基本介紹
車床是主要用車刀對鏇轉的工件進行車削加工的工具機。在車床上還可用鑽頭、擴孔鑽、鉸刀、絲錐、板牙和 滾花工具等進行相應的加工。車床主要用於加工軸、盤、套和其他具有迴轉表面的工件,是機械製造和修配工廠中使用最廣的一類工具機。
常見類型
車床的常見類型如下:
車床
車床是主要用車刀對鏇轉的工件進行車削加工的工具機。在車床上還可用鑽頭、擴孔鑽、鉸刀、絲錐、板牙和滾花工具等進行相應的加工。車床主要用於加工軸、盤、套和其他具有迴轉表面的工件,是機械製造和修配工廠中使用最廣的一類工具機。
古代滑輪、弓形桿的“弓車床”早在古埃及時代,人們已經發明了將木材繞著它的中心軸鏇轉時用刀具進行車削的技術。起初,人們是用兩根立木作為支架,架起要車削的木材,利用樹枝的彈力把繩索卷到木材上,靠手拉或腳踏拉動繩子轉動木材,並手持刀具而進行切削。
這種古老的方法逐漸演化,發展成了在滑輪上繞二三圈繩子,繩子架在彎成弓形的彈性桿上,來回推拉弓使加工物體鏇轉從而進行車削,這便是“弓車床”。
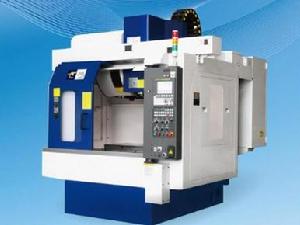
中世紀曲軸、飛輪傳動的“腳踏車床”到了中世紀,有人設計出了用腳踏板鏇轉曲軸並帶動飛輪,再傳動到主軸使其鏇轉的“腳踏車床”。16世紀中葉,法國有一個叫貝松的設計師設 計了一種用螺絲槓使刀具滑動的車螺絲用的車床,可惜的是,這種車床並沒有推廣使用。
十八世紀誕生了床頭箱、卡盤時間到了18世紀,又有人設計了一種用腳踏板和連桿鏇轉曲軸,可以把轉動動能貯存在飛輪上的車床上,並從直接鏇轉工件發展到了鏇轉床頭箱,床頭箱是一個用於夾持工件的卡盤。
英國人莫茲利發明了刀架車床(1797年)在發明車床的故事中,最引人注目的是一個名叫莫茲利的英國人,因為他於1797年發明了劃時代的刀架車床,這種車床帶有精密的導螺桿和可互換的齒輪。
莫茲利生於1771年,18歲的時候,他是發明家布拉默的得力助手。據說 ,布拉默原先一直是乾農活的,16歲那年因一次事故致使右踝傷殘,才不得不改行從事機動性不強的木工活。他的第一項發明便是1778年的抽水馬桶,莫茲利開始一直幫助布拉默設計水壓機和其他機械,直到26歲才離開布拉默,因為布拉默粗暴地拒絕了莫利茲提出的把工資增加到每周30先令以上的請求。
就在莫茲利離開布拉默的那一年,他製成了第一台螺紋車床,這是一台全金屬的車床,能夠沿著兩根平行導軌移動的刀具座和尾座。導軌的導向面是三角形的,在主軸鏇轉時帶動絲槓使刀具架橫向移動。這是近代車床所具有的主要機構,用這種車床可以車制任意節距的精密金屬螺絲。
3年以後,莫茲利在他自己的車間裡製造了一台更加完善的車床,上面的齒輪可以互相更換,可改變進給速度和被加工螺紋的螺距。1817年,另一位英國人羅伯茨採用了四級帶輪和背輪機構來改變主軸轉速。不久,更大型的車床也問世了,為蒸汽機和其他機械的發明立下了汗馬功勞。
各種專用車床的誕生為了提高機械化自動化程度,1845年,美國的菲奇發明轉塔車床;1848年,美國又出現回輪車床;1873年,美國的斯潘塞製成一台單軸自動車床,不久他又製成三軸自 動車床 ;20世紀初出現了由單獨電機驅動的帶有齒輪變速箱的車床。由於高速工具鋼的發明和電動機的套用,車床不斷完善,終於達到了高速度和高精度的現代水平。
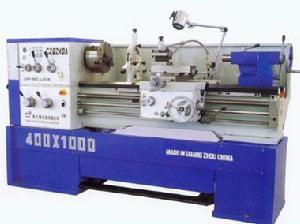
第一次世界大戰後,由於軍火、汽車和其他機械工業的需要,各種高效自動車床和專門化車床迅速發展。為了提高小批量工件的生產率,40年代末,帶液壓仿形裝置的車床得到推廣,與此同時,多刀車床也得到發展。50年代中,發展了帶穿孔卡、插銷板和撥碼盤等的程式控制車床。數控技術於60年代開始用於車床,70年代後得到迅速發展。
車床的分類車床依用途和功能區分為多種類型。
普通車床的加工對象廣,主軸轉速和進給量的調整範圍大,能加工工件的內外表面、端面和內外螺紋。這種車床主要由工人手工操作,生產效率低,適用於單件、小批生產和修配車間。
轉塔車床和迴轉車床具有能裝多把刀具的轉塔刀架或回輪刀架,能在工件的一次裝夾中由工人依次使用不同刀具完成多種工序,適用於成批生產。
自動車床能按一定程式自動完成中小型工件的多工序加工,能自動上 下料,重複加工一批同樣的工件,適用於大批、大量生產。
多刀半自動車床有單軸、多軸、臥式和立式之分。單軸臥式的布局形式與普通車床相似,但兩組刀架分別裝在主軸的前後或上下,用於加工盤、環和軸類工件,其生產率比普通車床提高3~5倍。
仿形車床能仿照樣板或樣件的形狀尺寸,自動完成工件的加工循環,適用於形狀較複雜的工件的小批和成批生產,生產率比普通車床高10~15倍。有多刀架、多軸、卡盤式、立式等類型。
立式車床的主軸垂直於水平面,工件裝夾在水平的迴轉工作檯上,刀架在橫樑或立柱上移動。適用於加工較大、較重、難於在普通車床上安裝的工件,一般分為單柱和雙柱兩大類。
鏟齒車床在車削的同時,刀架周期地作徑嚮往復運動,用於鏟車銑刀、滾刀等的成形齒面。通常帶有鏟磨附屬檔案,由單獨電動機驅動的小砂輪鏟磨齒面。
專門車床是用於加工某類工件的特定表面的車床,如曲軸車床、凸輪軸車床、車輪車床、車軸車床、軋輥車床和鋼錠車床等。
