。 2.2 ODM 所委託開發之模具均屬之。
三、定義 ODM:即 OFFER DESIGN MANUFACTURE 委託設計製造之意。 落模保養 : 模具於生產中之每日例行保養 ,及下模後未達定期保養之規定所實施之保養 定期保養 : 生產模次到達規定的時間或模數 ,由模房所進行的保養 四、權責 4.1 工程部(模具課、生技課):負責模具設計開發、接收、驗收、建檔登錄、定期保養、 落模保養、維修、協助工程變更修改模具等 。
成型課:負責模具保管、使用、落模保養、維護、盤點及報廢等管理 。
品管課:協助模具驗收 。
生管課:負責模具之轉移及試模之安排 。
五、內容
5.2 新模具開發、採購、驗收 重點模具的開發、採購、驗收等主要由總公司進行相關作業。於本地之新開模具由工程 部主導 5.3 模具轉移 因生產需要,相關單位擬將模具轉移至廠,轉移之相關工作由生管負責進行,模具轉移 時需附〖射出成型記錄表〗(附屬檔案 7.1)、〖模具評估報告〗(附屬檔案 7.2)、〖檢驗報 告〗(附屬檔案 7.3)及成品製作樣品。若無上述資料可比照相關部品,“工程圖面”驗收模 具。 若為廠現地開模,則於模具驗收時由模具課記錄〖射出成型記錄表〗(附屬檔案 7.4),並填 寫 〖模具評估報告〗 (附屬檔案 7.5) 品管課檢驗部品並記錄於 , 〖進料檢驗報告〗 (附屬檔案 7.6)。
模具課接到轉移、新開或維修好的模具時,需先開模檢查模具外觀是否有傷痕及瑕疵, 若無瑕疵則填寫〖試模通知單〗(附屬檔案 7.7),協調生管安排試模,並填寫〖模具試模品質編號:EP05 程 序 文 件 模具管理作業程式 版本:A 頁數:2/4確認單〗(附屬檔案 7.8),連同試模良品,送交品管、生技確認。確認完成後,轉交成型課 生產。 若模具開模檢查有瑕疵,則立即知會採購及相關單位,以便請廠商維修。 模具的試模及驗收,由模具課主導,生技、品管、成型、生管等單位協助,驗收完成後 方可轉成型課進行量產。 模具接收 成型課接到新轉移或維修好的模具後,將模具狀況登錄於〖模具基本資料明細表〗(附 件 7.9)上。
模具的保管與維護:
5.6.1 模具由模具房負責維修、落模保養與定期保養,成型課每月定期列出〖模具壽命 管制表〗(附屬檔案 7.10)對模具壽命進行管理。
5.6.2 模具於連續正常使用過程中,成型課每 24H 需對模具進行點檢,並記錄於〖模具 點檢記錄表〗(附屬檔案 7.11)。 若生產計畫完成或暫停生產而下模時,由使用單位對模具進行全面清洗,並交模 具課進行落模保養。若模具已達定期保養之規定階段 ,則模具課需進行定期保養
5.6.3 模具使用及保養完畢 ,由成型課人員負責將模具放入模具架上保管儲存 落模保養 5.7.1 若生產計畫完成或暫停生產而下模時,使用單位需將此模具最後一模之注塑品及 〖落模注鑄品檢查表〗(附屬檔案 7.12)連同模具,一起交給模具課進行落模保養。
5.7.2 模具課及品管課,先對落模品進行外觀檢視與尺寸檢查,觀看是否有外觀缺失尺 寸異常及需整修之部位,若有則於此落模時一倂整修,若無則依下列清洗項目進 行落模保養及清理。
5.7.3 落模射出品之檢視結果,由品管人員記錄於〖落模注鑄品檢查表〗中,模具課人 員依不良項目填寫維修內容, 維修完畢後交成型課進行試模, 並請品管人員確認。 修復後,〖落模注鑄品檢查表〗由成型,品管及模具課之主管簽核,並保留修復 後之樣品,以示修模確認與品質確認。
5.7.4 落模與修模之注塑樣品,由成型課負責保存,並且隨模具之上下模而更換,注塑 品或標示上,需註明保留之時間與型號等資料,以利追蹤。
