概述
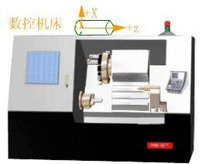
工具機坐標系又稱機械坐標系,用以確定工件、刀具等在工具機中的位置,是工具機運動部件的進給運動坐標系,其坐標軸及運動方向按標準規定,是工具機上的固有坐標系。工具機坐標系原點又叫工具機零點,它是其他所有坐標系,如工件坐標系以及工具機參考點的基準點。其原點位置則由工具機生產廠家設定。一般取在工具機卡盤端面與主軸中心線的交點處。工具機坐標系的原點在工具機製造出來時就已經確定,不能隨意改變。
工具機坐標系是工具機固有的坐標系,工具機坐標系的原點稱為工具機原點或工具機零點。在工具機經過設計、製造和調整後,這個原點便被確定下來,它是固定的點。
工具機坐標系XYZ是生產廠家在工具機上設定的坐標系,其原點是工具機上的一個固定點,作為數控工具機運動部件的運動參考點,在一般數控車床中,原點為卡盤端面與主軸軸線的交點;在一般數控立銑床中,原點為運動部件在X、Y、Z三根坐標軸反方向運動的極限位置的交點,即在此狀態下的工作檯左前角上。
數控裝置上電時並不知道工具機零點,為了正確地在工具機工作時建立工具機坐標系,通常在每個坐標軸的移動範圍內設定一個工具機參考點(測量起點),工具機起動時,通常要進行機動或手動回參考點,以建立工具機坐標系。
工具機參考點可以與工具機零點重合,也可以不重合,通過參數 指定工具機參考點到工具機零點的距離。工具機回到了參考點位置,也就知道了該坐標軸的零點位置, 找到所有坐標軸的參考點,CNC 就建立起了工具機坐標系。
工具機坐標軸的機械行程是由最大和最小限位開關來限定的。 工具機坐標軸的有效行程範圍是由軟體限位來界定的,其值由製造商定義。
確定方法
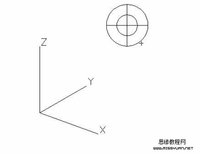
FANUC系統確定工件坐標系有三種方法。
第一種是:通過對刀將刀偏值寫入參數從而獲得工件坐標系。這種方法操作簡單,可靠性好,他通過刀偏與機械坐標繫緊密的聯繫在一起,只要不斷電、不改變刀偏值,工件坐標系就會存在且不會變,即使斷電,重啟後回參考點,工件坐標系還在原來的位置。
第二種是:用G50設定坐標系,對刀後將刀移動到G50設定的位置才能加工。對到時先對基準刀,其他刀的刀偏都是相對於基準刀的。
第三種方法是MDI參數,運用G54~G59可以設定六個坐標系,這種坐標系是相對於參考點不變的,與刀具無關。這種方法適用於批量生產且工件在卡盤上有固定裝夾位置的加工。
航天數控系統的工件坐標系建立是通過G92 Xa zb (類似於FANUC的G50)語句設定刀具當前所在位置的坐標值來確定。加工前需要先對刀,對到實現對的是基準刀,對刀後將顯示坐標清零,對其他刀時將顯示的坐標值寫入相應刀補參數。然後測量出對刀直徑Фd,將刀移動到坐標顯示X=a-d Z=b 的位置,就可以運行程式了(此種方法的編程坐標系原點在工件右端面中心)。在加工過程中按復位或急停健,可以再回到設定的G92 起點繼續加工。但如果出意外如:X或Z軸無伺服、跟蹤出錯、斷電等情況發生,系統只能重啟,重其後設定的工件坐標系將消失,需要重新對刀。如果是批量生產,加工完一件後回G92起點繼續加工下一件,在操作過程中稍有失誤,就可能修改工件坐標系,需重新對刀。鑒於這種情況,我們就想辦法將工件坐標系固定在工具機上。我們發現工具機的刀補值有16個,可以利用,於是我們試驗了幾種方法。
第一種方法:在對基準刀時,將顯示的參考點偏差值寫入9號刀補,將對刀直徑的反數寫入8號刀補的X值。系統重啟後,將刀具移動到參考點,通過運行一個程式來使刀具回到工件G92起點,程式如下:
N001 G92 X0 Z0;
N002 G00 T19;
N003 G92 X0 Z0;
N004 G00 X100 Z100;
