分料膠帶機的特點
1、分料切換點線路數量不受限制
採用傳統的三通或四通分料器時,上游一條膠帶機最多能向下游兩條或三條運輸線路進行分配。如果下游運輸線路為多條膠帶機,則需要在原有三通或四通分料器下部再增加三通或四通分料器進行再分配。因此,會增加轉運站高度及上游膠帶機的提升高度和傳動功率,從而增加工程投資及上游膠帶機的長期運行費用。而採用“分料膠帶機”(正、反轉及走行),可實現上游一條膠帶機向下游多條運輸線路(數量不限)進行分配。多點分配的“分料膠帶機”需要加大車走行機構;兩點分配則可將“分料膠帶機”直接固定在鋼平台上。
2、轉運落差小
傳統的三通或四通分料器因受其結構影響,轉運落差根據膠帶機的大小一般在4.5~8m。尤其是轉運粘滯性較大、含水率較高的物料時,需要將分料器的α角設定在65度~70度(以防粘料,造成分料器堵塞),因此更增大了轉運落差。落差大不僅造成易碎物料過度破損(轉運落差在3.5m~4m時,燒結礦、焦炭等易碎物料,每一次跌落破損0.9%~1%,而且對下游設備產生衝擊損壞。
新型“分料膠帶機”由於取消了分料漏斗,而代之以分料皮帶,其每一級落差可根據膠帶機的大小控制在1.5m~2m之間(見圖1)。
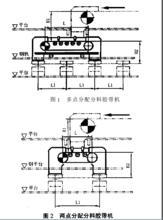
因而能有效地減小物料的跌落高度。對於燒結礦、焦炭等易碎物料的轉運(在運輸工藝中,易碎物料原則上必須採用低交方式轉運)非常合適,同時還能有效地保護下游設備免受衝擊,並可減小轉運站高度及上游膠帶機的提升高度。
3、垂直落料,不易粘結
與傳統的三通或四通分料器不同,“分料膠帶機”是通過可逆皮帶或移動皮帶向下游皮帶分料,故而物料可垂直落到下游皮帶上,從而有效地避免了粘性物料在溜管內的粘結和堵塞。
4、維護量小、易檢修
傳統的三通或四通分料器的易損件為溜管、分料翻板和轉動軸。它們均為隱蔽件,檢修空間狹小,且多為架空布置,檢修困難。當運輸磨琢性較大的物料時,檢修周期約為7~10天;運輸磨琢性小的物料時,檢修周期約為15~20天,每次檢修時間約為6~8小時。尤其是在冬天,其液壓傳動機構受寒冷氣候的影響,經常失靈。而“分料膠帶機”的所有結構無隱蔽件,並在頭、尾部護罩上留有若干檢視門,易觀察,可及時發現和排除故障。其易損件為膠帶,膠帶採用薄帶芯(可減少其層間摩擦,抗疲勞性能好)加厚耐磨上膠面,大大提高了其使用壽命。而且採用了一次成型的筒狀膠帶,支架採用分體法蘭連線形式,檢修時可直接套裝,故而能有效地縮短檢修時間。用於運輸磨琢性較大的物料時,檢修周期約為75~90天;運輸磨琢性小的物料時,檢修周期約為150~180天,每次檢修時間約為2~3小時。
當然,“分料膠帶機”的檢修周期要受運輸量、單位時間內運輸頻度、物料的磨琢性以及帶速等因素影響,但總體來說,其檢修周期較長,維護量小,且檢修時間短,最大程度地節省了檢修費用,有效地保證了正常生產。
5、設備可靠性好
“分料膠帶機”是結合生產工藝特點特殊設計製造的,它具有膠帶機運輸量大,運行平穩,維護量小,易檢修,經濟,可靠,適用範圍廣等特點。在大車走行以及正、反轉分配運行中,工作順暢,完全解決了傳統的三、四通分料器翻板與外部溜管的活動間隙內易卡料,造成卡阻,損壞設備或造成翻板運行不到位,在其間隙內產生漏料,以及分料斗易凍結、粘結、堵塞等問題。在物料的轉運分配作業中,其可靠性是傳統分料設備無可比擬的。
6、切換輸送不混料