5.7.5 當對於樣品之外觀有不同意見時,由品保部主管決議判定。必要時由總經理或管 理代表決議。 落模保養清洗項目 :
5.7.6 必須用布對澆口套、主流道、分流道、進澆口進行清理,直到各部位無油污、 塑膠及其它雜物為止,成型部分噴塗防鏽劑。
5.7.7 用風槍把水道里殘餘水吹出水道。
5.7.8 模具存放時與擺放木架的接觸面水咀一定要拆下。
5.7.9 對導柱、導套、滑塊加注適量潤滑脂,對頂針復位桿加注適量頂針油。
5.7.10 模具拆下後,送至模房做落模保養。 落模射出品之保管 模具定期保養 模具達定期保養之規定時,需由模具課進行定期保養,詳細之保養時間與項目 ,請參照
〖模具定期保養記錄表〗附屬檔案 7.13 之規定。保養完畢後,將結果記錄於〖模具定期保養 記錄表〗內。 保養內容 : 5.8.1 型腔部分檢查
南昌市盛利達壓鑄廠
編號:EP05 程 序 文 件 模具管理作業程式 版本:A 頁數:2/4
5.8.2 型腔部分清理
5.8.3 注射系統檢查
5.8.4 注射系統清理
5.8.5 導向滑動部分檢查
5.8.6 導向滑動部分清理
5.8.7 頂出系統檢查
5.8.9 頂出系統清理
5.8.10 冷卻系統檢查
5.8.11 冷卻系統清理
5.8.12 支撐系統檢查
5.8.13 支撐系統清理
5.8.14 模芯檢查
5.8.15 更換模芯
5.8.16 進膠點檢查
5.8.17 更換進膠點
5.8.18 滑塊檢查、更換滑塊
5.8.19 模仁檢查、更換模仁
5.8.20 鑲塊檢查、更換鑲塊 當模具達到原本之使用壽命時 ,除依落模保養之規定進行外觀與尺寸檢查之外 , 並對模 具進定期保養 . 若有異常經修復後 , 由工程與品保部門判定模具尚可使用 , 則此模具可繼續使用 , 並 依定期保養之規定定期保養 . 落模保養結果填寫於〖落模注鑄品外觀檢查表〗, 定期保養填寫於〖模具定期保養記錄 表〗, 並皆需註明 “ 達使用壽命驗證 “ 之字樣 . 5.9 模具報廢 模具達保證壽命期限 ,不堪使用或機種停產時,由成型課提出〖資產報廢單〗(附屬檔案 7.14) 申請報廢。 經工程、 品保、 生管單位會簽確認後 ,送交總 經理核准 .必要時呈台北總 經 理核准 .並由模具房記錄於〖機器/設備/治具履歷表〗(附屬檔案 7.15)上 5.10 新模具開發 業務有需求或模具報廢后需另開新模時 ,由生管課提出 〖模具需求申請表〗 (附屬檔案 7.16) , 經會簽工程部及呈總 經理核准後進行新模具開發. 5.11 模具的盤點、轉移 模具的盤點、轉移,由成型課負責 ,並記錄於〖模具基本資料明細表〗及模具清冊內。 5.12 模具的維修 5.12.1 模具需維修時、由成型課填寫〖模具維修處理單〗(附屬檔案 7.17),經部門主管同 意 ,並會簽生管單位後 ,送交模具房維修模具 . 5.12.2 模具房依據〖模具維修處理單〗之內容維修模具 ,維修完成後將模具送回成型課 確認維修狀況 ,以確認修模之結果是否符合需求 .若不符合需求需下模再次進 行修模 . 5.12.3 試模完後 ,請品保人員進行品質確認 . 5.12.4 確認無誤後將部件及模具交回成型課 , 並於〖模具維修處理單〗上做結案 .另 維修之內容記錄於〖機器/設備/治具履歷表〗上。 5.13 模具的修改 5.13.1 若因生產效率、品質因素要求修改模具,由成型課提出修模需求. 5.13.2 若因模具設計變更, 由設計單位/ 營業單位或生技課發出 〖工程變更通知單〗 (附 件 7.18),由生技課依變更內容填寫〖模、治工具製作(維修)委託單〗(附屬檔案
南昌市盛利達壓鑄廠
編號:EP05 程 序 文 件 模具管理作業程式 版本:A 頁數:2/4
