基本內容
產生背景
二戰結束不久,汽車工業中統治世界的生產模式是以美國福特製為代表的大量生產方式,這種生產方式以流水線形式少品種、大批量生產產品。在當時,大批量生產方式即代表了先進的管理思想與方法,大量的專用設備、專業化的大批量生產是降低成本,提高生產率的主要方式。與處於絕對優勢的美國汽車工業相比,日本的汽車工業則處於相對幼稚的階段,豐田汽車公司從成立到1950年的十幾年間,總產量甚至不及福特公司1950年一天的產量。汽車工業作為日本經濟倍增計畫的重點發展產業,日本派出了大量人員前往美國考察。豐田汽車公司在參觀美國的幾大汽車廠之後發現,採用大批量生產方式降低成本仍有進一步改進的餘地,而且日本企業還面臨需求不足與技術落後等嚴重困難;加上戰後日本國內的資金嚴重不足,也難有大量的資金投入以保證日本國內的汽車生產達到有競爭力的規模,因此他們認為在日本進行大批量少品種的生產方式是不可取的,而應考慮一種更能適應日本市場需求的生產組織策略。
以豐田的大野耐一等人為代表的精益生產的創始者們,在不斷探索之後,終於找到了一套適合日本國情的汽車生產方式:及時制生產、全面質量管理、並行工程、充分協作的團隊工作方式和集成的供應鏈關係管理,逐步創立了獨特的多品種、小批量、高質量和低消耗的精益生產方法。1973年的石油危機,使日本的汽車工業閃亮登場。由於市場環境發生變化,大批量生產所具有的弱點日趨明顯,而豐田公司的業績卻開始上升,與其它汽車製造企業的距離越來越大,精益生產方式開始為世人所矚目。
從精益生產到精益思想
20世紀90年代美國進行了一系列的對精益生產的研究和實踐。這其中包括美國軍方1993年出台的美國“國防製造企業戰略”、“精益航空計畫Lean Aerospace Initiative”等政府指令性的活動。除了汽車行業又有更多的美國企業如波音、洛克希德馬丁、普惠等投入到實施精益生產的大潮中來。在這個過程中,日本人提供了基本的思考和方法,用出色的實踐證明了精益生產的強大生命力;美國學者的研究、美國企業、乃至美國政府的研究和實踐,則證明了精益思想在世界上的普遍意義,並升華為新一代的生產哲理。終於在1996年James Womack和Daniel Jones 的《精益思想(Lean Thinking)》一書問世,精益生產方式由經驗變成為理論,新的生產方式正式誕生。 從上述精益思想發展的歷程說明,精益思想是人、過程和技術的集成。無論是豐田生產方式、還是後來的精益生產,都是從技術的改變和技術的可行開始的。過程的思想則是豐田生產方式產生的基礎。而人則是決定性的因素。精益思想比大批量生產關鍵性的改革是組織結構和分工原則的變化,這是解放被大量生產的分工和等級制度所束縛著的員工積極性的重要進步。
思想核心
概述
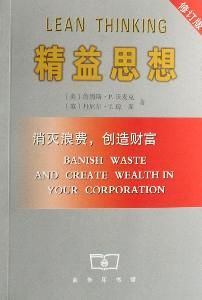
在市場競爭中遭受失敗的美國汽車工業,在經歷了曲折的認識過程後,終於意識到致使其競爭失敗的關鍵是
美國汽車製造業的大批量生產方式輸給豐田的精益生產方式。1985年,美國麻省理工學院的Daniel T.Jones教授等籌資500萬美元,用了近5年的時間對90多家汽車廠進行對比分析,於1992年出版了《改變世界的機器》一書,把豐田生產方式定名為精益生產,並對其管理思想的特點與內涵進行了詳細的描述。四年之後,該書的作者出版了它的續篇《精益思想》,進一步從理論的高度歸納了精益生產中所包含的新的管理思維,並將精益方式擴大到製造業以外的所有領域,尤其是第三產業,把精益生產方法外延到企業活動的各個方面,不再局限於生產領域,從而促使管理人員重新思考企業流程,消滅浪費,創造價值。
