軋輥磨床概述
磨床是鋼材板材軋制生產線的重要配套設備,其磨削精度和磨削效率直接影響鋼板的軋制質量與生產效率。軋輥在鋼板軋制過程中因高溫氧化和機械磨損等原因會導致
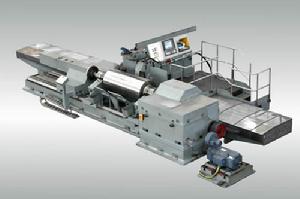
軋輥磨床型號
國內軋輥磨床主要型號有:MK8440、MK8450、MK8463、MK8480、MK84100、MK84125、MK84160、MK84200、MK84250、MK84300。軋輥磨床
概述套用領域
●多式軋機 ●鋁箔軋機 ●膠片業 ●印刷業 ●塗層軋輥 ●軋輥製造 ●特殊套用
軋輥磨床結構介紹
床身床身採用砂輪床身與工件床身分離的結構。床身調整墊鐵間距
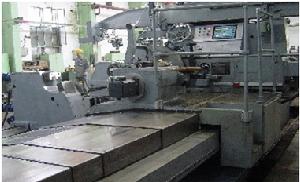
頭架
採用三級三角皮帶傳動保證了傳動的平穩和精度;使用交流主軸電機驅動能使頭架實現正向和反向鏇轉;頭架的位置控制功能,可實現撥盤角度自動定位,方便軋輥的吊裝,減少輔助時間。頭架潤滑系統選用了油脂泵,可實現自動定時給油。
尾架
尾架移動採用電動驅動方式,液壓自動鎖緊。尾架配備大行程(1000mm)液壓套筒。
砂輪主軸系統
砂輪主軸前後徑後軸承均採用高精度動靜壓軸承,主軸軸向採用高精度推力軸承。另外,在後軸承設計中增強了工作腔動靜壓軸承的靜態壓力效果,以克服較大皮帶拉力對軸瓦造成的損傷。主軸動靜壓軸承具有迴轉精度高,穩定性好,動態剛性強,不易振動等特點。
磨架及其進給機構
磨架採用單層整體結構,具有很高的剛性,磨架導軌為貼塑靜壓導軌,磨架進給機構由帶減速裝置的西門子交流伺服電機和經過精確預拉伸的精密滾珠絲桿副組成,具有很高的進給精度和靈敏度。
拖板(Z軸)
拖板採用V-平形形式的貼塑靜壓導軌,拖板進給機構由帶減速裝置的西門子交流伺服電機和經過精確預拉伸精密滾珠絲桿副組成,由數控系統通過交流伺服電機和圓光柵實現拖板的閉環位置控制。拖板採用滾珠絲桿傳動,與國內外同類磨床所採用的傳統齒輪齒條傳動相比,具有機械傳動鏈短、運動平穩、傳動精度高、間隙小等優點。
伺服電機及其控制系統
磨床所有伺服電機全部採用西門子全數位化交流伺服電機,精度高可靠性高。
頭架控制系統
頭架採用西門子1PH7型交流主軸電機驅動,內裝西門子Sine/Cos1Vpp,2048S/R光電編碼器,完成頭架速度及位置的閉環控制。頭架可實現正向和反向鏇轉以及撥盤角度自動定位。交流主軸電機的採用使頭架電機的維護工作量大大減少。針對軋輥驅動的特點頭架採用了低額定轉速、大啟動扭矩的交流主軸電機,在保證重型軋輥啟動需要的同時節約寶貴的能源。
砂輪控制系統
砂輪採用西門子1PH7型交流主軸電機驅動,內裝西門子Sine/Cos1Vpp,2048S/R光電編碼器,完成砂輪速度及位置的閉環控制。砂輪可實現正向和反向鏇轉以及角度自動定位。另外,交流主軸電機的採用極大地方便了砂輪電機的維護。砂輪採用了高達100KW的交流主軸電機,保證了磨床具有強力磨削能力,滿足用戶的軋輥快速大負荷加工要求。
電氣控制櫃及櫃內配電系統和控制元件
為保證磨床電氣系統的整體可靠性,從電氣控制櫃箱殼到櫃內的配電系統以及保護元件、開關元件、控制元件全部採用進口的國際名牌產品(西門子、威圖)。
U1軸
U1軸傳動系統是由帶直角減速裝置的西門子交流伺服電機驅動一套偏心輪傳動機構,通過連桿驅動中心架上層滑板.尾架端中心架被設定為二層,下層底座可沿床身導軌縱向移動,上層滑板在U1軸驅動下可橫向水平微量調整(調整量1.5),以實現對軋輥安裝精度的校正。中心架滑板的特殊結構設計,可以很方便的調換安裝在滑板上的中心架瓦座,大大縮短更換瓦座的輔助時間,特別適用於多規格軋輥的支承。
數控系統
