一. 概述
鍋爐性能最佳化系統,是基於現代控制理論的過程最佳化軟體系統, 結合國內發電設備情況和客觀條件,進行適應
公司專業技術人員前期對國內河北、山東、山西、貴州、江西、河南、廣西、雲南、寧夏等地的火電廠進行了設備運行狀況和存在問題專項調研,並現場採集了大量運行數據和相關資料。調研情況表明,目前國內火電廠鍋爐不同程度的存在下列問題:
1. 鍋爐熱效率和供電煤耗方面的問題;
2. 煤質變化造成燃燒不穩定,滅火問題;
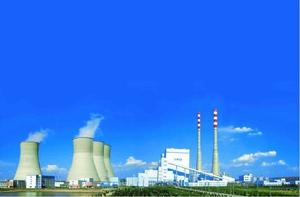
4. 受熱面表面腐蝕低溫、高溫和刷蝕磨損問題(水冷壁、過熱器、省煤器);
5. 氮氧化物排放超標問題;
6. 飛灰可燃物和大渣可燃物量偏高問題;
7. 過氧量偏高;
8. 過熱器、再熱器超溫問題;
9. 吹灰程式、次數和合理性問題;
10.省煤器等設備的磨損問題;
11.維修費用和生產成本偏高
以上問題不同程度的影響設備運行的安全性、經濟性和可靠性指標。因此,當前火電廠需要解決的問題是鍋爐整體性能的最佳化,而不僅僅是燃燒最佳化或耗差分析.我們的技術專家在現場實地考察和採集運行和維修相關數據後,與電廠專業技術人員系統的全面的分析設備問題的關鍵,全面了解用戶的需求,為用戶提供量化各項技術指標的鍋爐性能最佳化技術方案。在技術方案中將針對上述問題提出解決辦法和並預測可能的最佳化空間。
根據市場情況調研和現場得到的數據,目前國內外從事燃燒最佳化和鍋爐改造的知名廠家所做的各種類型最佳化和改造,供電煤耗最佳化效果平均為2克左右,最多達到原鍋爐設計水準。鍋爐性能最佳化系統採用的創新理念,充分挖掘系統冗餘空間,最佳化效果可以突破設計限制。套用鍋爐性能最佳化軟體的某用戶,在降低排煙熱損失和降低過熱器壁溫的情況下,同時降低了飛灰可燃物、鍋爐輔機廠用電,最佳化結果超乎一般常規的想像。
鍋爐性能最佳化軟體的套用不但給用戶帶來直接的經濟效益,而且引進了新的系統理念和分析技術.幫助我們突破傳統的運行模式,規範操作,全面提升運行管理水平的目的和更好的經濟效益。
二. 鍋爐性能最佳化系統原理和套用介紹
2.1. 引進鍋爐性能最佳化系統必要性分析
鍋爐燃燒過程是一個複雜的物理、化學過程,牽涉到的輸入和輸出變數多達160多個。依靠專業技術人員的經驗和傳統熱力學的計算分析方法,僅能對單個輸入變數和在有限範圍內解決個別輸出目標值的問題。隨著計算機技術和套用數學方法進入工業領域,使得解決比較棘手的多輸入和多輸出變數之間關係的難題變得容易了許多。隨著技術進步,進年來不斷推出的現代化的儀表和監測技術手段,可以彌補鍋爐原設計高溫區域測量監控信息不足的缺陷.為整個鍋爐系統的過程最佳化控制提供了更多的運行狀態信息,為控制邏輯增加了重要的控制點和調控依據. 鍋爐運行的多目標參數間存在著諸多矛盾,譬如燃燒效率與氮氧化物排放;低氧燃燒與還原性氣體腐蝕等等.需要用系統的觀念,全面考慮和協調多目標之間的關係,藉助先進的數學和計算機手段.利用人工智慧神經網路解決了多變數非線性關係的問題,開闢解決鍋爐最佳化控制的新途徑。鍋爐系統的各種儀表數據,可以提供反映運行狀況的信息。鍋爐專家在對系統深刻理解的基礎上,把各種運行數據信息與鍋爐的經濟、安全和可靠等性能指標之間的關係量化。利用統計學非線性回歸和人工智慧神經網路技術,可以將運行參數與鍋爐性能指標之間關係用數學模型的方式表達出來。在此基礎上,可以實現系統各部分之間和運行參數間的協調,達到綜合指標全面改善的目的。從而使鍋爐系統在節能和降低污染物排放的控制方面,能夠比傳統熱力試驗(如耗差分析)的方法和依靠運行人員的經驗做的更好。
鍋爐運行目前採用的熱工控制系統(DCS),建立在分散控制,分散風險的基礎上.控制功能只有燃燒控制、給水控制等有限的幾個分散控制單元。例如某一個輸出目標參數的控制,該控制單元最多只能同時輸入三個相關變數,無法顧及對其有影響的眾多輸入參數;對於多目標和多變數的問題,由於DCS系統沒有鍋爐系統整體控制的中樞和集中控制能力,不能解決多變數之間的相關關係的協調問題,鍋爐系統的運行無法達到整體協調控制.實際上DCS只能保證鍋爐系統的穩定運行,無法改善鍋爐系統的運行水平和技術指標。鍋爐性能最佳化系統具有全面協調系統的功能,可以直接給出最佳化運行方案或直接參與運行最佳化控制,彌補了DCS系統的不足.
