簡介
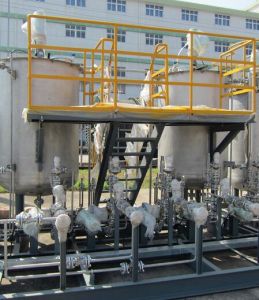
沿革煤焦化技術大規模用於工業生產始於18世紀。當時,傳統的木炭煉鐵因木材日益緊缺而受到限制,需要尋找代用燃料。1735年,在英國用煙煤製得的焦炭煉鐵,這標誌著焦化工業發展的開始。此後,焦化技術不斷變革,從原始的成堆乾餾,經過窯爐、倒焰爐、廢熱式焦爐、蓄熱式焦爐等各發展階段,形成了現代的煉焦過程。
煉焦用煤煉焦用煤最重要的特性是要求具有一定的粘結性,即粉狀煤料加熱時能軟化、熔融,經過膠質狀態,使煤粒彼此結合,固化成堅實的塊狀焦。此外,要求灰分、硫分雜質含量低。按中國煤分類方案,煉焦用煤主要的牌號是焦煤、肥煤、氣煤和瘦煤(見煤化學)。其中只有焦煤能單獨煉成質量較好的焦炭,但這類煤的貯量很少。為擴大煉焦用煤來源和改善焦炭質量,通常採用配煤煉焦。即根據各牌號煤的結焦特性,通過配煤實驗,找到合適的配合比例,煉出合格的焦炭。除了配煤煉焦以外,在煉焦工藝上採用搗固煉焦,配型煤煉焦以及仍在繼續改進的乾燥、預熱煤料直接入爐的工藝,這些提高入爐煤料堆密度的方法,都能有效地增加弱粘煤的用量。此外,在較瘦煤料中配入粘結劑,在較肥的煤料中配入瘦化劑,對於非煉焦用煤則先製成型煤、再進行單獨焦化等,均可獲得有一定強度的塊焦型焦。
成焦過程煤由常溫經過乾餾到焦炭成熟,要經歷煤乾燥和預熱、形成膠質體、縮合結焦等階段。煤在炭化室中成焦過程實際是成層結焦,因為熱量是從兩側爐牆供給,而煤的熱導率又低,平行於爐牆的各層煤料之間有較大的溫度差。這樣,在同一時間內,離爐牆不同距離的各層煤料處於不同的成焦階段,靠近爐牆的煤層先成焦,而後一層層地向炭化室軸線中心推移,當焦炭層從兩側擴展到炭化室中心並會合時,成焦過程即結束,整個成焦時間大約13~18h。
近年來,已提出了一種新的成焦理論,即所謂中間相理論。它是從光學物理的角度研究成焦過程,認為在煤熱解的膠質體液態中存在一種液晶(中間相)結構,而這種液晶是來源於鏡煤,並與焦炭的結構有密切的關係。
煉化學產品
有煤焦油、粗苯、氨等化學產品。各種煉焦化學品的產率與原料煤質和焦化條件有關,每噸乾煤可得煤焦油25~45kg,粗苯7~14kg,氨2.4~4.5kg。煉焦化學品的回收流程(見圖)一般包括煤氣與焦油的分離、氨吸收和粗苯回收幾部分。
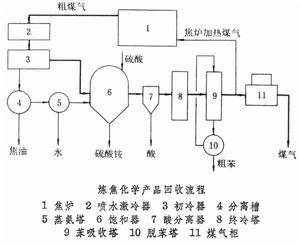
由焦爐導出的粗煤氣經噴水激冷後,在初冷器中冷凝出煤焦油和氨水,經分離槽分離,氨水入蒸氨塔。蒸出的氨和氣體中未溶於水的氨一併在飽和器中與硫酸進行中和反應生成硫酸銨。由飽和器來的氣體,經酸分離器除酸及終冷塔降溫後,入苯吸收塔用洗油吸收氣體中的粗苯,洗油中的粗苯在脫苯塔蒸出。脫出粗苯後的氣體即焦爐煤氣,經脫除有害的硫化物等後,作為燃料煤氣或化工原料。
存在問題
企業數量眾多,規模小,布局分散,產業集中度低,技術裝備整體落後,排放污染重、化工產品回收和綜合利用與集中加工不足,精深加工技術落後,產品品種少,質量水平低,產能過剩、經濟效益不高。
延遲工藝
