汽車焊裝生產線踏台
簡介
汽車企業在對焊裝生產線進行前期規划過程中,著重在焊裝車間的平面布置、焊裝生產線柔性化設計、焊裝車間物流方案等方面進行規劃。對於踏台此類生產線配套設施的關注程度不高,或者不加考慮。而在現場生產過程中,生產工藝及操作員工對踏台的實用性和安全性等方面要求較高,不規範的踏台往往不能滿足生產的需求及安全生產的目的,而且在反覆修改踏台的同時既耽誤生產,又浪費成本。
踏台設計的一般標準
總原則:安全、實用、易製作、易安裝、便於工裝維修。
1、高度
踏台高度的制定應符合人體工程學標準,即採取直立姿勢工作面的高度應符合設備高/人體身高=6/11的標準。結合焊裝生產線的實際情況,確定焊鉗的最舒適操作高度為900±150mm。在規劃踏台高度時,應結合3D 焊點高度數據來制定踏台高度,超出範圍的應做出相應修改。
2、寬度
踏台寬度制定按照生產線焊鉗型號來確定最小寬度,以焊鉗型號最大的焊鉗能自由翻轉為基數加 200mm 確定最小寬度,即假設焊鉗 X30-6045 在整條生產線型號最大,焊鉗能滿足擺放和自由翻轉要求的最小間距為800mm,則踏台寬度為1000mm。最大寬度應依據廠房設計中生產線鋼結構兩梁之間的距離而定,踏台裝配到位後生產線應介於兩梁之間,避免占據物流通道。
3、長度
踏台長度一般來說和整體生產線長度一致,首尾兩端適當加長布置以保證操作者的安全生產,且應預留工位器具、焊接設備和電控櫃等輔助設施的空間。
4、台階
踏台台階是整個踏台設計中需要考慮最多的環節。如台階寬度、高度、開口位置等等。如圖1踏台台階示意圖所示:
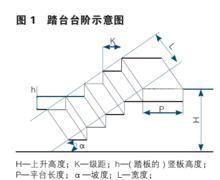
在踏台區域設定台階時應考慮以下因素:
①級距 K(兩個相鄰踏板之間的水平距離)和豎板高度 h(兩個相鄰踏板之間的垂直距離)應滿足下式:600 ≤ K+2h ≤ 660。其中 h ≤ 250mm, K ≥ 100mm。結合現場實際經驗和人機工程學理論,我們建議現場踏台設計中級距 K=230±30mm;豎板高度h=200±30mm。②坡度 α 應依據現場踏台高度、台階最大寬度等因素來確定。一般情況下,α在30°~38°之間。③最上一級踏板應與梯段平台為同一水平面。④踏台樓梯的上升高度H一般不宜超過3m,在特殊情況下,這一高度也不應該超過 4m。否者,在連續到達另一梯段之前,需要增加一梯段平台,梯段平台的長度至少應為 800mm,並大於或等於梯段的寬度。⑤踏台開台階的位置原則上應保證在相鄰工位間設定一開口,依據現場工位器具、電控裝置和焊接設備的分布情況而定。
5、護欄
為防止操作人員偶然跌落或偶然進入危險區域,需要在踏台區域裝置護欄。一般在平台區域裝配的平台護欄示意圖如圖 2 所示:
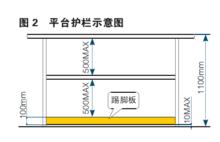
踏台區域增加平台護欄的原則:①當踏台高度超過 500mm 時,應安裝護欄。②如果操作平台和機器構架或牆壁之間的間距小於 200mm 並且構架的防護等效於護欄時,不需要設護欄。但是,當操作平台和相鄰的構架之間的間距大於 300mm 時,要有踢腳板。③護欄至少應包括一根中間橫桿或某種其他等效防護。扶手和橫桿及橫桿與踢腳板之間的自由空間不應超過 500mm。④當用立桿代替橫桿時,各立桿之間的水平間距最大為 180mm。⑤各支柱軸線間距離應限制在 1500mm 內。如果超過這一距離,應特別注意支柱的固定強度和固定的裝置。⑥護欄高度一般設定為 1100mm。⑦增加護欄的具體位置應考慮生產工藝。
如果踏台台階過高、過窄或有其他特殊要求時,應在台階處增加台階護欄,保證生產安全。一般的台階護欄示意圖如圖3所示:
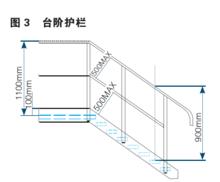
台階護欄的製作要求是:①當台階的上升高度超過500 mm並且斜梁外側有大於 200 mm 的橫向間距時,在其側邊應附加護欄。扶手的垂直高度至少應為 900mm。②為了保證安全抓握,扶手的直徑應為25~50mm 之間的圓形截面或便於用手抓握的等效截面。③護欄至少應包括一根橫桿或某一等效裝置。扶手和橫桿之間以及橫桿和斜梁之間的淨間距不應超過 500mm。④除安裝固定支撐的下端面以外,在扶手長度方面上,扶手的100mm距離內沒有障礙。
6、踢腳板
踢腳板是為避免物體由地板平面下落而設定的護欄下部的實體零件,最小高度100mm的踢腳板應安置得離基面不大於10mm,踢腳板所有尖角應打磨成鈍角。
7、其他
