基本簡介
與端面相關常用的概念是端面跳動,下面就解釋一下什麼是端面跳動。
端面跳動是指車輪的側面(與軸垂直的平面)平不平,誤差多大。測量方法是把車輪按基準面固定在轉軸上後,旋轉車輪,用表接觸其端面(側面),測出來的值。
用途:車輪端面不平時,在行走中會發生左右搖擺情況。
端面磨削原理
端面磨削主要是由送料盤、兩片砂輪組成的一種磨削方法。
滾子裝在送料盤的工作孔內,送料盤旋轉時,使滾子通過兩片砂輪中間的磨削區;砂輪進行高速旋轉,用兩片砂輪的端面同時磨出相互平行的滾子兩個端面。
當滾子由送料盤傳送到磨削區時,由於兩片砂輪同向高速旋轉的作用,使滾子母線貼靠著工作孔的內表面,滾子實現自轉。但滾子自轉的線速度遠遠低於砂輪切削點的線速度,加之送料盤作圓弧形運動的送進,而形成了砂輪對滾子的兩端面磨削,使滾子獲得理想的垂直度、平行度及端面粗糙度。
磨削特點:
1、同時進行兩端面磨削,利用送料盤送進,可以連續性生產,生產率高。
2、磨削時,利用兩砂輪的切削力,使滾子外圓母線貼靠著工作孔的內表面,可見這是以滾子外圓作定位基準,工作孔的內表面相當於支撐。
3、雙端面磨削過程和無心貫穿磨削過程相似,也要有引導、磨削及磨光區域,為此對兩砂輪的端面應進行修整;使之不相互平行,而是分別與送料盤的迴轉平面對稱地傾斜一定角度。
4、磨削時,可以得到較均勻的尺寸,易於實現自動上下料。
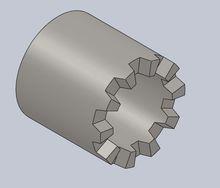
5、工藝(工具機)調整規律較難掌握,從磨削原理可以看出,滾子在工作孔內的支撐位置是隨砂輪磨削位置變化而變化,所以他們的定位方式很不完善,給調整帶來一定困難。
端面銑床安全操作規程
(1)操作者必須熟悉工具機的性能、結構、傳動系統、潤滑系統、操作手柄和開關等。嚴禁超性能、超負荷使用工具機。
(2)開車前按設備點檢卡檢查工具機,按規定加油、保證油質、油量和各部分潤滑良好。
(3)夾具和工件必須裝卡牢靠,其中心應該在工作檯中心位置。刀具拉近螺母必須鎖緊。
(4)工具機只有在裝上防護裝置並調整合適後,才允許開動,以防止切屑飛出、切削液飛濺、對操作者造成傷害。
(5)不得擅自鬆動極限行程撞塊,不允許超行程使用工具機。
(6)只有在工具機停止運轉後,才能進行刀具裝卸。
(7)主軸旋轉前,應確認主軸上的刀具已經夾緊。
(8)在主軸運轉過程中,嚴禁變換主軸轉速,嚴禁調整銑頭角度。不準用機動對刀和上刀,刀具進給運動未脫開時不得停車。
(9)使用工作檯縱向工作時,應將橫向和垂直方向緊固螺釘鎖緊,使用橫向工作時,則將縱向和垂直方向擰緊,以免工作檯振動。
(10)用刀盤銑削平面時,刀頭不得少於4個。加工較重的工件時,要裝上支撐架。
(11)在用快速走刀和自動進給時,應事先調整好限程擋塊。
(12)在加工過程中,注意身體的任何部位或衣服不要被外露的旋轉零件纏繞。
(13)本工具機的各種手柄、按鈕等只能由一人獨立操作,不允許兩名以上操作者同時操作工具機。
(14)操作者在使用工具機時,禁止蹬踏床身底座,雙手不得接觸工具機的任何運動部位。
(15)在加工過程中,不應清理切屑。
(16)隨時檢查工具機的潤滑情況,及時補充潤滑油。
(17)操作者使用工具機時,應注意不要被工具機的突出部位磕碰。
(18)操作者在操作工具機時,要密切注視切削情況,遇到突發危險,應按急停按鈕。
(19)工具機斷電順序應遵守先按下停止按鈕,再切斷總電源的原則。
(20)工作後將工作檯放在導軌中間,升降台落在下面。各手柄放在非工作位置,切斷電源,並清掃鐵屑,擦拭工具機,做好各項保養工作。
外圓與端面的加工工藝
在車削加工中最常見、最基本的加工就是車外圓。而且車外圓與車床上其他的加工形式有著密切的關係。因此,必須熟練掌握車外圓技術。
零件的裝夾
正確安裝的目的就是使工件在整個切削過程中始終保持正確的位置,工件安裝的質量和速度,直接影響到工件的加工質量和效率。同時,所有加工表面都位於零件的外圓上的,加工時將產生較大的切削力。車外圓時主切削力的方向與工件軸線不重合,必然的要影響到工件的穩固性。在數控車床上進行外圓加工一般可採用下面幾種裝夾方式:
(1)使用普通三爪卡盤安裝,工件安裝後一般不需要校正,只控制長度即可。
(2)利用軟卡爪,並適當增加夾持面的長度,以保證定位準確,裝夾穩固。
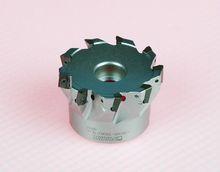
(3)利用尾座及頂尖做輔助,採用一夾一頂方式裝夾,最大限度的保證零件的穩固性。
選擇刀具及加工方式
外圓加工是最基本、最簡單的加工步驟,所選用的刀具其結構和種類也較普通。
(1)選擇通用標準刀具,選擇餘地較大。
(2)儘量選擇機夾不重磨刀具,有利於標準化選擇。
(3)可根據零件材料選擇特殊刀具。
加工路線主要是根據零件的形狀和毛坯來確定。當零件精度較低且餘量較小時,可不分粗、精車一刀車出,加工效率較高;當零件餘量較大時,不分粗、精車會使刀具前面壓力過大出現扎刀和折斷刀具的現象,應採用分次進刀的粗車方式,達到降低切削力和斷屑的目的。同時注意儘量的選擇強度較高的刀具。
切削用量與切削液的選擇
背吃刀量、進給速度和切削速度是切削用量三要素,受加工過程中,切削力的影響,切削速度大小可以調節的範圍較小。要增加切削穩定性,提高切削效率,就要在背吃刀量和進給速度上面做文章。在普通車床上進行外圓加工,切削速度和進給速度的選擇相對較低,一般取80~100米/分鐘。數控車床的各項精度要遠高於普通車床,在切削用量的選取上就可以選擇相對較高的速度。
端面加工可能出現的問題
1、工件外圓尺寸超差
原因:(1)刀具數據不準確
(2)切削用量選擇不當產生讓刀
(3)程式錯誤
(4)工件尺寸計算錯誤
2、外圓表面光潔度太差
原因:(1)切削速度過低
(2)刀具中心過高
(3)切屑控制較差
(4)刀尖產生積屑瘤
(5)切削液選用不合理
3、加工過程中出現扎刀引起工件報廢
原因:(1)進給量過大
(2)切屑阻塞
(3)工件安裝不合理
(4)刀具角度選擇不合理