延遲焦化與熱裂化相似,只是在短時間內加熱到焦化反應所需溫度,控制原料在爐管中基本上不發生裂化反應,而延緩到專設的焦炭塔中進行裂化反應,“延遲焦化”也正是因此得名。
延遲焦化裝置主要由8個部分組成:
⑴焦化部分,主要設備是加熱爐和焦炭塔。有一爐兩塔、兩爐四塔,也有與其它裝置直接聯合的。⑵分餾部分,主要設備是分餾塔。
⑶焦化氣體回收和脫硫,主要設備是吸收解吸塔,穩定塔,再吸收塔等。
⑷水力除焦部分。
⑸焦炭的脫水和儲運。
⑹吹氣放空系統。
⑺蒸汽發生部分。
⑻焦炭焙燒部分。國內選定爐出口溫度為495——500℃,焦炭塔頂壓力為0.15——0.2Mpa。
原料
延遲焦化原料可以是重油、渣油、甚至是瀝青。延遲焦化產物分為氣體、汽油、柴油、蠟油和焦炭。對於國產渣油,其氣體收率為7.0——10%,粗汽油收率為8.2——16.0%,柴油收率為22.0——28.66%,蠟油收率為23.0——33.0%,焦炭收率為15.0——24.6%,外甩油為1——3.0%。焦化汽油和焦化柴油是延遲焦化的主要產品,但其質量較差。焦化汽油的辛烷值很低,一般為51——64(MON),柴油的十六烷值較高,一般為50——58。但兩種油品的烯烴含量高,硫、氮、氧等雜質含量高,安定性差,只能作半成品或中間產品,城經過精製處理後,才能作為汽油和柴油的調和組分。焦化蠟油由於含硫、氮化合物、膠質、殘炭等含量高,是二次加工的劣質蠟油,目前通常摻煉到催化或加氫裂化作為原料。石油焦是延遲焦化過程的重要產品之一,根據質量不同可用做電極、冶金及燃料等。焦化氣體經脫硫處理後可作為制氫原料或送燃料管網做燃料使用。
發展
正是由於延遲焦化的上述優點,使得延遲焦化在中國得到了迅速的發展,這主要是因為:
⑴延遲焦化是解決柴汽比供需矛盾的有效手段。這是由於中國原油普遍偏重,且含蠟量高,柴油的收率低,國內原油的柴油餾分收率比國外原油平均低5——7百分點。因此目前中國每年大約進口80×104t柴油,同時不得不出口30×104t汽油,以求國內供需平衡。其次是由於中國煉油企業二次加工均以催化裂化為主,柴汽比低(延遲焦化為1.94,催化裂化為0.56),因此發展延遲焦化是解決柴汽比供需矛盾,增產柴油的有效辦法。⑵延遲焦化與加氫裂化相比,延遲焦化儘管存在輕質油產品安定性差、操作費用低(加工費約為加氫裂化操作費用的1/2——1/3),使其具有較強的競爭力。
由於延遲焦化具有投資少,操作費用低,轉化深度高等優點,延遲焦化已發展成為渣油輕質化最主要的加工方法之一。因此,在目前中國資金緊張,輕油產品尤其是柴汽比供需矛盾突出的情況下,延遲焦化是解決這一矛盾的較理想的手段之一。
安全技術
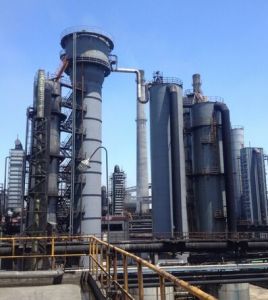
焦化廠一般由備煤、煉焦、回收、精苯、焦油、其他化學精製、化驗和修理等車間組成。其中化驗和修理車間為輔助生產車間。備煤車間的任務是為煉焦車間及時供應合乎質量要求的配合煤。煉焦車間是焦化廠的主體車間。煉焦車間的生產流程是:裝煤車從貯煤塔取煤後,運送到已推空的碳化室上部將煤裝入碳化室,煤經高溫乾餾變成焦炭,並放出荒煤氣由管道輸往回收車間;用推焦機將焦炭從碳化室推出,經過攔焦車後落入熄焦車內送往熄焦塔熄焦;之後,從熄焦車卸入涼焦台,蒸發掉多餘的水分和進一步降溫,再經輸送帶送往篩焦爐分成各級焦炭。回收車間負責抽吸、冷卻及吸收回收煉焦爐發生的荒煤氣中的各種初級產品。
