鍋爐結構
鍋爐採用單鍋筒,自然循環方式,總體上分為前部及尾部兩個豎井。前部豎井為總吊結構,四周有膜式水冷壁組成。自下而上,依次為一次風室、密相床、懸浮段,尾部煙道自上而下依次為高溫過熱器、低溫過熱器及省煤器、空氣預熱器。尾部豎井採用支撐結構,兩豎井之間由立式鏇風分離器相連通,分離器下部聯接回送裝置及灰冷卻器。燃燒室及分離器內部均設有防磨內襯,前部豎井用敖管爐牆,外置金屬護板,尾部豎井用輕型爐牆,由八根鋼柱承受鍋爐全部重量。
鍋爐採用床下點火(油或煤氣),分級燃燒,一次風比率占50—60%,飛灰循環為低倍率,中溫分離灰渣排放採用乾式,分別由水冷螺鏇出渣機、灰冷卻器及除塵器灰斗排出。爐膛是保證燃料充分燃燒的關鍵,採用湍流床,使得流化速度在3.5—4.5m/s,並設計適當的爐膛截面,在爐膛膜式壁管上鋪設薄內襯(高鋁質磚),即使鍋爐燃燒用不同燃料時,燃燒效率也可保持在98—99%以上。
高溫分離器入口煙溫在800℃左右,鏇風筒內徑較小,結構簡化,筒內僅需一層薄薄的防磨內襯(氮化矽磚)。其使用壽命較長。循環倍率為10—20左右。
循環灰輸送系統主要由回料管、回送裝置,溢流管及灰冷卻器等幾部分組成。
床溫控制系統的調節過程是自動的。在整個負荷變化範圍內始終保持濃相床床溫850-950℃間的某一恆定值,這個值是最佳的脫硫溫度。當自動控制不投入時,靠手動也能維持恆定的床溫。
保護環境,節約能源是各個國家長期發展首要考慮的問題,循環流化床鍋爐正是基於這一點而發展起來,其高可靠性,高穩定性,高可利用率,最佳的環保特性以及廣泛的燃料適應性,特別是對劣質燃料的適應性,越來越受到廣泛關注,完全適合我國國情及發展優勢。
煙風系統
循環流化床鍋爐系統通常由流化床燃燒室(爐膛)、循環灰分離器、飛灰回送裝置、尾部受熱面和輔助設備等組成。循環流化床鍋爐系統通常由燃燒系統和汽水系統所組成,燃料在鍋爐的燃燒系統中完成燃燒過程,並通過燃燒將化學能轉變為煙氣的熱能,以加熱工質;汽水系統的功能是通過受熱面吸收煙氣的熱量,完成工質由水轉變為飽和蒸汽,再轉變為過熱蒸汽的過程。
循環流化床鍋爐的煙風系統是循環流化床鍋爐的風(冷風和熱風)系統和煙氣系統的統稱。循環流化床鍋爐的風系統主要由燃燒用風和輸送用風兩部分組成。前者包括一次風、二次風、播煤風(也稱三次風),後者包括回料風、石灰石輸送風和冷卻風等。
鍋爐簡介
(circulating fluidized bed)
是在鼓泡床鍋爐(沸騰爐)的基礎上發展起來的,因此鼓泡床的一些理論和概念可以用於循環流化床鍋爐。但是又有很大的差別。早期的循環流化床鍋爐流化
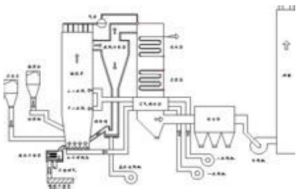
速度比較高,因此稱作快速循環循環床鍋爐。快速床的基本理論也可以用於循環流化床鍋爐。鼓泡床和快速床的基本理論已經研究了很長時間,形成了一定的理論。要了解循環流化床的原理,必須要了解鼓泡床和快速床的理論以及物料從鼓泡床→湍流床→快速床各種狀態下的動力特性、燃燒特性以及傳熱特性。
流態化
當固體顆粒中有流體通過時,隨著流體速度逐漸增大,固體顆粒開始運動,且固體顆粒之間的摩擦力也越來越大,當流速達到一定值時,固體顆粒之間的摩擦力與它們的重力相等,每個顆粒可以自由運動,所有固體顆粒表現出類似流體狀態的現象,這種現象稱為流態化。
對於液固流態化的固體顆粒來說,顆粒均勻地分布於床層中,稱為“散式”流態化。而對於氣固流態化的固體顆粒來說,氣體並不均勻地流過床層,固體顆粒分成群體作紊流運動,床層中的空隙率隨位置和時間的不同而變化,這種流態化稱為“聚式”流態化。循環流化床鍋爐屬於“聚式”流態化。
