概述
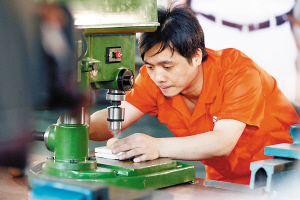
用鑽頭在實體材料上加工孔叫鑽孔。各種零件的孔加工,除去一部分由車、鏜、銑等工具機完成外,很大一部分是由鉗工利用鑽床和鑽孔工具(鑽頭、擴孔鑽、鉸刀等)完成的。
在鑽床上鑽孔時,一般情況下,鑽頭應同時完成兩個運動;主運動,即鑽頭繞軸線的鏇轉運動(切削運動);輔助運動,即鑽頭沿著軸線方向對著工件的直線運動(進給運動),鑽孔時,主要由於鑽頭結構上存在的缺點,影響加工質量,加工精度一般在IT10級以下,表面粗糙度為Ra12.5μm左右、屬粗加工。
特點
1、鑽頭轉速高。2、摩擦嚴重、散熱困難、熱量多、切削溫度高。
3、切削量大、排屑困難、易產生振動。
4、鑽頭的剛性和精度都較差,故鑽削加工精度低,一般尺寸精度為IT11~IT10,粗糙度為Ra100~25。
設備
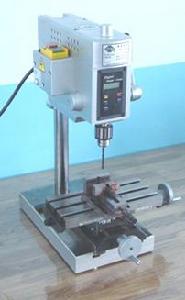
一、設備
常用的鑽床設備有台式鑽床、立式鑽床和搖臂鑽床三種,手電鑽也是常用的鑽孔工具。
1、台式鑽床
2、立式台鑽
3、搖臂鑽床
二、鑽頭
鑽頭是鑽孔用的刀削工具,常用高速鋼製造,工作部分經熱處理淬硬至62~65HRC。一般鑽頭由柄部、頸部及工作部分組成。
1、柄部
2、頸部
3、工作部分:它包括導向部分和切削部分。
三、鑽孔用的夾具
鑽孔用的夾具主要包括鑽頭夾具和工件夾具兩種。
1、鑽頭夾具:常用的是鑽夾頭和鑽套。
(1)鑽夾頭
(2)鑽套
2、工件夾具:常用的夾具有台虎鉗、平口鉗、V形鐵和壓板等。
操作方法
1、準確劃線
2、劃檢驗方格或檢驗圓
3、打樣沖眼
4、裝夾
5、試鑽
6、鑽孔
鑽孔將鑽透時,手動進給用力必須減小,以防進給量突然過大、增大切削抗力,造成鑽頭折斷、或使工件隨著鑽頭轉動造成事故。
擴孔與鉸孔
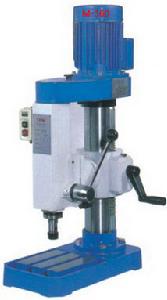
擴孔用以擴大已加工出的孔(鑄出、鍛出或鑽出的孔),它可以校正孔的軸線偏差,並使其獲得正確的幾何形狀和較小的表面粗糙度,其加工精度一般為IT9~IT10級,表面粗糙度、Ra=3.2~6.3μm。擴孔的加工餘量一般為0.2~4mm。
擴孔時可用鑽頭擴孔,但當孔精度要求較高時常用擴孔鑽(用掛圖或實物)。擴孔鑽的形狀與鑽頭相似,不同是:擴孔鑽有3~4個切削刃,且沒有橫刃,其頂端是平的,螺鏇槽較淺,故鑽芯粗實、剛性好,不易變形,導向性好。
鉸孔鉸孔是用鉸刀從工件壁上切除微量金屬層,以提高孔的尺寸精度和表面質量的加工方法。鉸孔是套用較普遍的孔的精加工方法之一,其加工精度可達IT6~IT7級,表面粗糙度Ra=0.4~0.8μm。
鉸刀是多刃切削刀具,有6~12個切削刃和較小頂角。鉸孔時導向性好。鉸刀刀齒的齒槽很寬,鉸刀的橫截面大,因此剛性好。鉸孔時因為餘量很小,每個切削刃上的負荷著小於擴孔鑽,且切削刃的前角γ0=0°,所以鉸削過程實際上是修刮過程。特別是手工鉸孔時,切削速度很低,不會受到切削熱和振動的影響,因此使孔加工的質量較高。
鉸孔按使用方法分為手用鉸刀和機用鉸刀兩種。手用鉸刀的頂角較機用鉸刀小,其柄為直柄(機用鉸刀為錐柄)。鉸刀的工作部分有切削部分和修光部分所組成。
鉸孔時鉸刀不能倒轉,否則會卡在孔壁和切削刃之間,而使孔壁劃傷或切削刃崩裂。
鉸孔時常用適當的冷卻液來降低刀具和工件的溫度;防止產生切屑瘤;並減少切屑細末粘附在鉸刀和孔壁上,從而提高孔的質量。
鑽頭