輸送是原料準備最基本的作業環節之一,尤其是在冶金行業的綜合原料場,多種物料經常通過單一或複合輸送線分送給不同用戶,工藝上嚴格要求每次切換物料不允許混料。以往採用傳統的分料器分配磨琢性較大的物料時必須加階梯形料襯,而分配粘性較大的物料時,物料易粘結在溜管壁上,造成每次換向分料及單向運輸再啟動時將前次物料帶入本次運輸物料中,造成混料。而“分料膠帶機”在正、反轉運行中,通過頭、尾部清掃器可及時將膠帶面上的殘餘物料清理乾淨。反向換料及單向送料再啟動時均不會帶有前一次的余料。避免了換料過程中混料引起的物料成分波動,滿足了物料轉運中最關鍵的質量要求。
分料膠帶機各零部件確定原則及結構組成
1、驅動裝置及頭、尾部下料點中心距確定
推薦驅動裝置採用外置式,儘量不要採用電動滾筒。多點分配時,根據上游及下游膠帶機中心距共同確定頭、尾部下料點中心距;兩點分配時,根據下游膠帶機中心距來確定。
2、頭部傳動滾筒、尾部改向滾筒直徑確定原則
因為分料膠帶機頭、尾部中心距很小,需採用非標設計的小直徑滾筒,才能滿足短中心距的要求,同時中間還留有放置緩衝裝置的位置,且可保證其整機結構輕巧。所以B=500~650mm分料膠帶機的頭、尾部滾筒直徑需控制在320mm,B=800~100mm分料膠帶機的頭、尾部滾筒直徑需控制在400mm,B=1200~1400mm分料膠帶的機頭、尾部滾筒直徑需控制在500mm。
3、緩衝裝置確定
緩衝裝置要求必須採用輥徑大於180mm的橡膠(或彈簧板式)平行重型緩衝托輥。緩衝托輥需密排,以減小膠帶撓度,從而減輕膠帶機運行阻力。
4、頻寬及帶厚的確定原則
因為緩衝裝置採用平行緩衝托輥,單位寬度截面上的運輸量較槽形緩衝托輥要小。考慮到運輸量的問題,“分料膠帶機”的寬度要比上、下游膠帶機放大一級。又因“分料膠帶機”的長度較小,運轉一周所需時間短,故單位時間內其單位長度上所受到的衝擊次數多,因此上帶面應儘量採用耐磨厚膠層,以增加膠帶的使用壽命,延長檢修周期,減少檢修次數。
5、拉緊裝置
因為“分料膠帶機”採用正、反轉給料形式,不能像普通皮帶機一樣採用尾部拉緊裝置來保證皮帶的張緊程度。因此,設計時在尾輪內側支架上設定了頂絲張緊裝置(膠帶機短,張緊行程很小),既便於安裝,又便於操作和檢修。
6、膠帶防跑偏措施
因為“分料膠帶機”中心距小,無法採用調心托輥,調心方式是利用頂絲張緊裝置調整尾輪左、右張緊度,以達到調心的目的;另外在中間架兩側加若干組立式擋輥防止膠帶跑偏。
7、轉運密封
“分料膠帶機”系轉運分配設備,物料因轉運落差,不可避免的會產生揚塵。為了保護崗位環境,凡是靜態縫隙點都採用剛性密封,動態縫隙點則採用柔性密封,從而做到整機全密封。
8、擋料板
因為“分料膠帶機”較短,中間緩衝托輥又呈水平布置,故運行時物料在帶面上的堆積高度較大。為了避免運輸量較大時出現撒料,皮帶兩側均設定了較高的擋料板。擋料板兩端伸入至頭、尾部滾筒中心線處,有效地防止了撒料。
9、整機走行
“分料膠帶機”為多點分配時,需設定大車走行機構,其軌道安裝在鋼平台上,走行機構的定位或對中採用接近開關控制;兩點分配時,直接將其固定在鋼平台上。
10、膠帶張力
“分料膠帶機”整體結構較小,因此選用功率小,膠帶張力也較小。在選用膠帶時,要儘量減少帶芯層數(一般控制在3層)。因為在帶速一定的情況下,“分料膠帶機”越短,膠帶通過頭尾、部滾筒越頻繁,交變頻率很高,且因其頭部傳動滾筒、尾部改向滾筒直徑較小,多層帶芯膠帶在頻繁通過頭、尾部滾筒時,小曲率半徑易使帶芯產生層間摩擦。因此,減少帶芯層數,有利於減少膠帶在通過頭、尾部滾筒時產生的帶芯層間摩擦,提高膠帶的使用壽命。
11、機架、頭部漏斗及頭部護罩結構
“分料膠帶機”支架採用上、下分體,法蘭連線形式。頭部漏斗及頭部護罩在與頭、尾部滾筒側面銜接處開半圓豁口,用法蘭封堵,便於在檢修時筒狀膠帶的更換。由於設備長度小,受料時為防止物料濺入另一側,在防塵罩入口處加設了一個柔性擋簾。