鍋爐性能最佳化系統的人工神經網路模組具有很強的適應複雜環境和多目標控制要求的能力,人工智慧神經網路通過線上實時輸入的入爐煤參數等大量現場儀表數據,不斷進行學習和訓練,對最佳化運行模型進行調整,實現對被控系統變化因素(如煤質變化;爐膛漏風變化等等)的自適應,使鍋爐系統趨於最佳的運行狀態。
鍋爐性能最佳化系統的人工智慧神經網路的功能特性,解決了多變數非線性關係的技術難題,通過有效數據的訓練,可以建立鍋爐最佳化運行數學模型;通過軟體的計算,得到滿足不同需求條件下的最佳運行參數組合。
2.2. 鍋爐性能最佳化系統概述
鍋爐性能最佳化是基於人工神經網路技術和專家系統,增加了鍋爐運行關鍵中間參數爐膛出口煙溫線上監測系統,通過試驗設計和專家系統創造數據,得到鍋爐系統各部分能量的交換信息,全面分析並調整鍋爐系統的可調參數,改善並協調各部分的能量交換,達到最佳運行參數組合方式.鍋爐系統燃燒產生的熱能按照性能最佳化的需求進行交換,將能量損失最小化,達到多目標全面最佳化的目的,實現線上開環指導鍋爐最佳化運行或閉環控制鍋爐最佳化運行。
鍋爐性能最佳化系統是國外先進的最佳化軟體融合國內最佳化特點研製開發的鍋爐性能最佳化系統軟體,基於先進的人工神經網路技術,引入國外成功的最佳化經驗,建立包含鍋爐多目標快速收斂的數學模型,為鍋爐運行人員提供一個涵蓋提升最佳化性能、補強薄弱環節和指導操作控制的分析平台。
鍋爐性能最佳化系統以鍋爐專家豐富的專業經驗和系統觀念為基礎,並針對鍋爐的具體特點進行多目標最佳化設計。利用計算機技術和最佳化控制邏輯,解決多輸入變數和多目標之間協調的難題;用科學的方法解決了傳統的認識誤區,突破了傳統運行模式。
鍋爐性能最佳化系統技術方案突破了當前常見最佳化方案的傳統理念和方法,立足於全面最佳化思想和技術路線。在鍋爐基本信息前期調查、企業需求分析和最佳化目標確定、試驗設計、增加關鍵中間參數控制、試驗數據採集、數據驗證、訓練人工神經網路、確定最佳化結果和建立鍋爐性能最佳化分析系統數學模型等方面都有創新和獨到之處。
同一台鍋爐可以根據不同的最佳化側重點,制定出提高鍋爐熱效率、降低供電煤耗、降低飛灰含碳量、減小與額定汽溫的偏差、降低污染物排放、提高鍋爐運行的安全性和穩定性等多種可操作性的最佳化方案。
2.3.鍋爐性能最佳化的原理
上世紀70年代,美國已經開始嘗試解決多重約束條件下的過程最佳化問題。限於當時的計算機水平和數學工具的匱乏,沒有取得有效的結果。近十年來,計算機技術的高速發展,提供了良好的技術基礎。燃煤電廠鍋爐性能最佳化就是解決多重約束條件下的熱力過程最佳化問題。最佳化系統的目標是建立一個分析平台,在平台上對鍋爐系統的多目標進行分析,找出鍋爐性能提升的最佳化潛力和薄弱環節,針對提升性能潛力、補償薄弱環節的具體方法和策略。
很多電廠多年來嘗試通過各種方法提高鍋爐效率,但一直沒有取得突破.到目前為止,採用傳統的熱力試驗和耗差分析的方法,最好的最佳化結果僅能達到鍋爐的設計水平。鍋爐性能最佳化系統以集中解決降低供電煤耗和NOx排放等綜合性指標為鍋爐性能最佳化目標,目前可以達到減少NOx排放、 改善鍋爐效率(反映到供電煤耗為2g/kwh以上),最佳化結果明顯。
鍋爐原始設計數據包含煤種、出力、排放和效率,各部件性能隨著時間惡化。理想的目標是當運行狀態改變,鍋爐的參數隨之進行相應的調整,使其保持較高燃燒效率。牽涉到鍋爐運行需要調整的技術參數多達數十個,其中包括:
(1) 燃燒器內的風粉比平衡;
(2) 良好的燃燒(過氧量、一氧化碳、飛灰含碳量和 NOx的最佳組合);
(3) 均勻的煙氣分布;
(4) 準確的吹灰控制;
(5) 穩定的系統負荷運行;
(6) 預期的磨煤機的輸出和煤粉的細度;
(7) 在設計範圍內的爐膛出口煙氣溫度和排煙溫度;
(8) 適當的設備和儀表校正;
(9) 關鍵參數在設計值內運行(系統內各部分運行參數的協調)。
技術人員可以依靠安裝、設定大量的線上監測儀表,實現以上各項參數的有效控制,但所需費用極為龐大。如果能夠採用信息技術和相關分析的方法,完全可以通過現有的儀表實現鍋爐各輸入量和目標參數的控制。
鍋爐系統設計中為了保證安全, 所屬設備和參數都有較大的設計餘量和安全係數(稱系統冗餘).有些方面設計得相當保守,使得設備能夠容忍一些運行上的偏差,保護鍋爐安全運行。實際運行中所有最惡劣的運行工況不可能同時發生,在某些區域系統有相當可觀的調整餘量,可以在確保全全的情況下減少這些餘量,達到比原設計更好的性能。在某些情況下,為達到更為理想的最佳化目標,對某些參數進行調整,甚至使其偏離設計值,就需要對調整方案進行正確地評估和謹慎操作。
鍋爐性能最佳化系統就是分析這些最佳化潛力的分析平台,在量化這些技術指標潛在的保守內容的同時,提供改善系統性能的方法。
達到多目標最佳化的技術思路,除了減少系統“冗餘”,還可以通過交換限制條件來達到多目標改善。從鍋爐燃燒方面深刻了解這些目標與限制條件的物理意義,化簡約束關係實際上就是大幅度簡化燃燒最佳化的數學結構。以目前的計算機發展水平,要想在不簡化鍋爐模型和計算工作量而進行最佳化是不可能的,如何簡化鍋爐模型就是制約性能最佳化成功與否的關鍵內容。通過相關性分析和相關度計算,可以有效簡化最佳化運行數學模型的結構和減少計算量,使最佳化方法能夠易於被現場技術人員接受.
