發展歷史
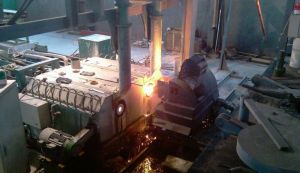
基本原理
在密閉的保持爐的熔湯表面上施加比大氣壓大0.01~0.05Mpa的空氣壓力或惰性氣體壓力,熔湯通過浸放在熔湯里的給湯管(升液管)上升,被壓進與爐子連線著的上方的模具內。熔湯是從型腔的下部慢慢開始充填,保持一段時間的壓力後凝固。凝固是從產品上部開始向澆口方向轉移,澆口部分凝固的時刻就是加壓結束的時間。於是就憑藉澆口的方向性凝固和從澆口開始的冒口壓力效果得到了完美的鑄件。最後當鑄件冷卻至固相溫度以下便可從模具中取出產品。
工藝過程
緩慢地向坩堝爐內通入乾燥的壓縮空氣,金屬液受氣體壓力的作用,由下而上沿著升液管和澆注系統充滿型腔,如圖1-38b所示。開啟鑄型,取出鑄件。
技術特點
特點
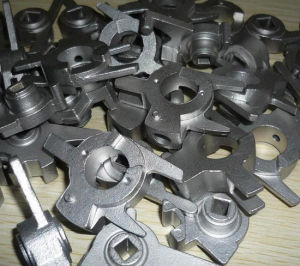
(2)採用底注式充型,金屬液充型平穩,無飛濺現象,可避免捲入氣體及對型壁和型芯的沖刷,提高了鑄件的合格率。
(3)鑄件在壓力下結晶,鑄件組織緻密、輪廓清晰、表面光潔,力學性能較高,對於大薄壁件的鑄造尤為有利。
(4)省去補縮冒口,金屬利用率提高到90~98%。
(5)勞動強度低,勞動條件好,設備簡易,易實現機械化和自動化。
優點和缺點(相對重力金型鑄造而言)
優缺點
優點:
1)鑄造利用率非常高。(85~95%)
由於沒有冒口和澆道,澆口較小,因此可以大幅度降低材料費和加工工時。
2)獲得完美的鑄件。
容易形成方向性凝固,內部缺陷少。
3)氣體、雜物的捲入少。
可以改變加壓速度,熔湯靠層流進行充填。
4)可以使用砂制型芯。
5)容易實現自動化,可以多台作業、多工序作業。
6)不受操作者熟練程度的影響。
7)材料的使用範圍廣。
各鑄造方法材料利用率
工藝方法 | 重力金型鑄造 | 高壓鑄造 | 低壓鑄造 |
材料利用率(%) | 45~55 | 50~60 | 85~95 |
缺點:
1)澆口方案的自由度小,因而限制了產品。
(澆口位置、數量的限制,產品內部壁厚變化等)
2)鑄造周期長,生產性差。
為了維持方向性凝固和熔湯流動性,模溫較高,凝固速度慢。
3)靠近澆口的組織較粗,下型面的機械性能不高。
4)為了保證澆口形狀和位置,需要全面的嚴密的管理(溫度、壓力等)
構成要素
低壓鑄造機由以下四種要素構成:
1)模具
2)保持爐(內藏給湯管)
3)模具開關機構液壓接頭及控制裝置
4)爐內壓力控制裝置
模具
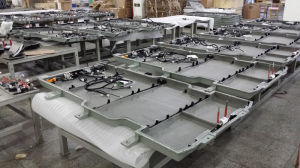
低壓鑄造品的設計基本要求是將壁厚整體平均化,或是將壁厚的分布考
慮容易實現方向性凝固的地方。也就是說對於澆口而言,斷面從小到大逐漸變化是產品設計的必要條件,因此如果產品的性能上無法進行這種設計時最好避開使用低壓鑄造法。在氣缸頭、氣缸體、輪轂等產品中普及使用這種鑄造法的第一理由就是形狀上容易達到方向性凝固。
鑄造方案還算比較單純,充分考慮鑄件整體的方向性凝固和澆口周圍的冒口效果的澆口位置、大小、數量的設定也是非常必要的。澆口的位置應該是鑄件整體的最大壁厚部位,並且要設在從熔湯前方和上方可能達到方向性凝固的部位。因產品形狀、大小等原因澆口數量有所差異,但通常是1-4個。在遠離澆口的位置如果壁較厚冒口無法到達時,有時也加上無頂冒口或過渡橋