鑽頭是鑽孔用的刀削工具,常用高速鋼製造,工作部分經熱處理淬硬至62~65HRC。一般鑽頭由柄部、頸部及工作部分組成。⒈柄部:是鑽頭的夾持部分,起傳遞動力的作用,柄部有直柄和錐柄兩種,直柄傳遞扭矩較小,一般用在直徑小於12mm的鑽頭;錐柄可傳遞較大扭矩(主要是靠柄的扁尾部分),用在直徑大於12mm的鑽頭。
⒉頸部:是砂輪磨削鑽頭時退刀用的,鑽頭的直徑大小等一般也刻在頸部。
⒊工作部分:它包括導向部分和切削部分。導向部分有兩條狹長、螺紋形狀的刃帶(棱邊亦即副切削刃)和螺鏇槽。棱邊的作用是引導鑽頭和修光孔壁;兩條對稱螺鏇槽的作用是排除切屑和輸送切削液(冷卻液)。切削部分結構見掛圖與實物,它有兩條主切屑刃和一條柄刃。兩條主切屑刃之間通常為118°±2°,稱為頂角。橫刃的存在使銼削是軸向力增加。
精度控制
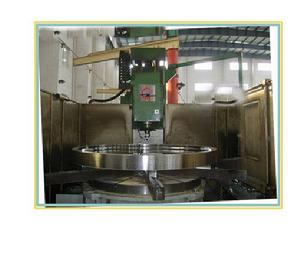
鑽孔的位置精度的控制,實質上是鑽削過程中鑽頭與工件的相互正確位置控制過程。為了考核操作者的操作技能,要求鑽孔時孔的位置調整隻能是手工、動態控制過程,不允許使用鑽模以及其他夾具,因此孔的位置精度受到劃線、工具機精度、工件和鑽頭的裝夾、鑽頭刃磨質量、工件位置及工具機切削用量的調整等一些不確定因素的影響,再加上要有一定的加工技巧和必要的保證措施,所以,當孔的位置精度要求較高時,就會導致出現嚴重超差現象。
如何有效地避免和消除孔的位置超差現象,是控制鑽孔時孔的質量關鍵。在鑽孔操作時,除了劃線正確之外,鑽正底孔、及時準確糾偏、修銼底孔的位置,是保證孔的位置精度的基礎。
劃線
由於開始鑽孔時的位置精度基本上取決於樣沖眼的位置,這樣就把動態控制孔的位置精度在一定程度上轉化為樣沖眼位置的沖制精度上來。
考慮到打樣沖眼在控制孔的位置精度時所起的重要的作用,所以,在具體操作時應注意:
①選取刀頭鋒利的高度尺,以便在加工表面上劃出孔中心線的溝痕較深,利用樣沖移動時孔中心線溝痕對它的阻力作用,來確定樣沖眼打制的正確位置。
②為了減少目測孔中心與理想位置的尺寸偏差,應劃出各尺寸孔的控制圓或控制方框(由於劃線精度的原因,建議採用劃控制方框的方法),並在鑽削過程中目測的同時,利用卡尺測量的方法,保證其位置精度。
③由於把修銼、鑽擴底孔進行糾偏方式轉移到樣沖眼位置偏差的糾正上來,可更有效地減少擴孔糾偏底孔的位置的次數,縮短操作加工時間,所以,打完樣沖眼後要仔細檢查其位置精度並作必要的糾偏。
工件及鑽頭的裝夾
由於在鑽孔過程中,如只採用目測的方法很難保證其位置精度,必須採用遊標卡尺等量具進行測量,為了方便測量,在工件安裝時要使工件高出機用虎鉗鉗口一定尺寸。鑽頭的裝夾要儘可能短,以提高其剛性和強度,從而更有利於其位置精度的保證。
鑽底孔
底孔的位置正確或者超差較小,可有效地減少擴孔糾偏底孔的位置的次數,縮短操作加工時間,對提高加工精度及加工效率具有特別重要的作用。
第一步:鑽頭直徑的選擇,鑽頭直徑太小,強度弱,加工過程中易折斷;鑽擴糾偏時,鑽頭彎曲、偏斜,導致向欲糾偏的相反方向加工,加大了原有的孔的位置誤差。鑽頭直徑太大,橫刃長,定心性能差,修銼、鑽擴糾偏孔的位置的次數相對減少。如果底孔孔徑相對圖紙規定的孔徑較大,有可能對超差的底孔不能消除。故應根據實際情況選擇合適的鑽頭,因為中心鑽既能很好定位又能保證足夠的剛度和強度,所以在鑽底孔時選用中心鑽為宜。
第二步:對正樣沖眼,中心鑽與樣沖眼的對正有兩種方法,一是用手轉動鑽夾頭,並移動平口鉗或轉動台鑽的工作檯,使中心鑽與樣沖眼對正。二是比較規整的工件儘可能處於浮動狀態,依靠鑽削力的拉動使工件位置產生微量的移動,讓鑽頭與樣沖眼自動對中。
