正文
利用蒸汽熱能作功的熱能動力裝置。其基本組成部分有汽輪機本體、凝汽器、循環水泵、凝結水泵、給水加熱裝置以及這些部件之間的管道和附屬檔案。汽輪機發電動力裝置與電廠鍋爐配套,組成火電廠的動力部分。汽輪機與發電機組成汽輪發電機組,前者驅動後者發出電能。原理 由鍋爐產生的具有一定壓力和溫度的過熱蒸汽進入汽輪機內膨脹做功,蒸汽的壓力和溫度都大為降低,排汽進入凝汽器,在循環水的冷卻作用下凝結成水,其潛熱由從循環水泵不斷送入凝汽器的循環水帶走。排出的凝結水由凝結水泵從凝汽器底部的集水箱中抽出,經由回熱系統及給水泵後,送往鍋爐作為鍋爐的給水(見圖)。
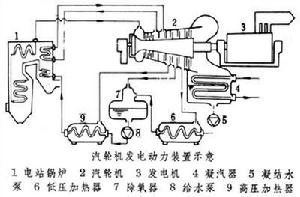
提高熱效率的方法 衡量汽輪機動力裝置熱效率的常用指標為熱耗率,其含義是生產一個單位電功率所需要的熱量。現代大容量汽輪發電機組的熱耗率為7900千焦/千瓦時左右。提高汽輪機動力裝置的熱效率主要有5個方法。
①採用給水回熱循環。將已經在汽輪中膨脹做功的蒸汽,在某一合適的參數下從汽輪機中抽出一部分,並用這部分蒸汽來加熱送往鍋爐的給水。與純冷凝循環相比,回熱循環中排給冷源的熱量損失要小一些,因為從汽輪機中抽出來的那部分蒸汽的熱能完全被用來加熱給水,不再構成冷源損失,進入凝汽器的熱量相應減少了,從而提高了循環熱效率。對不同進汽參數的汽輪機裝置,都分別有一個最佳抽汽回熱量(常以最佳給水溫度表示)。加熱給水的抽汽通常是在汽輪機不同壓力點上多次抽出並逐級將給水加熱的。這樣,以較低溫度的抽汽先加熱較低溫度的給水,這部分抽汽就能在汽輪機內多做些功,從而進一步提高裝置的熱效率。理論上,給水回熱的級數越多,裝置熱效率也就提高越多。但過多的回熱級數會增加設備投資費用。一般是中等功率汽輪機動力裝置的回熱系統不超過4~5級,高參數大功率裝置(100兆瓦以上)採用7~8級基至9級給水回熱。
②提高蒸汽參數。理論上,熱源與冷源的溫度決定在此溫差範圍內的任何熱機所能具有的最高熱效率。因此,儘可能提高汽輪機動力裝置的新蒸汽參數,降低排汽溫度,可顯著提高該裝置的熱效率。現代製造的汽輪機動力裝置採用的初蒸汽溫度基本上已達到了當前冶金工業技術經濟水平所能達到的最高極限值(565℃左右)。再提高汽溫則需要大量使用價格昂貴、加工工藝複雜的奧氏體鋼,綜合經濟效果並非有利。提高進汽壓力也能提高該裝置的熱效率。但在一定的進汽溫度下,過高的進汽壓力會導致排汽濕度增大,不但會加大濕汽損失,而且會加劇低壓部分葉片的沖刷腐蝕。所以現代汽輪機動力裝置參數的提高,主要體現在中間再熱循環的採用上。
③採用中間再熱循環。將在汽輪機的高壓部分(通常是高壓缸內)已膨脹做功的蒸汽(溫度和壓力都有所降低,其壓力一般在主汽壓力的18~22%)從汽輪機中全部引出,送至鍋爐的再熱器中再次加熱(一般加熱到新蒸汽同樣水平的溫度),然後再引回汽輪機內(一般為中壓缸的進汽端),繼續膨脹做功。採用中間再熱能起到與提高進汽溫度同樣的效果,又能降低排汽的濕度。從而為在進汽溫度的提高受到金屬材料限制的情況下進一步提高進汽壓力提供了可能。現代大容量高參數的汽輪機動力裝置都採用中間再熱循環。採用一次中間再熱,一般可使裝置的熱效率提高5%以上。如採用二次中間再熱,可使機組的熱效率再提高2%左右。但過多次的中間再熱會使汽輪機動力裝置的結構布置及運行方式過於複雜。
④採用雙工質聯合循環。利用熱力性能不同的工質組成聯合動力裝置,可改善整個裝置的經濟性。一個主要的聯合方式是,以高溫工質循環的排氣(汽)作為低溫工質循環的熱源。聯合裝置的工質有燃氣-蒸汽、汞蒸氣-蒸汽、蒸汽-氨(或氟里昂)等多種形式(見圖)。
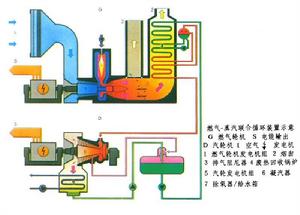