固體顆粒(床料)、流體(流化風)以及完成流態化過程的設備稱為流化床。
臨界速度
1. 對於由均勻粒度的顆粒組成的床層中,在固定床通過的氣體流速很低時,隨著風速的增加,床層壓降成正比例增加,並且當風速達到一定值時,床層壓降達到最大值,該值略大於床層靜壓,如果繼續增加風速,固定床會突然解鎖,床層壓降降至床層的靜壓。如果床層是由寬篩分顆粒組成的話,其特性為:在大顆粒尚未運動前,床內的小顆粒已經部分流化,床層從固定床轉變為流化床的解鎖現象並不明顯,而往往會出現分層流化的現象。顆粒床層從靜止狀態轉變為流態化進所需的最低速度,稱為臨界流化速度。隨著風速的進一步增大,床層壓降幾乎不變。循環流化床鍋爐一般的流化風速是2-3倍的臨界流化速度。
2. 影響臨界流化速度的因素:
(1)料層厚度對臨界流速影響不大。
(2)料層的當量平均料徑增大則臨界流速增加。
(3)固體顆粒密度增加時臨界流速增加。
(4)流體的運動粘度增大時臨界流速減小:如床溫增高時,臨界流速減小。床溫與臨界流速的關係如圖所示。
節能改造
① 加裝燃油節能器;
經燃油節能器處理之碳氫化合物,分子結構發生變化,細小分子增多,分子間距離增大,燃料的粘度下降,結果使燃料油在燃燒前之霧化、細化程度大為提高,噴到燃燒室內在低氧條件下得到充分燃燒,因而燃燒設備之鼓風量可以減少15%至20%,避免煙道中帶走之熱量,煙道溫度下降5℃至10℃。燃燒設備之燃油經節能器處理後,由於燃燒效率提高,故可節油4.87%至6.10%,並且明顯看到火焰明亮耀眼,黑煙消失,爐膛清晰透明。徹底清除燃燒油咀之結焦現象,並防止再結焦。解除因燃料得不到充分燃燒而爐膛壁積殘渣現象,達到環保節能效果。大大減少燃燒設備排放的廢氣對空氣之污染,廢氣中一氧化碳(CO)、氧化氮(NOx)、碳氫化合物(HC)等有害成分大為下降,排出有害廢氣降低50%以上。同時,廢氣中的含塵量可降低30%—40%。安裝位置:裝在油泵和燃燒室或噴咀之間,環境溫度不宜超過360℃。
② 安裝冷凝型燃氣鍋爐節能器;
燃氣鍋爐排煙中含有高達18%的水蒸氣,其蘊含大量的潛熱未被利用,排煙溫度高,顯熱損失大。天然氣燃燒後仍排放氮氧化物、少量二氧化硫等污染物。減少燃料消耗是降低成本的最佳途徑,冷凝型燃氣鍋爐節能器可直接安裝在現有鍋爐煙道中,回收高溫煙氣中的能量,減少燃料消耗,經濟效益十分明顯,同時水蒸氣的凝結吸收煙氣中的氮氧化物,二氧化硫等污染物,降低污染物排放,具有重要的環境保護意義。
③ 採用冷凝式餘熱回收鍋爐技術;
傳統鍋爐中,排煙溫度一般在160~250℃,煙氣中的水蒸汽仍處於過熱狀態,不可能凝結成液態的水而放出汽化潛熱。眾所周知,鍋爐熱效率是以燃料低位發熱值計算所得,未考慮燃料高位發熱值中汽化潛熱的熱損失。因此傳統鍋爐熱效率一般只能達到87%~91%。而冷凝式餘熱回收鍋爐,它把排煙溫度降低到50~70℃,充分回收了煙氣中的顯熱和水蒸汽的凝結潛熱,提升了熱效率;冷凝水還可以回收利用。
④ 鍋爐尾部採用熱管餘熱回收技術;
餘熱是在一定經濟技術條件下,在能源利用設備中沒有被利用的能源,也就是多餘、廢棄的能源。它包括高溫廢氣餘熱、冷卻介質餘熱、廢汽廢水餘熱、高溫產品和爐渣餘熱、化學反應餘熱、可燃廢氣廢液和廢料餘熱以及高壓流體余壓等七種。根據調查,各行業的餘熱總資源約占其燃料消耗總量的17%~67%,可回收利用的餘熱資源約為餘熱總資源的58%。
注意事項
