簡介
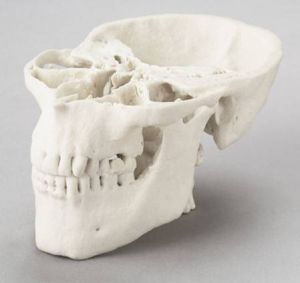
特點
RP技術將一個實體的複雜的三維加工離散成一系列層片的加工,大大降低了加工難度,具有如下特點:⑴成型全過程的快速性,適合現代激烈的產品市場;
⑵可以製造任意複雜形狀的三維實體;
⑶用CAD模型直接驅動,實現設計與製造高度一體化,其直觀性和易改性為產品的完美設計提供了優良的設計環境;
⑷成型過程無需專用夾具、模具、刀具,既節省了費用,又縮短了製作周期。
⑸技術的高度集成性,既是現代科學技術發展的必然產物,也是對它們的綜合套用,帶有鮮明的高新技術特徵。
以上特點決定了RP技術主要適合於新產品開發,快速單件及小批量零件製造,複雜形狀零件的製造,模具與模型設計與製造,也適合於難加工材料的製造,外形設計檢查,裝配檢驗和快速反求工程等。
形成過程
形象地比喻:快速成形系統相當於一台"立體印表機"。
它可以在沒有任何刀具、模具及工裝卡具的情況下,快速直接地實現零件的單件生產。根據零件的複雜程度,這個過程一般需要1~7天的時間。換句話說,RP技術是一項快速直接地製造單件零件的技術。
工作原理
RP系統可以根據零件的形狀,每次製做一個具有一定微小厚度和特定形狀的截面,然後再把它們逐層粘結起來,就得到了所需製造的立體的零件。當然,整個過程是在計算機的控制下,由快速成形系統自動完成的。不同公司製造的RP系統所用的成形材料不同,系統的工作原理也有所不同,但其基本原理都是一樣的,那就是"分層製造、逐層疊加"。這種工藝可以形象地叫做"增長法"或"加法"。
每個截面數據相當於醫學上的一張CT像片;整個製造過程可以比喻為一個"積分"的過程。
RP技術的基本原理是:將計算機內的三維數據模型進行分層切片得到各層截面的輪廓數據,計算機據此信息控制雷射器(或噴嘴)有選擇性地燒結一層接一層的粉末材料(或固化一層又一層的液態光敏樹脂,或切割一層又一層的片狀材料,或噴射一層又一層的熱熔材料或粘合劑)形成一系列具有一個微小厚度的的片狀實體,再採用熔結、聚合、粘結等手段使其逐層堆積成一體,便可以製造出所設計的新產品樣件、模型或模具。自美國3D公司1988年推出第一台商品SLA快速成形機以來,已經有十幾種不同的成形系統,其中比較成熟的有UV、SLA、SLS、LOM和FDM等方法。其成形原理分別介紹如下:
SLA原理
"StereolithographyAppearance"的縮寫,即立體光固化成型法.
用特定波長與強度的雷射聚焦到光固化材料表面,使之由點到線,由線到面順序凝固,完成一個層面的繪圖作業,然後升降台在垂直方向移動一個層片的高度,再固化另一個層面.這樣層層疊加構成一個三維實體.
SLA是最早實用化的快速成形技術,採用液態光敏樹脂原料,工藝原理如圖所示。其工藝過程是,首先通過CAD設計出三維實體模型,利用離散程式將模型進行切片處理,設計掃描路徑,產生的數據將精確控制雷射掃描器和升降台的運動;雷射光束通過數控裝置控制的掃描器,按設計的掃描路徑照射到液態光敏樹脂表面,使表面特定區域內的一層樹脂固化後,當一層加工完畢後,就生成零件的一個截面;然後升降台下降一定距離,固化層上覆蓋另一層液態樹脂,再進行第二層掃描,第二固化層牢固地粘結在前一固化層上,這樣一層層疊加而成三維工件原型。將原型從樹脂中取出後,進行最終固化,再經打光、電鍍、噴漆或著色處理即得到要求的產品。
SLA技術主要用於製造多種模具、模型等;還可以在原料中通過加入其它成分,用SLA原型模代替熔模精密鑄造中的蠟模。SLA技術成形速度較快,精度較高,但由於樹脂固化過程中產生收縮,不可避免地會產生應力或引起形變。因此開發收縮小、固化快、強度高的光敏材料是其發展趨勢。
3DSystems推出的ViperProSLAsystem
⒈光固化成型法是最早出現的快速原型製造工藝,成熟度高,經過時間的檢驗.