2)焦化安全生產技術及事故預防措施
⑴防火防爆。一切防火防爆措施都是為了防止生產可燃(爆炸)性混合物或防止產生和隔離足夠強度的活化能,以避免激發可燃性混合物發生燃燒、爆炸。為此,必須弄清可燃(爆炸)性混合物和活化能是如何產生的,以及防止其產生和互相接近的措施。
有些可燃(爆炸)性混合物的形成是難以避免的,如易燃液體貯槽上部空間就存在可燃(爆炸)性混合物。因此,在充裝物料前,往貯槽內先充惰性氣體(如氮),排出蒸氣後才可避免上述現象發生。此外,選用浮頂式貯槽也可以避免產生可燃(爆炸)性混合物。其他非正常形成可燃(爆炸)性混合物的原因和預防措施如下:
⑵泄漏。泄漏是常見的產生可燃(爆炸)性混合物的原因。可燃氣體、易燃液體和溫度超過閃點的液體的泄漏,都會在漏出的區域或漏出的液面上產生可燃(爆炸)性混合物。造成泄漏的原因主要有兩個:
一是設備、容器和管道本身存在漏洞或裂縫。有的是設備製造質量差,有的是長期失修、腐蝕造成的。所以,凡是加工、處理、生產或貯存可燃氣體、易燃液體或溫度超過閃點的可燃液體的設備、貯槽及管道,在投入使用之前必須經過驗收合格。在使用過程中要定期檢查其嚴密性和腐蝕情況。焦化廠的許多物料因含有腐蝕性介質,應特別注意設備的防腐處理,或採用防腐蝕的材料製造。
二是操作不當。相對地說,這類原因造成的泄漏事故比設備本身缺陷造成的要多些。由於疏忽或操作錯誤造成跑油、跑氣事故很多。要預防這類事故的發生,除要求嚴格按標準化作業外,還必須採取防溢流措施。《焦化安全規程》規定,易燃、可燃液體貯槽區應設防火堤,防火堤內的容積不得小於貯槽地上部分總貯量的一半,且不得小於最大貯槽的地上部分的貯量。防火堤內的下水道通過防火堤處應設閘門。此閘門只有在放水時才打開,放完水即應關閉。
⑶放散。焦化廠許多設備都設有放散管,加工處理或貯存易燃、可燃物料的設備或貯槽,放散管放散的氣(汽)體有的本身就是可燃(爆炸)性混合物,或放出後與空氣混合成為可燃(爆炸)性混合物。《焦化安全規程》規定,各放散管應按所放散的氣體、蒸氣種類分別集中淨化處理後方可放散。放散有毒、可燃氣體的放散管出口應高出本設備及鄰近建築物4m以上。可燃氣體排出口應設阻火器。
⑷防塵與防毒。煤塵主要產生在煤的裝卸、運輸以及破碎粉碎等過程中,主要產塵點為煤場、翻車機、受煤坑、輸送帶、轉運站以及破碎、粉碎機等處。一般煤場採用噴灑覆蓋劑或在裝運過程中採取噴水等措施來降低粉塵的濃度。輸送帶及轉運站主要依靠安設輸送帶通廓、局部或整體密閉防塵罩等來隔離和捕集煤塵。
破碎及粉碎設備等產塵點應加強密閉吸風,設定布袋除塵、濕式除塵、通風集塵等裝置來降低煤塵濃度。在焦化廠,一氧化碳存在於煤氣中,特別是焦爐加熱用的高爐煤氣中的一氧化碳含量在30%左右。焦爐的地下室、煙道通廓煤氣設備多,閥門啟閉頻繁,極易泄漏煤氣。所以,必須對煤氣設備定期進行檢查,及時維護,煙道通廓的貧煤氣閥應保證其處於負壓狀態。