循環流化床鍋爐採用了高效、節能、低污染的外循環流化床鍋爐燃煤新技術,它具有燃料適應性廣、燃燒效率高、高效脫硫、NOX排放低、結構簡單、操作方便等諸多優勢。
循環流化床鍋爐過熱器是該鍋爐的一個重要部件,其安全運行直接關係到鍋爐的使用壽命和生產成本,保證過熱器長期的安全運行具有十分重要的意義,在鍋爐操作過程中需要注意一下幾個方面:
1:煮爐期間必須保證中低水位,煮爐時,藥液不得進入過熱器,以免懸浮物在蛇形管中沉澱而造成堵塞。煮爐結束後,應停爐防水,徹底清理過熱器內壁的附著物和殘渣,試運行前用軟水沖洗過熱器2小時左右。
2:點火前必須打開過熱器排氣閥和疏水閥,到壓力上升時,關閉排氣閥同時打開分氣缸進氣閥和疏水閥。汽包壓力達到規定數值時,關小疏水閥直到10%左右的流量時,關閉疏水閥。
3:運行中如爐溫高時,應打開減溫水流量,此時疏水閥應關閉,應關小減溫水流量同時打開疏水閥。
4:在鍋爐運行中,如減溫水已增至最大時,過熱器蒸汽溫度還是很高,可通過以下方法降低蒸汽溫度:
(1)增加鍋爐的循環灰量,減少給煤的顆粒度。
(2)適當減少給煤量,降低爐溫。
(3)在氧氣許可的條件下,可適當減少二次風。
5:如減溫水已關閉,過熱器蒸汽溫度仍然偏低,可通過以下方法提高蒸汽溫度:
(1)放掉一些循環灰,提高爐膛的出口煙氣溫度。
(2)可適當增加二次風量。
6:時刻檢查過熱器和鍋筒的壓差,如壓差比平時突然變化,可採取如下措施:
(1)壓差增大,甚至大於10%的額定壓力,說明過熱器內部有堵塞現象,應停爐對過熱器內壁進行沖洗。
(2)壓差突然減少,應立即停爐檢查過熱器是否有爆管現象發生,如有,應更換過的熱器管子,再啟動鍋爐運行。
7:鍋爐給水對過熱器的安全運行具有十分重要的意義,鍋爐的水質應符合GB1576-2001《工業鍋爐水質》的要求。
(1)嚴格控制鍋爐鍋水的含鹽量和鹼度,測定氯鹽比。將含鹽量控制在≤3000mg/L,總鹼度≤14mg/L。
(2)PH值控制在標準要求的範圍內(10~12)。建議最好控制在10.8~11.3以內。
(3)鍋水鹼度過高會使水面泡沫層增厚,分離效果大大下降,也是造成蒸汽帶水的重要原因。同時水隨蒸汽進入過熱器,使鹽分沉積在管壁上阻礙傳熱,對鍋水相對鹼度應控制在0.2以下。
8:鍋爐運行前對鍋筒內件仔細檢查,要求鍋筒內件焊縫嚴密,無泄漏點。
9:嚴格控制燃燒高硫煤,防止過熱器出現高溫腐蝕現象。
10:定期檢查高溫過熱器的防磨,脫落的護瓦要即使焊補,磨穿的護瓦要即時更換,轉向的護瓦要即時校正。
11:鍋爐在運行過程中要加強排污操作,連續排污不能中斷,定期排污每班不能少於一次。
12:對有過熱器的鍋爐,鍋爐運行時不能長時間的低負荷運行,特別是低壓力高流量的運行,使得過熱蒸汽密度降低,流量增大,過熱器管子中的蒸汽速度大大增加,熱偏差增大,蒸汽阻力增加,傳熱惡化,傳熱量低的管子容易發生爆管現象,所以,鍋爐嚴禁長期低壓運行,建議運行壓力不低於80%的額定負荷,如確實需要低壓運行,需要對流量進行相應折算,計算出一定壓力下對應一事實上的安全流量。
安全事項
1 發生爆燃的幾種情況
鍋爐爆燃是由於爐膛內可燃物質的濃度在爆燃極限範圍內,遇到明火或溫度達到了燃點發生劇烈爆燃,燃燒產物在瞬間向周圍空間產生快速的強烈突破。以下介紹幾種循環流化床鍋爐易發生爆燃的情況。
1.1 揚火爆燃