第三步:檢測,為了提高孔的位置的檢測精度,應對檢測結果進行必要的修正:一是測量兩孔壁的最近點和最遠點,取平均值。二是採取鑽孔後插入相應的量棒再進行測量,以減小遊標卡尺測量爪非線型因素對測量結果的影響。
擴孔的位置控制
底孔的位置經檢測確定位置正確,應採取有效措施,防止在擴孔過程中孔的位置產生新的位置偏差。首先擴孔所用的鑽頭頂角要小,以減小鑽削時的徑向偏心力及振動,增大自動定心的作用和效果。然後用手轉動鑽夾頭,並移動平口鉗或轉動台鑽的工作檯,使鑽頭的兩主切削刃同時與原底孔的鑽頭進入端連線埠孔壁接觸後,再開動鑽床進行鑽孔,這樣操作基本上能保證原底孔的位置不變。
擴孔糾偏
對於孔的位置超差在0.20mm以內的底孔,可採取向糾偏方向推動工件,逐步加大鑽頭直徑進行擴孔方式加以解決。(注意:為了削弱鑽頭自動定心作用,應適當加大鑽頭頂角角度)
修銼糾偏
對於孔的位置超差大於0.20mm的底孔,若仍然採取上述方法,勢必會增加擴孔的次數和不同規格尺寸的鑽頭占有量,延長糾偏的時間。可採取圓銼修銼技術去除多餘的偏移餘量後,再配以鑽擴方式加以解決。
第一步:相關測量計算,先測量出底孔的尺寸誤差、形位誤差,如超差,相對理想位置,通過計算分析出孔的位置誤差值。然後,確定修銼底孔的方向(修銼底孔的方向,為實際孔的位置中心到理想位置中心的連線方向)和修銼孔的形狀(修銼孔的形狀應接近橢圓狀,橢圓的幾何中心與理想位置中心重合,橢圓的短軸為原底孔直徑,消除孔的位置誤差的最小底孔直徑,即為橢圓的長軸)。
第二步:選擇銼刀和修銼方法,所選的修銼圓銼直徑略小於原底孔直徑。直徑過大或等於底孔直徑,圓銼插不進底孔內或修銼時銼削困難。過小易修銼成梨狀,使鑽頭不對稱受力,鑽孔時產生新的孔的位置偏移誤差。修銼時可在台虎鉗上用手工修銼,也可藉助於鑽床主軸的鏇轉運動,把圓銼夾於鑽夾頭內,上下移動,推動工件進行加工。薄板件從底孔一端修銼即可;當工件較厚時,對於通孔來講,應從底孔兩端進行修銼,以減少銼內圓弧面與孔口端面的不垂直誤差。
第三步:擴孔,所選擴孔鑽頭的直徑應大於工件厚度中間平面的橢圓長軸的尺寸。擴孔應儘量選用短鑽頭,小的頂角、后角,低速切削。
第四步:檢測,檢測孔的尺寸精度、形位精度是否合格。如不合格,則重複上述過程,直至符合圖紙規定的技術要求為止。
在鑽孔過程中要按照先基準後一般、先高精度後一般的原則,即優先加工或保證基準位置上的孔,或尺寸精度、形位精度要求相對較高的孔。
如何有效地避免和消除孔的位置超差現象,是控制鑽孔時孔的質量關鍵,但是由於影響因素較多,所以需要反覆的強化訓練,以達到完全控制孔的位置精度的目的。這是一個循序漸進、精度逐步提高的漫長的過程。
擴孔與鉸孔
⒈擴孔擴孔用以擴大已加工出的孔(鑄出、鍛出或鑽出的孔),它可以校正孔的軸線偏差,並使其獲得正確的幾何形狀和較小的表面粗糙度,其加工精度一般為IT9~IT10級,表面粗糙度、Ra=3.2~6.3μm。擴孔的加工餘量一般為0.2~4mm。
擴孔時可用鑽頭擴孔,但當孔精度要求較高時常用擴孔鑽(用掛圖或實物)。擴孔鑽的形狀與鑽頭相似,不同是:擴孔鑽有3~4個切削刃,且沒有橫刃,其頂端是平的,螺鏇槽較淺,故鑽芯粗實、剛性好,不易變形,導向性好。
⒉鉸孔
鉸孔是用鉸刀從工件壁上切除微量金屬層,以提高孔的尺寸精度和表面質量的加工方法。鉸孔是套用較普遍的孔的精加工方法之一,其加工精度可達IT6~IT7級,表面粗糙度Ra=0.4~0.8μm。
鉸刀是多刃切削刀具,有6~12個切削刃和較小頂角。鉸孔時導向性好。鉸刀刀齒的齒槽很寬,鉸刀的橫截面大,因此剛性好。鉸孔時因為餘量很小,每個切削刃上的負荷著小於擴孔鑽,且切削刃的前角γ0=0°,所以鉸削過程實際上是修刮過程。特別是手工鉸孔時,切削速度很低,不會受到切削熱和振動的影響,因此使孔加工的質量較高。