⒉由CAD數字模型直接製成原型,加工速度快,產品生產周期短,無需切削工具與模具.
⒊可以加工結構外形複雜或使用傳統手段難於成型的原型和模具.
⒋使CAD數字模型直觀化,降低錯誤修復的成本.
⒌為實驗提供試樣,可以對計算機仿真計算的結果進行驗證與校核.
⒍可在線上操作,可遠程控制,利於生產的自動化.
SLA的缺憾
⒈SLA系統造價高昂,使用和維護成本過高.
⒉SLA系統是要對液體進行操作的精密設備,對工作環境要求苛刻.
⒊成型件多為樹脂類,強度,剛度,耐熱性有限,不利於長時間保存.
⒋預處理軟體與驅動軟體運算量大,與加工效果關聯性太高.
⒌軟體系統操作複雜,入門困難;使用的檔案格式不為廣大設計人員熟悉.
⒍立體光固化成型技術被單一公司所壟斷.
SLA的發展趨勢與前景
立體光固化成型法的的發展趨勢是高速化,節能環保與微型化.
不斷提高的加工精度使之有最先可能在生物,醫藥,微電子等領域大有作為.
SLS原理
選擇性雷射燒結(以下簡稱SLS)技術最初是由美國德克薩斯大學奧斯汀分校的Carlckard於1989年在其碩士論文中提出的。後美國DTM公司於1992年推出了該工藝的商業化生產設備SinterSation。幾十年來,奧斯汀分校和DTM公司在SLS領域做了大量的研究工作,在設備研製和工藝、材料開發上取得了豐碩成果。德國的EOS公司在這一領域也做了很多研究工作,並開發了相應的系列成型設備。
國內也有多家單位進行SLS的相關研究工作,如西安交通大學機械學院,快速成型國家工程研究中心,教育部快速成型工程研究中心,華中科技大學、南京航空航天大學、西北工業大學、中北大學和北京隆源自動成型有限公司等,也取得了許多重大成果,如南京航空航天大學研製的RAP-I型雷射燒結快速成型系統、北京隆源自動成型有限公司開發的AFS一300雷射快速成型的商品化設備。
選擇性雷射燒結是採用雷射有選擇地分層燒結固體粉末,並使燒結成型的固化層層層疊加生成所需形狀的零件。其整個工藝過程包括CAD模型的建立及數據處理、鋪粉、燒結以及後處理等。SLS技術的快速成型系統工作原理見圖1。
整個工藝裝置由粉末缸和成型缸組成,工作時粉末缸活塞(送粉活塞)上升,由鋪粉輥將粉末在成型缸活塞(工作活塞)上均勻鋪上一層,計算機根據原型的切片模型控制雷射束的二維掃描軌跡,有選擇地燒結固體粉末材料以形成零件的一個層面。粉末完成一層後,工作活塞下降一個層厚,鋪粉系統鋪上新粉.控制雷射束再掃描燒結新層。如此循環往復,層層疊加,直到三維零件成型。最後,將未燒結的粉末回收到粉末缸中,並取出成型件。對於金屬粉末雷射燒結,在燒結之前,整個工作檯被加熱至一定溫度,可減少成型中的熱變形,並利於層與層之間的結合。
與其它快速成型(RP)方法相比,SLS最突出的優點在於它所使用的成型材料十分廣泛。從理論上說,任何加熱後能夠形成原子間粘結的粉末材料都可以作為SLS的成型材料。可成功進行SLS成型加工的材料有石蠟、高分子、金屬、陶瓷粉末和它們的複合粉末材料。由於SLS成型材料品種多、用料節省、成型件性能分布廣泛、適合多種用途以及SLS無需設計和製造複雜的支撐系統,所以SLS的套用越來越廣泛。
SLS技術的金屬粉末燒結方法
3.1金屬粉末和粘結劑混合燒結