如果壓火時燃料加得多或停的晚,使壓火後床料內燃料的含量過多,這時燃料中的碳在缺氧狀況下不充分燃燒產生大量的CO,同時燃料在爐內高溫乾熘揮發出甲烷、氫等可燃性氣體。由於壓火後床料表面溫度降低,這些可燃性氣體遇不到明火,便在鍋爐爐膛內積聚。揚火時,隨著風機的啟動,床料開始流化,高溫的床料從下面翻出,這時可燃性氣體與明火接觸,瞬間發生燃燒,如果可燃物的濃度在爆燃極限範圍內,就會發生爆燃。個別司爐工在揚火時怕床溫降得過快造成滅火,在啟風機前先加入少量的燃料,新進入爐膛的燃料不但會揮發出可燃性氣體,同時會有大量的煤粉參與燃燒,這樣不但會增大產生爆燃的機率,還會加劇爆燃的強度。
1.2 大量返料突入爆燃
循環流化床鍋爐都有物料循環系統。循環流化床鍋爐運行時,大量固體顆粒在燃燒室、分離器和返料裝置等組成的循環迴路中循環,一般循環流化床鍋爐的循環倍率為5~20,也就是說有5~20倍給煤量的返料灰需要經過返料裝置返回燃燒室再次燃燒,循環物料是直徑在0.1mm左右的細灰,有很好的流動性,在返料風的吹送下,連續不斷地進入爐膛。運行中如果返料風過小,返料器內的物料就會停止流化或流動,從而造成返料器堵塞,細灰會在返料器內堆積,當細灰積累到一定時,細灰在自身重量的作用下產生流動或者由於操作調整增大風量使物料再次流化,這時成噸的細灰在短時間內進入爐膛。由於細灰的表面積大,此時返料風與空氣快速混合充滿爐膛,且細灰中一般含有20%左右的碳,在爐內高溫環境下極易發生爆燃。
1.3 油氣爆燃
流化床鍋爐一般採用柴油點火,點火過程中因為油中的雜質、點火風的調配、油壓太低等因素常會發生油槍滅火。滅火後,如果沒及時發現、關閉油閥,被霧化的燃油會繼續噴進爐膛內,這樣從爐膛到尾部煙道甚至到煙囪出口都充滿了油霧。這時如果再次點火或遇到其它明火,就會產生整個系統的爆燃。
2000年8月19日5點14分,平煤集團公司一自備電廠的35t/h循環流化床鍋爐開始點火,油壓在1.2~1.6MPa時,兩支點火油槍霧化著燃油噴燃進入爐膛,450~500mm厚的底料開始流化預熱,5點24分,即點火10min後,發現床溫開始下降,司爐工檢查發現兩支點火槍已熄火,立即又用火把再次點火,隨後就發生了爐膛內及燃燒系統爆燃和爐門竄出火舌傷人的事故。
事後檢查發現,鍋爐保溫少部分振脫,密封與膨脹縫部分發生泄漏,由於正壓大的作用尾部煙道的麻石塊振掉,造成煙風系統短路,需進行停爐處理。
事後分析產生爆燃的原因有以下幾方面:
(1)司爐工責任心不強。點火前沒有認真試驗點火槍的霧化情況,在發生點火中斷的情況下,沒進行認真檢查處理而再次點火,是造成爐膛內超標的油煙濃度遇到明火發生爆燃事故的直接原因。
(2)點火風的調配不適與油壓太低,造成噴油中斷滅火,滅火後沒有及時發現或發現後沒有採取措施再次點火而發生爆燃的原因。
(3)油槍霧化不良,噴咀堵塞,油燃燒不充分,爐膛內有大量的油蒸汽。
所以,這次爆燃是由油槍供油中斷滅火,大量油氣充滿燃燒於煙風系統中,可燃氣體溫度達到了燃點,遇到明火發生的劇烈爆燃。
1.4 煙道內可燃物再燃
在循環流化床鍋爐運行中,有時可能發生煙道內可燃物再燃事故,這時會出現以下現象:排煙溫度急劇增加,一、二次風出口溫度也隨之升高,煙道內及燃燒室內的負壓急劇變化甚至變為正壓;煙囪內冒黑煙,從引風機殼體不嚴處向外冒煙或向外噴火星等。
出現這種問題的原因主要有:燃燒調整不當,配風不合理,導致可燃物進入煙道;爐膛負壓過大,將未燃盡的可燃物抽入煙道;返料裝置堵灰使分離器效率下降,致使未燃盡顆粒填接進入煙道。
2 鍋爐爆燃的預防
針對以上幾種常見爆燃發生的原因,循環流化床鍋爐操作中應採取下列措施防止爆燃。