聯合車床主要用於車削加工,但附加一些特殊部件和附屬檔案後,還可進行鏜、銑、鑽、插、磨等加工,具有“一機多能”的特點,適用於工程車、船舶或移動修理站上的修配工作。
鏜床
工場手工業雖然是相對落後的,但是它卻訓練和造就了許許多多的技工,他們儘管不是專
門製造機器的行家裡手,但他們卻能製造各種各樣的手工器具,例如 刀、鋸、針、鑽、錐、磨以及軸類、套類、齒輪類、床架類等等,其實機器就是由這些零部件組裝而成的。
最早的鏜床設計者——達·芬奇鏜床被稱為“機械之母”。說起鏜床,還先得說說達·芬奇。這位傳奇式的人物,可能就是最早用於金屬加工的鏜床的設計者。他設計的鏜床是以水力或腳踏板作為動力,鏜削的工具緊貼著工件鏇轉,工件則固定在用起重機帶動的移動台上。1540年,另一位畫家畫了一幅《火工術》的畫,也有同樣的鏜床圖,那時的鏜床專門用來對中空鑄件進行精加工。
為大炮炮筒加工而誕生的第一台鏜床(威爾金森,1775年)到了17世紀,由於軍事上的需要,大炮製造業的發展十分迅速,如何製造出大炮的炮筒成了人們亟需解決的一大難題。
世界上第一台真正的鏜床是1775年由威爾金森發明的。其實,確切地說,威爾金森的鏜床是一種能夠精密地加工大炮的鑽孔機,它是一種空心圓筒形鏜桿,兩端都安裝在軸承上。
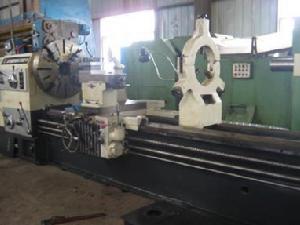
1728年,威爾金森出生在美國,在他20歲時,遷到斯塔福德郡,建造了比爾斯頓的第一座煉鐵爐。因此,人稱威爾金森為“斯塔福德郡的鐵匠大師”。1775年,47歲的威爾金森在他父親的工廠里經過不斷努力,終於製造出了這種能以罕見的精度鑽大炮炮筒的新機器。有意思的是,1808年威爾金森去世以後,他就葬在自己設計的鑄鐵棺內。
鏜床為瓦特的蒸汽機做出了重要貢獻如果說沒有蒸汽機的話,當時就不可能出現第一次工業革命的浪潮。而蒸汽機自身的發展和套用,除了必要的社會機遇之外,技術上的一些前提條件也是不可忽視的,因為製造蒸汽機的零部件,遠不像木匠削木頭那么容易,要把金屬製成一些特殊形狀,而且加工的精度要求又高,沒有相應的技術設備是做不到的。比如說,製造蒸汽機的汽缸和活塞,活塞製造過程中所要求的外徑的精度,可以從外面邊量尺寸邊進行切削,但要滿足汽缸內徑的精度要求,採用一般加工方法就不容易做到了。
斯密頓是十八世紀最優秀的機械技師。斯密頓設計的水車、風車設備達43件之多。在製作蒸汽機時,斯密頓最感棘手的是加工汽缸。要想將一個大型的汽缸內圓加工成圓形,是相當困難的。為此,斯密頓在卡倫鐵工廠製作了一台切削汽缸內圓用的特殊工具機。用水車作動力驅動的這種鏜床,在其長軸的前端安裝上刀具,這種刀具可以在汽缸內轉動,以此就可以加工其內圓。由於刀具安裝在長軸的前端,就會出現軸的撓度等問題,所以,要想加工出真正圓形的汽缸是十分困難的。為此,斯密頓不得不多次改變汽缸的位置進行加工。
對於這個難題,威爾金森於1774年發明的鏜床起了很大的作用。這種鏜床利用水輪使材料圓筒鏇轉,並使其對準中心固定的刀具推進,由於刀具與材料之間有相對運動,材料就被鏜出精確度很高的圓柱形孔洞。當時、用鏜床做出直徑為72英寸的汽缸,誤差不超過六便士硬幣的厚度。用現代技術衡量,這是個很大的誤差,但在當時的條件下,能達到這個水平,已經是很不簡單了。
但是,威爾金森的這項發明沒有申請專利保護,人們紛紛仿造它,安裝它。1802年,瓦特也在書中談到了威爾金森的這項發明,並在他的索霍鐵工廠里進行仿製。以後,瓦特在製造蒸汽機的汽缸和活塞時,也套用了威爾金森這架神奇的機器。原來,對活塞來說,可以在外面一邊量著尺寸,一邊進行切削,但對汽缸就不那么簡單了,非用鏜床不可。當時,瓦特就是利用水輪使金屬圓筒鏇轉,讓中心固定的刀具向前推進,用以切削圓筒內部,結果,直徑75英寸的汽缸,誤差還不到一個硬幣的厚度,這在當對是很先進的了。
工作檯升降式鏜床誕生(赫頓,1885年)在以後的幾十年間,人們對威爾金森的鏜床作了許多改進。1885年,英國的赫頓製造了工作檯升降式鏜床,這已成為了現代鏜床的雛型。
銑床
銑床系指主要用銑刀在工件上加工各種表面的工具機。通常銑刀鏇轉運動為主運動,工件(和)銑刀的移動為進給運動。它可以加工平面、溝槽,也可以加工各種曲面、齒輪等。銑床是用銑刀對工件進行銑削加工的工具機。銑床除能銑削平面、溝槽、輪齒、螺紋和花鍵軸外,還能加工比較複雜的型面,效率較刨床高,在機械製造和修理部門得到廣泛套用。
19世紀,英國人為了蒸汽機等工業革命的需要發明了鏜床、刨床,而美國人為了生產大量的武器,則專心致志於銑床的發明。銑床是一種帶有形狀各異銑刀的機器,它可以切削出特殊形狀的工件,如螺鏇槽、齒輪形等。
早在1664年,英國科學家胡克就依靠鏇轉圓形刀具製造出了一種用於切削的機器,這可算是原始的銑床了,但那時社會對此沒有做出熱情的反響。在十九世紀四十年代,普拉特設計了所謂林肯銑床。當然,真正確立銑床在機器製造中地位的,要算美國人惠特尼了。
第一台普通銑床(惠特尼,1818年)1818年,惠特尼製造了世界上第一台普通銑床,但是,銑床的專利卻是英國的博德默(帶有送刀裝置的龍門刨床的發明者)於1839年捷足先“得”的。由於銑床造價太高,所以當時問津者不多。