首先將金屬粉末和某種粘結劑按一定比例混合均勻,用雷射束對混合粉末進行選擇性掃描,雷射的作用使混合粉末中的粘結劑熔化並將金屬粉末粘結在一起,形成金屬零件的坯體。再將金屬零件坯體進行適當的後處理,如進行二次燒結來進一步提高金屬零件的強度和其它力學性能。這種工藝方法較為成熟,已經能夠製造出金屬零件,並在實際中得到使用。南京航空航天大學用金屬粉末作基體材料(鐵粉),加人適量的枯結劑,燒結成形得到原型件,然後進行後續處理,包括燒失粘結劑、高溫焙燒、金屬熔滲(如滲銅)等工序,最終製造出電火花加工電極。並用此電極在電火花工具機上加工出三維模具型腔。
3.2金屬粉末雷射燒結
雷射直接燒結金屬粉末製造零件工藝還不十分成熟,研究較多的是兩種金屬粉末混合燒結,其中一種熔點較低,另一種較高。雷射燒結將低熔點的粉末熔化,熔化的金屬將高熔點金屬粉末粘結在一起。由於燒結好的零件強度較低,需要經過後處理才能達到較高的強度。美國Texas大學Austin分校進行了沒有聚合物粘結劑的金屬粉末如CuSnNiSn青銅鎳粉複合粉末的SLS成形研究,並成功地製造出金屬零件。他們對單一金屬粉末雷射燒結成形進行了研究,成功地製造了用於F1戰鬥機和AIM9飛彈的工NCONEL625超合金和Ti6A14合金的金屬零件。美國航空材料公司已成功研究開發了先進的欽合金構件的雷射快速成形技術。中國科學院金屬所和西安交通大學等單位正致力於高熔點金屬的雷射快速成形研究,南京航空航天大學也在這方面進行了研究,用Ni基合金混銅粉進行燒結成形的試驗,成功地製造出具有較大角度的倒錐形狀的金屬零件(見圖4)。
3.3金屬粉末壓坯燒結
金屬粉末壓坯燒結是將高低熔點的兩種金屬粉末預壓成薄片坯料,用適當的工藝參數進行雷射燒結,低熔點的金屬熔化,流人到高熔點的顆粒孔隙之間,使得高熔點的粉末顆粒重新排列,得到緻密度很高的試樣。吉林大學郭作興等用此方法對FeCu,FeC等合金進行試驗研究,發現壓坯雷射燒結具有與常規燒結完全不同的緻密化現象,雷射燒結後的組織隨冷卻方式而異,空冷得到細珠光體,淬火後得到馬氏體和粒狀。
4SLS技術金屬粉末成型存在的問題
SLS技術是非常年輕的一個製造領域,在許多方面還不夠完善,如製造的三維零件普遍存在強度不高、精度較低及表面質量較差等問題。SLS工藝過程中涉及到很多參數(如材料的物理與化學性質、雷射參數和燒結工藝參數等),這些參數影響著燒結過程、成型精度和質量。零件在成型過程中,由於各種材料因素、工藝因素等的影響,會使燒結件產生各種冶金缺陷(如裂紋、變形、氣孔、組織不均勻等)。
4.1粉末材料的影響
粉末材料的物理特性,如粉末粒度、密度、熱膨脹係數以及流動性等對零件中缺陷形成具有重要的影響。粉末粒度和密度不僅影響成型件中缺陷的形成,還對成型件的精度和粗糙度有著顯著的影響。粉末的膨脹和凝固機制對燒結過程的影響可導致成型件孔隙增加和抗拉強度降低。
4.2工藝參數的影響
雷射和燒結工藝參數,如雷射功率、掃描速度和方向及間距、燒結溫度、燒結時間以及層厚度等對層與層之間的粘接、燒結體的收縮變形、翹曲變形甚至開裂都會產生影響。上述各種參數在成型過程中往往是相互影響的,如YongAkSong等研究表明降低掃描速度和掃描間距或增大雷射功率可減小表面粗糙度,但掃描間距的減小會導致翹曲趨向增大。