為了防止硫化氫、氰化氫中毒,焦化廠應當設定脫硫、脫氰工藝設施。過去國內只有城市煤氣才進行脫硫,冶金企業一般不脫硫。至於脫氰,一般只從部分終冷水或氨氣中脫氰生產黃血鹽。隨著對污染嚴重性認識的提高,近年來,各焦化廠已開始重視煤氣的脫硫脫氰問題。為了防止硫化氫和氰化氫中毒,蒸氨系統的放散管應設在有人操作的下風側。
危險因素
1從裝置邊生產邊施工的主要內容分析危險因素裝置運行期間主要需完成的改造工程量為:新焦碳塔塔體、鋼結構預製、安裝;新加熱爐鋼結構預製、安裝及加熱爐的製作;新焦碳塔、加熱爐部分管線的預製和安裝;新增放空塔的安裝;焦碳塔、加熱爐及其他設備基礎施工;新增換熱器、空冷器的安裝和配管;DN500、DN600管線的安裝;泵區、分餾區部分管線、儀表槽盒的安裝等。從施工內容分析主要存在的危險因素有:
1)碳塔、加熱爐、放空塔、換熱器、儀表槽盒安裝時動火作業易引發火災;
2)焦碳塔塔體、鋼結構的安裝、加熱爐的製作、鋼結構、管線的安裝時上下交叉作業易發生設備、人員傷害;
3)碳塔塔體、管線、鋼結構、加熱爐的鋼結構、管線、換熱器、放空塔、DN500、DN600管線安裝吊裝作業,存在吊裝危險及對周圍設備和管線的損壞;
4)焦碳塔、加熱爐及其他動設備基礎土建施工地面開挖,裝置通道出現溝、坑易造成人員傷害;
2從裝置邊生產邊施工的周圍環境分析危險因素
1)焦碳塔、加熱爐的安裝空間較小,安裝高度大,最高達到了102m,吊裝的重量大,最重達到了200t,同時東靠正在運行的爐——30l和塔——201,南側緊鄰裝置的主馬路,北邊是高壓泵房,西側有焦池和沉降池。其施工的主要危險因素有:
①周圍環境多為瓦斯、油氣,一旦瓦斯泄漏或火星掉入沉降池,極易發生火災爆炸事故;
②安裝空間狹窄、施工交叉作業較多,易碰撞周圍設備管線;
③焦碳塔及鋼結構需動用500t大吊車吊裝,吊裝的高度和重量都較大,存在吊裝危險及周圍設備管線的損壞。
2)新增的放空塔南側近鄰氣壓機區,西側靠近加熱爐進料罐V-104,北側有封油罐V-401。下方有運行地汽油泵B-111/112,紫油沖洗油泵B-113/114,封油泵B406/407。其施工地主要危險因素有:
①周圍環境為汽油、柴油、瓦斯、油氣及地漏和下水井,動火時易發生燃燒爆炸;
②吊裝時有一根DN20的汽油線和DN50的風線進行處理,易破壞管線發生火災。
③罐體吊裝屬大型設備吊裝,存在吊裝危險及對周圍設備管線的損壞。
3)新增空冷器和換熱器的安裝在冷換區,高度從7m——22m,周圍主要有換熱器、管線、地漏和下水井以及汽油、柴油、油氣。施工的主要危險因素有:
①地漏、地溝、下水井含油,汽油、柴油、油氣的泄漏,施工動火易引燃;
②施工易碰撞周圍設備管線。
4)DN500、DN600線以及儀表槽盒的安裝,施工的區域多、面廣,從加熱爐到泵區、冷換區、氣壓機區,周圍環境主要有機泵、管線、地漏、地溝、下水井,施工的主要危險因素有:
①地漏、地溝、下水井含油,施工動火易引燃;