鉸孔按使用方法分為手用鉸刀和機用鉸刀兩種。手用鉸刀的頂角較機用鉸刀小,其柄為直柄(機用鉸刀為錐柄)。鉸刀的工作部分有切削部分和修光部分所組成。
鉸孔時鉸刀不能倒轉,否則會卡在孔壁和切削刃之間,而使孔壁劃傷或切削刃崩裂。
鉸孔時常用適當的冷卻液來降低刀具和工件的溫度;防止產生切屑瘤;並減少切屑細末粘附在鉸刀和孔壁上,從而提高孔的質量。
注意事項
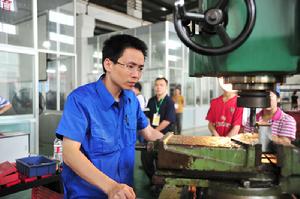
發生鑽頭折斷的主要原因除了材料的等級和鑽針的幾何形狀外,尚有以下幾種情況造成:
鑽孔機鑽機本身的震動及鑽軸的搖擺基本上隨鑽針直徑的減小而減小。
基板材料之組成鑽針之橫截面積隨鑽針直徑的減小而減小,因而,鑽屑的排除能力也逐漸下降。
孔的縱橫比
當孔的縱橫比增加時或鑽針的直徑減小,鑽孔變的困難,同時也容易斷針,特別是鑽針直徑減小後相對在碳化物合金結構中的分子顆粒就比較大(0.3毫米以下直徑鑽針)因此即使是晶粒界面或結構上的極小的缺點亦會造成超過破裂強度的影響,所以超小直徑鑽針的強度相對減弱。為彌補其強度必須增加鑽腹(Web)厚度及降低排屑槽面積的比例,也對排屑能力及切削阻力也產生副面的影響,有些實例顯示斷針也由於退屑不良造成,所以對強度的增加應著眼於高破壞強度碳化物材質的尋求及鑽針形狀的改進。
鑽孔條件
Α、鑽軸轉速(RPM)基本上鑽軸的轉速是由鑽頭的圓周速率計算出來的。
Β、進刀亮:在鑽孔過程中,進刀量與鑽針的切削阻力關係較為密切。
С、進料板或蓋板:起作用是保護線路板上的線路,減少毛頭的產生,改進孔的品質,增加放熱能力及鑽孔的精確度等。
D、穿透深度(DepthOfPenetration):是指鑽頭穿過線路板後在完成一行程所需對墊板(Back-up)所作的額外穿透程度而言,其長度由線路板每一疊最下層低面算起至鑽頭所在的最低點的位置它同樣增加了孔的縱橫比,繼而增加了斷針的頻率,所以穿透深度不能超過鑽頭的直徑,理想的穿透深度範圍應該控制在鑽針直徑的1/2或更小。
E、鑽孔方式:對小孔的鑽孔操作可採用較特殊的方法以改善孔的品質,孔位精度及減少斷針發生,較具代表性的方法是二次鑽孔(DoubleDrilling)及分段鑽孔(StepDrilling)二次鑽孔是採用兩種不同直徑的鑽針對同一孔作二次鑽孔的方法。
安全規程
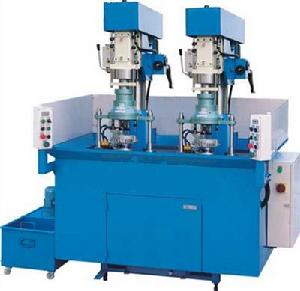
1、操作鑽床時不可帶手套,袖口必須紮緊,女工必須戴工作帽。
2、用鑽夾頭裝夾鑽頭時要用鑽夾頭鑰匙,不可用扁鐵和手錘敲擊,以免損壞夾頭和影響鑽床主軸精度。工件裝夾時,必須做好裝夾面的清潔工作。
3、工件必須夾緊,特別在小工件上鑽較大直徑孔時裝夾必須牢固,孔將鑽穿時,要儘量減小進給力。在使用過程中,工作檯面必須保持清潔。
4、開動鑽床前,應檢查是否有鑽夾頭鑰匙或斜鐵插在鑽軸上。使用前必須先空轉試車,在工具機各機構都能正常工作時才可操作。
5、鑽孔時不可用手和棉紗頭或用嘴吹來清除切屑,必須用毛刷清除,鑽出長條切屑時,要用鉤子鉤斷後除去。鑽通孔時必須使鑽頭能通過工作檯面上的讓刀孔,或在工件下面墊上墊鐵,以免鑽壞工作檯面。鑽頭用鈍後必須及時修磨鋒利。
6、操作者的頭部不準與鏇轉著的主軸靠得太近,停車時應讓主軸自然停止,不可用手去剎住,也不能用反轉制動。
7、嚴禁在開車狀態下裝拆工件。檢驗工件和變換主軸轉速,必須在停車狀況下進行。
8、清潔鑽床或加注潤滑油時,必須切斷電源。