因此,在進行最最佳化設計時就需要從總體上考慮各參數的最佳化,以得到對成型件質量的改善最為有效的參數組。製造出來的零件普遍存在著緻密度、強度及精度較低、機械性能和熱學性能不能滿足使用要求等一些問題。這些成型件不能作為功能性零件直接使用,需要進行後處理(如熱等靜壓HIP、液相燒結LPS、高溫燒結及熔浸)後才能投人實際使用。此外,還需注意的是,由於金屬粉末的SLS溫度較高,為了防止金屬粉末氧化,燒結時必須將金屬粉末封閉在充有保護氣體的容器中。
5總結與展望
快速成型技術中,金屬粉末SLS技術是人們研究的一個熱點。實現使用高熔點金屬直接燒結成型零件,對用傳統切削加工方法難以製造出高強度零件,對快速成型技術更廣泛的套用具有特別重要的意義。展望未來,SLS形技術在金屬材料領域中研究方向應該是單元體系金屬零件燒結成型,多元合金材料零件的燒結成型,先進金屬材料如金屬納米材料,非晶態金屬合金等的雷射燒結成型等,尤其適合於硬質合金材料微型元件的成型。此外,根據零件的具體功能及經濟要求來燒結形成具有功能梯度和結構梯度的零件。我們相信,隨著人們對雷射燒結金屬粉末成型機理的掌握,對各種金屬材料最佳燒結參數的獲得,以及專用的快速成型材料的出現,SLS技術的研究和引用必將進入一個新的境界。
LOM原理
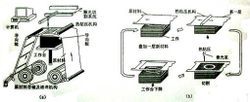
成形材料:塗敷有熱敏膠的纖維紙;
製件性能:相當於高級木材;
主要用途:快速製造新產品樣件、模型或鑄造用木模。
FDM原理
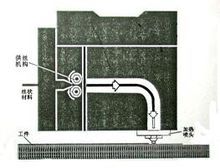
成形材料:固體絲狀工程塑膠;
製件性能:相當於工程塑膠或蠟模;
主要用途:塑膠件、鑄造用蠟模、樣件或模型。
特點:1、優點:(1)操作環境乾淨,安全,在辦公室課進行;(2)工藝乾淨、簡單、易於操作且不產生垃圾;(3)尺寸精度高,表面質量好,易於裝配,可快速構建瓶狀或中空零件;(4)原材料以捲軸絲的形式提供,易於搬運和金額快速更換;(5)原料價格便宜;(6)材料利用率高;(7)可選用的材料較多,如染色的ABS和醫用ABD、PC、PPSF、人造橡膠、鑄造用蠟。
2、缺點:(1)精度較低,難以構建結構複雜的零件;(2)與截面垂直方向的強度小;(3)成型速度相對較慢,不適合構建大型零。
意義方向
意義
大大縮短新產品研製周期,確保新產品上市時間;
------使模型或模具的製造時間縮短數倍甚至數十倍;
提高了製造複雜零件的能力;
------使複雜模型的直接製造成為可能;
顯著提高新產品投產的一次成功率;
------可以及時發現產品設計的錯誤,做到早找錯、早更改,避免更改後續工序所造成的大量損失;
支持同步(並行)工程的實施;
------使設計、交流和評估更加形象化,使新產品設計、樣品製造、市場定貨、生產準備、等工作能並行進行;
支持技術創新、改進產品外觀設計;
------有利於最佳化產品設計,這對工業外觀設計尤為重要。
成倍降低新產品研發成本;
------節省了大量的開模費用
快速模具製造可迅速實現單件及小批量生產。使新產品上市時間大大提前,迅速占領市場。