(1)揚火時一定要先啟動引風機通風5min後再啟動送風機,以保證爐內積聚的可燃性氣體排出,防止遇到明火。
(2)鍋爐壓火時一定要先停止給煤。當床溫趨向穩定或稍有下降趨勢時,再停送風機,防止壓火後床料內煤量太多,產生大量可燃性氣體及乾燥的煤粉。
(3)壓火後,揚火前儘量避免有燃料進入爐內,不可在揚火時先給燃料後啟風機。
(4)當運行中發生返料堵塞存灰較多時,通過放灰系統將灰放掉。
(5)點火過程中如果發生油槍滅火,應先關閉油閥,保持風機運行通風5min後,再次點火。
(6)點火過程中,如果油槍噴咀堵塞,油槍霧化不良,導致床溫上升困難,達不到加煤溫度,應停止點火,對油槍噴咀進行清洗或更換後再點火。
(7)點火過程中,一定要控制好加煤量,一般總加煤量不能超過床料量的20%。
(8)如發現煙溫不正常升高時,應加強燃燒調整,使風煤比調整到合適的範圍內;若是由於返料裝置堵灰造成的應立即將返料裝置內的堵灰放淨;若煙道內可燃物再燃燒使排煙溫度超過300℃以上,應立即壓火處理,嚴密關閉各人行孔門和擋板,禁止通風,然後在煙道內投入滅火裝置或用蒸汽進行滅火,當排煙溫度恢復正常時可再穩定一般時間,然後再打開人行孔檢查、確認煙道內無火源並經引風機通風約15min後方可啟動鍋爐。
優點
(1)燃料適應性廣
這是循環流化床鍋爐的主要優點之一。在循環流化床鍋爐中按重量計,燃料僅占床料的1~3%,其餘是不可燃的固體顆粒,如脫硫劑、灰渣等。因此,加到床中的新鮮煤顆粒被相當於一個“大蓄熱池”的灼熱灰渣顆粒所包圍。由於床內混合劇烈,這些灼熱的灰渣顆粒實際上起到了無窮的“理想拱”的作用,把煤料加熱到著火溫度而開始燃燒。在這個加熱過程中,所吸收的熱量只占床層總熱容量的千分之幾,因而對床層溫度影響很小,而煤顆粒的燃燒,又釋放出熱量,從而能使床層保持一定的溫度水平,這也是流化床一般著火沒有困難,並且煤種適應性很廣的原因所在。
(2)燃燒效率高
循環流化床鍋爐的燃燒效率要比鼓泡流化床鍋爐高,通常在95~99%範圍內,可與煤粉鍋爐相媲美。循環流化床鍋爐燃燒效率高是因為有下述特點:氣固混合良好;燃燒速率高,其次是飛灰的再循環燃燒。
(3)高效脫硫
由於飛灰的循環燃燒過程,床料中未發生脫硫反應而被吹出燃燒室的石灰石、石灰能送回至床內再利用;另外,已發生脫硫反應部分,生成了硫酸鈣的大粒子,在循環燃燒過程中發生碰撞破裂,使新的氧化鈣粒子表面又暴露於硫化反應的氣氛中。這樣循環流化床燃燒與鼓泡流化床燃燒相比脫硫性能大大改善。當鈣硫比為1.5~2.0時,脫硫率可達85~90%。而鼓泡流化床鍋爐,脫硫效率要達到85~90% ,鈣硫比要達到3~4,鈣的消耗量大一倍。與煤粉燃燒鍋爐相比,不需採用尾部脫硫脫硝裝置,投資和運行費用都大為降低。
(4)氮氧化物(NOX)排放低
氮氧化物排放低是循環流化床鍋爐另一個非常吸引人的特點。運行經驗表明,循環流化床鍋爐的NOX排放範圍為50~150ppm或40~120mg/MJ。循環流化床鍋爐NOX排放低是由於以下兩個原因:一是低溫燃燒,此時空氣中的氮一般不會生成NOX ;二是分段燃燒,抑制燃料中的氮轉化為NOX ,並使部分已生成的NOX得到還原。
(5)燃燒強度高,爐膛截面積小
爐膛單位截面積的熱負荷高是循環流化床鍋爐的另一主要優點。其截面熱負荷約為3.5~4.5MW/m2,接近或高於煤粉爐。同樣熱負荷下鼓泡流化床鍋爐需要的爐膛截面積要比循環流化床鍋爐大2~3倍。
(6)負荷調節範圍大,負荷調節快