N005 G00 T18;
N006 G92 X100 Z100;
N007 M30;
程式運行到第四句還正常,運行第五句時,刀具應該向X的負向移動,但卻異常的向X、Z的正向移動,結果失敗。分析原因懷疑是同一程式調一個刀位的兩個刀補所至。
第二種方法:在對基準刀時,將顯示的與參考點偏差的Z值寫入9號刀補的Z值,將顯示的X值與對刀直徑的反數之和寫入9好刀補的X值。系統重啟後,將刀具移至參考點,運行如下程式:
N001 G92 X0 Z0;
N002 G00 T19;
N003 G00 X100 Z100;
N004 M30;
程式運行後成功的將刀具移至工件G92起點。但在運行工件程式時,刀具應先向X、Z的負向移動,卻又異常的向X、Z的正向移動,結果又失敗。分析原因懷疑是系統運行完一個程式後,運行的刀補還在記憶體當中,沒有清空,運行下一個程式時它先要作消除刀補的移動。
第三種方法:用第二種方法的程式將刀具移至工件G92起點後,重啟系統,不會參考點直接加工,試驗後能夠加工。但這不符合工具機操作規程,結論是能行但不可行。
第四種方法:在對刀時,將顯示的與參考點偏差值個加上100後寫入其對應刀補,每一把刀都如此,這樣每一把刀的刀補就都是相對於參考點的,加工程式的G92起點設為X100 Z100,試驗後可行。這種方法的缺點是每一次加工的起點都是參考點,刀具移動距離較長,但由於這是G00 快速移動,還可以接受。
第五種方法:在對基準刀時將顯示的與參考點偏差及對刀直徑都記錄下來,系統一旦重啟,可以手動的將刀具移動到G92 起點位置。這種方法麻煩一些,但還可行。
數控工具機的工件坐標系確定是影響加工精度的一大因素,對於不同型號的工具機又有不同的要求,只有準確掌握、靈活運用這些知識,才能操作好數控工具機。
設定步驟
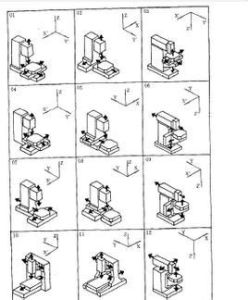
1、工具機坐標系G50
G50指令格式介紹及注意事項
G50 工件坐標系設定
代碼格式:G50 X(U)___ Z(W)____;
代碼功能:
設定當前位置的絕對坐標,通過設定當前位置的絕對坐標在系統中建立工件坐標系(也稱浮動體系)。執行本代碼後,系統將當前位置作為程式零點,執行回程式零點操作時,返回這一位置。工件坐標系建立後,絕對坐標編程按這個坐標系輸入坐標值,直至再次執行G50建立新的工件坐標系。
代碼說明:G50為非模態G代碼;
X:當前位置新的X軸絕對坐標;
U:當前位置新的X軸絕對坐標與執行代碼前的絕對坐標的差值;
Z:當前位置新的Z軸絕對坐標;
W:當前位置新的Z軸絕對坐標與執行代碼前的絕對坐標的差值。
G50代碼中,X(U)、Z(W)均未輸入時,不改變當前坐標值,把當前點坐標值設定為程式零點。
2、對刀原理
因為刀具在安裝時伸出長度不一樣,各有長短,每一把刀轉到切削方向時,刀具刀尖不可能處於同一點上。對刀是為了把每一把刀具刀尖與工件坐標原點的尺寸關係,這種尺寸關係是保證每一把具在加工工件時都是從同一點出發。
四種刀具在安裝到刀架上時,伸出的長度的長短不一,造成每把刀尖不能對正工件同一點上。
3、設定步驟
(1)、第一把刀對刀操作(建立坐標系)
進入MDI方式,輸入“T0100”——按“輸入”——按“循環啟動”。換“手動方式”——“開動主軸”——按“快速”鍵——按“移動鍵(上、下、左、右)”移動刀具靠近工件——按“快速”鍵(重複按“快速”鍵變為慢速)——車削工件端面一刀(不要移動刀具)——進入MDI方式—— “G50”(G50設定坐標系)按“輸入”鍵——“Z0”——按“輸入”鍵——按“循環啟動”(這樣可以對好Z軸的尺寸)——轉換“手動方式”——按“移動鍵(上、下、左、右)”移動刀具去車削工件外圓一刀(不要移動刀具)——“停主軸” ——用遊標卡尺測量工件直徑φ——進入MDI方式—— “G50” (G50設定坐標系)按“輸入”鍵——錄入工件直徑尺寸“Xφ”—— 按“輸入”鍵——按“循環啟動”鍵(這樣可以對好X軸的尺寸)
