施工準備
材料
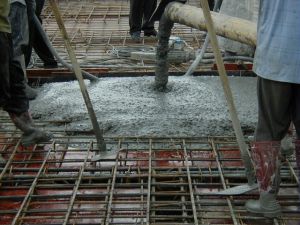
砂:細砂。混凝土低於C30時含泥量不大於5%,高於C30 時含泥量不大於3%。
石子:粒徑16-30mm,混凝土低於C30時含泥量不大於2%。高於C30時不大於1%。
混凝土外加劑:FJ-1泵送劑。應符合有關標準的規定,其摻量經試驗符合要求後,方可使用。
作業條件
1.澆築混凝土層段的模板、鋼筋、預埋鐵件及管線等全部安裝完畢,經檢查合格,符合設計要求,並辦完隱蔽、預檢手續。2.澆築混凝土用架子及走道已支搭完畢,經檢查合格。
3.水泥、砂、石及外加劑等經檢查符合有關標準要求,試驗已下達混凝土配合比通知單。
4.電子計量器經檢查衡量準確、靈活,振搗器(棒)經檢驗試運轉正常。
操作工藝
清理
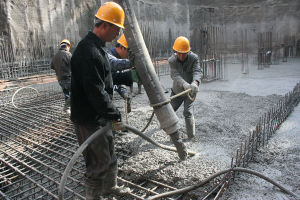
混凝土攪拌
1.根據配合比確定每盤各種材料用量,骨料含水率應經常測定及時調整配合比用水量。2.裝料順序:一般先倒石子,再裝水泥,最後倒砂子。摻外加劑時,粉狀外加劑應根據每盤加量應預加工裝入小包裝內(塑膠袋為宜),用時與細粗骨料同時加入;液狀外加劑應按每盤用量與水同時裝入攪拌機攪拌。
3.攪拌時間:為使混凝土攪拌均勻,自全部拌合料裝入攪拌筒中起到混凝土開始卸料為止,混凝土攪拌的最短時間為90秒(1.5分鐘)。
混凝土運輸
泵送混凝土時必須保證混凝土泵連續工作,如發生故障,停歇時間超過45分鐘或混凝土出現離析現象,應立即用壓力水或其他方法沖洗管內殘留的混凝土。振搗要求
1.混凝土自料口下落的自由傾落高度不得超過2米,如超過2米時必須採取措施。2.澆築混凝土時應分段分層連續進行,每層澆築高度應根據結構特點、鋼筋疏密程度決定,一般分層高度為振搗器作用部分長度的1.25倍,最大不超過50厘米。
3.使用插入式振搗器應快插慢拔,插點要均勻排列,逐點移動,順序進行,不得遺漏,做到均勻振實。移動間距不大于振搗棒作用半徑的1.5倍(一般為30-40cm)。振搗上一層時應插入下層5cm,以消除兩層間的接隙。
4.澆築混凝土應連續進行。如必須間歇,其間歇時間應儘量縮短,並應在前層混凝土初凝之前,將次層混凝土澆築完畢。
5.澆築混凝土時應經常觀察模板、鋼筋、預留孔洞、預埋件和插筋等有無移動、變形或堵塞情況,發現問題應立即停止澆灌,並應在已澆築的混凝土凝結前修正完好。
柱的澆築
1.柱澆筑前底部應先填以5-10cm厚與混凝土配合比相同的減半石子混凝土,柱混凝土應分層振搗,使用插入式振搗器時每層厚度不大於50cm,振搗棒不得觸動鋼筋和預埋件。除上面振搗外,下面要有人隨時敲打模板。2.柱高在3米之內,可在柱頂直接下灰澆築,柱高超過3米時應採取措施用串筒分段澆築。每段的高度不得超過2米。
3.柱子混凝土應一次澆築完畢,如需留施工縫時應留在主梁下面。
梁板澆築
1.肋形樓板的梁板應同時澆築,澆築方法應由一端開始用“趕漿法”,即先將梁根據梁高分層澆築成階梯形,當達到板底位置時再與板的混凝土一起澆築,隨著階梯形不斷延長,梁板混凝土澆築連續向前推進。2.和板連成整體的大斷面允許將梁單獨澆築,其施工縫應留在板底以下2-3cm處。澆搗時,澆築與振搗必須緊密配合,第一層下料慢些,梁底充分振實後再下二層料。用“趕漿法”保持水泥漿沿梁底包裹石子向前推進,每層均應振實後再下料,梁底及梁膀部位要注意振實,振搗時不得觸動鋼筋及預埋件。
3.樑柱結點鋼筋較密時,澆築此處混凝土時宜用細石子同強度等級混凝土澆築,並用小直徑振搗棒振搗。
4.澆築板的虛鋪厚度應大於板厚,用插入式振搗器順澆築方向拖拉振搗,並用鐵插尺檢查混凝土厚度,振搗完畢後用長木抹子抹平。施工縫處或有預埋件及插筋處用木抹子找平。澆築板混凝土時不允許用振搗棒鋪攤混凝土。
5.施工縫位置:沿著次梁方向澆築樓板,施工縫應留置在次梁跨度的中間三分之一範圍內。施工縫的表面應與梁軸線或板面垂直,不得留斜槎。施工縫宜用木板或鋼絲網擋牢。