9、鑽床不用時,必須將工具機外露滑動面及工作檯面擦淨,並對各滑動面及各注油孔加注潤滑油。
鑽孔用的夾具
鑽孔用的夾具主要包括鑽頭夾具和工件夾具兩種。⒈鑽頭夾具:常用的是鑽夾頭和鑽套。
⑴鑽夾頭:適用於裝夾直柄鑽頭。鑽夾頭柄部是圓錐面,可與鑽床主軸內孔配合安裝;頭部三個爪可通過;緊固扳手轉動使其同時張開或合攏。
⑵鑽套:又稱過渡套筒,用於裝夾錐柄鑽頭。鑽套一端孔安裝鑽頭,另一端外錐面接鑽床主軸內錐孔。
⒉工件夾具:常用的夾具有台虎鉗、平口鉗、V形鐵和壓板等。裝夾工件要牢固可靠,但又不準將工件夾得過緊而損傷過緊,或使工件變形影響鑽孔質量(特別是薄壁工件和小工件)。
鑽孔30
鑽孔30是項目西部鑽探計畫的一部份,鑽孔30位於礦權區西部,旨在測試與Musley歷史礦床有關的鉀鹽礦化帶的延伸區域並使更多的礦產被納入探明和控制礦產資源量級別。
AllanapotashCorp在鑽孔DK-11-30內發現了兩個較強的鉀鹽礦化帶。鑽孔30內193.70米深處發現了一個鉀石鹽區,其中5.35米礦段KCL品位達32.02%,包括195.20米至197.70米處KCL品位達43.85%的高品位礦段。鑽孔更深處約215.30米處也發現了一個較強的鉀鹽鎂礬岩區,其中6.90米礦段上KCL品位達22.5%。
控制方法
鑽孔的位置精度的控制,實質上是鑽削過程中鑽頭與工件的相互正確位置控制過程。為了考核操作者的操作技能,要求鑽孔時孔的位置調整隻能是手工、動態控制過程,不允許使用鑽模以及其他夾具,因此孔的位置精度受到劃線、工具機精度、工件和鑽頭的裝夾、鑽頭刃磨質量、工件位置及工具機切削用量的調整等一些不確定因素的影響,再加上要有一定的加工技巧和必要的保證措施,所以,當孔的位置精度要求較高時,就會導致出現嚴重超差現象。如何有效地避免和消除孔的位置超差現象,是控制鑽孔時孔的質量關鍵。在鑽孔操作時,除了劃線正確之外,鑽正底孔、及時準確糾偏、修銼底孔的位置,是保證孔的位置精度的基礎。
⒈劃線
由於開始鑽孔時的位置精度基本上取決於樣沖眼的位置,這樣就把動態控制孔的位置精度在一定程度上轉化為樣沖眼位置的沖制精度上來。考慮到打樣沖眼在控制孔的位置精度時所起的重要的作用,所以,在具體操作時應注意:
①選取刀頭鋒利的高度尺,以便在加工表面上劃出孔中心線的溝痕較深,利用樣沖移動時孔中心線溝痕對它的阻力作用,來確定樣沖眼打制的正確位置。
②為了減少目測孔中心與理想位置的尺寸偏差,應劃出各尺寸孔的控制圓或控制方框(由於劃線精度的原因,建議採用劃控制方框的方法),並在鑽削過程中目測的同時,利用卡尺測量的方法,保證其位置精度。③由於把修銼、鑽擴底孔進行糾偏方式轉移到樣沖眼位置偏差的糾正上來,可更有效地減少擴孔糾偏底孔的位置的次數,縮短操作加工時間,所以,打完樣沖眼後要仔細檢查其位置精度並作必要的糾偏。
⒉工件及鑽頭的裝夾
由於在鑽孔過程中,如只採用目測的方法很難保證其位置精度,必須採用遊標卡尺等量具進行測量,為了方便測量,在工件安裝時要使工件高出機用虎鉗鉗口一定尺寸。鑽頭的裝夾要儘可能短,以提高其剛性和強度,從而更有利於其位置精度的保證。
⒊鑽底孔
底孔的位置正確或者超差較小,可有效地減少擴孔糾偏底孔的位置的次數,縮短操作加工時間,對提高加工精度及加工效率具有特別重要的作用。
第一步:鑽頭直徑的選擇,鑽頭直徑太小,強度弱,加工過程中易折斷;鑽擴糾偏時,鑽頭彎曲、偏斜,導致向欲糾偏的相反方向加工,加大了原有的孔的位置誤差。鑽頭直徑太大,橫刃長,定心性能差,修銼、鑽擴糾偏孔的位置的次數相對減少。如果底孔孔徑相對圖紙規定的孔徑較大,有可能對超差的底孔不能消除。故應根據實際情況選擇合適的鑽頭,因為中心鑽既能很好定位又能保證足夠的剛度和強度,所以在鑽底孔時選用中心鑽為宜。