核心
精益思想的核心就是(消除浪費)以越來越少的投入——較少的人力、較少的設備、較短的時間和較小的場地創造出儘可能多的價值;同時也越來越接近用戶,提供他們確實要的東西。精確地定義價值是精益思想關鍵性的第一步;確定每個產品(或在某些情況下確定每一產品系列)的全部價值流是精益思想的第二步;緊接著就是要使保留下來的、創造價值的各個步驟流動起來,使需要若干天才能辦完的訂貨手續,在幾小時內辦完,使傳統的物資生產完成時間由幾個月或幾周減少到幾天或幾分鐘;隨後就要及時跟上不斷變化著的顧客需求,因為一旦具備了在用戶真正需要的時候就能設計、安排生產和製造出用戶真正需要的產品的能力,就意味著可以拋開銷售,直接按用戶告知的實際要求進行生產,這就是說,可以按用戶需要拉動產品,而不是把用戶不想要的產品硬推給用戶。
實踐
精益思想包括精益生產、精益管理、精益設計和精益供應等一系列思想,其核心是通過“及時適量”、“零庫存”、“傳票卡”等現場管理手段實現“訂貨生產”,從而確保產品質量並降低成本。精益思想最初是體現在對產品質量的控制中,即指不追求產品的成本優勢和技術領先,而是強調產品的成本與技術的合理匹配、協調。此後,企業界將精益思想逐步引伸、延展到企業經營活動的全過程,即追求企業經營投入和經濟產出的最大化、價值最大化。從字面意思來看,“精”體現在質量上,追求“盡善盡美”、“精益求精”;“益”體現在成本上,只有成本低於行業平均成本的企業才能獲得收益。因而,精益思想不單純追求成本最低、企業眼中的質量最優,而是追求用戶和企業都滿意的質量、追求成本與質量的最佳配置、追求產品性能價格的最優比。
思想原則
概述
什麼是精益管理?精益企業到底是怎樣的面貌呢?詹姆斯·沃麥克(James Womack)和丹尼爾·瓊斯(Daniel Jones)在他們精闢的著作《精益思想》中提煉出精益管理五原則,顧客確定價值(Customervalue)、識別價值流(Value stream mapping)、價值流動(Value flow)、拉動(Pulling)、盡善盡美(Perfection)。精益管理的核心思想可概括為消除浪費、創造價值。
精益管理是精益生產理論的擴展,是精益思想在企業各層面的深入套用,精益管理是以精益思想為指導、以持續追求浪費最小、價值最大的生產方式和工作方式為目標的管理模式。
顧客確定價值
顧客確定價值就是以客戶的觀點來確定企業從設計到生產到交付的全部過程,實現客戶需求的最大滿足。以客戶的觀點確定價值還必需將生產的全過程的多餘消耗減至最少,不將額外的花銷轉嫁給用戶。精益價值觀將商家和客戶的利益統一起來,而不是過去那種對立的觀點。以客戶為中心的價值觀來審視企業的產品設計、製造過程、服務項目就會發現太多的浪費,從不滿足客戶需求到過分的功能和多餘的非增值消耗。當然,消滅這些浪費的直接受益者既是客戶也是商家。與之對照的是,企業過去的價值觀都是以自己為中心的。完全由商家設計和製造的產品、完全由商家設計好的服務項目,大吹大擂那些目的在於增加贏利的、額外的、甚至是“畫蛇添足”的功能,並不一定是用戶所需要的、或必需的。最後將大量的浪費以成本的方式轉嫁給了用戶。而用戶享受到的僅僅是為實現這個轉嫁的殷勤。
識別價值流
