粉末冶金成形
正文
粉末冶金生產中的基本工序之一,目的是將鬆散的粉末製成具有預定幾何形狀、尺寸、密度和強度的半成品或成品。模壓(鋼模)成形是粉末冶金生產中採用最廣的成形方法。18世紀下半葉和19世紀上半葉,西班牙、俄國和英國為製造鉑製品,都曾採用了相似的粉末冶金工藝。當時俄國索博列夫斯基(П.Г.Соболевсκий)使用的是鋼模和螺鏇壓機。英國的沃拉斯頓(W.H.Wollaston)使用壓力更大的拉桿式壓機和純度更高的鉑粉,製得了幾乎沒有殘餘孔隙的緻密鉑材。後來,模壓成形方法逐漸完善,並用來製造各種形狀的銅基含油軸承等產品。20世紀30年代以來,在粉末冶金零件的工業化生產過程中,壓機設備、模具設計等方面不斷改進,模壓成形方法得到了更大的發展,機械化和自動化已達到較高的程度。為了擴大製品的尺寸和形狀範圍,特別是為了提高製品密度和改善密度的均勻性相繼出現和發展了多種成形方法。早期出現的有粉末軋制、冷等靜壓制、擠壓、熱壓等;50年代以來又出現了熱等靜壓制、熱擠壓、熱鍛等熱成形方法。這些方法推動了全緻密、高性能粉末金屬材料的生產。模壓成形 將金屬粉末裝入鋼模型腔,通過模沖對粉末加壓使之成形。
模壓過程 裝在模腔中的粉末由於顆粒間的摩擦和機械嚙合作用會產生所謂“拱橋”現象,形成許多大小不一的孔隙。加壓時,粉末體的體積被壓縮,其過程一般用壓坯相對密度-壓制壓力曲線表示(圖1)。在開始階段粉末顆粒相對移動並重新分布,孔隙被填充,從而使壓坯密度急劇增加,達到最大裝填密度;這時粉末顆粒已被相互壓緊,故當壓制壓力增大時,壓坯密度幾乎不變,曲線呈現平坦。隨後繼續增加壓制壓力,粉末顆粒將發生彈、塑性變形或脆性斷裂,使壓坯進一步緻密化。由於顆粒間的機械嚙合和接觸面上的金屬原子間的引力,壓制後的粉末體成為具有一定強度的壓坯。有關粉末壓制理論,從1923年沃克(E.E.Walker)公布他的論點開始,已出現有數十種理論和經驗公式,其中阿吉(L.F.Athy,1930)、巴利申(Μ.Ю.Бальшин,1938)、川北公夫(1963)等人的公式有一定的實用意義;儘管如此,這些理論至今仍處於探索階段。
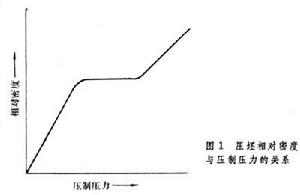
彈性後效 壓坯在除去壓力或脫模以後,由於內應力鬆弛,壓坯體積發生彈性膨脹,這種現象稱為彈性後效。彈性後效是設計壓模的重要參數。
壓模和壓機 模壓成形的主要設備是壓模和壓機。壓模設計的原則是:充分發揮粉末冶金少切削和無切削的工藝特點,保證達到壓坯質量的三項要求(即幾何形狀、尺寸精度和光潔度、密度的均勻性);合理地選擇模具材料和壓模結構,提出模具的加工要求。壓機分為機械壓機和液壓機兩類。機械壓機的特點是速度快,生產率高;其缺點是壓力較小,衝程短,衝壓不夠平穩,保壓困難,不適於壓制較大和較長的製品。與機械壓機相比,液壓機(圖2)的特點是壓力大,行程長,比較平穩,能實現無級調速和保壓,適於壓制尺寸較大較長的製品;其缺點是速度慢,生產率低。
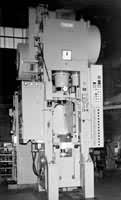
等靜壓 通過液體或氣體傳遞壓力使粉末體各向均勻受壓而實現緻密化的方法,稱為等靜壓制,簡稱等靜壓(見等靜壓加工)。等靜壓可分為冷等靜壓和熱等靜壓兩種。
冷等靜壓 通常是將粉末密封在軟包套內,然後放到高壓容器內的液體介質中,通過對液體施加壓力使粉末體各向均勻受壓,從而獲得所需要的壓坯。液體介質可以是油、水或甘油。包套材料為橡膠之類的彈塑性材料。金屬粉末可直接裝套或模壓後裝套。由於粉末在包套內各向均勻受壓,所以可獲得密度較均勻的壓坯,因而燒結時不易變形和開裂。其缺點是壓坯尺寸精度差,還要進行機械加工。冷等靜壓已廣泛用於硬質合金、難熔金屬及其他各種粉末材料的成形。
