簡介
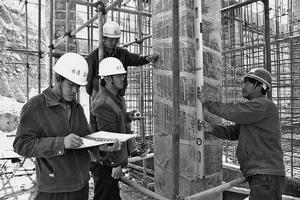
從混凝土的製備、混凝土的運輸、混凝土的澆築、混凝土的養護等幾方面闡述了混凝土工程施工的各個環節的施工要求,並提出了具體的操作方法。
混凝土的製備
混凝土的製備就是根據混凝土的配合比,把水泥、砂、石、外加劑、礦物摻和料和水通過攪拌的手段使其成為均質的混凝土。水泥進場時應對其品種、級別、包裝或散裝倉號、出廠日期等進行檢查,並應對其強度、安定性及其他必要的性能指標進行復驗,其質量必須符合國家標準的規定。當在使用中對水泥質量有懷疑或水泥出廠超過3個月(快硬矽酸鹽水泥超過1個月)時,應進行復驗,並按復驗結果使用。在鋼筋混凝土結構、預應力混凝土結構中,嚴禁使用含氯化物的水泥。
混凝土配合比
混凝土應根據實際採用的原材料進行配合比設計,並按普通混凝土拌和物性能試驗方法等標準進行試驗、試配,以滿足混凝土強度、耐久性和工作性能(坍落度等)的要求,不得採用經驗配合比。同時,應符合經濟、合理的原則。混凝土生產時,砂、石的實際含水率可能與配合比設計存在差異,因此在混凝土拌制前應測定砂、石含水率並根據測試結果調整材料用量,提出施工的配合比。
混凝土攪拌
為了拌制出均勻優質的混凝土,除合理地選擇攪拌機外,還必須正確地確定攪拌制度,即一次投料量、攪拌時間和投料順序等。一次投料量,不同類型的攪拌機都有一定的進料容量,攪拌機不宜超載過多,以免影響混凝土拌和物的均勻性,一次投料量宜控制在攪拌機的額定容量以下。施工配料就是根據施工配合比以及施工現場攪拌機的型號,確定現場攪拌時原材料的一次投料量。攪拌混凝土時,根據計算出的各組成材料的一次投料量,按重量投料。混凝土攪拌的最短時間應滿足規範的規定。投料順序是影響混凝土質量及攪拌機生產率的重要因素。按照原材料加入攪拌筒內的投料順序的不同,常用的投料順序有:一次投料法,二次投料法,兩次加水法。
運輸
混凝土的運輸是指混凝土拌和物自攪拌機中出料至澆築入模這一段運送距離以及在運送過程中所消耗的時間。
對混凝土運輸的要求
在運輸過程中應保持混凝土的均質性,避免產生分離、泌水、砂漿流失、流動性減少等現象。混凝土應以最少的轉運次數和最短的時間,從攪拌地點運至澆築地點,使混凝土在初凝前澆築完畢。混凝土的運輸應保證混凝土的灌築量。對於採用滑升模板施工的工程和不允許留施工縫的大體積混凝土的澆築,混凝土的運輸必須保證其澆築工作的連續進行。
混凝土的運輸方法
混凝土運輸分為地面運輸、垂直運輸和樓地面運輸三種情況。運輸預拌混凝土,多採用自卸汽車或混凝土攪拌運輸車。混凝土如來自現場攪拌站,多採用小型機動翻斗車、雙輪手推車等。混凝土垂直運輸多採用塔式起重機、混凝土泵、快速提升架和井架等。混凝土樓地面運輸一般以雙輪手推車為主。
混凝土的澆築
混凝土澆築
在混凝土澆筑前,應檢查模板的標高、位置、尺寸、強度和剛度是否符合要求;檢查鋼筋和預埋件的位置、數量和保護層厚度,並將檢查結果填入隱蔽工程記錄表;清除模板內的雜物和鋼筋的油污;對模板的縫隙和孔洞應堵嚴;對木模板套用清水濕潤,但不得有積水。