價值流是指從原材料轉變為成品、並給它賦予價值的全部活動。這些活動包括:從概念到設計和工程、到投產的技術過程,從訂單處理、到計畫、到送貨的信息過程,和從原材料到產品的物質轉換過程,以及產品全生命周期的支持和服務過程。精益思想識別價值流的含義是在價值流中找到那些是真正增值的活動、那些是可以立即去掉的不增值活動。精益思想將所有業務過程中消耗了資源而不增值活動叫做浪費。識別價值流就是發現浪費和消滅浪費。識別價值流的方法是“價值流分析 Value Stream map Analysis”——首先按產品族為單位畫出當前的價值流圖,再以客戶的觀點分析每一個活動的必要性。價值流分析成為實施精益思想最重要的工具。
價值流並不是從自己企業的內部開始的,多數價值流都向前延伸到供應商,向後延長到向客戶交付的活動。按照最終用戶的觀點全面的考察價值流、尋求全過程的整體最佳,特別是推敲部門之間交接的過程,往往存在著更多的浪費。
價值流動
如果正確的確定價值是精益思想的基本觀點、識別價值流是精益思想的準備和入門的話,“流動Flow”和“拉動 Pull”則是精益思想實現價值的中堅。精益思想要求創造價值的各個活動(步驟)流動起來,強調的是不間斷地“流動”。“價值流”本身的含義就是“動”的,但是由於根深蒂固的傳統觀念和做法,如部門的分工(部門間交接和轉移時的等待)、大批量生產(工具機旁邊等待的在制品)等等阻斷了本應動起來的價值流。精益將所有的停滯作為企業的浪費,號召“所有的人都必須和部門化的、批量生產的思想做鬥爭”,用持續改進、JIT、單件流(one-piece flow)等方法在任何批量生產條件下創造價值的連續流動。當然,使價值流流動起來,必需具備必要的環境條件。這些條件是:過失、廢品和返工都造成過程的中斷、回流。實現連續的流動要求每個過程和每個產品都是正確的。全面質量管理和後來的 6 Sigma 都成為精益思想的重要組成部分。環境、設備的完好性是流動的保證。5S、TPM 全員生產保全都是價值流動的前提條件之一。有正確規模的人力和設備能力,避免瓶頸造成的阻塞。
需求拉動
“拉動”就是按客戶的需求投入和產出,使用戶精確的在他們需要的時間得到需要的東西。實行拉動以後用戶或製造的下游就象在超市的貨架上一樣地取到他們所需要的東西,而不是把用戶不太想要的產品強行推給用戶。拉動原則由於生產和需求直接對應,消除了過早、過量的投入,而減少了大量的庫存和現場在制品,大量的壓縮了提前期。拉動原則更深遠的意義在於企業具備了當用戶一旦需要,就能立即進行設計、計畫和製造出用戶真正需要的產品的能力,最後實現拋開預測,直接按用戶的實際需要進行生產。
實現拉動的方法是實行 JIT 生產和單件流。當然,JIT 和單件流的實現最好採用單元布置,對原有的製造流程做深刻的改造。流動和拉動將使產品開發時間減少 50%、訂貨周期減少 75%、生產周期降低 90%,這對傳統的改進來說簡直是個奇蹟。
盡善盡美
奇蹟的出現是由於上述 4 個原則相互作用的結果。改進的結果必然是價值流動速度顯著的加快。這樣就必須不斷地用價值流分析方法找出更隱藏的浪費,作進一步的改進。這樣的良性循環成為趨於盡善盡美的過程。Womack 又反覆地闡述了精益製造的目標是:“通過盡善盡美的價值創造過程(包括設計、製造和對產品或服務整個生命周期的支持)為用戶提供盡善盡美的價值”。“盡善盡美”是永遠達不到的,但持續地對盡善盡美的追求,將造就一個永遠充滿活力、不斷進步的企業。由顧客確定產品價值結構