總而言之,RP技術是九十年代世界先進制造技術和新產品研發手段。在工業已開發國家,企業在新產品研發過程中採用RP技術確保研發周期、提高設計質量已成為一項重要的策略。當前,市場競爭愈演愈烈,產品更新換代加速。要保持我市產品在國內外市場的競爭力,迫切需要在加大新產品開發投入力度、增強創新意識的同時,積極採用先進的創新手段。RP技術在不需要任何刀具、模具及工裝卡具的情況下,可實現任意複雜形狀的新產品樣件的快速製造。用RP技術快速製造出的的模型或樣件可直接用於新產品設計驗證、功能驗證、外觀驗證、工程分析、市場訂貨等,非常有利於最佳化產品設計,從而大大提高新產品開發的一次成功率,提高產品的市場競爭力,縮短研發周期,降低研發成本。快速原型製造技術生產力促進中心的成立為本市企業套用RP技術開展產品創新活動提供了很好的前提條件。
發展方向
RP技術已經在許多領域裡得到了套用,其套用範圍主要在設計檢驗、市場預測、工程測試(應力分析、風道等)、裝配測試、模具製造、醫學、美學等方面。RP技術在製造工業中套用最多(達到67%),說明RP技術對改善產品的設計和製造水平具有巨大的作用。
快速成形技術還存在許多不足,下一步研究開發工作主要在以下幾方面:
⑴改善快速成形系統的可靠性、生產率和製作大件能力,尤其是提高快速成形系統的製作精度;
⑵開發經濟型的快速成形系統;
⑶快速成形方法和工藝的改進和創新;
⑷快速模具製造的套用;
⑸開發性能良好的快速成形材料;
⑹開發快速成形的高性能軟體等。
技術特點
1製造快速
RP技術是並行工程中進行複雜原型或者零件製造的有效手段,能使產品設計和模具生產同步進行,從而提高企業研發效率,縮短產品設計周期,極大的降低了新品開發的成本及風險,對於外形尺寸較小,異形的產品尤其適用。
2CAD/CAM技術的集成
設計製造一體化一直來說是一個難點,計算機輔助工藝(CAPP)在現階段由於還無法與CAD、CAM完全的無縫對接,這也是制約製造業信息化一直以來的難點之一,而快速成型技術集成CAD、CAM、雷射技術、數控技術、化工、材料工程等多項技術,使得設計製造一體化的概念完美實現。
3完全再現三維數據
經過快速成型製造完成的零部件,完全真實的再現三維造型,無論外表面的異形曲面還是內腔的異形孔,都可以真實準確的完成造型,基本上不再需要再藉助外部設備進行修復。
4成型材料種類繁多
各類RP設備上所使用的材料種類有很多,樹脂、尼龍、塑膠、石蠟、紙以及金屬或陶瓷的粉末,基本上滿足了絕大多數產品對材料的機械性能需求。
5創造顯著的經濟效益
與傳統機械加工方式比較,開發成本上節約10倍以上,同樣,快速成型技術縮短了企業的產品開發周期,使的在新品開發過程中出現反覆修改設計方案的問題大大減少,也基本上消除了修改模具的問題,創造的經濟效益是顯而易見的。
6套用行業領域廣
RP技術經過這些年的發展,技術上已基本上形成了一套體系,同樣,可套用的行業也逐漸擴大,從產品設計到模具設計與製造,材料工程、醫學研究、文化藝術、建築工程等等都逐漸的使用RP技術,使得RP技術有著廣闊的前景。
市場前景
發展動力
在現代化工業生產中,60%~90%的工業產品需要使用模具加工,模具工業已經成為製造業中的一項基礎工業,是技術成果轉化的手段,同時又是高新技術產業的重要領域,在歐美等工業已開發國家被成為“點鐵成金”的“磁力工業”。可見,模具工業在世界各國經濟發展中具有重要的顯著地位。