第二步:對正樣沖眼,中心鑽與樣沖眼的對正有兩種方法,一是用手轉動鑽夾頭,並移動平口鉗或轉動台鑽的工作檯,使中心鑽與樣沖眼對正。二是比較規整的工件儘可能處於浮動狀態,依靠鑽削力的拉動使工件位置產生微量的移動,讓鑽頭與樣沖眼自動對中。
第三步:檢測,為了提高孔的位置的檢測精度,應對檢測結果進行必要的修正:一是測量兩孔壁的最近點和最遠點,取平均值。二是採取鑽孔後插入相應的量棒再進行測量,以減小遊標卡尺測量爪非線型因素對測量結果的影響。
⒋擴孔的位置控制
底孔的位置經檢測確定位置正確,應採取有效措施,防止在擴孔過程中孔的位置產生新的位置偏差。首先擴孔所用的鑽頭頂角要小,以減小鑽削時的徑向偏心力及振動,增大自動定心的作用和效果。然後用手轉動鑽夾頭,並移動平口鉗或轉動台鑽的工作檯,使鑽頭的兩主切削刃同時與原底孔的鑽頭進入端連線埠孔壁接觸後,再開動鑽床進行鑽孔,這樣操作基本上能保證原底孔的位置不變。
⒌擴孔糾偏
對於孔的位置超差在0.20mm以內的底孔,可採取向糾偏方向推動工件,逐步加大鑽頭直徑進行擴孔方式加以解決。(注意:為了削弱鑽頭自動定心作用,應適當加大鑽頭頂角角度)
⒍修銼糾偏
對於孔的位置超差大於0.20mm的底孔,若仍然採取上述方法,勢必會增加擴孔的次數和不同規格尺寸的鑽頭占有量,延長糾偏的時間。可採取圓銼修銼技術去除多餘的偏移餘量後,再配以鑽擴方式加以解決。
第一步:相關測量計算,先測量出底孔的尺寸誤差、形位誤差,如超差,相對理想位置,通過計算分析出孔的位置誤差值。然後,確定修銼底孔的方向(修銼底孔的方向,為實際孔的位置中心到理想位置中心的連線方向)和修銼孔的形狀(修銼孔的形狀應接近橢圓狀,橢圓的幾何中心與理想位置中心重合,橢圓的短軸為原底孔直徑,消除孔的位置誤差的最小底孔直徑,即為橢圓的長軸)。
第二步:選擇銼刀和修銼方法,所選的修銼圓銼直徑略小於原底孔直徑。直徑過大或等於底孔直徑,圓銼插不進底孔內或修銼時銼削困難。過小易修銼成梨狀,使鑽頭不對稱受力,鑽孔時產生新的孔的位置偏移誤差。修銼時可在台虎鉗上用手工修銼,也可藉助於鑽床主軸的鏇轉運動,把圓銼夾於鑽夾頭內,上下移動,推動工件進行加工。薄板件從底孔一端修銼即可;當工件較厚時,對於通孔來講,應從底孔兩端進行修銼,以減少銼內圓弧面與孔口端面的不垂直誤差。
第三步:擴孔,所選擴孔鑽頭的直徑應大於工件厚度中間平面的橢圓長軸的尺寸。擴孔應儘量選用短鑽頭,小的頂角、后角,低速切削。#p#分頁標題#e#
第四步:檢測,檢測孔的尺寸精度、形位精度是否合格。如不合格,則重複上述過程,直至符合圖紙規定的技術要求為止。
在鑽孔過程中要按照先基準後一般、先高精度後一般的原則,即優先加工或保證基準位置上的孔,或尺寸精度、形位精度要求相對較高的孔。
如何有效地避免和消除孔的位置超差現象,是控制鑽孔時孔的質量關鍵,但是由於影響因素較多,所以需要反覆的強化訓練,以達到完全控制孔的位置精度的目的。這是一個循序漸進、精度逐步提高的漫長的過程。
鑽孔條件
Α.鑽軸轉速(RPM)基本上鑽軸的轉速是由鑽頭的圓周速率計算出來的.從生產力及刀具壽命的角度來看有其適宜的速度範圍.對一般直徑的鑽頭而言是100-200米/分鐘,但對於超小直徑鑽頭而言,此速
花線鑽軸
度變得相當高,甚至超過10000轉/分鐘(對0.3毫米以下直徑的鑽針而言)其最高值在120000-150000轉/分鐘之間,因此在振動及孔位精度的限制下此類高速鑽頭的選算必須從效率的角度考慮.