第一台萬能銑床(布朗,1862年)銑床沉默一段時間後,又在美國活躍起來。相比之下,惠特尼和普拉特還只能說是為銑床的發明套用做了奠基性的工作,真正發明能適用於工廠各種操作的銑床的功績應該歸屬美國工程師約瑟夫·布朗。
1862年,美國的布朗製造出了世界上最早的萬能銑床,這種銑床在備有萬有分度盤和綜合銑刀方面是劃時代的創舉。萬能銑床的工作檯能在水平方向鏇轉一定的角度,並帶有立銑頭等附屬檔案。他設計的“萬能銑床”在1867年巴黎博覽會上展出時,獲得了極大的成功。同時,布朗還設計了一種經過研磨也不會變形的成形銑刀,接著還製造了磨銑刀的研磨機,使銑床達到了現在這樣的水平。
刨床
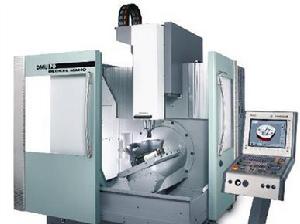
在發明過程中,許多事情往往是相輔相承、環環相扣的:為了製造蒸汽機,需要鏜床相助;蒸汽機發明發後,從工藝要求上又開始呼喚龍門刨床了。可以說,正是蒸汽機的發明,導致了“工作母機”從鏜床、車床向龍門刨床的設計發展。其實,刨床就是一種刨金屬的“刨子”。
加工大平面的龍門刨床(1839年)由於蒸汽機閥座的平面加工需要,從19世紀初開始,很多技術人員開始了這方面的研究,其中有理察·羅伯特、理察·普拉特、詹姆斯·福克斯以及約瑟夫·克萊門特等,他們從1814年開始,在25年的時間內各自獨立地製造出了龍門刨床。這種龍門刨床是把加工物件固定在往返平台上,刨刀切削加工物的一面。但是,這種刨床還沒有送刀裝置,正處在從“工具”向“機械”的轉化過程之中。到了1839年,英國一個名叫博默德的人終於設計出了具有送刀裝置的龍門刨床。
加工小平面的牛頭刨床另一位英國人內史密斯從1831年起的40年內發明製造了加工小平面的牛頭刨床,它可以把加工物體固定在床身上,而刀具作往返運動。
此後,由於工具的改進、電動機的出現,龍門刨床一方面朝高速切割、高精度方向發展,另一方面朝大型化方向發展。
磨床
磨削是人類自古以來就知道的一種古老技術,舊石器時代,磨製石器用的就是這種技術。以後,隨著金屬器具的使用,促進了研磨技術的發展。但是,設計出名副其實的磨削機械還是近代的事情,即使在19世紀初期,人們依然是通過鏇轉天然磨石,讓它接觸加工物體進行磨削加工的。
第一台磨床(1864年)1864年,美國製成了世界上第一台磨床,這是在車床的溜板刀架上裝上砂輪,並且使它具有自動傳送的一種裝置。過了12年以後,美國的布朗發明了接近現代磨床的萬能磨床。
人造磨石——砂輪的誕生(1892年)人造磨石的需求也隨之興起。如何研製出比天然磨石更耐磨的磨石呢?1892年,美國人艾奇遜試製成功了用焦炭和砂製成的碳化矽,這是一種現稱為C磨料的人造磨石;兩年以後,以氧化鋁為主要成份的A磨料又試製成功,這樣,磨床便得到了更廣泛的套用。
以後,由於軸承、導軌部分的進一步改進,磨床的精度越來越高,並且向專業化方向發展,出現了內圓磨床、平面磨床、滾磨床、齒輪磨床、萬能磨床等等。
鑽床
古代鑽床——“弓轆轤”鑽孔技術有著久遠的歷史。考古學家現已發現,公元前 4000年,人類就發明了打孔用的裝置。古人在兩根立柱上架個橫樑,再從橫樑上向下懸掛一個能夠鏇轉的錐子,然後用弓弦纏繞帶動錐子鏇轉,這樣就能在木頭石塊上打孔了。不久,人們還設計出了稱為“轆轤”的打孔用具,它也是利用有彈性的弓弦,使得錐子鏇轉。
第一台鑽床(惠特沃斯,1862年)到了1850年前後,德國人馬蒂格諾尼最早製成了用於金屬打孔的麻花鑽;1862年在英國倫敦召開的國際博覽會上,英國人惠特沃斯展出了由動力驅動的鑄鐵櫃架的鑽床,這便成了近代鑽床的雛形。
以後,各種鑽床接連出現,有搖臂鑽床、備有自動進刀機構的鑽床、能一次同時打多個孔的多軸鑽床等。由於工具材料和鑽頭的改進,加上採用了電動機,大型的高性能的鑽床終於製造出來了。
數控工具機
是數字控制工具機的簡稱,是一種裝有程式控制系統的自動化工具機。該控制系統能夠邏輯地處理具有控制編碼或其他符號指令規定的程式,並將其解碼,從而使工具機動作並加工零件的控制單元,數控工具機的操作和監控全部在這個數控單元中完成,它是數控工具機的大腦。
加工精度高,具有穩定的加工質量;
可進行多坐標的聯動,能加工形狀複雜的零件;
加工零件改變時,一般只需要更改數控程式,可節省生產準備時間;
工具機本身的精度高、剛性大,可選擇有利的加工用量,生產率高(一般為普通工具機的3~5倍);
工具機自動化程度高,可以減輕勞動強度;
對操作人員的素質要求較高,對維修人員的技術要求更高。
數控工具機一般由下列幾個部分組成:
主機,是數控工具機的主體,包括工具機身、立柱、主軸、進給機構等機械部件。它是用於完成各種切削加工的機械部件。
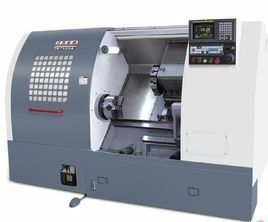
數控裝置,是數控工具機的核心,包括硬體(印刷電路板、CRT顯示器、鍵盒、紙帶閱讀機等)以及相應的軟體,用於輸入數位化的零件程式,並完成輸入信息的存儲、數據的變換、插補運算以及實現各種控制功能。
