基本介紹

轉向節是汽車轉向橋上的主要零件之一,轉向節的功用是承受汽車前部載荷,支承並帶動前輪繞主銷轉動而使汽車轉向。在汽車行駛狀態下,它承受著多變的衝擊載荷,因此,要求其具有很高的強度。
轉向節通過三個襯套和兩個螺栓與車身相連,並通過法蘭盤的制動器安裝孔與制動系統相連。在車輛高速行駛時,路面通過輪胎傳遞到轉向節上的振動,是我們分析時考慮的主要因素。計算時利用已有的整車模型,對整車施加4G的重力加速度,算出轉向節三個襯套中心點和兩個螺栓安裝孔中心點的支反力作為施載入荷,並約束法蘭盤連線制動系統端面上所有結點的123456自由度。
套用範圍

轉向傳動軸在汽車上套用比較廣泛。在發動機前置後輪或全輪驅動的汽車上,由於彈性懸架的變形,變速器或分動器輸出軸與驅動橋輸入軸的軸線相對位置經常變化,所以普遍採用十字軸轉向傳動軸。在轉向驅動橋中,內、外半軸之間的夾角隨行駛需要而變,這時多採用等速轉向傳動軸。當後驅動橋為獨立懸架時,也必須採用轉向傳動軸。
轉向節按扭轉方向是否有明顯的彈性,可分為剛性轉向節和撓性轉向節。剛性轉向節是靠零件的鉸鏈式連線傳遞動力的,可分成不等速轉向節(如十字軸式)、準等速轉向節(如雙聯式、凸塊式、三銷軸式等)和等速轉向節(如球叉式、球籠式等)。撓性轉向節是靠彈性零件傳遞動力的,具有緩衝減振作用。
不等速轉向節是指轉向節連線的兩軸夾角大於零時,輸出軸和輸入軸之間以變化的瞬時角速度比傳遞運動,但平均角速度比為1的轉向節。準等速轉向節是指在設計角度下工作時以等於1的瞬時角速度比傳遞運動,而在其它角度下工作時瞬時角速度比近似等於1的轉向節。輸出軸和輸入軸以等於1的瞬時角速度比傳遞運動的轉向節,稱之為等速轉向節。
組成特點

轉向節形狀比較複雜,集中了軸、套、盤環、叉架等四類零件的結構特點,主要由支承軸頸、法蘭盤、叉架三大部分組成。支承軸頸的結構形狀為階梯軸,其結構特點是由同軸的外圓柱面、圓錐面、螺紋面,以及與軸心線垂直的軸肩、過渡圓角和端面組成的迴轉體;法蘭盤包括法蘭面、均布的連線螺栓通孔和轉向限位的螺紋孔;叉架是由轉向節的上、下耳和法蘭面構成叉架形體的
轉向輪定位參數
為了保持汽車直線行駛的穩定性、轉向的輕便性和減小輪胎與機件間的磨損,轉向輪、轉向節和前軸三者之間與車架必須保持一定的相對位置,這種具有一定相對位置的安裝稱為轉向輪定位,也稱前輪定位。正確的前輪定位應做到:可使汽車直線行駛穩定而不擺動;轉向時轉向盤上的作用力不大;轉向後轉向盤具有自動回正作用;輪胎與地面間不打滑以減少油耗,延長輪胎使用壽命。前輪定位包括主銷後傾、主銷內傾、前輪外傾及前輪前束。
主銷後傾角

主銷在汽車的縱向平面內,其上部有向後的一個傾角γ,即主銷和地面垂直線在汽車縱向平面內的夾角,如圖所示。
主銷後傾角γ能形成回正的穩定力矩,當主銷具有後傾角γ時,主銷軸線和路面的交點將位於車輪與路面接觸點的前面。當汽車直線行駛時,若轉向輪偶然受到外力作用而稍有偏轉(向右偏轉如圖箭頭所示),將使汽車行駛方向向右偏離。這時,由於汽車本身離心力的作用,在車輪與路面接觸點b處,路面對車輪作用著一個側向反力
。反力對車輪形成一個繞主銷軸線作用的力矩L,其方向正好與車輪偏轉方向相反。在此力矩的作用下,將使車輪迴到原來的中間位置,從而保證汽車穩定直線行駛,故此力矩稱為回正力矩。
但此力矩也不宜過大,否則在轉向時為了克服該穩定力矩,駕駛員要在轉向盤上施加較大的力(即所謂的轉向沉重)。因穩定力矩的大小取決於力臂L的大小,而力臂L的大小取決於後傾角γ的大小。
現在一般採用的γ角不超過2-3°。現代高速汽車由於輪胎氣壓降低、彈性增加,而引起穩定力矩增大。因此,γ角可以減小到接近於零,甚至為負值。
主銷內傾角