近年來,鍋爐性能最佳化計算機軟體套用在工業領域增長很快,成為解決系統多輸入、多輸出變數等多重約束條件的強大工具,典型套用如圖2所示的控制輸入和輸出參數。
輸入參數最佳化模組 輸出參數
圖2.鍋爐性能最佳化邏輯
2.4.最佳化參數
2.4.1對每一個性能目標建立起相對的輸出變數的限制條件與最佳化指數;
? 選擇過程內的中間參數及其限制條件;
? 建立輸入參數與其運行範圍;
? 執行參數試驗來收集數據以及挖掘性能改善的潛力;
? 使用最佳化軟體來獲得輸出參數的最佳化值與輸入參數的運行數據。
在選擇輸入參數、過程輸入和輸出參數的控制如圖2所示。
輸出參數-代表電廠的效率、費用、排放、可靠性、安全性和出力等目標。選擇可靠性和安全性等運行參數所代表的功能目標,以數學的方式進行最佳化計算,可以是直接的、間接的(計算出來的)或模糊(觀察)得到的。
過程中間參數-是定位於輸入和輸出參數之間的參數。燃煤電廠的控制系統主要集中於輸出控制,從鍋爐可靠性考慮,這種控制方式不夠理想,必須用控制輸入和過程中間變數的方法避免輸出變化。
輸入參數-定義為可以被運行人員控制或調整的參數。輸入參數的選擇基於與輸出參數的關係,為了減少數據計算和數據採集量,只有選擇主要與關鍵性的運行參數才能選出輸入參數,一個輸入參數可以影響多個目標,並有相互矛盾的影響。輸出參數可以受到多輸入參數影響。
2.5.數據採集和參數測試
數據質量-所有的技術處理都是基於數據,數據質量源於校正完好的儀器儀表,決定著最佳化系統的成敗。為了解決儀器數據問題,數據驗證功能模組可以忽略或按估計值取代失真數據。
選擇數據-根據設計參數、運行情況及適量的試驗,參考現有大量的性能最佳化記錄和經驗,分析並得到關鍵的、多重的、敏感的範圍輸入、中間輸入和輸出參數。
試驗設計-做出獨特的試驗方案和數據採集、分析的計畫,以很精練的方案獲取寬泛的邊界範圍和參數,通過統計學計算和相關性分析輸入參數、過程輸入和輸出參數的數量最小化,以避免大量的測試、潛在的計算難度和錯誤,而後從大量的參數中篩選適量的關鍵參數,這些參數將是未來系統最佳化的核心參數。
分析數據-從歷史紀錄、現場測試或未來運行中得到的數據,通過參數變化測試來決定性能最佳化的潛力,得到必要的數據來建立數學模型,以得到最快的最佳化結果。並將飛灰含碳量測量數據和NOx線上監測數據作為反饋信號引入鍋爐性能最佳化系統中,作為線上最佳化基礎參數。如果系統的一些關鍵性運行參數改變,有可能需要重新調試,以確定變化後的數學模型。
實時數據-對於要求閉環線上直接控制DCS進行最佳化運行的機組,由於最佳化系統線上運行,需要及時提供設備運行輸入變數的前饋和輸出變數的反饋信息,需用戶額外增加必要的線上監測儀器和設備.如煤質線上分析;氮氧化物線上監測;飛灰可燃物線上監測等.以上實時數據作為最佳化控制系統的計算依據,需要非常可靠和準確.