西安交通大學機械學院,快速製造國家工程研究中心,教育部快速製造工程研究中心,總結當前製造業呈現如下發展趨勢:
1、生產、經營及市場全球化;
2、用戶需求個性化、多樣化;
3、產品生命周期短,更新換代加速;
4、產品技術高科技化;
5、市場競爭激烈化。
數據統計
據統計,我國新產品的平均開發周期為18個月,產品的生命周期為10.5年。而美國1990年已實現“3個3”,即產品的生命周期為3年,產品的試製周期為3個月,產品的設計周期為3周。因此,製造企業要想在21世紀求得生存和發展,就必須面對這一新的形勢,不斷研究或引進新的技術。
過去,傳統的零件成型方法是採用多種機械加工工具機,以及刀具和模具,還要有高水平的技工,成本高,製造周期往往長達幾星期,甚至幾個月,不能適應新產品的更新。為克服上述問題,近幾年來開發成功了快速成型製造技術和相應的快速成型機。它是利用雷射等物理方法,向用戶提供物理模型和快速修改設計方案,從而大大減少了新產品開發前期的時間和費用。快速成型技術廣泛套用於航空航天、汽車、電子、通訊、醫療、建築、家電、玩具、家具、日用五金及工藝品製作等眾多領域。
快速成型技術使之在以下四方面受益:
設計者
在設計產品時,通常分為概念設計及詳細設計。由於設計者的能力有限,不可能在短時間內,僅憑圖紙上的思維,就把結構、形狀及尺寸等問題考慮得很周全並使結果最佳化,不但費時費力,往往難免有所疏漏,從而造成返工。為解決上述問題,在現代製造技術領域中,提出了並行工程的方法,它以小組協同工作為基礎,通過網路共享數據等信息資源,來同步考慮產品設計、製造的有關技術問題,從而實現並行設計的思想。然而,僅僅依靠計算機及數字模擬,沒有必要的物理模擬手段,也難於完美地進行並行設計。快速模型採用快速成型技術之後,設計者在設計的最初階段,就能拿到實在的產品樣品,並可在不同階段快速地修改、重做樣品,甚至做出試製用工模具及少量的產品,據此判斷有關的各種問題。這給設計者創造了一個優良的設計環境,無需多次反覆思考、修改,即可儘快得到最佳化結果。因此,快速成型技術是真正實現並行設計的強有力手段。
製造者
製造者在產品設計的最初階段,也能拿到實在的產品樣品、甚至試製用的工模具及少量產品,這使得他們能及早地對產品設計提出意見,做好原材料、標準件、外協加工件、加工工藝和批量生產用工模具等準備,最大限度地減少失誤和返工,大大節省工時、降低加工成本和提高產品質量。
推銷者
推銷者在產品設計的最初階段,也可拿到產品樣品、甚至少量產品,這使得他們能據此及早、實在地向用戶宣傳,徵求意見,並進行比較準確的市場需求預測,而不是僅憑抽象的產品描述或一張圖紙、一份樣本來推銷。所以,快速成型技術的套用可以顯著地降低新產品的銷售風險和成本,大大縮短其投放市場的時間和提高競爭能力。
用戶
用戶在產品設計的最初階段,也能見到產品樣品,甚至少量產品,這使得他們及早、深刻地認識產品,進行必要的測試,並且提出有關的意見,從而可以在儘可能短的時間內,以合理的價格得到性能最符合要求的產品。
綜上所述,快速成型技術必將能承擔起21世紀製造業持續高速發展的重任,為現代製造業提供源源不斷的超動力。