②施工易碰撞周圍設備管線;
③周圍環境的油品、油氣、瓦斯較多,施工動火易發生燃燒爆炸;
④施工的機具、設備、管架容易造成人員摔傷、碰傷等人身事故。
3從裝置工藝、操作條件分析危險因素
延遲焦化是在高溫條件下,熱破壞加工渣油從而得到石油焦、汽油、柴油、蠟油和氣體的二次加工裝置。焦化過程是一種熱分解和縮合的綜合過程。裝置屬於高溫(裝置最高溫度可達1000℃以上,介質溫度最高500℃)、高壓(最高壓力3.8MPa),易燃、易爆的裝置。裝置所用原料為常減壓的減壓渣油,其自燃點為230——240℃,而裝置的操作溫度多在300℃以上,一旦泄漏極易發生火災,生產的乾氣和汽油沸點和閃點都很低,與空氣混合均能形成爆炸性混合氣體,其爆炸極限分別為1.5%——15%(V/V)和1.4%——7.6%(V/V)。同時由於其產品柴油、蠟油的自燃點都低於裝置的操作溫度,極易發生火災,存在較大危險。為了加大裝置的處理量,裝置實行單程+18h生焦,生產組織難度較大,操作變動頻繁;同時設備運行時間較長,許多設備超負荷運行;尤其加熱爐運行時間長,存在一定程度的結焦;受改造的影響,生產管理人員較少,部分設備帶病運行。改造施工的危險因素有:燃燒爆炸對人員的傷害以及設備損壞、財產損失。
發展現狀
2014年上半年,全國規模以上焦化企業實現主營業務收入2614.46億元,同比下降6.34%;盈虧相抵實現利潤為-32.89億元,同比下降420%;焦化企業的虧損面達53.04%,虧損企業合計虧損額99.67億元。企業的生存與發展、生產經營陷入前所未有的困境。
據國家統計局統計,1-6月全國累計生產焦炭2.3億噸,同比下降1.1%;全國煤焦油產量約970萬噸,粗(輕)苯產量約245萬噸;焦爐煤氣制甲醇約300萬噸,相比2013年略有下降。
今年以來,焦炭價格持續下跌,出現了多年罕見的局面。2013年,焦炭平均價格為1396元/噸,其中最高價格為1632元/噸,最低價格為1260元/噸。1~6月份,焦炭平均價格為1122元/噸,其中最高價格為1268元/噸,最低價格為1069元/噸。焦炭平均價格同比下降274元/噸,下降幅度近20%;而部分地區焦炭價格最高下跌逾400元/噸。
《焦化行業深度評估及投資前景預測51report》分析認為,焦炭價格大幅下滑,既有煉焦煤價格下降的因素影響,更反映出國內焦炭市場需求疲軟、產能嚴重過剩、定價機制不嚴謹的無序競爭狀態。一些地區煉焦企業開工率較低、企業生產不穩定,對煉焦化工產品的生產和經營效益產生了很大影響;企業平均負債率高達77.8%、銀行貸款難度加大等因素,使多數焦化企業生產經營陷入空前的困境。
目前影響焦化行業總體經濟運行的原因,一方面是全球經濟復甦仍在深刻調整之中,我國巨觀經濟運行反映出較為明顯的下行壓力,焦炭市場需求疲軟,節能減排的剛性約束與日俱增。而另一方面則是焦化行業自身存在的問題,目前煉焦企業產能集中度偏低、規模偏小,產品同質化嚴重。尤其是煤焦油、苯精製等企業,加工規模小,產品質量不高,屬低級粗加工層次,一些煉焦過程中獨有的特種化工產品不能合理、有效地提取。