Β.進刀量
在鑽孔過程中,進刀量與鑽針的切削阻力關係較為密切.當進刀量增加時鑽頭所收的扭力及推力也比例的增加.對小鑽針而言,為了增加破壞強度所作的加大鑽腹及減小排屑槽面積的比例,使得鑽孔過程中推力需要增加的很多,排屑變得很不適當,因此反而不能增加進刀量.通常在鑽小孔時,進刀量控制範圍在0.005-0.03毫米/轉(0.2-0.1密耳/轉)之間.當鑽孔的直徑減小或孔的縱橫比增加時,進刀量(FeedRate)也許相對減小.
С進料板或蓋板
起作用是保護線路板上的線路,減少毛頭的產生,改進孔的品質,增加放熱能力及
鑽頭
鑽孔的精確度等.但對小孔而言蓋板的使用不完全有用,因會造成孔深度增加,及孔縱橫比的增加,在使用0.1-0.2毫米(4-8密耳)值超小鑽針時,有時不用蓋板反而能獲得更佳的結果.在使用蓋板時,厚度的選擇以工作是不產生飄動為原則下越薄越好,若材料是鋁,適當的厚度為0.1-0.2毫米,若為酚類,適當的厚度為0.3-0.5毫米(12-20密耳)較低的稜線平面及平滑的表面是對蓋板的要求,尤其是對高準確度的鑽孔
D穿透深度
(DepthOfPenetration):是指鑽頭穿過線路板後在完成一行程所需對墊板(Back-up)所作的額外穿透程度而言,其長度由線路板每一疊最下層低面算起至鑽頭所在的最低點的位置它同樣增加了孔的縱橫比,繼而增加了斷針的頻率,所以穿透深度不能超過鑽頭的直徑,理想的穿透深度範圍應該控制在鑽針直徑的1/2或更小.
E:鑽孔方式
對小孔的鑽孔操作可採用較特殊的方法以改善孔的品質,孔位精度及減少斷針發生,較具代表性的方法是二次鑽孔(DoubleDrilling)及分段鑽孔(StepDrilling)二次鑽孔是採用兩種不同直徑的鑽針對同一孔作二次鑽孔的方法.先用高剛性(HighRigidity),短排屑槽(Flute),不易彎折的鑽針先鑽出部分深
攻牙機
度以作為導引孔(GuideHole),其餘部分再用規定排屑槽長度的鑽針來完成.由於先用不易彎折的鑽針鑽出導引孔,所以第二支鑽針開始鑽時在導引孔處能容許少許彎曲(Bending),同時孔位準確度好.
孔曲(HoleDeviation)與鑽頭斷針有相當密切的關係.當孔曲超過一定值後,鑽針通常會在未達到設定的鑽孔數前斷針,所以對深孔操作鑽孔起始位置的孔位及孔曲程度是非常重要的,由此可知採用兩次鑽孔來鑽導引孔的方式是十分有效的.但在該情況下,兩次鑽孔若少有偏移導引孔位置時便會發生斷針情形,因此採用兩次鑽孔就必須使用高精確度的鑽孔機。
分段式鑽孔是以同一鑽針作多次往復式動作來完成鑽孔操作,由於在鑽孔過程中,鑽針多次提起以利散熱及排屑,因此減小斷針及提高孔的品質對含許多內層的多層板的小孔鑽孔尤為有效.例1.6毫米的板厚,0.15毫米的孔徑,出使用分段式鑽孔外,超小鑽針易產生環氧膠渣及由於切屑的拖曳形成孔壁粗糙且斷針的機會大增.
原因分析
發生鑽頭折斷的主要原因除了材料的等級和鑽針的幾何形狀外,尚有以下幾種情況造成:鑽孔機
鑽機本身的震動及鑽軸的搖擺基本上隨鑽針直徑的減小而減小。一半而言,對振動的要求位鑽振直徑在0.1-0.3毫米時,振幅在微米以下;鑽針直徑在0.35-0.5毫米時,振幅在10微米以下,同時從生產力的觀點來說,鑽針直徑減小時,鑽軸轉速必須相對增加.雖然高速鑽軸已經發展到80000轉/分鐘,但在使用最大轉速時,仍會有震動問題,高性能高頻率之氣動鑽軸正是我們所需,它允許超高速(100000轉/分鐘或更高轉速,理想值150000轉/分鐘)同時在高精度的要求下,機器的震動要限制在最小程度.
基板材料之組成
鑽針之橫截面積隨鑽針直徑的減小而減小,因而,鑽屑的排除能力也逐漸下降.此外,依據線路板製造材質的不同,鑽屑的形狀及切削阻力也跟著改變,這是有必要改變鑽孔操作條件,甚至鑽針形狀及製造材料也要修正以符合特殊要求.銅層部分(含內層)的鑽孔是特別困難的,它在切削阻力上(包括扭力及推力)都數倍於基材,甚至切削也比較長,因此基板的機械加工性主要變化在銅箔的厚度及內層銅箔的數量,換言之,即較厚的銅箔及較多的內層銅箔在鑽孔時是比較困難的.當銅箔層數增加時對鑽頭的磨損程度也增加,特別是刃帶的磨損,除此之外,隨銅箔厚度的增加及層數的增加斷針的可能性也增加.