6.施工縫處須待已澆築混凝土的抗壓強度不小於1.2MPa時,才允許繼續澆築,在繼續澆築混凝土前,施工縫混凝土表面應鑿毛,剔除浮動石子,並用水沖冼乾淨後,先澆一層水泥漿,然後繼續澆築混凝土,應細緻操作振實,使新舊混凝土緊密結合。
樓梯澆築
1.樓梯段混凝土自下而上澆築,先振實底板混凝土,達到踏步混凝土一起澆搗,不斷連續向上推進,並隨時用木抹子將踏步上表面抹平。2.施工縫:樓梯混凝土宜連續澆築完,多層樓梯的施工縫應留置在樓梯段三分之一部位。
養護
混凝土澆築完畢後,應在12h以內加以覆蓋和澆水,澆水次數應保持混凝土有足夠的濕潤狀態,養護期一般不少於7晝夜。質量標準
保證項目
1.混凝土所用的水泥、水、骨料、外加劑等必須符合施工規範及有關規定,檢查出廠合格證或試驗報告是否符合質量要求。2.混凝土的配合比、原材料計量、攪拌、養護和施工縫處理必須符合施工規範規定。
3.混凝土強度的試塊取樣、製作、養護和試驗要符合《混凝土強度檢驗評定標準》(GBJ107-87)的規定。
4.結構嚴禁出現裂縫。
基本項目
混凝土應振搗密實,不得有蜂窩、孔洞、露筋、縫隙、夾渣等缺陷。允許偏差
軸線位移5mm垂直度8mm標高±10mm截面尺寸:+8,-5mm表面平整度:8mm預埋管件5mm
成品保護
1.要保證鋼筋和墊塊的位置正確,不得踩樓板、樓梯的彎起鋼筋,不碰動預埋件和插筋。2.不用重物衝擊模板,不在梁或樓梯踏步模板吊幫上登踩,應搭設跳板,保護模板的牢固和嚴密。
3.已澆築樓板、樓梯踏步的上表面混凝土要加以保護,必須在混凝土強度達到1.2MPa以後,方準在面上進行操作及安裝結構用的支架和模板。
注意問題
1、蜂窩:原因是混凝土一次下料過厚,振搗不實或漏振;模板有縫隙水泥漿流失;鋼筋較密而混凝土坍落度過小或石子過大;基礎、柱、牆根部下層台階澆築後未停歇就繼續澆築上層混凝土,以致上層混凝土根部砂漿從下部湧出而造成。2、露筋:原因是鋼筋墊塊位移,間距過大、漏放,鋼筋緊貼模板造成露筋或梁、板底部振搗不實也可能出現露筋。
3、麻面:模板表面不光滑或模板濕潤不夠,構件表面混凝土易粘附在模板上造成脫皮麻面。
4、孔洞:原因是在鋼筋較密的部位混凝土被卡,未經振搗就繼續澆築上層混凝土。
5、縫隙及夾層:施工縫處雜物清理不淨或未澆底漿等原因造成縫隙、夾層。
6、梁、柱結點處斷面尺寸偏差過大:主要原因是柱接頭模板剛度太差。
7、現澆樓板和樓梯上表面平整偏差太大:主要原因是混凝土澆築後表面不認真用抹子抹平。
基本條件
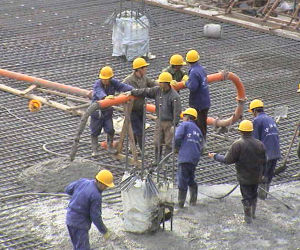
2、當工地晝夜平均氣溫連續3d低於5C或最低氣溫低於-3C時,應按冬期施工辦理,混凝土的入模溫度不應低於5C。
3、新澆混凝土入模溫度與鄰接的己硬化混凝土或岩土、鋼筋、模板介質間的溫差不得大於15C。與新澆築混凝土接觸的己硬化混凝土、岩土介質、鋼筋和模板的溫度不得低於2°C。
4、在相對濕度較小、風速較大的環境條件下,可釆取場地灑水、噴霧、擋風等措施,或在此時避免澆築有較大暴露面積的構件。
5、混凝土應分層澆築,分層厚度(指搗實後厚度)應根據攪拌與運輸能力、澆築速度、振搗能力和結構特點等條件確定。泵送混凝土的最大攤鋪厚度不宜大於600mm,其它混凝土最大攤鋪厚度不宜大於400mm。
在新澆築完成的下層混凝土上再澆築新混凝土時,應在下層混凝土初凝前澆築完成上層混凝土。上下層同時澆築時,上層與下層前後澆築距離應保持1.5m以上。在傾斜面上澆築混凝土時,應從低處開始逐層擴展升高,保持水平分層。
6、混凝土澆築應連續進行。當因故間歇時,其間歇時間應小於前層混凝土的初凝時間。對不同混凝土的允許間歇時間應根據環境溫度、水泥性能、水膠比和外加劑類型等條件通過試驗確定。
當超過允許間歇時間時,應按澆築中斷處理,同時應留置施工縫,並作出記錄。施工縫的平面應與結構的軸線相垂直。
7、在澆築混凝土過程中或澆築完成時,如混凝土表面泌水較多,須在不擾動已澆築混凝土的條件下,釆取措施將水排除。繼續澆築混凝土時,應查明原因,釆取措施,減少泌水。
8、澆築混凝土期間,應設專人檢查支架、模板、鋼筋和預埋件等的穩固情況,當發現有鬆動、變形、移位時,應及時處理。