2.6. 鍋爐性能最佳化系統技術核心
2.6.1系統觀念全面分析: 現場採集運行數據和了解用戶需求,基於系統觀念突破專業局限,全面分析鍋爐系統運行中存在的內在問題和產生問題的原因,在最佳化燃燒的同時,全面考慮能量交換的均衡和來自各方面的影響因素。
2.6.2挖掘設計保守係數: 在鍋爐設計的過程中,對設備和參數都有較大的設計餘量和安全係數,以保護鍋爐安全運行。實際運行中所有最惡劣的運行工況不可能同時發生,在某些區域系統有調整餘量,可以在確保全全運行的前提下挖掘這些餘量(系統冗餘),來達到或超過原設計性能指標。鍋爐性能最佳化系統其中一項工作就是分析並挖掘這些潛在的最佳化空間,在量化潛在的最佳化空間的同時,提出具體改善鍋爐性能的方法和最佳化指標。
2.6.3採集關鍵數據,全面協調運行參數:人工智慧神經網路經過數據採集、建模、線上或離線調整(校正)等過程對機組的各種運行工況獲得豐富的"知識",然後利用統計學、非線性回歸分析等數學工具對當前運行目標參數進行協調和最佳化,得出最佳運行參數組合。例如,過量空氣係數問題,在一定範圍內當過量空氣係數增大時,爐內燃料燃燒就越充分,不完全燃燒損失就越小;但過量空氣係數增大的同時也造成了鍋爐排煙熱損失的增加和其它不利影響。人工神經網路的任務就是要在這兩者之間找到一個最佳的平衡點,使得熱效率達到最優的水平。鍋爐是一個多輸入變數和多輸出目標參數的系統,輸入參數之間;輸入與輸出參數之間;輸出與輸出參數之間都存在著相關關係和諸多矛盾,協調解決多變數的非線性關係問題,超過了現場技術人員的能力,也不是依靠經驗和一般的經驗和簡單的熱力試驗可以解決的,鍋爐性能最佳化鍋爐性能最佳化系統為用戶提供了全面解決這些問題的理想方案。
2.7. 鍋爐性能最佳化系統特點
2.7.1鍋爐性能最佳化系統以鍋爐專家豐富的專業經驗和系統觀念為基礎,充分了解鍋爐存在的問題和用戶的需求,並針對鍋爐的具體特點進行多目標最佳化設計,直接指導最佳化試驗.利用計算機技術和最佳化控制邏輯,解決多輸入變數和多目標之間最佳化組合的難題,用科學的方法解決傳統的認識誤區,突破傳統運行模式。
2.7.2線上開環指導或閉環控制運行,直接完成最佳化燃燒運行,並可以根據用戶不同需求,完成不同燃燒形式組態,實現全面或單項性能指標(不損害其它性能指標)最佳化。鍋爐性能最佳化系統技術方案突破了普通最佳化方案的傳統理念和方法,立足於全面最佳化思想和技術路線。在鍋爐基本信息前期調查、企業需求分析和最佳化目標確定、試驗設計、增加關鍵中間參數控制、試驗數據採集、數據驗證、訓練人工神經網路、確定最佳化結果和建立鍋爐性能最佳化分析系統數學模型等方面都有創新和獨到之處。
2.7.3最佳化系統安裝調試和最佳化過程占用時間短,30天左右即可完成並見到效果。鍋爐性能最佳化分析是一個極為複雜的過程,對過程進行合理簡化並建立簡化的數學模型是鍋爐性能最佳化系統成功訓練人工神經網路的關鍵。邊界條件的確定、中間變數的引入、篩選高品質數據和創造數據的方法、豐富的鍋爐運行經驗和成功建立數學模型是多變數非線性函式多度空間快速收斂的基礎。
2.7.4效果顯著:最佳化系統指導下,供電煤耗至少可降低2g/kwh,系統設計綜合考慮機組調峰運行和燃燒質量不同的低價格煤種,通過改變調節參數改善氮氧化物排放、減少減溫水流量、降低廠用電、飛灰含碳、提高熱效率等,保護汽機滑壓運行、增強機組可靠性和可用率、延長停機間隔時間和縮減停機時間等多重目標進行全面最佳化。在市場經濟環境下,發電企業追求的是機組經濟性、可靠性、安全性及排放物的有效控制,理想目標是鍋爐能夠長期安全穩定、高效率、低排放的運行。雖然達到這一理想目標比較困難,但通過增加監測裝置控制與性能最佳化等新技術,制定不同時期的最佳化方案和多重目標,從相對單一的運行目標向多目標最佳化過渡,可以改善設備的運行水平,提高鍋爐的可靠性、穩定性及經濟性。
2.7.5鍋爐性能最佳化系統增加了爐膛出口溫度監測系統,可以有效防止過熱器、再熱器等部件超溫和高溫腐蝕等問題產生,並可幫助用戶預防和控制爐膛結焦結渣。
鍋爐性能最佳化系統的核心是設定關鍵中間運行參數,爐膛出口是鍋爐輻射區和對流區的分界區域,是鍋爐設計和運行的關鍵控制點。引進國外先進的航天遙感技術和裝置,對該點進行實時線上監測,得到反映鍋爐系統燃燒狀態和換熱過程中關鍵數據,從而也有效地解決人工神經網路訓練快速收斂的問題。
