氨合成
正文
指合成氨原料氣(氮氫混合氣)在高溫、高壓和催化劑存在下直接合成為氨的工藝過程。其反應式為:鐵催化劑的活性 氨合成採用添加有助催化劑的鐵催化劑。助催化劑的成分有氧化鉀、 氧化鋁、 氧化鎂、氧化鈣、氧化鈷等。開工前鐵催化劑組成(FeO·Fe2O3)可看作四氧化三鐵(見金屬氧化物催化劑),其中Fe2+/Fe3+通常約為0.5(原子比),它對氨合成反應沒有催化作用,開工操作時需用氫氣將它還原成金屬鐵才有活性。
Fe3O4+4H2─→3Fe+4H2O
不同還原條件下得到的催化活性有很大差異。正常生產時,鐵催化劑常因氮氫混合氣中含有少量硫化合物、碳的氧化物等氣體而降低活性,通常規定一氧化碳和二氧化碳不超過10ppm(體積)。鐵催化劑的壽命(見催化劑壽命)與其製造質量、使用條件有密切關係,短的1~2年,長的可達8~9年。氨的分離 氨合成的單程轉化率不高,為了取得產品氨,需將氨氣從氨合成塔出口氣中分離出來。工業上通常用兩種方法:①冷凝法,利用氨的臨界溫度比氮、氫高的特點,只需把含氨混合氣冷卻,其中的氨即可從氣態冷凝成液態。溫度越低,冷凝的氨越多。工業生產都採用產品液氨作製冷劑。為了節省製冷劑用量,混合氣先用水冷卻。②吸收法,利用氨氣在水中的溶解度比氮、氫氣大的性質,在高壓下用水吸收,製成濃氨水。從濃氨水製取液氨尚需經過氨水精餾、氨氣冷凝等步驟,消耗熱能較多,工業上已很少採用。但近年利用有機溶劑吸收氨的研究,已取得了進展。
迴路流程 為使氨合成塔出口氣中的氮、氫氣在氨氣分離以後能繼續循環利用,採用迴路流程,以便返回到氨合成塔。此法的保證條件是:①不斷補充新鮮氮氫混合氣進入迴路;②從氨合成塔出口氣中分離氨;③為補償迴路氣體壓力損失而設定循環氣壓縮機;④回收利用氨合成反應熱;⑤為避免新鮮氮氫混合氣中少量甲烷和氬等惰性氣體在迴路中積累過多,必須排放適量的循環氣。為此,設計有多種迴路流程。
早期氨合成流程多採用往復式壓縮機,反應熱未加利用。出塔氣體先經水冷卻,一部分氨被冷凝,再進入氨分離器。為降低循環氣中甲烷、氬的含量,出氨分離器後的氣體要少量放空,大部分則進入循環氣壓縮機,補充壓力後進入濾油器,新鮮氮氫混合氣也在此加入。混合後氣體通過冷交換器內上部的換熱器與分離液氨後的循環氣體換熱,然後在氨冷凝器中冷卻到0℃以下,使大部分氨冷凝並返回冷交換器內下部的分離器,在此分離出液氨。分離氨後的氣體去上部換熱器,被加熱到20~30℃進氨合成塔,從而完成一個循環。
現代氨合成流程採用離心式壓縮機(見彩圖),可以回收反應熱(見圖)。
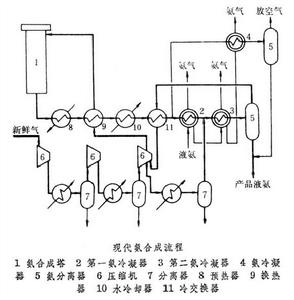
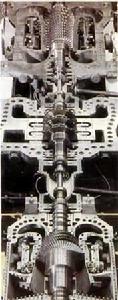
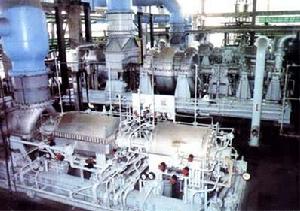