7.19)提出修模需求,模具課配合修改模具 5.13.3 修改完後由模房人員開立〖試模通知單〗請生管安排機台與時間試模。 5.13.4 試完模後 ,將修改品交給修改單位確認是否符合需求 , 若不符合需求需下模再 次進行修模 . 5.13.5 修改品確認無誤後於量產前 ,需填寫〖模具試模品質確認單〗,連同試模良品, 送交品管、生技確認。確認完成後才可轉交成型課生產。
5.13.6 完成後於〖模、治工具製作(維修)委託單〗上做結案 .另維修之內容記錄於 〖機器/設備/治具履歷表〗上。
六、參考資料 無。 七、附屬檔案 7.1 〖射出成型記錄表〗(樣張) 7.2 〖模具評估報告〗(RE08) 7.3 〖檢驗報告〗(樣張) 7.4 〖射出成型記錄表〗(RT01) 7.5 〖模具評估報告〗(RE08) 7.6 〖進料檢驗報告〗(RQ01-1) 7.7 〖試模通知單〗(RT09) 7.8 〖模具試模品質確認單〗(RT08) 7.9 〖模具基本資料明細表〗(RE09) 7.10〖模具壽命管制表〗(RT05) 7.11〖模具點檢記錄表〗(RT06) 7.12〖落模注塑品檢查表〗(RE37) 7.13〖模具定期保養記錄表〗(RE36) 7.14〖資產/消耗品報廢申請單〗(RE06) 7.15〖機器/設備/治具履歷表〗(RE01) 7.16〖模具需求申請表〗(RE48) 7.17〖模具維修處理單〗(RT07) 7.18〖工程變更通知單〗(樣張) 7.19〖模、治工具製作(維修)委託單〗(RE25)
壓鑄模具是鑄造液態模鍛的一種方法, 一種在專用的壓鑄模鍛機上完成的工藝。它的基本工藝過程是:金屬液先低速或高速鑄造充型進模具的型腔內,模具有活動的型腔面,它隨著金屬液的冷卻過程加壓鍛造,既消除毛坯的縮孔縮松缺陷,也使毛坯的內部組織達到鍛態的破碎晶粒。毛坯的綜合機械性能得到顯著的提高。
壓鑄模具是鑄造液態模鍛的一種方法, 一種在專用的壓鑄模鍛機上完成的工藝。它的基本工藝過程是:金屬液先低速或高速鑄造充型進模具的型腔內,模具有活動的型腔面,它隨著金屬液的冷卻過程加壓鍛造,既消除毛坯的縮孔縮松缺陷,也使毛坯的內部組織達到鍛態的破碎晶粒。毛坯的綜合機械性能得到顯著的提高。
產業現狀
國內壓鑄模具現狀:
我國壓鑄模具行業發展迅速,總產量增長明顯,國產壓鑄模具總產量僅次於美國,已經躍居世界第二位,成為名符其實的壓鑄大國。能有如此成就主要源於我國憑藉著得天獨厚的廣闊市場以及相對低廉的資源與勞動力優勢,已非常明顯的性價比在國際壓鑄件貿易市場中占據著較大優勢,很據形勢來看,未來我國壓鑄行業發展前景十分廣闊。
雖然我國的壓鑄模具在“十一五”期間有了重大的突破。但是其國際知名度排位仍然靠後,產量也日益攀升但是大多數壓鑄模具僅供於國內的需求。由於技術的制約使得質量難以突破,同時國內的一些大型需求企業也頻頻向國外的壓鑄模具企業伸出橄欖枝,嚴重的貿易逆差使得國內壓鑄企業舉步維艱。
國際壓鑄模具現狀
在國際壓鑄模具市場競爭日趨激烈的情境下,日本壓鑄模具業也在努力降低生產成本。在市場規模上,不論產值或國內需求以日本衰退最為明顯。日本模具廠商在技術上較重視拋光與研磨加工製程,德國模具廠商則由提高機械加工與放電加工的精度與效率著手,以降低手工加工的時間。日本壓鑄模具業正逐漸將技術含量不高的模具轉向人力成本低的地區生產,只在本國生產技術含量較高的產品,日本這種加快向國外轉移的趨勢,這使日本本國壓鑄模具使用量減少。
影響我國壓鑄模具業發展的因素分析
制約我國壓鑄模具行業發展的主要原因有:第一,國內壓鑄模具在原材料的使用上面仍有許多不足之處;第二,技術的落後,是我國壓鑄模具產業的發展受到了非常大的阻礙;第三,我國壓鑄模具業的配套體系也不完善。