。但是水冷氣缸頭的形狀變得複雜,要想達到理想的壁厚分配是非常困難的,方案上對這些問題進行為維持方向性凝固的嚴格的溫度控制和條件管理等,根據情況還可以在成為熱點的部位進行空氣、水等的冷卻或埋入冷鐵。
澆口的截面積對於防止熔湯亂流以便更好地充填模具空間而言是非常重要的因素。最小截面積a的公式如下:
a=澆口的最小截面積
W=鑄件的重量(kg)
T=從澆口處開始的澆鑄時間(S)[充填時間]
m=熔湯的比重(2.4~2.5)
Υ=電阻係數(0.3-0.4)
g=重力加速度(9.8m/s)
H=壓力頭(m)(熔湯麵到產品上端的高度)
在圖5-3中a部截面做成圓形是較理想的,但事實上由於產品形狀的限制經常是不得不做成不規則的形狀。在這種情況下為了防止該部分的過冷,最小截面積最好應是澆口附近產品壁厚的2倍以上。澆口的高度h比較低時可以得到較大的因澆口處熱量提供和加壓而引起的補縮效果,而且也容易實現方向性凝固,但這是防止氧化物的濾渣網的固定部位,由於因鑄造條件的變動引起澆口長度的變化,因而一般情況下考慮30-40mm較多。
(2)模具結構上特徵
低壓鑄造模具的澆口在下面,下型部分通過給湯管與保持爐連結,所以不能使用擠壓結構,而採用把鑄件放在上型或橫型里的方法,下型的溫度很高,因此拔模斜度需要比其它模具做得大一些。
模具內部的空氣、砂芯產生的氣體需要充分考慮分型方法和排氣道等,應該在儘量減少隨著熔湯充填而產生的背壓的情況下排出去。如果背壓高到影響加壓速度時,會產生熔湯流動不良、表面縮孔等,因此希望控制在0.002Mpa以下。
關於凸台、加強筋、葉片等形狀的部位,可以考慮嵌入式排氣孔插入模具。在分型面和平面部設計排氣槽,再加上排氣孔、拉深加工等手段儘量做到排氣良好的設計。另外砂芯產生的氣體量較大、時間也較長,可以在模具結構上設計確定的排氣路線,追加吸引機構。
保持爐
(1)鐵坩鍋爐
這是實用化早期的爐型,操作簡單,因此仍大量使用,但由於鐵慢慢熔解會增加熔湯鐵的含量,所以必須定期(1個星期)進行塗層處理。另外,它不適合用於高純度合金的鑄造。
(2)石墨坩鍋爐
由於不能對石墨坩鍋直接施加壓力,因此這是一種對爐子整體加壓的構造。由於腐蝕少,所以可以連續用90-120天左右。但缺點是用鈉進行改良處理時,坩鍋的壽命會變短。
(3)耐火材料爐
這種爐的使用隨著鑄件的大型化、1模多個的推進而逐步增大了。因為氣密室整體構成了爐體,所以容積大(700-1000kg),熔湯的補充次數少。連續使用時間長,鑄造條件穩定,熱源有加熱熔湯麵的輻射式加熱器和保護管浸入熔湯直接加熱的浸泡式加熱器兩種。
浸泡式加熱器耐火材料爐由於是用浸泡式加熱器直接加熱熔湯,與輻射式耐火材料爐相比,熱效率高出40%以上,電力消耗少,熔湯溫度變化非常小,控制適應性高。因為空氣溫度較低,所有氧化物的產生也較少。因為加熱器管的壽命、維護保養的不方便及成本高等問題影響了使用的普及程度,但從節省能源的觀點來看今後會很快地普及使用的。但是由於採用耐火材料爐與採用鐵坩鍋相比,從熔湯表面和坩鍋傳來的熱量變得非常少,模具溫度分布會發生變化,上下模具之間的溫差坡度也變小,因此有必要開發適合這種設備的鑄造方案。
給湯管