遠紅外輻射式煙氣測溫儀是遠距離非接觸式測量裝置,可安裝在任何觀察口、檢修口等爐壁開孔牆面外部。在鍋爐性能最佳化系統安裝之前,根據機組的特點,在相關技術人員的配合下,選定遠紅外煙氣測溫系統的安裝位置。
2.7.6 最佳化方法簡便易行,易於現場掌握。提供現場培訓和定期訪問,保證最佳化系統穩定運行。鍋爐性能最佳化系統與傳統鍋爐燃燒調整和耗差分析的不同之處,就是擺脫傳統熱力模型和理論計算的模式,利用運行數據信息直接指導鍋爐性能最佳化。實現方法是根據歐美工業已開發國家的成功經驗,利用模糊數學理論和人工神經網路技術,找出多變數之間的非線性關係,計算得到運行參數的最佳組合,幫助技術人員全面系統的理解約束條件和系統潛力,從而挖掘出系統的最優性能或在多重約束條件下找出一個最佳方案。
2.7.7 數據驗證模組:借鑑航空航天領域成熟的數據驗證數學模型編制的功能模組,實現儀表數據線上實時跟蹤分析。對於異常數據和偏差情況及時發現並予以糾正。該方法處理數據快捷、分析準確,可以篩選掉不良數據,填補高品質數據,為技術人員分析運行狀況,早期發現問題提供依據。
2.7.8 鍋爐性能最佳化系統具有良好的魯棒性:鍋爐性能最佳化系統的自學習功能,能在一定範圍內適應鍋爐燃燒過程中的眾多不確定性因素,輸入變數變動幅度在10%左右能實現自適應.如果變動的幅度過大,可根據具體變動情況,在離線情況下進行調試和建立幾種與之相適應的最佳化運行模式.在實時監測數據的支持下,進行模式無縫切換或直接實時最佳化控制.最佳化運行的前提是保證鍋爐系統的安全穩定運行。
鍋爐性能最佳化系統項目內容和實施程式及案例
鍋爐性能最佳化方案有三種:
1、簡化方案:不安裝任何測點、運行最佳化軟體的伺服器系統和工作站,現場做鍋爐性能最佳化試驗並提供最佳化運行指導曲線。
2、線上開環指導鍋爐最佳化運行。
3、線上閉環控制鍋爐最佳化運行(由於國內煤質,設備等問題暫不推薦)。
3.0.項目內容
? 煙氣測溫系統儀器的安裝、調試
? 鍋爐性能最佳化系統與DCS系統接口和單向通訊
? 鍋爐系統運行特性全面試驗和數據採集
? 數據篩選、驗證;建立鍋爐運行最佳化數學模型
? 運行最佳化系統的調試和最佳化結果預測並驗證
? 運行最佳化控制系統的調整和投入最佳化運行指導或最佳化運行控制
3.1.試驗前提
(1)要求試驗期間入爐煤煤質、機組負荷保持相對穩定;
(2)保持試驗要求的磨煤機輸出和煤粉細度;
(3)適當的設備和儀表校正,保證關鍵儀表數據準確。
3.2.試驗內容
鍋爐系統運行參數線上分析和可調參數如下所示:
(1)調節過氧量;
(2)調節風門擋板;
(3)調整給粉機轉速;
(4)調整燃燒器擺角;
(5) 爐膛與風箱壓差;
(6) 調節控制爐膛出口煙溫(過程參數);
(7)有關的運行參數等(具體試驗內容需要根據鍋爐設備的實際情況制定)。
3.3.項目實施程式
項目開始前由工作組成員對鍋爐運行參數和現狀進行調研和分析,根據調研分析結果制定具體最佳化試驗設計和調試方案,確定最佳化目標、最佳化範圍和邊界參數;根據所擬定的方案安排試驗設計、確定性能最佳化基礎數據採集清單;工作組成員根據試驗設計,通過DCS系統和相關儀器儀表採集不同負荷工況下的基礎數據;待基礎數據採集工作完成後,利用統計回歸分析對試驗數據進行分析和篩選,篩選後得到的高質量試驗數據用於指導軟體工程師進行人工神經網路訓練,最終確定鍋爐系統最佳化數學模型,並將飛灰含碳量測量數據和NOx線上監測數據作為反饋信號引入鍋爐性能最佳化系統中,作為線上最佳化依據。最佳化運行結果經過預測和驗證,開環最佳化指導模式下,向鍋爐運行人員實時發布最佳化運行提示,並給專業技術人員提供鍋爐運行最佳化指導檔案和最佳化運行曲線(不同負荷工況條件);閉環最佳化控制模式下,最佳化指令通過DCS直接輸出最佳化運行指令。本文3.4節為實際最佳化過程案例,總過程大體分6個階段。
現場試驗和調試結束後,技術人員提供系統操作技術培訓,指導鍋爐專業技術人員全面掌握最佳化系統的使用和維護。
鍋爐性能最佳化實施程式如附圖3所示。
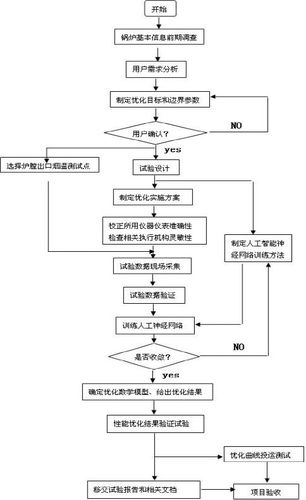
附圖3 鍋爐性能最佳化流程圖
四.經濟效益分析
4.0最佳化系統設計目標:
在機組安全運行的基礎上,提高鍋爐機組運行效率0.5-1%根據現場採集數據和綜合分析,鍋爐性能最佳化系統投入使用後,預期可以達到降低供電煤耗2g/kwh左右;降低氮氧化物排放量100mg/m3.