在地基或基土上澆築混凝土時,應清除淤泥和雜物,並應有排水和防水措施。對乾燥的非粘性土,套用水濕潤;對未風化的岩土,套用水清洗,但表面不得留有積水。在降雨雪時,不宜露天澆築混凝土。
混凝土的澆築,應由低處往高處分層澆築。每層的厚度應根據搗實方法、結構的配筋情況等因素確定。
在澆築豎向結構混凝土前,應先在底部填入與混凝土內砂漿成分相同的水泥砂漿;澆築中不得發生離析現象;當澆築高度超過3m時,應採用串筒、溜管或振動溜管使混凝土下落。
在混凝土澆築過程中應經常觀察模板、支架、鋼筋、預埋件、預留孔洞的情況,當發現有變形、移位時,應及時採取措施進行處理。
混凝土澆築後,必須保證混凝土均勻密實,充滿整個模板空間,新舊混凝土結合良好,拆模後,混凝土表面平整光潔。
為保證混凝土的整體性,澆築混凝土應連續進行。當必須間歇時,其間歇時間宜縮短,並應在前層混凝土凝結前將次層混凝土澆築完畢。混凝土運輸、澆築及間歇的全部時間不應超過混凝土的初凝時間。
施工縫
由於技術上的原因或設備、人力的限制,混凝土的澆築不能連續進行,中間的間歇時間需超過混凝土的初凝時間,則應留置施工縫,施工縫的位置應在混凝土澆筑前按設計要求和施工技術方案確定。由於該處新舊混凝土的結合力較差,是結構中的薄弱環節,因此,施工縫宜留置在結構受剪力較小且便於施工的部位。
混凝土的搗實
混凝土的搗實就是使入模的混凝土完成成型與密實的過程,從而保證混凝土結構構件外形正確,表面平整,混凝土的強度和其他性能符合設計的要求。
混凝土澆築入模後應立即進行充分的振搗,使新入模的混凝土充滿模板的每一角落,排出氣泡,使混凝土拌和物獲得最大的密實度和均勻性。
混凝土的振搗分為人工振搗和機械振搗。人工振搗是利用搗棍或插釺等用人力對混凝土進行夯、插,使之成型。只有在採用塑性混凝土,而且缺少機械或工程量不大時才採用人工振搗。採用機械振實混凝土,早期強度高,可以加快模板的周轉,提高生產率,並能獲得高質量的混凝土,應儘可能採用。
養護
混凝土的凝結與硬化是水泥與水產生水化反應的結果,在混凝土澆築後的初期,採取一定的工藝措施,建立適當的水化反應條件的工作,稱為混凝土的養護。養護的目的是為混凝土硬化創造必要的濕度、溫度等條件。常採用的養護方法有:標準養護、熱養護、自然養護,根據具體施工情況採用相應的養護方法。
對高聳構築物和大面積混凝土結構不便於覆蓋澆水或使用塑膠布養護時,宜噴塗保護層(如薄膜養生液等)養護,防止混凝土內部水分蒸發,以保證水泥水化反應的正常進行。
防治措施
現將混凝土工程施工通病的原因及防治措施簡述如下:
(1)蜂窩即混凝土結構局部出現酥鬆、砂漿少、石子多、石子之間形成空隙類似蜂窩狀的窟窿。
產生的原因有:①混凝土配合比不當,或材料計量不準,造成砂漿少、石子多;②攪拌時間不夠,未拌勻,和易性差,振搗不密實;③下料高度太高造成混凝土離析;④未分層下料,振搗不實、漏振或振搗時間不夠;⑤模板縫隙未堵嚴,水泥漿流失;⑥鋼筋較密,使用的石子粒徑過大或坍落度過小等。