這是將熔湯從保持爐引向模具的管子,截面積是Æ80-Æ120mm左右的圓或橢園形。以前是以鑄鐵表面加上塗料的為主,但因燒損會增加熔湯鐵的含量,
給湯管自身的壽命變短,所以陶瓷製的給湯管逐漸成為主流。但是成本高、抗熱衝擊性能差、異形截面形狀成形難等是需要探討的課題。
氣缸頭中
工序
(1)上塗料,準備模具、安裝
(2)熔解、除渣、除氣、保持爐給湯
(3)鑄造作業
(a)裝澆口濾渣網
(b)裝砂芯
(c)吹空氣
(d)合模
(e)加壓
(f)凝固
(g)開模
(h)取出產品
批量生產中的氣缸頭的工序概要,分為上塗料、準備模具等前期準備工序、熔解、熔湯處理、給鑄造機供湯的給湯工序以及鑄造作業工序等,這種工序都非常重要,不能馬虎,要維持品質關鍵是如何做到在穩定的條件下堅持管理鑄造作業。
(1)模具的保養、上塗料
模具的保養、上塗料是指每500-700模次進行包括模具保養、保持爐和給湯管內的清掃作業,將模具的模框、嵌塊、拔模銷、排氣塊等分解後,用空氣
除去鋁渣和砂芯的燃燒剩餘物等。排氣塊的堵塞對熔湯流動性、氣孔等品質有很大影響,所以應該仔細地清除掉,而且還有必要檢查排氣孔,排氣型芯等的通氣程度。
下一個工序上塗料是以確保排氣性,減低脫模阻力,保護模具表面,確保保溫隔熱性,確保熔湯流動性等為目的。在保養結束後,將模具加熱至473K(200C)左右,用鋼絲輪刷除去表面的氧化皮後再上塗料,操作是用噴槍來進行的,但根據噴吹壓力,距離、速度、濃度、模具溫度等,其強度和粗糙度有很大區別。
在塗複雜的模具時,需要熟練地進行操作,但為了保持穩定的上塗料的效果應儘快使操作標準化,塗層厚度粗糙度等因部位不同而存差異。一般而言,產品面是0.1-0.2mm,光潔度要求高的加工基準面,燃燒室面等套用粒子細小的塗料塗0.05mm的厚度,塗料一般利用市場上的,基本構成是骨材(碳酸鈣、陶土、氧化鋁、雲母、石墨等)、粘接劑(矽酸鈉)和水等。
關於模具塗料的選擇並沒有定量的評價尺度,一般在實際產品中使用後再來決定。
(2)熔解、熔湯處理
作為合金最普通的是AC4B、AC2B。在提出延伸率、耐腐蝕性的要求時,可以使用AC4C等,另外作為高品質化的對策同時也使用加鈉、鍶的改良處理和加鈦的微細化處理,熔湯處理除了以往的加精煉劑的脫氧處理以外,為了得到穩定的品質,使用鏇轉式除氣裝置進行除氣處理的做法也日益增多。
(3)鑄造作業
·裝澆口濾渣網
此工序的目的為了防止從給湯管進來的氧化物、砂子等雜物以及加強熔湯層流化。把做成澆口形狀的鍍鋅網(Æ0.4-0.6mm,12-14個網孔)用專用夾具固定起來。這樣做人工作業比較多,但也可以試一試進行自動化設計或給湯管內吹惰性氣體等方法。
·裝砂芯、吹氣
水道中子、氣道中子、凸輪軸室中子等,材質大多是中子砂。因形狀的複雜化、與其它部件的共用化等引起中子的增加。一般是人工作業,但由於是模具內的高溫作業,所以越來越多地採用由機器人自動安裝。包括活砂鑄型在內自動安裝進模具的方法也開始使用。脫模時因要除去裝中子時落下的砂子,所以要吹空氣。
·合模、加壓、凝固、開模、取出產品
這些工序都是在自動化、標準化的循環周期下進行運轉的。加壓力、加壓速度、加壓時間、凝固時間等各種條件要根據溫度進行調整。
鑄造條件
(1)溫度