數控主機採用西門子新一代全數字控制系統840D,一體化S7-300可程式控制器,工具機外部的I/O接點通PROFIBUS工業現場匯流排傳輸到中央控制系統,人機接口功能由新型高性能SINUMERIKPCU50模組完成.與國外同類磨床所採用的磨床廠自行開發的工控機專用系統比較,840D系統功能更加強大、更加可靠、維護更加簡單,(因為840D系統經過了成千上萬用戶的使用驗證和西門子多年不斷的改進)。由於840D系統的通用性,使磨床的維護變得異常方便,所有的電氣部件均可以在市場上採購到,磨床電氣系統不存在進口磨床所常見的黑匣子問題。
人機接口
顯示器採用西門子15寸液晶顯示器OP15,中文/英文顯示,作業系統採用MS-WINDOWSXP。系統具有完備的報警與診斷功能,配備豐富的幫助及操作提示。設計完善的畫面和操作選單,能被操作者和維護人員方便而快速地全面掌握。
測量架系統(X1軸)
測量臂導軌採用德車STAR的進口直線導軌,傳動系統由帶減速裝置的西門子交流伺服電機通過無鍵連線方式驅動經過精確預拉伸的精密滾珠絲桿,由數控系統通過交流伺服電機和直線光柵實現測量架的閉環位置控制。測量架採用直線導軌和滾珠絲桿傳動,與國內外同類磨床所采和的齒輪齒條傳動相比,具有運動平穩、傳動精度高、靈敏性好、定位準確等優點,從而大大提高了測量系統的測量精度。
高精度數控曲線磨削裝置(U軸)
本裝置採用靜壓偏心套結構(內裝主軸動靜壓軸承),傳動系統由帶減速裝置的西門子交流伺服電機通過無鍵連線方式驅動精密滾珠絲矸,通過直線滾動導軌副定位,使滾珠螺母上下移動進而帶動高精度靜壓偏習套作小角度擺動,使裝於靜壓偏心套內的砂輪主軸相對於輥面作微量無間隙切入(或退出)運動。該運動與拖板(Z軸)運動相複合,從而在軋輥表面磨削出所需曲線。特殊設計的傳動結構,確保了傳動系統始終處於無間隙狀態,從而可以獲得很高的曲線磨削精度。
軋輥磨削工藝
(1)砂輪速度粗、精磨鋼質軋輥25~35m/s粗、精磨冷硬鑄鐵軋輥20~25m/s超精磨削、鏡面磨削時15~20m/s(2)工件(軋輥)速度粗磨時30~50m/min精磨時15~30m/min精密拋光磨削時10~15m/min當磨削細長輥子時應採用低速,尤其是磨削輥身尺寸小的光壓延輥時,工件軋輥的速度小於10m/min。(3)拖板縱向進給速度粗磨時240~600m/min;或取工件每轉拖板縱向進給量約為砂輪寬度的2/3~3/4。精磨時80~200m/min;或取工件每轉拖板縱向進給量約為砂輪寬度的1/4~1/2。(4)拖板每往復行程橫進給量粗磨時橫進給量應根據軋輥的硬度和磨削輥面的直徑而定,一般取0.03~0.05mm/往復行程。對於材料硬 、輥頸大的軋輥,應減小橫進給量。精磨時0.005~0.01mm/往復行程。精密拋光磨削時0.002~0.005mm/往復行程。軋輥磨床的操作及保養
操作規程1:操作人員經考試合格取得操作證,方準進行操作,操作者應熟悉本機的性能、結構等,並要遵守安全和交接班制度。
2:操作者必須根據磨床說明書的要求,詳細了解並熟記各潤滑部位,潤滑方法及潤滑油的種類、牌號,按磨床潤滑圖表的規定進行給油保養。
3:開工前,應按規定穿戴好防護用品,對照交接班記錄薄,對磨床各部位進行詳細檢查,發現問題應及時逐級報告,異狀未經排除不得開車工作。
4:開工前應對軋輥磨床下列部位進行檢查:
(1)油池中的油量應達到規定的油麵高度。
(2)調整皮帶鬆緊度是否合適。
(3)防護罩和砂輪要裝卡牢固,位置正確,防塵氈墊密貼良好。
(4)檢查電氣系統是否良好,周圍環境應清潔,無短路。
(5)按軋輥磨床說明書規定的潤滑處所,順次注入潤滑油。
(6)接通總電源,順次啟動油泵等電機,注意運轉狀態,發現異狀,異音應立即關閉電源。
(7)開動軋輥磨床,空轉3min,查看各部動作是否正常,著咱是否正常,冷卻液是否暢通。
(8)裝卡砂輪前應防止砂輪受潮,砂輪應做份平衡試驗;嚴禁砂輪有裂紋。
(9)裝卡砂輪時,須在砂輪和壓板間墊以0.5——1.0mm的紙墊,並用專用扳子均勻用力緊固。