當負荷變化時,只需調節給煤量、空氣量和物料循環量,不 必像鼓泡流化床鍋爐那樣採用分床壓火技術。也不象煤粉鍋爐那樣,低負荷時要用油助燃,維持穩定燃燒。一般而言,循環流化床鍋爐的負荷調節比可達(3~4):1。負荷調節速率也很快,一般可達每分鐘4%。
(7)易於實現灰渣綜合利用
循環流化床燃燒過程屬於低溫燃燒,同時爐內優良的燃盡條件使得鍋爐的灰渣含炭量低(含炭量小於1%),屬於低溫燒透,易於實現灰渣的綜合利用,如作為水泥摻和料或做建築材料。同時低溫燒透也有利於灰渣中稀有金屬的提取。
(8)床內不布置埋管受熱面
循環流化床鍋爐的床內不布置埋管受熱面,因而不存在鼓泡流化床鍋爐的埋管受熱面易磨損的問題。此外,由於床內沒有埋管受熱面,啟動、停爐、結焦處理時間短,可以長時間壓火等。
(9)燃料預處理系統簡單
循環流化床鍋爐的給煤粒度一般小於13mm,因此與煤粉鍋爐相比,燃料的製備破碎系統大為簡化。
(10)給煤點少
循環流化床鍋爐的爐膛截面積小,同時良好的混合和燃燒區域的擴展使所需的給煤點數大大減少。既有利於燃燒,也簡化了給煤系統。>>攜帶型里氏硬度計的使用原理除濕機原理疏水閥的類型和工作原理無堵塞泵葉輪的結構形式及特點坩堝的用途不鏽鋼管的種類
石灰石系統
摘要
石灰石系統是CFB機組非常重要的一個輔助系統,近年來,隨著外購成品粉的成本越來越大,並且石灰石粉粒度控制越來越差,更多的電廠選擇自己製備石灰石粉,而製備系統中的細碎環節是首要關鍵的環節,因此做好細碎環節的設計,設備選型尤為重要,本篇將以白馬600MW CFB電廠細碎系統設計選型為基礎,重點論述石灰石粉製備中細碎環節的合理設計。
關鍵字
石灰石;破碎;粉磨;級配;出力
說明
發展低碳經濟已成為全球性共識,我國已把發展低碳經濟,應對氣候變化作為國家經濟社會發展的重大戰略,到2020年的行動目標,單位GDP的CO2排放強度比2005年下降40-50%。在實現這一目標的過程中,電力行業,尤其是火力發電領域承擔著及其重要的責任。
當前,我國清潔煤發電技術和裝備有了巨大的進步,大容量CFB鍋爐技術已臻於成熟,300MW等級CFB鍋爐在國內已全面普及,600MW等級機組已經開始研究並已實施。為了滿足脫硫環保的要求,CFB機組的運行石需要摻燒石灰石粉,進入膛內的石灰石粉品質,粒徑及級配,石灰石粉量等都有嚴格的要求,石灰石粉一旦達不到要求,就會影響爐內脫硫的效果,甚至影響其它系統。
目前國內CFB很多電廠石灰石粉直播系統的運行還不夠理想,其中最重要的原因之一就是粉碎設備,尤其是細碎設備的設計和選型不當,因此做好石灰石粉細碎設備系統的設計,是一項非常迫切和重要的工作。
1、粉碎的基本概念,方式和原則
1.1粉碎的基本概念
固體物料在外力作用下克服其內聚力使之破碎的過程稱為粉碎。因處理物料的尺寸大小不同,可大致分為破碎和粉磨兩個過程:使大塊物料碎裂成小塊物料的加工過程稱之為破碎;使小塊物料碎裂成細粉末狀物料的加工過程稱為粉磨。
1.2粉碎的方式
基本的粉碎方式有:擠壓粉碎,衝擊粉碎,摩擦剪下粉碎和劈裂粉碎等,如下圖:
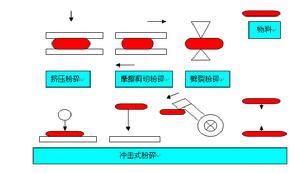
粉碎方式 | 機理 | 典型設備 |
擠壓粉碎 | 工作部件對物料施加擠壓作用,物料在壓力作用下發生粉碎。 | 顎式破碎機 |
擠壓-剪下粉碎 | 物料在擠壓和剪下兩種作用力下發生粉碎。 | 柱磨,雷蒙磨,鋼球磨,立磨,棒磨 |
劈裂粉碎 | 對物料在工作部件的劈裂作用下而粉碎 | 沖鏇破碎機 |
衝擊粉碎 | 工作部件高速運動對物料進行衝擊或者物料高速運動向固定壁衝擊而發生粉碎。 | 錘式破碎機 |