熱等靜壓 這是50年代出現的新技術。將金屬粉末裝入高溫下易於變形的包套內,然後置於可密閉的缸體中(內壁配有加熱體的高壓容器),關嚴缸體後用壓縮機打入氣體並通電加熱。隨著溫度升高,缸內氣體壓力增大。粉末在這種各向均勻的壓力和溫度的作用下成為具有一定形狀的製品。加壓介質一般用氬氣。常用的包套材料為金屬(低碳鋼、不鏽鋼、鈦),還可用玻璃和陶瓷。由於溫度和等靜壓力的同時作用,可使許多種難以成形的材料達到或接近理論密度,並且晶粒細小,結構均勻,各向同性和具有優異的性能。熱等靜壓法最適宜於生產硬質合金、粉末高溫合金、粉末高速鋼和金屬鈹等材料和製品;也可對熔鑄製品進行二次處理,消除氣孔和微裂紋;還可用來製造不同材質緊密粘接的多層或複合材料與製品。
粉末鍛造 將金屬粉末壓製成預成形坯,燒結後再加熱進行鍛造(見模鍛),以減少甚至完全消除其中的殘餘孔隙的方法,稱為粉末鍛造。其鍛造方式有三種:①熱復壓。預成形坯的形狀接近成品形狀,外徑略小於鍛模模腔內徑。因為鍛造時材料不發生橫向流動,鍛件有0~2%的殘餘孔隙度。②無飛邊鍛造。這種鍛造在限模中進行,材料有橫向流動,鍛件不產生飛邊。③閉模鍛造。預成形坯的形狀較簡單,且外徑比鍛模內徑小得多,鍛造時產生飛邊,是一種與常規鍛造相類似的方法。無飛邊鍛造和閉模鍛造常用於生產要求緻密度很高的零件。預成形坯的設計和製造是粉末鍛造的關鍵步驟之一。此外,對於熱鍛預成形坯必須加以保護,以免氧化和脫落的氧化皮陷入鍛件中造成鍛造廢品。粉末鍛件的密度可達理論密度的98%以上。與常規鍛造相比,粉末鍛造的壓力小,溫度低,材料利用率高,工藝簡單,尺寸精確;鍛件的性能可接近普通鍛件,而且方向性小。粉末鍛件廣泛套用於汽車工業、運輸機械等方面。
粉末擠壓 粉末擠壓的優點在於擠壓件長度尺寸不受限制,產品密度均勻,生產可連續進行、效率高、靈活性大,設備簡單、操作方便。粉末擠壓又分為金屬粉末直接擠壓和裝包套後熱擠壓兩種(見擠壓加工)。
直接擠壓 將塑性良好的有機物和金屬粉末混合後,置入擠壓模具內,在外力作用下使增塑粉末通過一定幾何形狀的擠壓嘴擠出,成為各種管材、棒材及其他異形的半成品。影響擠壓過程的主要因素是增塑劑的含量、預壓壓力、擠壓溫度和擠壓速度。
包套擠壓 熱擠壓能把熱壓和熱塑性加工結合在一起,從而獲得全緻密的優質材料;但為了防止粉末或壓坯氧化,需要將它們裝入包套內進行熱擠壓。包套的材質必須滿足下列要求:包套材料在擠壓溫度下的剛性應儘量接近被擠壓粉末,不與粉末發生反應並可通過酸洗或機械加工的方法除掉。
粉末軋制 將金屬粉末餵入一對轉動的軋輥輥縫中,由於摩擦力的作用粉末被軋輥連續壓縮成形的方法。它是生產板帶狀粉末冶金材料的主要工藝。一般包括粉末直接軋制、粉末粘接軋制和粉末熱軋等。粉末軋制的特點是:能生產特殊結構和性能的材料,成材率高,工序少,設備投資小,生產成本低。
其他方法 ①松裝燒結。用於製造各種多孔材料和製品,如過濾器等。②粉漿澆注。可製造各種複雜形狀的製品,如管、坩堝、球形器皿及空心製品等。③高能高速成形和爆炸成形。可製造大型、複雜形狀製品,如渦輪葉片等。近年來用於成形激冷凝固粉末引起了普遍的重視。④軟模成形。可成形諸如球體、圓錐體、多台階體等各種普通壓制方法難以成形的壓坯。⑤楔形壓制。適用於製造環形長製品和較厚的帶材。⑥放電成形。用於中、小型而且形狀複雜的製品成形。
配圖
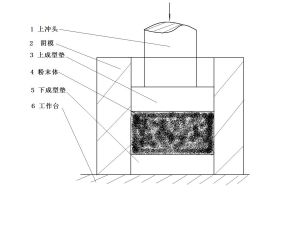
在壓機的工作檯上放好模具,如右圖所示,連線在壓機上的沖頭,在壓機的壓力作用下,粉末體
被壓成預定的形狀,然後去壓力,沖頭自動抬起。在陰模底下墊一個合適的圈再用壓機的沖頭把
陰模內的下成型墊、壓好的毛坯、上成型墊一起頂出來,······。這樣,就完成了一次成型。這是
最基本的成型方法。隨著科學技術的發展······。