①使用的材料性能或經處理後(刷防鏽漆)應能耐環境引起的腐蝕。②可能與使用者接觸的某些部分應設計得不會產生傷害或阻滯(如避免尖角、焊接毛刺、粗糙的邊緣等)。③各踏板和梯段平台應具有良好的防滑性能。④打開或關閉活動部分(門),應不會對使用者或附近的其他人產生進一步危險(例如剪下或偶然墜落)。⑤為了保證安全,裝配用的附屬檔案、鉸鏈、支座、支承件和安裝件都應有足夠的剛度和穩定性。⑥踏板和構架尺寸的設計應使它們能承受預期的載荷。⑦踏台平面之間的高度差應在 10mm 以下。
踏台設計和製造過程中的一些建議
1、夾具、踏台一體化設計理念
許多企業的踏台製作理念是由負責焊裝生產線規劃的工藝規劃師主控,按照前期積累的踏台設計經驗及該生產線的規劃需求,對現場踏台的高度、寬度和台階位置等做一簡單的數據分析,確定出踏台的具體尺寸進行製作。在夾具到達現場時,將前期製作踏台與現場夾具進行匹配並套用於生產。通過這個流程製作的踏台往往存在很大的問題,在實際生產過程中需要經過許多次的修改才能交付車間使用。這種方法既耽誤生產進度,又存在安全隱患,造成資源的浪費。基於上述原因,建議將夾具、踏台進行一體化設計,將踏台的設計尺寸由夾具廠家主控。夾具廠家設計夾具的時候,對夾具的功能尺寸和配套設施(電控櫃、電控開關、氣路和電路)的分布有最直觀的數據,並且當夾具製作完畢調試階段,夾具廠家也能實際了解現場操作的要求,模擬現場情況的踏台設計更能滿足今後生產的要求。這樣做有幾點好處:第一、更安全、相容性更好;夾具廠家在設計踏台時,踏台和夾具之間的間隙可通過多種方式進行控制,使踏台與夾具的接觸曲面更貼合,相容性更好,實現踏台與夾具的“無縫結合”,消除了安全隱患。第二、節約成本;在公司工藝人員的配合下,由夾具廠家主控的踏台設計,踏台的一次成型率更高,可以避免後期的反覆修改所帶來的資源浪費。第三、便於維修;由於是夾具廠家主控踏台的設計,其勢必將夾具前期的安裝和後期的維修考慮到踏台的設計過程中來,這樣更能大大避免踏台後期的修改和便利於後期的生產。
2、夾具前期規劃建議
①建議夾具廠家在設計夾具時,將所有氣路儘量安裝在 BASE板以下,方便踏台匹配,避免踏台與夾具匹配時產生縫隙。②由於踏台只是生產過程中的配套設備,如果前期能將夾具做低或者將夾具置於地溝中,避免現場踏台的製作,既安全,又節約成本。③在前期規劃時,將車間物流、電控櫃放置、操作檯布局、工位器具放置等生產線其他匹配設備考慮到規劃中去。
3、踏台後期安裝問題
①踢腳板製作和裝配過程中,應避免產生直角。②踏台與夾具線匹配時避免產生縫隙。③所有方向朝外的踏台應使用蒙板包裹至踏台低端(距地面 10mm),更安全、更美觀、更衛生。④踏台結構必須符合標準,並且踏台的角座需要加固,保證踏台的穩定性和平度。
伸縮式踏台在焊裝調整線上的套用
焊裝調整線存在的問題
操作者在焊裝調整線上對駕駛室白車身總成進行的補焊、打磨、修磨和裝調等,對駕駛室白車身總成質量具有舉足輕重的作用。集瑞聯合重工有限公司的焊裝調整線由於工位較多、白車身尺寸較大,因此選擇了滑橇輸送式的線體結構。該焊裝調整線主要由滑橇、驅動滾床(又稱輥床)和電氣控制系統(主要由PLC組成)等部分組成。載貨汽車駕駛室白車身總成的高度尺寸遠大於轎車白車身總成的高度尺寸,因此在焊裝調整線兩側配備了高度為80~100cm的踏台,目的是方便
操作者對卡車白車身腰線以上部分進行相應操作。從實際使用情況看,這種踏台雖然能夠為操作者在車身X向和Z向的操作提供很大的便利,但由於卡車白車身寬度尺寸較大,Y向操作仍存在操作盲區,相應鈑金缺陷無法處理,如果勉強操作則存在安全隱患。
改進措施
為解決上述問題,在現有操作台的基礎上增加了伸縮式踏台工裝,並需保證伸縮式踏台和白車身滑橇各自運行的安全性。
1、伸縮式踏台的驅動方式
目前常用的驅動方式有電動、液壓傳動和氣動。前兩種驅動方式需要較大的空間,氣動驅動方式需要的空間相對較小,且所需氣源是焊裝調整線原來就具備的條件,因此伸縮式踏台採用氣動驅動方式。
2、伸縮式踏台操作安全性的保證
焊裝調整線滑橇式輸送結構通過PLC技術根據編輯信號控制滑橇在滾床上的前進和停止等動作,伸縮式踏台也採用PLC技術控制踏台的伸出和縮回。滑橇式輸送結構和伸縮式踏台都採用PLC控制技術可以使兩者的信號進行互鎖編輯,從而保證滾床和滑橇在運動時,伸縮式踏台無法工作,反之亦然,確保了操作的安全性。
3、伸縮式踏台的安裝
伸縮式踏台的滾輪和導軌使用螺栓連線,通過對螺栓的上、下調節可以對滾輪和導軌進行上、下調節,從而保證踏台滾輪和導軌之間充分配合,也避免了由於地面的開裂或沉降等因素對伸縮式踏台運行的影響。