1.3粉碎的基本原則
對於物料的粉碎,經過大量理論研究和運行實踐證明,存在一個破碎和粉磨最佳經濟點即至某一粒度以上宜採用破碎,至某一粒度以下宜採用粉磨,也就是常說的分段破碎原則。破碎機運行時,破碎用的錘頭或者刀具處於高速運動狀態,通過撞擊或者切削的作用力方式,更適合將大塊的原料破碎成為較粗的物料;磨機運行時,速度相對慢得多,通過較為笨重的碾輥等大質量金屬件碾磨擠壓物料,更適合將小塊物料進一步粉碎,有利於製備系統的節能,提高經濟性。部分學者通過研究得出自己的研究結果:①諾爾斯及法欒特從碎礦和磨礦能耗降低的角度出發,用邦德公式計算結果作圖,得出碎至12.7mm交給磨礦時能耗最低。②前蘇聯研究者從碎磨成本最低的角度出發測算出大型選廠碎礦最終粒度4-8mm最好,小型選廠最終10-15mm.。
綜合下來,目前國內物料粉碎基本可按以下粒度選擇粉碎設備型式:

2、CFB機組石灰石粉出力及粒度級配的需求
2.1石灰石粉耗量要求
CFB機組的石灰石耗量主要與以下3個因素有關:①煤質中的含硫量,②機組的容量,③煙氣排放標準。我國的煤質硫分偏高,單位發熱量低,隨著煙氣排放標準越來越高,所需石灰石耗量也越來越大。
2.2粒度,級配要求
CFB機組對石灰石粒度,級配有著嚴格的要求。摻燒的石灰石粉偏粗時,石灰石粉在爐膛內反應的表面積不足,會導致脫硫效率偏低;摻燒的石灰石粉偏細時,石灰石粉會因為在膛內停留的時間過短,也會導致脫硫效率偏低。目前階段CFB機組要求石灰石成品粉粒徑小於等於1mm,下圖是某工程爐內要求的石灰石粉粒度級配曲線::

3、石灰石粉碎設備的選擇
電廠購買的石灰石原料,往往都是礦山初步破碎後的石灰石原料,電廠石灰石製備系統設計時,可根據原料進廠粒度,按照分段破碎的原則,選擇採用破碎+磨製或者直接採用磨製的方式。
3.1石灰石的粗碎
石灰石原料進廠粒度一般在100mm左右,經過粗碎機破碎後粒度要求在30mm以下,相對容易實現,一般採用國產破碎機即可。
3.2石灰石的細碎
根據CFB鍋爐廠要求,石灰石成品粉粒徑小於等於1mm,宜採用粉磨方式製備,也有個別廠家採用進口破碎機。
以下是國內電廠常用的粉磨設備:
序號 | 磨機種類 | 出料粒徑範圍 | 備註 |
1 | 鋼球磨 | ≤0.075mm | 偏小 |
2 | 棒磨 | 0~4mm | |
3 | 雷蒙磨 | 0.15~0.01mm | 偏小 |
4 | 深湘柱磨機 | 0~2mm | |
5 | 沖鏇式破碎機 | 0~2mm | |
6 | 齒輥式破碎機 | 0~5mm | 美國鋼萊克 |
7 | 錘式破碎機 | 0~5mm | 德國奧貝瑪 |
CFB機組要求石灰石粒徑在0—1mm這個區間,這個區間的粒度和粒度分布要求實際是難以達到的。
國外絕大多數破碎機公司包括美國鋼萊克機械製造有限公司、德國的FAM、美國賓夕法尼亞州破碎機公司、美國破碎機公司、德國奧貝瑪破碎技術有限公司等,現在一般都不做這種粒度的破碎,國內用過破碎機的經驗告訴我們,實際上運行效果也很難以保證成品粉的粒徑要求,如安徽淮北臨煥電廠等,採用美國鋼萊克破碎機,設計要求1mm,但實際運行平均粒徑是3mm,最大粒徑5mm;德國奧貝瑪公司採用破碎機加機械篩分的閉式系統,後面介紹對比情況。
鋼球磨是制粉系統常用的設備之一,可靠性較高,出力大。但是它的出料粒徑偏細,控制手段少,不能滿足設計要求,另外他耗電量較大,噪音大、粉塵污染較大,設備價格也較高。
雷蒙磨達不到這個級配要求,另外出力也較小,不適宜用於大型CFB機組石灰石粉製備。