4.1 降低供電煤耗(以300MW機組為例)
鍋爐性能最佳化系統在不增加灰中含碳量的前提下,確保鍋爐熱效率目標的基礎上供電煤耗至少可以降低2g/kwh左右(根據目前已經取得的最佳化業績,較好的情況可以降低8-12克/Kwh),鍋爐年節約煤耗(按2g/kwh計算):
(2×10-6)t/kwh×300MW×6000h×700元/t=252萬
按目前平均煤價700元/噸計算,通過鍋爐性能最佳化節煤年直接經濟效益至少在252萬元人民幣以上。
4.2降低NOx排放
2003年2月28日由國家發展改革委員會、財政部、國家環境保護總局、國家經濟貿易委員會根據國務院令字第369號《排污費徵收使用管理條例》,制定頒布了《排污費徵收標準管理辦法》規定從2004年7月1日起,NOx排放按實際排放污染當量收費,每污染當量NOx收費0.6元(每污染當量為0.95千克)。
參照1004噸蒸發量鍋爐參數測算:總排煙量1.3×106m3/h;按照年運行6000小時,以降低100mg/m3估算(實際最佳化值需根據現場情況確定)。
則年NOx排放節約費用為:
1.3×106m3/h×100×10-6kg/m3×6000h×0.6元/0.95kg= 44.46萬元
直接經濟效益合計:
年總節約費用為252萬元+44.46萬元=296.36萬元 以上
4.3間接經濟效益分析
增加關鍵點運行參數控制,實時線上監測爐膛出口煙溫,預防和控制鍋爐結焦問題;控制過熱器與再熱器的管壁溫度,降低過熱器和再熱器的等效強制停機率, 延長鍋爐部件使用壽命,有效的降低鍋爐維修費用和可用率,間接經濟效益非常可觀。
綜上所述,通過鍋爐性能最佳化系統的投入,除提高鍋爐運行技術管理水平外,每年還為電廠帶來296萬元以上的直接效益。該系統投入正常運行後當年應可收回投資,具有較好的社會效益和企業經濟效益。
五.鍋爐性能最佳化系統設計與構成
5.0.軟體系統設計原則
5.0.1總體原則
① 鍋爐性能最佳化系統所採用的技術符合併遵守國際標準,互連繫統應遵守ISO(國際標準組織)的OSI(開放系統互連)標準,能滿足企業未來一定時期發展和升級要求。
② 先進性套用軟體系統的先進性充分進行綜合考慮。不僅對網路環境進行綜合分析評價,而且還對套用軟體系統開發所用的資料庫系統及開發工具及所選擇的開發方法、開發策略、開發規範、軟體開發所貫穿的管理思想等諸方面做出詳細的介紹。
③ 開放性軟體系統的開放性的主要目的是便於系統的擴展和未來的信息管理系統整合.涉及到計算機系統、網路和套用軟體等諸多領域。保證系統的開放性,主要體現在數據結構、軟體文檔和資料庫的開放。在軟體開發過程中應執行一套行之有效的用以確保系統的一致性和完整性的標準和規範,並將有關標準、規範作為軟體系統補充說明檔案提交用戶。
④ 實用性所提供的套用軟體產品以用戶鍋爐特性為基礎,專業人員和運行人員使用系統時,應用程式做到界面友好,簡單、易學、易用,較短時間可以使用該系統.套用軟體系統模組化,各模組功能清晰明了,便於使用人員了解整個鍋爐運行系統的最佳化控制過程。
⑤ 易維護性軟體維護的主要目標是適用性維護和改善性維護。為了提高軟體的可維護性,應為用戶提供軟體說明書;軟體系統維護手冊並做到:
(a)建立可維護性的開發環境。
(b)建立質量保證體系。
(c)將重用性作為軟體開發的指導思想,設計易於重用的軟體部份。
(d)設計階段就要考慮到軟體的運行和維護。
(e)適應未來可能的變化,採用“模組構件”的組件方式進行。
⑥ 安全性和可靠性
系統必須具有很高的可靠性和安全性,這是必須具備的一個重要的條件,在資料庫系統和網路系統的多層管理和安全體系控制下,對套用軟體安全系統建立的方式,系統數據備份和容災、容錯等方面有完善的考慮。
5.0.2功能設計原則
① 鍋爐性能最佳化控制系統能夠全面的提高鍋爐熱效率;穩定過熱、再熱汽溫,減小與額定汽溫的偏差;降低污染物排放(如NOx);降低廠用電率;提高鍋爐運行的安全性、經濟性和可靠性。不影響DCS系統的安全可靠運行。
② 鍋爐性能最佳化控制系統可以開環指導和閉環控制手段實現鍋爐性能最佳化,系統與DCS採取單向通訊方式(閉環為雙向通訊),即最佳化控制系統從DCS獲取鍋爐運行的實時數據,不返回到DCS。
③ 鍋爐性能最佳化控制系統的硬體安全、可靠、先進。性能最佳化控制系統具有魯棒性,能在一定範圍內自適應鍋爐輸入參數的變化,自學習並自動控制相關的操作機構,達到自動最佳化的目的。
④ 鍋爐性能最佳化控制系統具有易於使用、易於維護,控制的輸入輸出和最佳化控制目標都可以自由設定。