驅動裝置,是數控工具機執行機構的驅動部件,包括主軸驅動單元、進給單元、主軸電機及進給電機等。它在數控裝置的控制下通過電氣或電液伺服系統實現主軸和進給驅動。當幾個進給聯動時,可以完成定位、直線、平面曲線和空間曲線的加工。
輔助裝置,指數控工具機的一些必要的配套部件,用以保證數控工具機的運行,如冷卻、排屑、潤滑、照明、監測等。它包括液壓和氣動裝置、排屑裝置、交換工作檯、數控轉台和數控分度頭,還包括刀具及監控檢測裝置等。
編程及其他附屬設備,可用來在機外進行零件的程式編制、存儲等。
數控工具機加工流程說明
CAD:Computer Aided Design,即計算機輔助設計。2D或3D的工件或立體圖設計
CAM:Computer Aided Making,即計算機輔助製造。使用CAM軟體生成G-Code
CNC:數控工具機控制器,讀入G-Code開始加工
數控工具機加工程式說明
CNC程式可分為主程式及副程式(子程式),凡是重複加工的部份,可用副程式編寫,以簡化主程式的設計。
字元(數值資料)→字語→單節→加工程式。
只要打開Windows作業系統里的記事本就可編輯CNC碼,寫好的CNC程式則可用模擬軟體來模擬刀具路徑的正確性。
數控工具機基本機能指令說明
所謂機能指令是由位址碼(英文字母)及兩個數字所組成,具有某種意義的動作或功能,可分為七大類,即G機能(準備機能),M機能(輔助機能),T機能(刀具機能),S機能(主軸轉速機能),F機能(進給率機能),N機能(單節編號機能)和H/D機能(刀具補正機能)。
數控工具機 參考點說明
通常在數控工具機程式編寫時,至少須選用一個參考坐標點來計算工作圖上各點之坐標值,這些參考點我們稱之為零點或原點,常用之參考點有機械原點、回歸參考點、工作原點、程式原點。
機械參考點(Machine reference point):機械參考點或稱為機械原點,它是機械上的一個固定的參考點。
回歸參考點 (Reference points):在機器的各軸上都有一回歸參考點,這些回歸參考點的位置,以行程監測裝置極限開關預先精確設定,作為工作檯及主軸的回歸點。
工作參考點 (Work reference points):工作參考點或稱工作原點,它是工作坐標系統之原點,該點是浮動的,由程式設計者依需要而設定,一般被設定於工作檯上(工作上)任一位置。
程式參考點 (Program reference points):程式參考點或稱程式原點,它是工作上所有轉折點坐標值之基準點,此點必須在編寫程式時加以選定,所以程式設計者選定時須選擇一個方便的點,以利程式之寫作。
鋼製伸縮式導軌防護罩為高品質的2-3mm厚鋼板冷壓成形而成,根據要求也可以為不鏽鋼的。特殊的表面磨光會使其另外升值。我們可以為所有的工具機種類提供相應的導軌防護類型(水平、垂直、傾斜、橫向)。
曲軸工具機
曲軸高效專用工具機也有它的加工局限性,只有合理套用合適的加工工具機,才能發揮出曲軸加工工具機的高效專用性,從而提高工序的加工效率。
1、當曲軸軸頸有沉割槽時,數控內銑工具機不能加工;如果曲軸軸頸軸向有沉割槽時,數控高速外銑工具機和數控內銑工具機均不能加工,但數控車-車拉工具機能很方便地加工。
2、當平衡塊側面需要加工時,數控內銑工具機應當為首選工具機,因為內銑刀盤外圓定位,剛性好,尤其適用於加工大型鍛鋼曲軸;此時不適合用數控車-車拉工具機,因為在曲軸的平衡塊側面需要加工的情況下,採用數控車-車拉工具機加工,平衡塊側面是斷續切削,且曲軸轉速又很高,在這種工況下,崩刀現象比較嚴重。
3、當曲軸的軸頸無沉割槽,且平衡塊側面不需加工時,原則上幾種工具機都能加工。當加工轎車曲軸時,主軸頸採用數控車-車拉工具機,連桿頸採用數控高速外銑工具機則應成為最佳高效加工選擇;當加工大型鍛鋼曲軸時,則主軸頸和連桿頸均採用數控內銑工具機比較合理。
曲軸可以分為體形較大的鍛鋼曲軸和輕量化的轎車曲軸,鍛鋼曲軸軸頸一般無沉割槽,且側面需要加工,餘量較大;轎車曲軸一般軸頸有沉割槽,且側面不需要加工。因此可以得出結論:加工鍛鋼曲軸採用數控內銑工具機,加工轎車曲軸主軸頸採用數控車-車拉工具機,連桿頸採用數控高速外銑工具機是比較合理的高效加工選擇。
鍛壓工具機
鍛壓工具機是金屬和機械冷加工用的設備,他只改變金屬的外形狀。鍛壓工具機包括卷板機,剪板機,沖床,壓力機,液壓機,油壓機,折彎機等。
工具機附屬檔案的種類有很多,包括柔性風琴式防護罩(皮老虎)、刀具刀片.鋼板不鏽鋼導軌護罩、伸縮式絲槓護罩、捲簾防護罩、防護裙簾、防塵折布、鋼製拖鏈、工程塑膠拖鏈、工具機工作燈、工具機墊鐵、JR—2型矩形金屬軟管、DGT導管防護套、可調塑膠冷卻管、吸塵管、通風管、防爆管、行程槽板、撞塊、排屑機、偏擺儀、平台\花崗石平板\鑄鐵平板及各種操作件等。
運動傳動
車床的運動傳動包含以下內容:
工具機的運動
根據在切削過程中所起的作用來區分,切削運動分為主運動和進給運動。
主運動:是形成工具機切削速度或消耗主要動力的工作運動。
進給運動:是使工件的多餘材料不斷被去除的工作運動。
切削過程中主運動只有一個,進給運動可以多於一個。主運動和進給運動可由刀具或工件分別完成,也可由刀具單獨完成。工具機的運動除了切削運動外,還有一些實現工具機切削過程的輔助工作而必須進行的輔助運動。