熔湯溫度因合金種類、產品形狀而稍有不同,但一般在680~730°C的範圍內。熔湯溫度對內部缺陷和外觀品質等有很大影響,所以實際操作時管理範圍是14°C左右。模具溫度在低壓鑄造時更顯得重要。
從方向性凝固的觀點來看模溫分布是從澆口往上型方向變低,一般而言澆口480~520°C,下型400~450°C,橫型350~400°C,上型250~350°C,但是為了改善內部品質(強化方向性凝固)、縮短鑄造周期,可以進行上型和橫型的冷卻(水冷、空冷,一般冷卻模具整體的線式冷卻比較多)。
在多個澆口的情況下,澆口間距離變近、澆口間溫度變高,使澆口和成形部位的凝固容易發生反轉。如果是由於產品形狀的限制無法修改模具方案的話,採用在澆口間加上點式冷卻,加大澆口的溫差坡度等方法也是比較有效的。模具溫度是由鑄造周期、熔湯溫度、氣氛溫度等決定的,所以在試製作階段要抓住這些條件和內部外觀品質的關係。
改善負面因素,在可能的範圍內大幅度地改變鑄造條件進行品質變動的試驗,然後訂出管理範圍。這些能做到的話就可以確保穩定的品質。另外條件和品質的關係在短時間內還很難完全掌握,所以同時進行凝固解析也是有效的手段。
(2)加壓時間
這是指充填開始到澆口部凝固為止的加壓時間。因產品數量、產品形狀、模具溫度、熔湯溫度、澆口直徑、澆口數量等原因加壓時間會有所不同,但一般氣缸頭是2~8分鐘,根據重量相應延長。溫度條件是影響最大的,在穩定條件下是固定的時間,澆口長度(相當於冒口高度)也較穩定。
但是在鑄造開始時,短時間停頓後模具溫度降低,波動變大,並隨著鑄造數量的增加和溫度條件的波動,澆口部分和給料管內的氧化物堆積起來,澆口截面積減小。在這些情況下,從熔湯、模具傳來的熱量發生變動,凝固時間變得不穩定。於是成形部的凝固時間發生改變,從產品到澆口的方向性凝固被破壞,產品內部容易出現縮孔等內部缺陷。因此穩定溫度條件、保持澆口和給料管等給湯系統的正常狀態是非常重要的。
以前操作者是觀察澆口的狀態後再調整時間的,後來引進了測量鑄造時的溫度後實時自動調整到最佳條件的控制器。在所有的工序中這是最花時間的部分,因此為了提高生產性要積極地考慮模具冷卻、1模2件、2段加壓等縮短時間的方法。
(3)凝固時間
這是從加壓完畢到產品脫模的時間,是脫模時冷卻到鑄件不出現變形、拉傷等的時間。一般而言是加壓時間的1/3左右,但和加壓時間一樣也隨溫度發生變化。從生產性考慮凝固時間短點好。可以加快冷卻速度,讓脫模阻力小的橫型先行,積極地對開模後的產品和模具進行冷卻。
(4)加壓條件
低壓鑄造法是用氣體對熔湯麵加壓使熔湯上升進行充填的鑄造法,因此加壓條件影響到熔湯流動性和冒口效果,是品質管理的重要項目。充填時必要的壓力如下面公式計算:
P(Mpa)=Υ×(1+S/A)×△H×10(2)
Υ=熔湯比重(2.4~2.5)
S=給湯管截面積(m)
A=加壓實際(有效)面積(m)
△H=熔湯麵變動量(m)(給湯管內上升量+加壓面下降量)
根據鑄造機的結構和產品會有所不同,公式(2)中下劃線的部分在批量生產的產品中一般是0.025左右,可以根據公式(2)來決定加壓力。加壓力是由到產品上端的熔湯頂升力和冒口壓力組成,其中前者是由鑄造機和模具的構造決定的,冒口壓力一般在0.005~0.01Mpa左右。為了冒口效果冒口壓力高一點好,但如果超過0.01Mpa,模具排氣道會閉塞,塗料脫落,熔湯容易壓進砂制型芯,所以冒口壓力不會太高。