主銷在汽車的橫向平面內,其上部向內傾斜一個β角(即主銷軸線與地面垂直線在汽車橫向平面內的夾角)成為主銷內傾角。
主銷內傾角β也有使車輪自動回正的作用,如圖所示。當轉向輪在外力作用下由中間位置偏轉一個角度時,車輪的最低點將陷入路面以下。但實際上車輪下邊緣不可能陷入硬路面以下,而是將轉向輪連同整個汽車前部向上抬起一個相應的角度。這樣,汽車本身的重力有使轉向輪迴到原來中間位置的效應。
此外,主銷的內傾還使得主銷軸線與路面交點到車輪中心平面與地面交線距離c減小,從而可減小轉向時駕駛員加在轉向盤的力,使轉向操縱輕便,同時也可以減小從轉向輪傳到轉向盤的衝擊力。但c值也不宜過小,即內傾角不宜過大,否則在轉向時車輪繞主銷偏轉的過程中,輪胎與路面間將產生較大的滑動,因而增加了輪胎與路面間的摩擦阻力。這不僅是轉向變得沉重,而且加速了輪胎的磨損。因此,一般內傾角β不大於8°,距離c一般為40-60mm。
主銷內傾角是在前梁設計中保證的,由機械加工來實現。加工時,將前梁兩端主銷孔軸線上端向內傾斜就形成內傾角β。
車輪外傾角
除上述主銷後傾角和內傾角兩個角度保證汽車穩定直線行駛外,車輪外傾角α也具有定位作用。α是通過前輪中心的汽車橫向平面與前輪平面的交線與地面垂線之間的夾角,如圖4(a)、(c)所示。如果空車時前輪的安裝正好垂直於路面,則滿載時,車橋將因承載變形而可能出現前輪內傾,這將加速輪胎的偏磨損。另外,路面對前輪的垂直反作用力沿輪轂的軸線分力,將使輪轂壓向外端的小軸承,加重了外端小軸承及輪轂緊固螺母的負荷,安裝前輪時應預先使其有一定的外傾角,以防止前輪內傾。同時,前輪有了外傾角也可以與拱形路面相適應。但是,外傾角也不宜過大,否則也會使輪胎產生偏磨損。
前輪的外傾是在轉向節設計中確定的。設計時使轉向節軸頸的軸線與水平面成一角度,該角度即為前輪外傾角α(一般為1°左右)。
前輪前束
前輪有了外傾角後,在滾動時就類似於滾錐,從而導致前輪向外滾開。由於轉向橫拉桿和車橋的約束使前輪不可能向外滾開,前輪將在地面上出現邊滾邊滑的現象,從而加劇輪胎磨損。為了消除前輪外傾帶來的這種不良後果,在安裝前輪時,使汽車兩前輪的中心面不平行,兩輪前邊緣間的距離B小於後邊緣間的距離A,A-B之差成為前輪前束。這樣可使前輪在每一順勢滾動方向接近於向著正前方,從而很大程度上減輕和消除了由於前輪外傾而產生的不良後果。