棒磨機磨石灰石粉通常是在傳統的棒磨機的基礎上增加了選粉系統。由於製造等方面的原因,其篩板的製造還達不到原設計要求,帶來的問題是出力下降,可靠性降低。同時,他的出力也較小(20t/h),耗電量較大,噪音大、粉塵污染也比較大、設備價格較高。
沖鏇式破碎機是國內近幾年來開發的一種新型破碎機,但雖然它具有破碎性能好、體積小、電耗低等特點,但沖鏇式破碎機刀片磨損很快,使用壽命大約500h,更換頻率高,維護量大,另外出力也較小(20t/h),不能滿足設計要求。
柱磨機是近年來在石灰石粉破碎上普遍採取的一種磨機,採用反覆滾壓原理生產石灰石粉,具有產量高、噪音小、磨損小、耗電量低、控制調節手段較多等優點,尤其是易損件輥輪由耐磨合金鑄鐵經過特殊熱處理生產的,其使用壽命時間長,襯板為2年,輥輪3年。另外可以調節轉速、碾輥與襯板的間隙、下料筒高度等方式來控制出料的粒徑,技術性能指標(加上後續閉式系統)是目前各種細碎設備里最接近設計要求的(後面介紹測試數據)。
綜合對比下來,柱磨機占有明顯的優勢,推薦採用柱磨機。

3.3錘式破碎機和柱磨機系統的試驗測試
為切實做好石灰石粉碎設備的選型工作,我們對全國範圍內採用石灰石粉製備電廠進行了廣泛的調研,在此基礎上對四川白馬300CFBMW電廠和雲南巡檢司電廠的石灰石粉製備系統開展了重點調研、測試試驗和分析工作。白馬電廠300MW CFB機組石灰石製備採用的是兩級破碎機+機械篩分系統的閉式系統,二級破碎機德國奧貝瑪錘擊式破碎機;雲南巡檢司電廠2*300MW CFB機組石灰石粉製備採用的是一級破碎機+柱磨機+氣力風選系統的閉式系統。經測試國網白馬電廠石灰石製備,設計出力65t/h,實際出力30t/h;華電雲南巡檢司電廠石灰石製備,設計出力50t/h,實際出力50t/h.
根據試驗測試的結果,柱磨機系統在出力和級配方面數據明顯優於錘擊式破碎機系統,更能滿足大型CFB機組的要求。
3.4白馬電廠石灰石粉製備系統的套用
白馬600MW CFB工程為1*600機組,石灰石粉耗量為85.94t/h,石灰石入廠粒徑《=30mm,要求成品粉粒徑《=1mm。安工程需要,設定3套50t/h製備系統。設計時,按兩級破碎機和柱磨機兩個方案擬定,兩種方案經濟比較如下:
項目 | 兩級破碎(二級採用進口設備) | 柱磨機 | 備註 |
初投資 | 3*400萬 | 3*218 | |
運行費 | 3*91.7 | 3*69.5 | |
維護費 | 3*135 | 3*40 |
經濟性上來看,柱磨機占有明顯的優勢。
白馬電廠最終採用柱磨機方案。
結論
綜上所述,CFB機組石灰石粉碎系統設計和設備的選擇推薦原則如下:
1, 應遵循分級粉碎原則,粗碎採用破碎機,細碎採用柱磨機。
2, 當石灰石來料粒度《=30mm時,可直接採用磨機。
3, 石灰石粉的細碎設備推薦採用柱磨機。
參考文獻
[3]陳建斌,羅明鑫。石灰石製備系統收資報告,2006,11.
[4] 楊愛麗,胡學武。循環流化床鍋爐島石灰石制粉系統的設備配置及設計最佳化,2003,10.
參考設備
[1]長沙深湘通用機器有限公司
作者簡介:
易禮容(1968.3-),男,最高學曆本科,高級工程師,從事於電力行業除灰渣系統技術研究、設計工作。
王仕能(1979.1-),男,最高學曆本科,工程師,從事於電力行業除灰渣系統技術研究、設計工作。
許華(1962.12-),男,最高學曆本科,教授級高級工程師,從事於電力行業除灰渣系統技術研究、設計工作