在氣缸頭中使用了很多砂芯,因此將中子產生的燃氣高效率地排出模具是很有必要的。但氣缸頭的中子形狀變得很複雜,數量也多,所以在模具上無法充分設計排氣道。在這種情況下採用將冒口壓力提高至上限來防止氣體捲入產品內部的手段是比較有效的。
如果加壓速度太慢,熔湯的充填效果會變差,引起熔湯流動性不良;如果太快,又會引起亂流,出現捲入氣體、異物等缺陷。由於根據流路形狀不同流速會有差異,所以模具內各部分的速度有所變化。給湯管內要控制熔湯溫度的下降,速度便快;模具內部要控制亂流,速度便慢,冒口壓力高。一般而言,薄壁鑄件需要快速充填,厚壁鑄件則相反。
表5.2、圖5.8表示了雙缸1模2件氣缸頭中的加壓力和加壓速度的設定。熔湯補充後,隨著鑄造的進行熔湯麵下降,因此必須增加與液面下降量相對應的加壓力。穩定初期液面位置,然後從液面變化量來決定壓力補充值。特別是對熔湯麵積變化大的坩堝型保持爐而言更需要進行詳細的條件設定。已普及了能全部設定這些加壓條件的控制器,所以因加壓條件而引起的故障已得到很大改善。
加壓條件例(氣缸頭1模2件)
部位 | 壓力( MPa ) | 加壓度(Mpa/s)10 |
熔湯麵—澆口距離h | 1~2 | |
澆口部P1 | h(mm)*0.0025 | |
成形部、成形部高度h2 | 0.3~0.7 | |
產品上端P2 | P1+h2*0.0025 | |
冒口 | 0.005~0.01 | 1~2 |
最後壓力P3 | P1+P2+0.005~0.01 |
給湯管和爐床間的距離如果太短的話,在加壓時熔湯的流動會出現亂流,因此一般而言要確保不影響熔湯使用量的200mm左右。最後為了防止從熔湯表面吸收氫氣,對作為加壓氣體使用的空氣要進行除濕處理。
缺陷
與重力金型鑄造法、砂型鑄造法比較類似,表5.3中顯示了低壓鑄造中具有代表性的缺陷和原因及其對策。卻顯得原因並不僅限於一個,而常常是多個因素綜合影響的。因此在考慮對策時需要從模具方案、鑄造條件開始進行充分的調查,用定量的數據明確找出原因。
特別是在批量生產中鑄造條件的微妙變化都會產生影響,因此也需要注意除了可以定量化的溫度條件外,還必須仔細調查模具排氣、上塗料、熔湯品質的變化等。下面列舉兩個氣缸頭中具有代表性的改善不良事例。
低壓鑄件的主要缺陷和對策
缺 陷 | 原 因 | 對 策 |
縮 | 方向性 | 縮短加壓凝固時間,緩和壁厚變化 |
孔 | 鐵含量增加 | 防止從設備、工具等處混入鐵 |
熔湯 | 加壓速度慢 | 加快加壓速度 |
流動 | 熔湯溫度、模溫低 | 縮短加壓、凝固時間,提高熔湯溫度 |
不良 | 排氣道堵塞 | 補塗料、清掃排氣道 |
排氣道堵塞 | 補塗料、清掃排氣道 | |
噴火 | 砂芯吸濕 | 縮短造型到鑄造的時間 |
泄壓 | 換密封墊、修理模具變形 | |
上塗料不夠 | 補塗料 | |
熗火 | 加壓速度快 | 變更加壓條件 |
排氣道堵塞 | 補塗料、清掃排氣道 | |
排氣道堵塞 | 補塗料、清掃排氣道 | |
冷 | 熔湯溫度、模溫低 | 縮短加壓、凝固時間,提高熔湯溫度 |
隔 | 捲入了氧化物 | 加高金屬網 |
砂芯吸濕 | 縮短造型到鑄造的時間 | |
加壓時間短 | 延長加壓時間 | |