前輪前束可通過改變橫拉桿的長度來調整。調整時,可根據各廠家規定的測量位置,使兩輪前後距離差A-B符合規定的前束值。一般前束值為0~12mm。測量位置除了如圖5所示位置外,還通常取兩輪胎中心平面處的前後差值,也可以取兩前輪輪輞內側面處前後的差值。此外,前束也可用前束角表示。
加工工藝
1.轉向節是汽車重要安全零部件,全世界的行業人士都及其重視其安全特性,充分認識其安全特性對轉向節的加工有著特別重要的作用,並應貫穿到整個製造過程的控制。
2.轉向節分類,分體式主要用於乘用車(轎車),整體式主要用於商用車(貨車);整體式又分為獨立懸掛轉向節和非獨立懸掛轉向節。從毛坯角度講,整體式的鍛造毛坯都屬於比較有技術複雜係數的產品,對於機加,非獨立懸掛轉向節的加工比較有典型意義,下面所闡述的主要內容就是以非獨立懸掛轉向節作為標本來分析,起到觸類旁通的作用。
3.轉向節的加工分為毛坯製造和成品機加。目前,毛坯主要以鍛件為主,也有採用鑄造毛坯的,但比較少。毛坯的鍛造工藝主要為劈叉、拔桿、預鍛、終鍛等工序組成,一般的鍛造手冊都可以查閱到這種典型工藝,國內的毛坯廠家比較多,網上可查。
4.下面說下機加:
從機加工藝來講,轉向節分為桿部、法蘭盤和叉部等3個部分加工。
(1)桿部加工以中心孔定位,車和磨為主,加工關鍵是磨削。
(2)法蘭盤加工主要是制動器安裝孔的加工,要保證其位置度,同時要兼顧加工效率 。並且,利用其中1孔作為加工叉部定位用。
(3)叉部加工是轉向節加工的難點,採用兩銷一面定位,其加工主要是保證主銷孔的同軸度,以及主銷孔與內端面的垂直度,是整個加工工藝的投資重點和設備選型的關鍵。大部分轉向節在此部位還有橫拉桿裝配用的錐孔,這更增加了叉部加工難度,錐孔加工是許多廠家難以100%合格的項目,應予重視,否則,轉向節的早期失效就從這裡開始。
(4)桿部的強化處理以提高轉向節的疲勞壽命,對大多數類型的轉向節都有這方面的技術要求,一般為滾壓和中頻淬火,以消除表面形成殘餘壓應力,提高產品疲勞強度。國內加工對滾壓要求不高,難點在中頻淬火,主要是感應器的設計和製造,不過,在這方面國內有專業廠家給與解決。
(5)主銷孔壓裝襯套後的加工,有的壓裝後不要求加工,有的壓裝後要求加工。從裝配角度講,壓裝後加工更有利於裝配,否則影響轉向的靈活性。
好了,以上就是轉向節加工主要內容,根據具體轉向節的不同,會有不同程度的變化,同時,加工設備的選擇對整個工藝的影響比較大,因此,具體工藝應根據生產綱領和可供選擇的設備來制訂。
淬火處理
淬火是使鋼強化的基本手段之一,將鋼淬火成馬氏體,隨後回火以提高韌性,是使鋼獲得高綜合機械性能的傳統方法。
轉向節的工作能力一般取決於強度和剛度,轉向節經過淬火,使轉向節的剛度強度都提高了,從而更加耐用,質量更高
常用轉向節淬火設備有以下幾種

16kw超音頻淬火設備技術參數:
型 號 | WH-VI-16 | 輸入功率 | 16kw |
電 源 | 單相220V | 電 壓 | 180-250V |
冷卻水壓 | 0.1Mpa | 輸入電流 | 42A |
水溫保護 | 55℃ | 效率 | 90% |
振盪頻率 | 10-80KHz | 冷卻水壓 | 0.1Mpa |
外形尺寸 | 500×240×450 mm³ | 重量 | 20kg±5% |
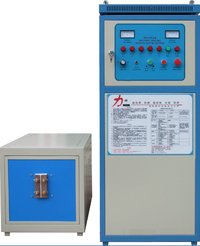
60Kw高頻淬火設備技術參數:
型號 | WH-VI-60 | 輸入功率 | 60KW |
輸入電壓 | 342V-430V | 最大輸入電流 | 90A |
冷卻水流量(主機) | 25L/min(0.1mpa) | 冷卻水流量(變壓器) | 18L/min (0.1mpa) |
振盪頻率 | 15-35KHZ | 冷卻水壓 | 0.1-0.3Mpa |
主機體積 | 590×450×780mm3 | 變壓器體積 | 420×355×450mm3 |
主機重量 | 65±5%kg | 變壓器重量 | 50±5%kg |

