基本內容
高速鋼刀具簡介
高速鋼刀具是一種比普通刀具要堅韌,更容易切割的刀具,是一種新產品。在機械製造中用於切削加工,絕大多數的刀具是機用的,也有手用的。由於機械製造中使用的刀具基本上都用於切削金屬材料,所以,越是堅韌的刀具越能被廣泛套用,高速鋼刀具完全符合這一特點。
高速鋼又名風鋼或鋒鋼,意思是淬火時即使在空氣中冷卻也能硬化,並且很鋒利。它是一種成分複雜的合金鋼,含有鎢、鉬、鉻、釩、鈷等碳化物形成元素。合金元素總量達10~25%左右。它在高速切削產生高熱情況下(約500℃)仍能保持高的硬度,HRC能在60以上。這就是高速鋼最主要的特性——紅硬性。而碳素工具鋼經淬火和低溫回火後,在室溫下雖有很高的硬度,但當溫度高於200℃時,硬度便急劇下降,在500℃硬度已降到與退火狀態相似的程度,完全喪失了切削金屬的能力,這就限制了碳素工具鋼製作切削工具用。而高速鋼由於紅硬性好,彌補了碳素工具鋼的致命缺點,可以用來製造切削工具。
高速鋼的熱處理工藝較為複雜,必須經過退火、淬火、回火等一系列過程。退火的目的是消除應力,降低硬度,使顯微組織均勻,便於淬火。退火溫度一般為860~880℃。淬火時由於它的導熱性差一般分兩階段進行。先在800~850℃預熱(以免引起大的熱應力),然後迅速加 熱到淬火溫度1190~1290℃(不同牌號實際使用時溫度有區別),後油冷或空冷或充氣體冷卻。工廠均採用鹽爐加熱,現真空爐使用也相當廣泛。淬火後因內部組織還保留一部分(約30%)殘餘奧氏體沒有轉變成馬氏體,影響了高速鋼的性能。為使殘餘奧氏體轉變,進一步提高硬度和耐磨性,一般要進行2~3次回火,回火溫度560℃,每次保溫1小時。
生產製造方法:通常採用電爐生產,曾採用粉末冶金方法生產高速鋼,使碳化物呈極細小的顆粒均勻地分布在基體上,提高了使用壽命。
用途:用於製造各種切削工具。如車刀、鑽頭、滾刀、機用鋸條及要求高的模具等。
種類
高速鋼是一種複雜的鋼種,含碳量一般在0.70~1.65%之間。含合金元素量較多,總量可達10~25%。按所含合金元素不同可分為:①鎢系高速鋼(含鎢 9~18%);②鎢鉬系高速鋼(含鎢5~12%,含鉬2~6%);③高鉬系高速鋼(含鎢0~2%,含鉬5~10%);④釩高速鋼,按含釩量的不同又分一般含釩量(含釩 1~2%)和高含釩量(含釩2.5~5%)的高速鋼;⑤鈷高速鋼(含鈷 5~10%)。按用途不同高速鋼又可分為通用型和特殊用途兩種。①通用型高速鋼:主要用於製造切削硬度HB≤300的金屬材料的切削刀具 (如鑽頭、絲錐、鋸條)和精密刀具(如滾刀、插齒刀、拉刀),常用的鋼號有W18Cr4V、W6Mo5Cr4V2等。②特殊用途高速鋼:包括鈷高速鋼和超硬型高速鋼(硬度HRC68~70),主要用於製造切削難加工金屬(如高溫合金、鈦合金和高強鋼等)的刀具,常用的鋼號有W12Cr4V5Co5、W2Mo9Cr4VCo8等。
物理性能
高速鋼一般不做抗拉強度檢驗,而以金相、硬度檢驗為主。
鎢系和鉬系高速鋼經正確的熱處理後,洛氏硬度能達到63以上,鈷系高速鋼在65以上。鋼材的酸浸低倍組織不得有肉眼可見的縮孔 、翻皮。中心疏鬆,一般疏鬆應小於1級。
金相檢驗的內容主要包括脫碳層、顯微組織和碳化物不均勻度3個項目。
1.高速鋼不應有明顯的脫碳。顯微組織不得有魚骨狀共晶萊氏體存在。
2.高速鋼中碳化物不均勻度對質量影響最大,冶金和機械部門對碳化物不均勻度的級別 十分重視。根據鋼的不同用途可對碳化物不均勻度提出不同的級別要求,通常情況下應小於3級。
3.用高速鋼製造切削工具,除因其具有高硬度、高耐磨性和足夠的韌性之外,還有一個重要因素是具有紅硬性。(紅硬性是指刀具在高速切削時,刀刃在紅熱狀態下抵抗軟化的能力。)
一種衡量紅硬性的方法是先把鋼加熱至580~650℃,保溫1小時,然後冷卻,這樣反覆4次後測量其硬度值。高速鋼的淬火溫度一般均接近鋼的熔點,如鎢系高速鋼為1210~1240℃,高鉬系高速鋼為1180~1210℃。淬火後一般需在 540~560℃之間回火3次。提高淬火溫度可以增加鋼的紅硬性。為了提高高速鋼刀具的使用壽命,可對其表面進行強化處理,如低溫氰化、氮化、硫氮共滲等。