孔的縱橫比
當孔的縱橫比增加時或鑽針的直徑減小,鑽孔變的困難,同時也容易斷針,特別是鑽針直徑減小後相對在碳化物合金結構中的分子顆粒就比較大(0.3毫米以下直徑鑽針)因此即使是晶粒界面或結構上的極小的缺點亦會造成超過破裂強度的影響,所以超小直徑鑽針的強度相對減弱,.為彌補其強度必須增加鑽腹(Web)厚度及降低排屑槽面積的比例,也對排屑能力及切削阻力也產生副面的影響,有些實例顯示斷針也由於退屑不良造成.所以對強度的增加應著眼於高破壞強度碳化物材質的尋求及鑽針形狀的改進.
安全制度
⒈操作鑽床時不可帶手套,袖口必須紮緊,女工必須戴工作帽。⒉用鑽夾頭裝夾鑽頭時要用鑽夾頭鑰匙,不可用扁鐵和手錘敲擊,以免損壞夾頭和影
工作帽
響鑽床主軸精度。工件裝夾時,必須做好裝夾面的清潔工作。
⒊工件必須夾緊,特別在小工件上鑽較大直徑孔時裝夾必須牢固,孔將鑽穿時,要儘量減小進給力。在使用過程中,工作檯面必須保持清潔。
⒋開動鑽床前,應檢查是否有鑽夾頭鑰匙或斜鐵插在鑽軸上。使用前必須先空轉試車,在工具機各機構都能正常工作時才可操作。
⒌鑽孔時不可用手和棉紗頭或用嘴吹來清除切屑,必須用毛刷清除,鑽出長條切屑時,要用鉤子鉤斷後除去。鑽通孔時必須使鑽頭能通過工作檯面上的讓刀孔,或在工件下面墊上墊鐵,以免鑽壞工作檯面。鑽頭用鈍後必須及時修磨鋒利。
⒍操作者的頭部不準與鏇轉著的主軸靠得太近,停車時應讓主軸自然停止,不可用手去剎住,也不能用反轉制動。
⒎嚴禁在開車狀態下裝拆工件。檢驗工件和變換主軸轉速,必須在停車狀況下進行。
⒏清潔鑽床或加注潤滑油時,必須切斷電源。
⒐鑽床不用時,必須將工具機外露滑動面及工作檯面擦淨,並對各滑動面及各注油孔加注潤滑油。
鑽孔事故
鑽孔事故,是提高鑽進效率和降低成本的最大障礙。因此,必須加以防止,使事故的發生率降低到最低程度。並且在事故發生後,能及時得到正確的處理。經驗證明,鑽孔事故的發生,雖有客觀原因,但只要主觀上重視,在工作中貫徹執行各項操作規程,掌握技術,認真操作,隨時採取有效的預防措施,事故是可以減少和避免的。
鑽探工作者,應熟悉各種孔內事故發生的原因以及發生錢的預兆,才能在工作中加以防止。如事故以及發生,應首先弄清產生的原因和目前孔內情況,只要掌握事故原因及孔內情況後,才能進行處理。不能盲目從事,以免處理不當又發生重複事故,增加問題的嚴重性和複雜性。
通常鑽孔中發生的有鑽具阻留事故,鑽具折斷事故和孔口落入工具鐵件事故等。
第一類:鑽具阻留事故
⒈卡鑽:凡是所下管柱及工具在井內不能上提、下放或轉動的現象。
⒉夾鑽:即粗徑鑽具在孔壁或套管之間被鑽粒或硬岩石粗顆粒夾住,雖不堵水或不完全堵水,但鑽具被阻留在孔內,起不出來。
⒊埋鑽:是指鑽孔上部的孔段在鑽進中倒塌,將鑽具掩埋在孔底。
⒋淤鑽:是指由於大量的細粒岩粉或流砂填塞於鑽具周圍及上部,將鑽具淤住,停水便不能鑽進,鑽具提不上來。
⒌燒鑽:是指在鑽進中缺水,粗徑鑽具底部發高熱,與孔壁燒結在一起,拔不出來。
第二類:鑽具折斷事故
粗徑鑽具折斷,即指鑽進中由於三用接頭處的鑽桿接頭絲扣斷開;岩心管的絲扣斷開或脫扣;鑽頭接手與鑽頭的絲扣斷開或脫扣,講粗徑鑽具的某一部分掉落在孔底。
鑽桿折斷,即指鑽進中或在處理其他鑽孔事故時,因受力過大,使鑽桿或鑽桿接頭折斷,將鑽具丟落在孔底。
第三類:工具鐵件落入鑽孔事故
該類事故即指鑽場上的工具或鐵件掉入鑽孔中,影響起鑽和鑽進而言。