200kw中頻淬火設備技術參數:
型號 | GS-ZP-200 | 輸入功率 | 200KW |
最大輸入電流 | 300A | 工作電壓 | 342-430V |
振盪頻率 | 2-4KHz | 進水口水壓 | 0.2-0.5Mpa |
主機體積 | 810*530*1780 | 分機體積 | 500*800*580 |
水溫保護點 | 50℃ | 機身顏色 | 灰色+白色 |

淬火工具機技術參數:
最大淬火長度 (mm) | 4000 | 最大迴轉直徑 ( mm) | ≤φ500 |
工件移動速度 ( mm/s) | 2-60 | 鏇轉速度 (r/min) | 25-125 |
頂尖移動速度 ( mm/min) | 480 | 工件重量 ( kg) | ≤1500 |
輸入電壓 ( V ) | 三相380 | 電機總功率 ( kw) | 3 |
技術突破
在2008~2010年期間爆發的全球金融危機將整個汽車行業拖入了一個前所未有的低谷。經過此次危機後,隨著行業逐漸回暖,在旺盛需求的推動下汽車廠商們正想方設法縮短交貨期。現在,數以百萬計的零配件必須要在很短的時間內加工完成,所以如何提高生產效率已成為應對該行業挑戰的關鍵所在。
最近,伊斯卡推出了一系列解決方案,可有效避免停機時間,縮短零件加工周期,削減單件加工成本(CPP),由此提高生產效率。這些高效加工方案的突出優勢還包括:革命性3P(高性能、高生產率、高收益率)理念、束魔塗層技術(SUMO TEC)硬質合金牌號及塗層、工程方面以及創新性研發。伊斯卡決定將汽車配件劃分為多個門類(套用)並針對性地制定系統性的最佳化加工解決方案。轉向節便屬於其中的一種套用。

轉向節是最複雜最精密的汽車零配件之一。要實現快速低成本生產,採用高效的精密切削刀具不可或缺。以往轉向節都是由鑄鐵或鋼材製成的,但目前市場趨向於改用鋁合金。一方面,這是出於減輕汽車重量,提高燃油經濟性的最佳化需要。另一方面,採用鋁合金的加工成本要遠遠低於採用鑄鐵的加工成本(分別為15~25美分和約1美元)。不過,並非所有情況下,鋁合金轉向節都可以替換鑄鐵或鋼質轉向節 ,但不論何種時候(鋁合金或鑄鐵),都可以通過以下方法來降低加工成本:採用組合刀具、採用FMR(快速金屬切削)刀具和採用換刀速度快的刀具。
採用組合刀具
採用組合刀具,避免換刀是最省錢的辦法之一。而且,由於許多轉向節加工用的數控工具機刀庫容量往往有限,採用組合刀具有時不僅僅是建議,也是必要的措施。
採用FMR(快速金屬切削)刀具
採用FMR(快速金屬切削)刀具可以縮短加工時間並節省額外成本。
1.更高的進給量

伊斯卡束魔變色龍鑽(SUMOCHAM)的進給量比常規硬質合金鑽提高多達2倍。傳統硬質合金鑽受碳化鎢(WC)的力學性質限制,無法承受相對較高的扭矩並容易損壞,只能採用很小的轉進給量。這意味著製造商們無法充分“擠壓”工具機的性能,只能低效率工作。相比之下,束魔變色龍鑽主體由高強度刀具鋼製成,可以承受很高扭矩載荷。此外,和這種可換刀頭設計理念相比,硬質合金鑽還有一個弱點,對總體跳動較敏感,T.I.R.(總體指標偏差)容易造成硬質合金意外折斷。相比鋼製鑽桿,硬質合金鑽頭鑽桿承受彎曲變形的能力極其有限。只要總體跳動值比平均值稍微高出一點,它就很容易折伊斯卡束魔變色龍(SUMOCHAM)可換頭式鑽削系統擁有以下諸多優點,由此成為全球轉向節製造商的首選:
AlTiN塗層硬質合金刀頭結合鋼製鑽桿,可提升端面鑽削加工的每轉進給量多達2倍;刀頭更換,無需對刀時間;頭多次更換也不會影響刀槽壽命;易於集成至柔性組合刀具,適合定製刀具設計。
2.更高的切削速度