高速鋼刀具歷史:
100年前,美國機械工程師泰勒(F.W Taylor)和冶金工程師懷特(M.White)在經過廣泛而系統的切削試驗之後,確立了切削用高速鋼的最佳成分W18Cr4V(C 0.75%,W 18%,Cr 4.0%,V 1.0%),當時切削中碳鋼速度為
30m/min,比之前提高了十幾倍。這一成果帶來了機械加工的劃時代革命,也因此使得刀具材料在進入19世紀
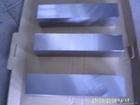
後呈現出異乎尋常的發展速度,創造了前所未有的輝煌。100年來,儘管不斷出現各種新的刀具材料,但高速鋼依然沒有被歷史所淘汰,一直沿用並發展至今,甚至曾長期 占據霸主地位。
刀具材料的發展因其對切削技術、機械加工的直接影響,從而間接地影響了人類經濟社會的發展,而刀具材料史上最具里程碑意義的事件莫過於高速鋼的成功研製。更多的人願意用1900年巴黎博覽會上高速鋼刀具的公開演示作為“高速鋼元年”,不僅因為這個時間的簡單易記,或許更因為高速鋼刀具當年所引起的轟動效應;有人則願意記錄泰勒和懷特研製成功高速鋼的1898年,因為那是一個從無到有的突破;另有一些文獻記錄則強調1906年,那一年泰勒和懷特確立了真正影響後世百年的W18Cr4V。哪一年對今天的我們而言,或許已不再那么重要,重要的是高速鋼乃至其他刀具材料的發展到底將去向何方?
1910年,一位英國人這樣寫道:“在1900年巴黎博覽會上,一些工程師看到了一部高速運轉的車床,上面裝有一個工具,正用它尖頭的熾熱消除一個暗藍色 碎片,工程師們意識到他們親眼見證了工具鋼和工具機方面的一個革命的開始。”巴黎的這件展覽品是匹茲堡伯利恆鋼鐵公司的產品,它正是泰勒和懷特所進行的試驗的刀具材料,是由製造時經過一種熱處理的鉻鎢鋼製成的,其車削速度比碳鋼高出十幾倍。儘管刀具由於與工件磨擦生熱而呈暗紅色,但卻鋒利不減,削鐵如泥,觀眾無不瞠目結舌。此後,這種鋼就獲得了“高速鋼(high-speed steel)”的美名。 人們開始認識到這種鋼的優點,並設計可以利用這種鋼的有效刀具——車刀、刨刀、鑽頭、銑刀等等。一場革命開始了。最初高速鋼只用於粗切,但是隨著不斷的改進,各種刀具都紛紛變成了高速鋼材料。人們逐漸發現高速鋼具有高硬度、高耐磨性和高耐熱性等特點,有較好的工藝性能,強度和韌性配合好,而且具有很好的紅硬性。於是,高速鋼成為了刀具材料市場上幾十年的“霸主”。
在隨後的時間裡,隨著被加工材料的不斷變化以及生產加工的需要,人們不斷改變高速鋼的成分,先後出現了鈷高速鋼、高鉬高速鋼M1、鎢鉬高速鋼M2、高碳高釩高速鋼(超高速鋼)、加硫易切削高速鋼、超硬高速鋼M40系列;直至1965年,美國Crucible Steels公司發明了粉末冶金高速鋼,之後由瑞典Stora廠於1970年投入生產。 目前,高速鋼常用於鑽頭、絲錐、鋸條以及滾刀、插齒刀、拉刀等精密刀具,尤適用於製造複雜的薄刃和耐衝擊的金屬切削刀具。高速鋼刀具100年來的發展大致可以分為兩半,前半個世紀是高速鋼刀具的輝煌,高速鋼被用來製造幾乎所有品種的刀具以實現各種切削加工。但隨著各種被加工材料機械性能的不斷提高,高速鋼逐漸難以招架。
1923年,硬質合金的出現使得切削速度提高到每分鐘一百多米至幾百米,而且其硬度更高,可以切削高速鋼所加工不了的材料,但由於硬質合金脆性較大,可加工性又差,因此只能在部分加工範圍內代替高速鋼,在很長一段時間內並沒有撼動高速鋼的霸主地位。但後來,硬質合金的性能不斷提高,發展了許多新品種,逐漸蠶食著高速鋼刀具的市場份額。 隨後又出現了陶瓷、立方氮化硼、人造金剛石等更為先進的刀具材料,它們的硬度和耐磨性又超過了硬質合金。儘管它們由於脆性大、價格昂貴等原因難以占據較大的市場份額,但這對高速鋼刀具而言,尤其是近三四十年以來,無疑使其下滑萎縮十分明顯,硬質合金刀具至今已經替代了很大一部分高速鋼刀具。於是,逐漸形成了以硬質合金刀具和高速鋼刀具為主體的行業架構。 如今,高速鋼刀具的確是風光不再了。根據有關統計,硬質合金刀具已占世界刀具消費總額的55%,高速鋼刀具為40%,超硬刀具為5%。近20年高速鋼刀具產值每年遞減1.25%,而硬質合金刀具則每年遞升1.1%。