工具機的傳動
工具機的傳動機構指的是傳遞運動和動力的機構,簡稱為工具機的傳動。
工具機的傳動方式按傳動機構的特點分為機械傳動、液壓傳動、電力傳動、氣壓傳動以及以上幾種傳動方式的聯合傳動等。按傳動速度調節變化特點將傳動分為有級傳動和無級傳動。
工具機的傳動系統
傳動系統也叫傳動鏈,他有首末兩個端件。首端件又叫主動件,末端件又叫從動件。每一條傳動系統從首端件到末端件都是按一定傳動規律組成,這就是傳動比,以此來保證工具機的性能。一般的工具機傳動系統按其所擔負運動的性質可分為主運動傳遞系統,進給運動傳遞系統和快速空行程傳動系統三種。對傳動系統圖一般了解即可。
工具機分類
1. 普通工具機:包括普通車床、鑽床、鏜床、銑床、刨插床等。
2. 精密工具機:包括磨床、齒輪加工工具機、螺紋加工工具機和其他各種精密工具機。
3. 高精度工具機:包括坐標鏜床、齒輪磨床、螺紋磨床、高精度滾齒機、高精度刻線機和其他高精度工具機等。
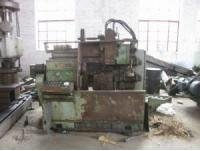
4.數控工具機:數控工具機是數字控制工具機的簡稱,是一種裝有程式控制系統的自動化工具機。該控制系統能夠邏輯地處理具有控制編碼或其他符號指令規定的程式,並將其解碼,從而使工具機動作並加工零件。
5.按工件大小和工具機重量可分為儀表工具機、中小型工具機、大型工具機、重型工具機和超重型工具機。
6.按加工精度可分為普通精度工具機、精密工具機和高精度工具機。
7.按自動化程度可分為手動操作工具機、半自動工具機和自動工具機。
8.按工具機的控制方式,可分為仿形工具機、程式控制工具機、數控工具機、適應控制工具機、加工中心和柔性製造系統。
9.按工具機的適用範圍,又可分為通用、專用工具機。金屬切削工具機可按不同的分類方法劃分為多種類型。
按加工方式或加工對象可分為車床、鑽床、鏜床、磨床、齒輪加工工具機、螺紋加工工具機、花鍵加工工具機、銑床、刨床、插床、拉床、特種加工工具機、鋸床和刻線機等。每類中又按其結構或加工對象分為若干組,每組中又分為若干型。
按工件大小和工具機重量可分為儀表工具機、中小型工具機、大型工具機、重型工具機和超重型工具機。
按加工精度可分為普通精度工具機、精密工具機和高精度工具機。
按自動化程度可分為手動操作工具機、半自動工具機和自動工具機。
按工具機的自動控制方式,可分為仿形工具機、程式控制工具機、數字控制工具機、適應控制工具機、加工中心和柔性製造系統。
按工具機的適用範圍,又可分為通用、專門化和專用工具機。
專用工具機中有一種以標準的通用部件為基礎,配以少量按工件特定形狀或加工工藝設計的專用部件組成的自動或半自動工具機,稱為組合工具機。
對一種或幾種零件的加工,按工序先後安排一系列工具機,並配以自動上下料裝置和工具機與工具機間的工件自動傳遞裝置,這樣組成的一列工具機群稱為切削加工自動生產線。
柔性製造系統是由一組數字控制工具機和其他自動化工藝裝備組成的,用電子計算機控制,可自動地加工有不同工序的工件,能適應多品種生產。
工具機組成
各類工具機通常由下列基本部分組成:支承部件,用於安裝和支承其他部件和工件,承受其重量和切削力,如床身和立柱等;變速機構,用於改變主運動的速度;進給機構,用於改變進給量;主軸箱用以安裝工具機主軸;刀架、刀庫;控制和操縱系統;潤滑系統;冷卻系統。
工具機附屬裝置包括工具機上下料裝置、機械手、工業機器人等工具機附加裝置,以及卡盤、吸盤彈簧夾頭、虎鉗、迴轉工作檯和分度頭等工具機附屬檔案。
切削加工
工具機的切削加工是由刀具與工件之間的相對運動來實現的,其運動可分為表面形成運動和輔助運動兩類。
表面形成運動是使工件獲得所要求的表面形狀和尺寸的運動,它包括主運動、進給運動和切入運動。主運動是從工件毛坯上剝離多餘材料時起主要作用的運動,它可以是工件的鏇轉運動(如車削)、直線運動(如在龍門刨床上刨削),也可以是刀具的鏇轉運動(如銑削和鑽削)或直線運動(如插削和拉削);進給運動是刀具和工件待加工部分相向移動,使切削得以繼續進行的運動,如車削外圓時刀架溜板沿工具機導軌的移動等;切入運動是使刀具切入工件表面一定深度的運動,其作用是在每一切削行程中從工件表面切去一定厚度的材料,如車削外圓時小刀架的橫向切入運動。
輔助運動主要包括刀具或工件的快速趨近和退出、工具機部件位置的調整、工件分度、刀架轉位、送夾料,啟動、變速、換向、停止和自動換刀等運動。
評價工具機技術性能的指標最終可歸結為加工精度和生產效率。加工精度包括被加工工件的尺寸精度、形狀精度、位置精度、表面質量和工具機的精度保持性。生產效率涉及切削加工時間和輔助時間,以及工具機的自動化程度和工作可靠性。這些指標一方面取決於工具機的靜態特性,如靜態幾何精度和剛度;而另一方面與工具機的動態特性,如運動精度、動剛度、熱變形和噪聲等關係更大。
數控刀具
數控刀具是機械製造中用於切削加工的工具,又稱切削工具。廣義的切削工具既包括刀具,還包括磨具;同時“數控刀具”除切削用的刀片外,還包括刀桿和刀柄等附屬檔案!