澆口不夠 | 熔湯溫度、模溫高 | 降低熔湯溫度 |
金屬網安裝不良 | 擴大金屬網固定餘量 | |
冷卻速度慢 | 冷卻模具 | |
氣孔 | 熔湯氣體量多 | 脫氣處理 |
方向性凝固被破壞 | 縮短加壓凝固時間,緩和壁厚變化 | |
落渣 | 落下了中子砂 | 追加排砂道,修正中子干涉部位 |
拉傷 | 脫模溫度高 | 增加凝固時間和拔模斜度 |
例1:進氣道壁壓力泄漏對策
壓力泄漏是從澆口上的進氣道壁厚處上端的縮孔引起的。如果達到了方向性凝固,那么凝固是從產品上端外圍向澆口處開始的,不會產生縮孔。但是由於某些鑄造條件的變化,四周的熱傳導變差,在圍著砂芯的該部位處凝固的方向出現反轉,出現了縮孔。
關於鑄造條件和出現缺陷的關係,經過調查,明確了如果澆口部溫度和熔湯溫度低過一定範圍的話就容易出現缺陷的事實。作為對策和解決辦法,要保持良品溫度範圍,穩定鑄造條件。為了擴大良品範圍要在鑄造方案和材料兩方面來考慮對策。
縮孔對策內容
目的 | 對策內容 |
鑄造條件的穩定 | 鑄造作業的標準化 |
根據溫度進行加壓、凝固條件的自動設定 | |
根據澆口、給湯管面積的擴大增加熱量 | |
強化方向性凝固 | 根據上型冷卻增加溫差坡度 |
緩和壁厚急變(加圓角、增加對下型的壁厚) | |
改善材料 | 緩和壁厚急變(加圓角、增加對下型的壁厚) |
例2:下台面疏鬆的改善
柴油機氣缸頭與汽油機的相比,下台面的機械性熱負荷高,因此必然要求是疏鬆氣孔少的緻密組織和高機械性能。小型轎車的氣缸頭從鑄鐵向鋁合金髮展,所以對高排氣量的發動機也開始了能否適用的試驗。
在我國鋁合金氣缸頭主要採用低壓鑄造法,把澆口開在下型面,為了保持模具溫度凝固速度當然變慢,因此即使對組織進行熱處理,機械性質也不會有太大的提高。到目前為止為了解決這些問題,採用了諸如TIG焊接的局部強化、重力鑄造中的下台面冷卻等方法。在低壓鑄造中雖是比較難的問題,但可以根據鑄造方案的改變(階梯式澆口)和鑄造條件的控制來改善組織和強度,實現批量生產。
圖5.10顯示了改善解決前後的鑄造方案,以前的方案是基本的氣缸頭的鑄造方案,但為了促進方向性凝固,對上型和進氣橫型進行了冷卻。對此為了減少氣孔量,在改善方案中加了對下型面的急冷,同時也保持了前方案的方向性凝固。
特別是對下型進行充分的冷卻是非常必要的,所以在改善方案中確保了冷卻水的流量、壓力和進行了嚴格的溫度控制。澆口周圍做成砂型,確保了充分的澆口截面和熱量,另外用澆口部橫型的加熱器進行保溫控制,冷卻上型和反澆口側的橫型從而達到對澆口的方向性凝固。
但是由於大量使用冷卻,也因模具溫度低、模具間溫差大出現了一些問題(如型芯燒成氣體難以排出、熔湯流動性差、模具塗料壽命短、型芯位置精度偏差大等)。所以採用1模1件在生產。
表5.5中顯示了兩種方案鑄造條件的不同之處,是組織、機械性質的對比。其中1是指氣孔量巨觀腐蝕了特定部位,根據對擴大後的氣孔量占有率進行畫像解析而得出的定量化數據。所謂DAS是2次枝晶冒口間隔的省略,表示顯微組織的大小。DAS越小凝固速度越快。階梯式澆口方案中所有的項目都得到了提高。從表中可以看出,低壓鑄造法的薄弱處即下型面的組織和強度都得到了很大地改善,但是品質和管理的方便程度還不如重力模具鑄造法。
階梯式澆口方案的鑄造條件