(2)、第二把刀對刀操作:
“手動方式”——將刀具退刀到安全位置按手動“換刀”鍵,換成第二把刀(檢查刀具補償號為00號刀補)
“手動方式”——按“移動鍵(上、下、左、右)”鍵——快速將刀具移動靠近工件端面——按“手輪方式”(或稱“單步方式”)——選擇移動量“0.01 mm”(手輪每轉動一格,則刀具在該方向移“0.01 mm”)——移動刀具碰到工件端面——按“刀補”鍵(進入刀補設定頁面)——按游標移動鍵,進行游標上下移動,移動游標到002處——按“Z0”——按“輸入”——按“手動方式”——移動刀具靠近工件外圓——按“手輪方式”——移動刀具碰到工件外圓——(按“刀補”鍵)——檢查並移動游標到002處——按“Xφ”——按“輸入”
(3)重複第(1)點可對三、四號刀。
第一、二、三、四把刀檢驗操作:(檢驗操作可在所有刀對完後進行)
(1)進入MDI方式——“T0101”(或T0202、T0303、T0404)——按“輸入”鍵——按“循環啟動”——“G0”——按“輸入”鍵—— “Xφ”——按“輸入”鍵 ——“Z 2”(2mm為刀具安全距離)——按“輸入”——按“循環啟動” 。
(2)輸入“Z60”——按“輸入”——按“循環啟動”。
注意事項:
以上MDI方式的調用為:按“錄入方式”“程式”“下翻一頁”
以上對刀時,刀具號應為T0100、T0200、T0300、T0400不帶刀補。
檢驗刀具時,刀具號應為T0101、T0202、T0303、T0404帶刀補。
加工程式時,刀具號應為T0101、T0202、T0303、T0404帶刀補。
有關指令
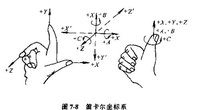
1、絕對尺寸與增量尺寸指令(G90/G91)
G90表示程式段中的尺寸字為絕對尺寸,G91表示程式段中的尺寸字為增量尺寸。G90是以各軸移動的終點位置坐標值編程,G91是以各軸的移動量直接編程。它們均為續效指令。 CNCPOP.COM
注意:有些數控系統沒有絕對和增量尺寸指令,當採用絕對尺寸編程時,尺寸字用X、Y、Z表示;當採用增量尺寸編程時,尺寸字用U、V、W表示。
2、平面選擇指令(G17、G18、G19)
G17、G18、G19分別表示在XY、ZX、YZ坐標平面內進行加工,常用於確定圓弧插補平面、刀具半徑補償平面,它們均為續效指令。有的數控工具機(如數控車床)只在一個平面內加工,則在程式中不必加入平面選擇指令。立式數控銑床大都在XY平面內加工,故G17可以省略。
3、工件坐標系設定指令(G92/G50)
G92指令是規定工件坐標系原點的指令,工件坐標系原點又稱編程零點。當用絕對尺寸編程時,必須先建立一坐標系,用來確定刀具起點在坐標系中的坐標值。
格式:G92 X__ Y__ Z__;(數控銑床、加工中心)
G50 X__ Z__;(數控車床)
坐標值X、Y、Z為刀位點在工件坐標系中的初始位置。執行G92指令時,工具機不動作,即X、Y、Z軸均不移動,但CRT顯示器上的坐標值發生了變化。 本文來自CNCPOP
注意:有些數控工具機直接採用零點偏置指令(G54~G59)來設定工件坐標系。 cncpop.com
4、零點偏置指令(G54~G59) CNCPOP.COM
G54~G59可設定的零點偏置給出工件零點在工具機坐標系中的位置(工件零點以工具機零點為基準的偏移量)。工件裝夾到工具機上後,通過對刀求出偏移量,並通過操作面板輸入到規定的數據區,程式可以通過選擇相應的功能G54~G59激活此值。