根據刀具結構可分為:
整體式:刀具為一體,由一個坯料製造而成,不分體;
焊接式式:採用焊接方法連線,分刀頭和刀桿;
機夾式:機夾式又可分為不轉位和可轉位兩種;通常數控刀具採用機夾式!
特殊型式:如複合式刀具,減震式刀具等。
根據製造刀具所用的材料可分為:
高速鋼刀具;
硬質合金刀具;
金剛石刀具;
其他材料刀具,如立方氮化硼刀具,陶瓷刀具等。
從切削工藝上可分為
車削刀具,分外圓、內孔、螺紋、切斷、切槽刀具等多種;
鑽削刀具,包括鑽頭、鉸刀、絲錐等;
鏜削刀具;
銑削刀具等。
刀具的發展在人類進步的歷史上占有重要的地位。中國早在公元前28~前20世紀,就已出現黃銅錐和紫銅的錐、鑽、刀等銅質刀具。戰國後期(公元前三世紀),由於掌握了滲碳技術,製成了銅質刀具。當時的鑽頭和鋸,與現代的扁鑽和鋸已有些相似之處。
然而,刀具的快速發展是在18世紀後期,伴隨蒸汽機等機器的發展而來的。1783年,法國的勒內首先制出銑刀。1792年,英國的莫茲利制出絲錐和板牙。有關麻花鑽的發明最早的文獻記載是在1822年,但直到1864年才作為商品生產。
那時的刀具是用整體高碳工具鋼製造的,許用的切削速度約為5米/分。1868年,英國的穆舍特製成含鎢的合金工具鋼。1898年,美國的泰勒和.懷特發明高速鋼。1923年,德國的施勒特爾發明硬質合金。
在採用合金工具鋼時,刀具的切削速度提高到約8米/分,採用高速鋼時,又提高兩倍以上,到採用硬質合金時,又比用高速鋼提高兩倍以上,切削加工出的工件表面質量和尺寸精度也大大提高。
由於高速鋼和硬質合金的價格比較昂貴,刀具出現焊接和機械夾固式結構。1949~1950年間,美國開始在車刀上採用可轉位刀片,不久即套用在銑刀和其他刀具上。1938年,德國德古薩公司取得關於陶瓷刀具的專利。1972年,美國通用電氣公司生產了聚晶人造金剛石和聚晶立方氮化硼刀片。這些非金屬刀具材料可使刀具以更高的速度切削。
1969年,瑞典山特維克鋼廠取得用化學氣相沉積法,生產碳化鈦塗層硬質合金刀片的專利。1972年,美國的邦沙和拉古蘭發展了物理氣相沉積法,在硬質合金或高速鋼刀具表面塗復碳化鈦或氮化鈦硬質層。表面塗層方法把基體材料的高強度和韌性,與表層的高硬度和耐磨性結合起來,從而使這種複合材料具有更好的切削性能。
刀具按工件加工表面的形式可分為五類。加工各種外表面的刀具,包括車刀、刨刀、銑刀、外表面拉刀和銼刀等;孔加工刀具,包括鑽頭、擴孔鑽、鏜刀、鉸刀和內表面拉刀等;螺紋加工工具,包括絲錐、板牙、自動開合螺紋切頭、螺紋車刀和螺紋銑刀等;齒輪加工刀具,包括滾刀、插齒刀、剃齒刀、錐齒輪加工刀具等;切斷刀具,包括鑲齒圓鋸片、帶鋸、弓鋸、切斷車刀和鋸片銑刀等等。此外,還有組合刀具。
按切削運動方式和相應的刀刃形狀,刀具又可分為三類。通用刀具,如車刀、刨刀、銑刀(不包括成形的車刀、成形刨刀和成形銑刀)、鏜刀、鑽頭、擴孔鑽、鉸刀和鋸等;成形刀具,這類刀具的刀刃具有與被加工工件斷面相同或接近相同的形狀,如成形車刀、成形刨刀、成形銑刀、拉刀、圓錐鉸刀和各種螺紋加工刀具等;展成刀具是用展成法加工齒輪的齒面或類似的工件,如滾刀、插齒刀、剃齒刀、錐齒輪刨刀和錐齒輪銑刀盤等。
各種刀具的結構都由裝夾部分和工作部分組成。整體結構刀具的裝夾部分和工作部分都做在刀體上;鑲齒結構刀具的工作部分(刀齒或刀片)則鑲裝在刀體上。
刀具的裝夾部分有帶孔和帶柄兩類。帶孔刀具依靠內孔套裝在工具機的主軸或心軸上,藉助軸向鍵或端面鍵傳遞扭轉力矩,如圓柱形銑刀、套式面銑刀等。
工具機附屬檔案
工具機配件,指除工具機主體外的所有可方便更換的元件。
工具機配件主要包括刀具夾具、操作件、分度頭、工作檯、卡盤、接頭、排屑裝置、軟管、拖鏈、防護罩等。其中刀具夾具又分切削刀具、工裝夾具、刨刀、數控刀具及配套系統、刀帶、拉刀、切刀、滾刀、齒輪刀具、機用鋸片、數控刀具、夾頭、沖頭、車刀、鉸刀、鏜刀、插齒刀、剃齒刀、機用刀片、刀柄、銑刀、螺紋刀具、鑽頭、刀桿、其他刀具、夾具、絲錐;操作件分手輪、拉手、手柄、把手、門鈕、其它操作件產品;
分度頭分為等分分度頭、半萬能分度頭、萬能分度頭、簡易分度頭、立臥分度頭、數控分度頭、懸臂分度頭;
工作檯手動迴轉工作檯、立臥迴轉工作檯、數控立臥迴轉工作檯、數控移動工作檯、角度工作檯、可調工作檯;
卡盤分二爪自定心卡盤、短圓柱型三爪自定心卡盤、短圓錐型三爪自定心卡盤、電動三爪自定心卡盤、電動三爪卡盤、可調三爪自定心卡盤、四爪管子複合卡盤、四爪單動卡盤、高速通孔動力卡盤、三爪楔式(動力)自定心卡盤、三爪手緊卡盤、錐柄卡盤、三爪自定心卡盤、四爪自定心卡盤、精密三爪自定心卡盤、四爪複合卡盤、六爪自定心卡盤;