⑤ 鍋爐性能最佳化控制系統具有完善的保護功能,使其具有高度的可靠性,系統發生任何故障都不影響DCS的正常工作,從而影響鍋爐安全運行。
⑥鍋爐性能最佳化控制系統裝有網路防病毒軟體,採取有效措施,以防止各類計算機病毒的侵害、人為的破壞。
⑦鍋爐性能最佳化控制系統能達到全部功能要求。
鍋爐性能最佳化控制系統結合工藝系統和機組特點進行設計,是專用的性能最佳化控制系統。最佳化控制系統的平台和模組是通用的,但目前是一個半定值的軟體,實施過程中要針對鍋爐系統進行具體的試驗、組態和定製。
5.1 鍋爐性能最佳化系統配置方案
(1)遠紅外輻射式煙氣測溫儀
該測溫儀是引進國外先進的技術,對爐膛出口溫度進行非接觸性、實時線上監測,是鍋爐性能最佳化系統的一個關鍵中間控制參數。
爐膛出口點是對流區和輻射區的分界點,通常把這一特別控制點稱為FEGT(爐膛出口煙氣溫度).爐膛出口煙溫對鍋爐運行控制非常重要,通過對FEGT這一關鍵參數的控制,可幫助鍋爐運行人員及時發現運行狀態的變化、及時反映最佳化軟體對運行狀態的調整效果.提供預防結焦和積灰控制、智慧型吹灰控制、過熱蒸汽控制和低NOX 燃燒等最佳化調整的依據。
遠紅外輻射式煙氣測溫儀是遠距離非接觸式測量裝置,可安裝在任何觀察口、檢修口等爐壁開孔牆面外部。與堅固的具有保護性冷卻套和具有空氣冷卻、吹掃、過濾器的連線管路相配合,適用於惡劣的測試環境。安裝使用簡便,輸出為4-20毫安標準信號,可直接接入DCS系統.系統的測量範圍為120~1650℃(或300~1200℃),完全可以滿足燃煤電廠鍋爐的一般要求。
● 遠紅外測溫儀特點
遠紅外輻射式煙氣測溫系統。可沿著煙氣的流程安裝多個測點.實現鍋爐熱力交換系統的溫度參數系統監測,實現鍋爐系統能量交換的均衡和協調控制。
(a)鍋爐啟動過程控制:鍋爐啟動過程中,必須對FEGT進行監測,控制過熱器壁溫不超過允許值。很多電廠採用帶有冷卻裝置的熱電偶類測量設備用以監測FEGT,限制其在規定的溫度極限內。但當FEGT超過600℃時必須將其收回來,以免被燒毀,不能實現線上連續測量。遠紅外煙氣測溫儀是遠距離非接觸式測量裝置,可以取代傳統的伸縮式爐內測溫探頭。並進行鍋爐啟動階段和運行全過程的FEGT監測,且體積小、造價低,使用方便、維護簡單。
(b)鍋爐性能最佳化分析系統配套:遠紅外輻射式煙氣測溫儀,用於鍋爐性能最佳化分析系統關鍵參數監測。鍋爐性能最佳化需求分析、數據採集、人工神經網路建模、試驗設計、試驗驗證、運行訓練及操作指導等全過程中,把FEGT實時線上監測數據作為過程參數,配合配風、配煤、燃燒器擺角角度、減溫水控制等燃燒參數,實現鍋爐性能的多目標最佳化。
(c)結焦與積灰控制:熔融的煤灰在蒸汽攜帶下撞擊在水冷壁或管壁上,冷卻凝固形成結焦。控制FETG低於煤灰的熔融、軟化溫度,可使乾燥的煤灰不能粘附在換熱管上,能明顯的改善對流通道內的積灰問題;對流煙道的積灰減少,過熱器和引風機的能耗將會降低,從而提高熱負荷,防止吹灰器的腐蝕。
(d)智慧型吹灰控制:保證煙氣的正常流動和換熱器正常工作,吹灰是清除煤灰的有效手段。運行人員可根據FEGT值進行包括吹灰時間、吹灰順序設定的吹灰器投停自動控制,也可用於提醒運行人員進行手動吹灰操作。利用時間、溫度歷史曲線的記錄,對吹灰器的運行時間進行控制。在吹掃時監測鍋爐的溫度變化,用以改善爐管的傳熱性能,並防止吹灰不足造成結焦的情況發生。監測鍋爐煙氣溫度並與蒸汽的出口溫度相比較,由此來確定吹灰器的最佳運行時機。
(e)低NOX燃燒控制:缺氧燃燒被廣泛套用於低NOX燃燒中,爐膛區域的嚴重缺氧,形成還原性氣氛,加劇了向火側水冷壁管的腐蝕。燃料的燃燒焰炬加長或二次燃燒,使FEGT升高,造成過熱器和再熱器換熱管的超溫過熱,運行人員的職責主要是維持FEGT在設計值限度內,儘量忽略其它因素的影響。必要時,需要採取折衷方案或多目標最佳化控制系統。
(f)高溫報警:監測鍋爐最佳運行條件下的煙氣最高允許溫度,用以防止水冷壁管,再熱器與過熱器的超溫和由此造成的爆管。
(g)爐膛一次風監測:監測爐膛中具有分割牆的鍋爐中各個分割區內的煙氣溫度,並保持溫度的均勻分布。
煙氣側參數控制的意義
維持鍋爐的合理運行需要正確的煙氣側參數的控制,FEGT這個特別點對於鍋爐的安全穩定運行有重大意義,該系統提供了廣泛的煙氣溫度測量範圍,FEGT的實時線上監測,為鍋爐系統最佳化運行提供過程控制關鍵參數和最佳化調整的依據。見3.4.6項目實施結果-爐膛出口煙溫控制對鍋爐性能的影響.