防治措施為:①嚴格控制配合比,嚴格計量,經常檢查;②混凝土攪拌要充分、均勻;③下料高度超過2m要用串筒或溜槽;④分層下料、分層搗固、防止漏振;⑤堵嚴模板縫隙,澆築中隨時檢查糾正漏漿情況;
處理措施為:①對小蜂窩,洗刷乾緩笥?:2水泥砂漿抹平壓實;②較大蜂窩,鑿去薄弱鬆散顆粒,洗淨後支模,用高一強度等級的細石混凝土仔細填塞搗實;③較深蜂窩可在其內部埋壓漿管和排氣管,表面抹砂漿或澆築混凝土封閉後進行水泥壓漿處理。
(2)麻面即混凝土局部表面出現缺漿和許多小凹坑、麻點。
產生的原因為:①模板表面粗糙或雜物未清理乾淨,鋼模板隔離劑未刷或未刷均勻,拆模時粘壞混凝土表面;②木模板未充分濕潤,使混凝土表面水分被模板吸收而失水出現麻面;③模板拼縫不嚴、縫隙漏漿;④振搗不實等。
防治措施為:①模板要清理乾淨,澆築混凝土前木模板要充分濕潤,鋼模板要均勻塗刷隔離劑;②堵嚴板縫,澆築中隨時處理好漏漿;③振搗應充分密實;④處理方法,表面做粉刷的可不處理,表面不做粉刷的,應在麻面部位充分濕潤後用水泥砂漿抹平壓光。
(3)孔洞即混凝土構件上有較大空隙、局部沒有混凝土或蜂窩特別大。
產生原因為:①在鋼筋較密或預留孔洞處混凝土下料受阻,未振搗就繼續向上澆築;②混凝土離析嚴重,石子成堆、嚴重跑漿且未認真振搗;③一次下料過多過厚,振動器振不到,形成孔洞;④混凝土內掉人工具、木塊等雜物,擋住混凝土等。
防治措施為:①在鋼筋密集處採用高一強度等級的細石混凝土,認真分層搗固或配以人工插搗;②有預留孔洞處應從其兩側同時下料,認真振搗;③及時清除落人混凝土中的雜物;④處理方法,鑿除孔洞周圍鬆散混凝土,用高壓水沖洗乾淨,立模後用高一強度等級的細石混凝土仔細澆築搗固。
(4)露筋即混凝土內部主筋、副筋或箍筋局部裸露出來,未被混凝土包裹。
產生的原因為:①澆築混凝土時鋼筋保護層墊塊位移、太少或漏放,致使鋼筋緊貼模板;②構件截面小、鋼筋密,石子卡在鋼筋上阻止了砂漿充滿模板;③混凝土配合比不當、離析、露筋處缺漿漏漿;④澆筑前木模板未濕潤,脫模時粘掉保護層混凝土等。
防治措施為:①澆築混凝土前應檢查鋼筋及保護層墊塊位置正確,木模板應充分濕潤;②鋼筋密集時粗集料應選用適當粒徑的石子;③保證混凝土配合比與和易性符合設計要求;
處理方法:表面露筋可洗淨後在表面抹1:2水泥砂漿,露筋較深應處理好界面後用高一級細石混凝土填塞壓實。
(5)縫隙、夾層即混凝土記憶體在成層的鬆散混凝土。
產生原因為:施工縫或後澆帶未經處理就澆築混凝土,或下料高度過高造成混凝土離析。
防治措施為:認真按規定要求處理好施工縫和後澆帶表面,澆築混凝土高度超過2m時要用串筒或溜槽;發生縫隙或夾層現象後要鑿去鬆散混凝土,用水泥砂漿或細石混凝土強力填塞或壓漿。
(6)缺棱掉角
產生原因為:①木模板未充分濕潤,鋼模板未塗隔離劑或刷不勻;②澆築後混凝土養護不好;③拆模過早且拆模後構件受外力碰撞等。
防治措施為:①澆築混凝土前模板要充分濕潤或塗刷隔離劑;②按規定做好混凝土養護工作;③按規定時間拆模並做好成品保護工作。