接頭分金屬螺口軟管接頭、法蘭式接頭、圓定座、固定圈;
排屑裝置分鏈板式排屑裝置、永磁式排屑裝置、複合式排屑裝置、螺鏇式排屑裝置、磁刮板式排屑裝;
軟管分尼龍軟管、聚乙烯軟管、雙層開口管、橢圓軟管。
工具機配件的合理運用有助於提高工作效率和節約成本,在機加工中已經得到了廣泛的注意和運用。
操作規程
操作者必須經過考試合格,持有本工具機的《設備操作證》方可操作本工具機。
工作前
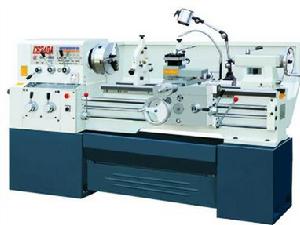
1、仔細閱讀交接班記錄,了解上一班工具機的運轉情況和存在問題;
2、檢查工具機、工作檯、導軌以及各主要滑動面,如有障礙物、工具、鐵屑、雜質等,必須清理、擦拭乾淨、上油;
3、檢查工作檯,導軌及主要滑動面有無新的拉、研、碰傷,如有應通知班組長或設備員一起查看,並作好記錄;
4、檢查安全防護、制動(止動)、限位和換向等裝置應齊全完好;
5、檢查機械、液壓、氣動等操作手柄、伐門、開關等應處於非工作的位置上;
6、檢查各刀架應處於非工作位置;
7、檢查電器配電箱應關閉牢靠,電氣接地良好;
8、檢查潤滑系統儲油部位的油量應符合規定,封閉良好。油標、油窗、油杯、油嘴、油線、油氈、油管和分油器等應齊全完好,安裝正確。按潤滑指示圖表規定作人工加油或機動(手位)泵打油,查看油窗是否來油;
9、停車一個班以上的工具機,應按說明書規定及液體靜壓裝置使用規定(詳見附錄Ⅰ)的開車程式和要求作空動轉試車3~5分鐘。
檢查:
1)操縱手柄、伐門、開關等是否靈活、準確、可靠。
2)安全防護、制動(止動)、聯鎖、夾緊機構等裝置是否起作用。
3)校對機構運動是否有足夠行程,調正並固定限位、定程擋鐵和換向碰塊等。
4)由機動泵或手拉泵潤滑部位是否有油,潤滑是否良好。
5)機械、液壓、靜壓、氣動、靠模、仿形等裝置的動作、工作循環、溫升、聲音等是否正常。壓力(液壓、氣壓)是否符合規定。確認一切正常後,方可開始工作。
凡連班交接班的設備,交接班人應一起按上述(9條)規定進行檢查,待交接班清楚後,交班人方可離去。凡隔班接班的設備,如發現上一班有嚴重違犯操作規程現象,必須通知班組長或設備員一起查看,並作好記錄,否則按本班違犯操作規程處理。
在設備檢修或調整之後,也必須按上述(9條)規定詳細檢查設備,認為一切無誤後方可開始工作。
工作中
1、堅守崗位,精心操作,不做與工作無關的事。因事離開工具機時要停車,關閉電源、氣源;
2、按工藝規定進行加工。不準任意加大進刀量、磨削量和切(磨)削速度。不準超規範、超負荷、超重量使用工具機。不準精機粗用和大機小用;
3、刀具、工件應裝夾正確、緊固牢靠。裝卸時不得碰傷工具機。找正刀具、工件不準重錘敲打。不準用加長搬手柄增加力矩的方法緊固刀具、 工件;
4、不準在工具機主軸錐孔、尾座套筒錐孔及其他工具安裝孔內,安裝與其錐度或孔徑不符、表面有刻痕和不清潔的頂針、刀具、刀套等;
5、傳動及進給機構的機械變速、刀具與工件的裝夾、調正以及工件的工序間的人工測量等均應在切削、磨削終止,刀具、磨具退離工件後停車進行;
6、應保持刀具、磨具的鋒利,如變鈍或崩裂應及時磨鋒或更換;
7、切削、磨削中,刀具、磨具未離開工件,不準停車;
8、不準擅自拆卸工具機上的安全防護裝置,缺少安全防護裝置的工具機不準工作;
9、液壓系統除節流伐外其他液壓伐不準私自調整;
10、工具機上特別是導軌面和工作檯面,不準直接放置工具,工件及其他雜物;
11、經常清除工具機上的鐵屑、油污,保持導軌面、滑動面、轉動面、定位基準面和工作檯面清潔;
12、密切注意工具機運轉情況,潤滑情況,如發現動作失靈、震動、發熱、爬行、噪音、異味、碰傷等異常現象,應立即停車檢查,排除故障後,方可繼續工作;
13、工具機發生事故時應立即按總停按鈕,保持事故現場,報告有關部門分析處理;
14、不準在工具機上焊接和補焊工件。
工作後
1、將機械、液壓、氣動等操作手柄、伐門、開關等板到非工作位置上;
2、停止工具機運轉,切斷電源、氣源;
3、清除鐵屑,清掃工作現場,認真擦淨工具機。導軌面、轉動及滑動面、定位基準面、工作檯面等處加油保養;
4、認真將班中發現的工具機問題,填到交接班記錄本上,做好交班工作。
故障診斷方法