方案 | 熔湯溫度 | 模具溫度 | 加壓時間 | 個數 | ||
(C) | 下型 | 上型 | 模型(EX) | (Min) | ||
以前方案 | 695 | 540 | 410 | 445 | 6 | 2 |
階梯式澆口 | 705 | 300 | 345 | 465 | 3.8 | 1 |
氣缸頭的下型面品質
方案 | 材質 | 氣孔量 | DAS值(mm) | 拉伸強度(N/mm) | 延伸率(%) |
以前方案 | AC2B | 1 | 55 | 260 | 1 |
階梯式澆口 | AC2B | 0.55 | 35 | 280 | 2 |
重力金型法 | AC4C | 0.4 | 25 | 300 | 5 |
發展方向
低壓鑄造法從被大量使用以來已經30多年了,已確立了鋁合金鑄件的重要工作法之一的地位。特別是在氣缸頭中的作用巨大,今後低壓鑄造仍會是主流方法。從空冷小型發動機的氣缸頭開始,到水冷化、多氣筒化、功能的擴大、DOHC化和材料重量的增加,並且形狀越來越複雜,壁厚變化也加大,鑄造的難度也逐年增加,同時為了降低成本進行生產性改善,考慮了1模2件、交換模具時工序改進、動模速度提高和與後處理工序的結合等,冷卻控制和加壓控制等技術也逐年提高,已出現了包括砂芯的搬運和組裝在內的完全自動化線,這同時也從高溫作業解放出來,改善了作業環境。
根據以上內容,可以考慮以下氣缸頭鑄造技術的課題:
1)提高材料強度(直噴式汽油機、柴油機氣缸頭的鋁合金化推進)
2)生產性的提高(提高控制技術、後處理線的同步化、全自動化生產線的推
進)
3)其他品種少量生產對策(包括模具準備工序的縮減、中子造型和後處理的
緊湊的生產線設計)
4)縮短開發時間
5)技能的延續(上塗料、鑄造條件的調整等)
關於1)項,如何對下型進行冷卻是重點,但以往的技術在低壓鑄造中很
難套用,所以認為更適合採用重力鑄造。因此例2是最大限度地發揮了低壓鑄
造的優點克服了問題點的實際例子。在歐美國家氣缸頭的主要鑄造法仍是重力鑄造法,所以為了擴大今後的市場必須解決這個問題。
關於2)和3)項,這是隨著FA技術的進步必然要發展的問題。考慮到鑄件的高強度化和高生產性化的要求,條件控制會變得比更複雜,因此緊湊的自由度高的生產線結構可以保持綜合的高水準。
關於4)項,重點在於需要在設計初期階段和用戶共同開發以及積極運用CAE技術。
最後的第5)項是最緊迫的項目,越推進自動化和無人化,這個問題越顯得重要。由於很難定量數據化,而且與經驗有關的項目較多,所以地道的技能教育和繼承是很重要的。同時為了達到定量化控制而進行的基礎研究和開發也同樣重要。
關於低壓鑄造技術以氣缸頭為中心進行了上述解釋說明,作為輕合金鑄件的主要工作方法之一,還只能以傳統產品為主(氣缸頭、輪轂、氣缸架等),這是因為為了滿足品質上的要求和得到方向性凝固而受到了產品形狀的限制。
今後要發揮低壓鑄造法的材料消耗少、內部品質高等優勢,以便能適合更多的產品。但是必須解決受產品形狀制約、生產性低等問題。為此第一要通過活用積極的CAE技術(凝固流動解析、應力解析),推進與用戶的平行工程技術,以便得到最佳澆口方案和產品形狀。然後使用以控制技術和機器人技術為代表的自動化技術,推進模具溫度控制、鑄造壓力控制、工序自動化和準備工序的省力化等。