(2)系統伺服器和操作員站
用於採集並保存基礎試驗數據、建立最佳化分析平台、對試驗數據進行人工神經網路訓練、對最佳化結果和預測結果的發布。
(3)硬體配置系統結構
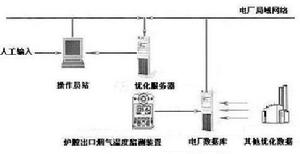
鍋爐性能最佳化系統硬體網路結構圖如圖4:
圖4 系統硬體配置網路結構圖
i. 伺服器-戴爾或研華伺服器 (配置從略)
ii. 操作員站-戴爾PC機 (配置從略)
iii. 硬體接口-PLC可程式控制器或與用戶DCS通訊適配的硬體
5.2鍋爐性能最佳化系統軟體結構和數據接口
軟體系統主要由下列模組組成:
1、數據處理模組:該模組實現機組實時運行數據的處理和分析功能。
2、數據通訊模組:該模組實現與DCS及系統主機的實時數據單向通訊功能。
3、鍋爐燃燒模型建模平台(套用人工神經網路技術):該模組可以構建基於人工神經網路技術的,針對鍋爐綜合性能的最佳化運行模型。
4、數據校驗模組:該模組實現對數據流程中各個環節實時數據的實時檢查功能。
5、離線預測模組:該模組實現最佳化曲線的預測功能。
6、圖形用戶界面:該模組實現用戶圖形界面的組建功能。
鍋爐性能最佳化系統從電廠現有的DCS資料庫中提取所需運行參數,通過人工智慧神經網路建立最佳化模型指導鍋爐運行,達到鍋爐性能最佳化的目的。
鍋爐性能最佳化系統線上開環指導或閉環控制最佳化運行,需要與DCS或SIS系統接口,進行數據交換和發布最佳化運行提示和控制指令,具體接口方案與熱控技術人員或DCS廠家確認,需要根據DCS廠商的接口規定和用戶單位專業技術人員的要求,全面規劃後提供。
鍋爐性能最佳化系統包括系統軟體和最佳化軟體兩大部分;系統軟體為正版作業系統和資料庫;最佳化軟體內有數據處理和人工神經網路最佳化兩個模組。其軟體結構(如下圖5)。
鍋爐性能最佳化系統與電廠現有的DCS資料庫交換數據,只需要根據具體DCS系統的通訊方式和I/O接口規定,以DCS-資料庫系統-鍋爐性能最佳化系統方式建立通信。開環系統,只需從DCS系統採集數據,最佳化結果不進入DCS系統,比較簡單;閉環控制系統,需要通過PLC可程式控制器硬體系統隔離或軟體接口程式方式與DCS資料庫或者其他資料庫(PI或者MIS)交換數據,設計上已給予充分考慮,對電廠現有的資料庫不會造成任何安全上的問題,發布的最佳化控制指令與DCS控制邏輯不會發生衝突。
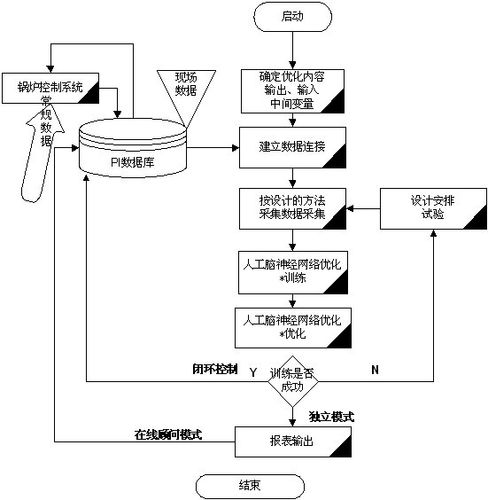
圖5鍋爐性能最佳化系統軟體結構示意圖
以上方案簡述了鍋爐性能最佳化系統的硬體、軟體和系統構成和最佳化過程.系統組態和具體設計方案,需要根據DCS廠商的接口規定和用戶單位專業技術人員的要求,全面規劃後提供。
天津鷹麟節能科技發展有限公司
技術部:王帥 劉澤源