什麼是精益企業,我們認為,精益企業是把精益管理套用於企業所有層面,從管理系統上能有效杜絕浪費,從文化上人人竭力追求持續改善,並實現經營業績卓越、持續競爭力強的企業。
國內精益思想
與世界先進國家相比,我國的企業界和學術界對精益思想尚缺乏系統的和足夠高度的認識,在有組織的進行精益思想的普及教育和推廣方面存在太大的差距,更大範圍套用精益思想幾乎還是空白。隨著一汽、寶鋼對精益運營的成功實施,國內的企業也逐漸意識到了精益運營管理的重要性及其廣大的套用前景,紛紛在抓緊研究套用。
精益生產在上世紀70年代末期由日本引入我國。長春第一汽車製造廠是最早引進精益生產方式的企業。1979年下半年,“一汽”開始邊學習,邊創造條件,邊試點,逐步推廣套用精益生產模式。1981年,精益生產的創始入之一,豐田公司的大野耐一先生訪問了“一汽”,幫助推廣精益生產方式,內容主要是套用看板系統控制生產現場作業。到1984年,在短短的實行精益生產四年的時間裡,在20個專業廠有283 1種汽車零部件實行看板取貨,42種協作產品由協作廠直送工位,壓縮了流動資金1830萬元,取消中間倉庫17個,節約倉庫面積1661平方米。在看板取貨的基礎上組織了看板生產,全廠10條生產線61種零件實行了看板生產。80年代初,中國企業管理協會組織推廣現代管理方法,看板管理被作為推廣的現代管理方法之一,在全國範圍內進行宣傳,並為許多企業所採用。在《改變世界的機器》一書中文版於1991年在中國出版後,中國製造業開始廣泛學習和試圖導入此先進生產方式。
同名書籍基本信息
作者:(美)詹姆斯 P.沃麥克(James P.Womack)/(英)丹尼爾 T.瓊斯(Daniel T.Jones)
譯者:沈希瑾/張文杰/李京生
出版社:機械工業出版社
出版年: 2011-5
頁數: 351
定價: 48.00元
ISBN: 9787111337546
內容簡介
打算嘗試精益的人,該怎么做?
已經實行精益的人,下一步怎么辦?
本書包含了最新的精益理論、方法和工具,一一解答上述問題。
這是目前關於流程再造最好的書,也是最好讀的。——《高業周刊》
本書中文簡體字版由FreePress通過AiWA授權機械工業出版社在中國大陸獨家出版發行。未經出版者書面許可,不得以任何方式抄襲、複製或節錄本書中的任何部分。
《精益思想》於1996年秋季首次出版,歷經10年,暢銷十多個國家,銷量達到幾十萬冊以上。本書的成功在於它對精益生產方式做了最好的總結,為讀者提供了精益的核心原則,實地考察了美國、德國、日本若干具有代表性的大小企業推行精益的實際情況和心得,為準備跨入精益之門和進一步學習、實施精益的人提供了最好的指南,從而成為精益方面的經典著作。
精益原則:根據客戶需求,重新定義價值;識別價值流,重新制定企業活動;使價值流動起來;依靠客戶需求拉動價值流;不斷改善,追求盡善盡美。
作者簡介
Janes P.Wonack,前MIF資深教授,為企業提供精益諮詢,也向小型製造廠投資。他創辦了精益企業研究所(LEI)並擔任所長,這家研究所是一個非営利教育和研究機構,致力於精益思想的傳播和套用。
目錄
修訂版前言
第1版前言從精益生產到精益企業
第一部分 精益原則
導論和浪費針鋒相對的精益思想
第1章價值
第2章價值流
第3章流動
第4章拉動
第5章盡善盡美
第二部分 從思想到行動:精益的飛躍
第6章簡單事例
第7章複雜事例
第8章嚴峻的考驗
第9章精益思想和德國技術
第10章大豐田,小昭和