例如,對於鋁合金轉向節:經PCD(聚晶金剛石)或DLC(類金剛石)塗層刀具的加工速度遠超未經塗層的硬質合金。雖然這些刀具價格更貴,但由於切削快、壽命長,投資回收快且單件加工成本低很多。轉向節一般都是大批量生產的,故PCD和DLC塗層刀具性價比極高,套用廣泛。最要注意的問題是採用合適的冷卻液並確保其以適當的角度噴向切削區域,從而提供有效的潤滑並避免產生積屑瘤。
3.全新刀具設計理念
採用全新刀具設計理念,大幅增加刀齒密度,從而成倍提高加工效率:轉向節的主軸承孔採用鏜桿、帶導向塊的單刃鉸刀或可調式雙刃鏜刀進行精加工。
這些方法十分可靠,因此長期被人們套用。缺點是進給量超低(採用單刃或雙刃刀具時進給速度只能保持0.15~0.3mm/r),延緩了整個加工過程。
為了加快加工速度,轉向節製造商們試圖用多齒釺焊鉸刀替代這些傳統刀具,這解決了加工周期過長的問題,但又產生了一個新的問題。大直徑鉸刀價格昂貴,如果每次磨損就要更換,用戶很不划算。此外,由於主軸承孔公差要求極高,這些鉸刀無法進行重磨。
後來,這一老辦法有了新的改進。它是一種微調式鉸刀環,帶有釺焊硬質合金切削刃。這種刀具切削速度很快(例如用10齒鉸刀環加工一個?90.0H6孔,其進給量可以達到1mm/r),並且可以使用一顆錐頭螺釘進一步調整直徑來補償磨損。這種直徑調整機制可以達到很高的公差,在大多數情況下有利於延長刀具的壽命。鉸刀環很快成為了加工主軸承孔的常用刀具,但由於以下致命缺點,這一設計理念沒能成為一種最徹底的解決方案:
如果某個刀刃產生了缺口(由於工件材料質量差等原因,這種情況時有發生),會暴露未塗層的基體而形成積屑瘤(BUE),導致精加工表面受損;無法均勻調整刀齒,因此無法精確控制徑向偏差。因此,一些刀齒會參與比其他刀齒更深的切削,加速了其過度磨損。
刀齒磨損後,鉸刀環需要送去重新安裝刀齒。重新安裝費用不菲,通常占到了新鉸刀環價格的65%~70%。用戶還必須控制鉸刀環庫存,以便安排重新修磨和重塗層等。所有這些都要占用額外的資源,所以許多用戶都不喜歡這個辦法。
那么轉向節主軸承孔精加工的終極刀具在哪裡呢?多年前,伊斯卡的研發專家們想出了一種新辦法,並立刻贏得了汽車業的熱烈追捧。

這種全新刀具是一種可換刀片式微調多齒鉸刀。每一個刀片都可以在幾秒鐘內單獨進行精密的調整以獲得所需直徑。憑藉這些功能,這種鉸刀既滿足高孔徑公差要求,又消除了鉸刀的徑向偏差問題,延長了刀具的壽命。此外,高強度的立裝刀片,提高了加工經濟性:具有4個切削刃。切削刃不需重新刃磨和重新塗層。多數情況下,轉向節加工工具機具有兩個主軸,為此伊斯卡還提供第二套方案作為備用(一把為右手刀,備用的為左手刀),左手鉸刀可以使用右手鉸刀未使用的額外的4個切削刃,刀片性價比更高。可視情況輕鬆地更換刀片牌號(在釺焊鉸刀上這是不允許的)。
採用換刀速度快的刀具
採用不用從工具機取出即可更換刀片或刀片更換速度超快的刀具,從而避免或縮短停機時間並節省額外費用。