另一方面,高速鋼材料中的一些主要元素如鎢的儲藏資源在世界範圍內日漸枯竭,據估計其儲量只夠再開採使用40~60年,因此高速鋼本身也面臨嚴峻的發展危機。國際生產工程學會(CIRP)在一項研究報告中指出:“由於刀具材料的改進,允許的切削速度每隔十年幾乎提高一倍。”在這100年中,不斷有新的材料出 現,原有的材料也不斷改進。 儘管高速鋼刀具在全世界的銷售額不斷減少,但是高性能的鈷高速鋼和粉末冶金高速鋼的使用量卻在不斷增加,主要用於鈦合金等難加工材料的切削。它們比普通的高速鋼有更好的耐磨性、紅硬性和使用的可靠性,尤其是粉末冶金高速鋼的性能更好,甚至在綜合評價中優於硬質合金刀具。粉末冶金工藝可在高速鋼中加入較多合金元素而不會損害材料的強韌性或耐磨性,從而可製成具有高硬度、高耐磨性、可吸收切削衝擊、適合高切除率加工和斷續切削加工的刀具,大有逐漸取代脆性較大、在切削衝擊下易發生碎裂的整體硬質合金刀具的趨勢。
近幾年,用高性能高速鋼製造的刀具已擴大套用到一般的加工中,成為國外高速鋼刀具的常規產品。世界粉末冶金高速鋼在刀具上的套用及各類刀具占的百分比已達到齒輪刀具占70%,拉刀占30%,立銑刀占20%,鑽頭占1%,這有助於維持高速鋼刀具的套用領域。 儘管世界範圍來講,已全面進入硬質合金刀具時代,但就國內而言,高速鋼刀具依然占有相當強勢的份額。不過,我國高速鋼刀具仍舊主要是普通高速鋼,高速鋼的品級有待提升。 由於礦藏資源日益枯竭以及其他刀具材料的不斷侵蝕,高速鋼刀具是否真能在歷史舞台上繼續活躍100年,實難可知,但顯而易見的是,它肯定會在較長時間內繼續存在並繼續發揮重要的作用。國內頻頻有聲討普通高速鋼生產的聲音,甚至大有打殺圍堵的意味,一位行業專家則堅稱,“目前國內普通高速鋼的市場需求依然旺盛(儘管這並不符合世界刀具發展的主流),有需求生產企業自然樂意供應,我們目前更應該做的恐怕是引導而不是圍堵,引導企業提升高速鋼刀具的品級,減少大量低附加值產品的生產。
高速鋼刀具硬度與熱處理
1、常用高速鋼刀具硬度推薦值
通用高速鋼(HSS)淬火回火後的硬度可達63~67HRC,高性能高速鋼(HSS-E) 、粉末高速鋼(SPM) 可達66~70HRC。對於在一定切削條件下的刀具來說,必定有一個恰當的硬度值,表1是部分高速鋼刀具硬度的推薦值。
從表1可以看出,對一般刀具來說,若採用HSS硬度控制在65~66HRC 較好,而M42之類的HSS-E硬度雖可達到69~70HRC,但實際上此類刀具的硬度最佳範圍為66~67HRC。
表1高速鋼刀具硬度推薦值
刀具名稱 推薦硬度值(HRC) 過熱級別
HSS HSS-E、SPM
直柄麻花鑽 ≤Ø4mm 63.5~66 64~66 不許過級
>Ø4mm 64~66 65~67 ≤2
密齒大薄片銑刀 62~65 64~66 不許過熱
車刀 4~16mm 64~66 66~67 ≤2
>16mm 65~67 66~68 ≤4
齒輪滾刀 64~66 65~67.5 ≤2
中齒鋸片銑刀
螺釘槽銑刀 厚度≤1mm 62.5~65 64~65.5 不許過熱
厚度>1mm 63.5~66 65~67 ≤1
立銑刀 ≤Ø6mm 63.5~66 65~66.5 ≤1
>Ø6mm 64.5~66.5 65~67 ≤2
三面刃銑刀 厚度≤8mm 64~66 65~67 ≤1
厚度>8mm 64~66.5 65~67 ≤2
磨牙機用絲錐 M3~8 62~65 64~66 不許過熱
M>8 63~66 65~67 不許過熱