(10)砂輪裝好後應空載運轉5min,操作者應避開正面,確認砂輪運轉正常後,方準使用。
5:活塞桿的裝卡必須符合規定,,必須確認磨床的狀態正常後,方準開車。
6:加工軋輥必須事先清除被加工部位的油垢,黒污和灰塵等。根據工件的材質合理選用砂輪和磨製量,嚴禁磨削工件毛坯。
7:裝卡和測量工件時,必須使砂輪退離工件和停車。工件與砂輪未離開時,不得中途停車。砂輪在接近工件時,不準用機動進給。
8:工作時禁止操作者離開磨床或托人代管,如因停電或其他原因必須離開時,應將砂輪離開工件後停車。重新開動磨床時,應確認各部無異狀後方準開車。
9:磨床工作時,應注意各傳動部分狀態,如油溫和油壓是否正常,冷卻液是否暢通準確地澆到工件上;油泵與電機的溫度是否正常,有否異狀異音;各操作手柄是否位里正確,各緊固件有否鬆動位移等。
10:禁止在工作檯面與油漆表面放置金屬物品。
11:禁止在工作檯面及床體上敲打、拆裝、矯直工件。
12:磨床發生事故後,應保持現場,切斷電源.迅速報告,妥善處理。
13:工作完畢後,應將砂輪退離工件,切斷總電源,各手柄放置在空位上。恢復磨床正常狀態,做好日常保養。
14:認真填寫交接班記錄簿等有關記錄。
日常保養
1:必須根據軋輥磨床說明書的要求,在各潤滑部位,按規定的潤滑方法及潤滑油的種類、牌號,按磨床潤滑圖表的規定,進行給油保養。
2:潤滑油注入油箱及其他容器前,應經建油網過濾,油箱油量必須達到油標線。
3:油壺、油槍等感油器具必須清潔完整,不同牌號的油脂不準混裝。
4:油箱內不得留有好毛雜質,油箱中潤滑油如有沉澱、起垢、積水等現象應立即更換。
5:凡軟於油杯潤滑部位,每班至少擰進二扣以上。
6:禁止向冷卻液中加水,冷卻液不足時應添加製成的冷卻液。
7:工作檯的油盤、排冷卻液的管和過健網,要經常清除磨屑、油垢、雜物等。
8:隨時注意清掃導軌、工作檯等部位的磨屑、灰塵、油垢等,確保磨床在運轉中不致發生拉傷、擦傷等現象。
9:經常檢查砂輪,不準使用裂紋砂輪.防護罩、砂輪的位里和裝卡必須安全可靠。
10:工作完畢要認真擦拭磨床,各滑動面塗上一層薄油,對各部位應做到無油垢、磨屬、灰塵等雜物。
11:對工件、附屬檔案、工具進行清理,擺放整齊。清掃工作場地。
12:按自檢自修範圍.注意軋輥磨床的使用和保養。
定期保養
1:定期修理時,應更換潤滑油,清洗油箱必須將各機構清洗、擦拭乾淨。
2:換油時必須清洗濾油器,異油線、油杯、油盤,並流通油路;所有導油線,建油氈應清洗壓乾後,浸油放入油盤、油槽內。
3:油盤、油杯的濾油氈、導油線二周清洗一次;檔毛氈墊每周清洗一次。
4:冷卻液每隔2——3周更換一次。更換時要徹底清洗冷卻液箱,不許有殘留舊液與其他雜質等,冷卻液泵在3——4個月必須清洗一次。冷卻濃的配製應符合規定。
5:按規定定期送檢壓力表。
注意事項
1)操作時應密切注意砂輪與工件表面的接觸狀況。當工件表面剛與砂輪接觸時,可聽到連續的噝噝聲,工件表面的水跡可被鏇轉的砂輪帶走,同時可見到微弱的火花,此時即可加冷卻液。冷卻液宜選用濃度稍高的皂化液,使用前必須經過嚴格的清潔過濾。然後進給,每次進給量為0.005mm/每雙行程。至火花消失時,磨削完畢,此時將橫向進給手輪向進給方向按住,使砂輪向工件微微壓進,但不作進給,即等於對工件進行一次拋光,以進一步提高磨削表面質量。
2)在環境溫度較高(如夏季)情況下進行磨削時,工具機照明燈不宜靠近工件,以防止工件受熱膨脹而影響磨削質量。
3)如出現工件表面拉毛現象,說明冷卻液不乾淨或砂輪表面有浮砂,應重新過濾冷卻液或刷掉砂輪表面浮砂。
4)如出現工件局部燒傷現象,可能是冷卻液不充分或進給量過大,或砂輪鈍化等原因所致。
5)如加工後的工件表面局部出現細微波紋,可能是主軸鬆動、電機振動或其它原因造成的,可視具體情況採取相應措施加以解決。