數控工具機電氣故障診斷有故障檢測、故障判斷及隔離和故障定位三個階段。第一階段的故障檢測就是對數控工具機進行測試,判斷是否存在故障;第二階段是判定故障性質,並分離出故障的部件或模組;第三階段是將故障定位到可以更換的模組或印製線路板,以縮短修理時間。為了及時發現系統出現的故障,快速確定故障所在部位並能及時排除,要求故障診斷應儘可能少且簡便,故障診斷所需的時間應儘可能短。為此,可以採用以下的診斷方法:
直觀法
利用感覺器官,注意發生故障時的各種現象,如故障時有無火花、亮光產生,有無異常響聲、何處異常發熱及有無焦煳味等。仔細觀察可能發生故障的每塊印製線路板的表面狀況,有無燒毀和損傷痕跡,以進一步縮小檢查範圍,這是一種最基本、最常用的方法。
CNC系統的自診斷功能
依靠CNC 系統快速處理數據的能力,對出錯部位進行多路、快速的信號採集和處理,然後由診斷程式進行邏輯分析判斷,以確定系統是否存在故障,及時對故障進行定位。現代CNC系統自診斷功能可以分為以下兩類:
(1) 開機自診斷開機自診斷是指從每次通電開始至進入正常的運行準備狀態為止,系統內部的診斷程式自動執行對CPU、存儲器、匯流排、I/O 單元等模組、印製線路板、CRT 單元、光電閱讀機及軟碟驅動器等設備運行前的功能測試,確認系統的主要硬體是否可以正常工作。
(2) 故障信息提示當工具機運行中發生故障時,在CRT 顯示器上會顯示編號和內容。根據提示,查閱有關維修手冊,確認引起故障的原因及排除方法。一般來說,數控工具機診斷功能提示的故障信息越豐富,越能給故障診斷帶來方便。但要注意的是,有些故障根據故障內容提示和查閱手冊可直接確認故障原因;而有些故障的真正原因與故障內容提示不相符,或一個故障顯示有多個故障原因,這就要求維修人員必須找出它們之間的內在聯繫,間接地確認故障原因。
數據和狀態檢查
CNC系統的自診斷不但能在CRT 顯示器上顯示故障報警信息,而且能以多頁的“診斷地址”和“診斷數據”的形式提供工具機參數和狀態信息,常見的數據和狀態檢查有參數檢查和接口檢查兩種。
(1) 參數檢查數控工具機的工具機數據是經過一系列試驗和調整而獲得的重要參數,是工具機正常運行的保證。這些數據包括增益、加速度、輪廓監控允差、反向間隙補償值和絲槓螺距補償值等。當受到外部干擾時,會使數據丟失或發生混亂,工具機不能正常工作。
(2) 接口檢查CNC系統與工具機之間的輸入/輸出接口信號包括CNC 系統與PLC、PLC 與工具機之間接口輸入/輸出信號。數控系統的輸入/輸出接口診斷能將所有開關量信號的狀態顯示在CRT 顯示器上,用“1”或“0”表示信號的有無,利用狀態顯示可以檢查CNC系統是否已將信號輸出到工具機側,工具機側的開關量等信號是否已輸入到CNC 系統,從而可將故障定位在工具機側或是在CNC 系統。
報警指示燈顯示故障
現代數控工具機的CNC 系統內部,除了上述的自診斷功能和狀態顯示等“軟體”報警外,還有許多“硬體”報警指示燈,它們分布在電源、伺服驅動和輸入/輸出等裝置上,根據這些報警燈的指示可判斷故障的原因。
備板置換法
利用備用的電路板來替換有故障疑點的模板,是一種快速而簡便的判斷故障原因的方法,常用於CNC 系統的功能模組,如CRT 模組、存儲器模組等。需要注意的是,備板置換前,應檢查有關電路,以免由於短路而造成好板損壞,同時,還應檢查試驗板上的選擇開關和跨接線是否與原模板一致,有些模板還要注意模板上電位器的調整。置換存儲器板後,應根據系統的要求,對存儲器進行初始化操作,否則系統仍不能正常工作。
交換法
在數控工具機中,常有功能相同的模組或單元,將相同模組或單元互相交換,觀察故障轉移的情況,就能快速確定故障的部位。這種方法常用於伺服進給驅動裝置的故障檢查,也可用於CNC 系統內相同模組的互換。
敲擊法
CNC 系統由各種電路板組成,每塊電路板上會有很多焊點,任何虛焊或接觸不良都可能出現故障。用絕緣物輕輕敲打有故障疑點的電路板、接外掛程式或電器元件時,若故障出現,則故障很可能就在敲擊的部位。
測量比較法
為檢測方便,模組或單元上設有檢測端子,利用萬用表、示波器等儀器儀表,通過這些端子檢測到的電平或波形,將正常值與故障時的值相比較,可以分析出故障的原因及故障的所在位置。由於數控工具機具有綜合性和複雜性的特點,引起故障的因素是多方面的。上述故障診斷方法有時要幾種同時套用,對故障進行綜合分析,快速診斷出故障的部位,從而排除故障。同時,有些故障現象是電氣方面的,但引起的原因是機械方面的;反之,也可能故障現象是機械方面的,但引起的原因是電氣方面的;或者二者兼而有之。因此,對它的故障診斷往往不能單純地歸因於電氣方面或機械方面,而必須加以綜合,全方位地進行考慮。