凹凸半圓銑刀 64~66 65~67.5 ≤1
角度銑刀 63.5~66 64~67 ≤1
拉刀 63.5~66 64~67 不許過熱
推刀 64~66 65~67.5 ≤1
插齒刀 64~66 65~67 ≤1
刨齒刀 64~66 65~67 ≤2
剁刀片 62~64 63~65 不許過熱
錐齒輪銑刀 64~66 65~67 不許過熱
2 刀具的硬度和韌性的關係
硬度和韌性是集中在刀具上一對最為突出的矛盾,刀具材料從碳素工具鋼、合金工具鋼、高速鋼、硬質合金髮展到當前的陶瓷、立方氮化硼等超硬材料,刀具的硬度越來越高,韌性卻越來越差。從某種意義上講,謀求刀具的高韌性比高硬度難得多。
在高速鋼刀具產品中,只對硬度作具體規定,用HSS製造的刀具,除鑽頭、中心鑽有下限硬度(HRCP63) 要求外,其餘產品一律為63~66HRC,而對韌性未作任何要求。
幾十年的實踐證明,過高的硬度反而使刀具的壽命下降。60年代初,全國工具行業總工程師會議曾決定,高速鋼刀具硬度超過66.5HRC 不得出廠。由於當時超硬高速鋼和粉末高速鋼還未套用,那樣的規定對促進刀具業的發展有指導意義。到了70年代,日本學者提出“對於一般刀具把硬度控制在65~66HRC”的觀點。從全國曆年刀具行評結果可知,凡獲一等品、優等品的高速鋼刀具,其硬度都在65HRC以上,足以說明,低硬度不可能高壽命。國家規定的硬度下限指標,筆者認為只是合格品的最低水平,如果連合格品標準也達不到,在市場競爭中就沒有立足之地。
這裡應該特別指出的是,同規格刀具,常因材料不同而使熱處理工藝各異,儘管硬度完全相同,但刀具壽命不盡相同,甚至有較大的差距,就是同爐號相同材料製造的同規格刀具,也會出現上述情況。硬度只是表面現象,金相組織才是本質的東西,光測硬度不看金相不可取。高硬度並非高壽命,刀具壽命的高低,還與原材料碳化物偏折、淬火晶粒度、碳化物溶解程度、回火情況、過熱級別等諸多因素有關。通過何種熱處理工藝達到工藝要求的硬度值,歷來是熱處理行家們關心的問題,其中淬火加熱溫度最為重要,稍有疏忽,就會出現質量問題。常用高速鋼淬火溫度見表2。
表2 常用高速鋼淬火溫度
牌號 W18 Cr4V W6Mo5 Cr4V2 W9Mo3 Cr4V W2Mo9 Cr4V W7Mo4 Cr4V W4Mo3 Cr4V W6Mo5 Cr4V2Al W2Mo9 Cr4VCo8 W6Mo5 Cr4V2Co5 APM23 HAP50 S390PM CPM M4
推薦淬火溫度(℃) 1260- 1290 1210- 1230 1220- 1240 1180- 1200 1210- 1240 1160- 1185 1200- 1215 1160- 1190 1190- 1215 1170- 1190 1180- 1220 1190- 1230 1170- 1190
1.除大規格鑽頭、車刀以及滾刀淬火金相奧氏體晶粒度為9~9.5級外,其餘刀具淬火金相宜控制在10~10.5級較妥:
2 粉末高速鋼淬火金相為10~11級:
3 回火溫度一般為550~560℃,回火4次。
3 結語
高速鋼刀具的硬度是影響刀具壽命的主要指標,硬度高,耐磨,但韌性差。硬度過高在使用中易發生崩刃, 導致刀具永久性失效: 硬度適中,韌性好,使用中難免要磨損,但可以修磨使刀具恢復原有的功能。當被切削材料硬度高時,刀具的硬度取上限, 反之取中下限。硬度63~64HRC的刀具,雖然達到國家標準,但在實際使用中,壽命不會很高。
提高高速鋼刀具耐用度的有效措施:
對拉刀、滾刀、鉸刀、銑刀等複雜高速鋼刀具,在低溫條拌下,進行碳、氮、硫、硼、氧等多元素共滲,使刀具的耐用度平均提高2 倍~5倍。這是因為這些元素滲人刀具表層後,使刃具表層的化學成分發生了變化,在切削過程中起到了減小摩擦和自潤滑作用,從而降低了切削力和切削熱,提高了刀具耐用度,降低了生產成本。 此工藝簡單,工作溫度低,是一種提高複雜高速鋼刀具耐用度的有效措施。