類型
有油型和水型兩種。
油型
又分礦物油切削油(或複合油)、極壓切削油、活性切削油三種。所用的礦物油有煤油、柴油、輕質潤滑油餾分。礦物油中加入一定比例的動、植物油(5%~10%)便是複合油,適用於輕負荷的切削加工。極壓切削油中加有硫、磷、氯極壓添加劑,以滿足黑色金屬,齒輪等深度金屬加工的要求。活性切削油中加入活性硫等化合物,用於高合金材料深孔鑽、攻絲等深度加工。
水型
可進一步分成通用型、防鏽型、極壓型和透明型四種。前三種均為石油潤滑油基礎油中加入乳化劑及其他添加劑(抗磨劑等)的水包油型乳化液。透明型可以是加入少量潤滑油或不加入潤滑油(即全水基合成切削液)的透明液體。水型切削油是近數十年來發展較快、使用較廣的品種。
還有一種完全是水的切削液,即電解強鹼水。強鹼水設備生產的強鹼水,PH最高可達13--13.5。
與切削油和水性切削液相比,鹼性電解水的原料是100%的水,來源穩定且價格低廉,成本僅是水性切削液的十分之一甚至更少。具有優越的冷卻、清洗性能,不發泡,容易涮洗,同時鹼性電解水又具有良好的防鏽性能。而且切削油和水性切削液中都含有有機化合物、油性劑、界面活性劑等成分,對人體健康和環境有破壞作用,而鹼性電解水對人體和環境無害,是一種環保、低成本的切削液,在高速淺層切削上可以完全取代水性切削液。
選用分析
切削油的選用原則必須滿足切削性能和使用性能的要求,即應具備良好的潤滑、冷卻、防鏽和清洗性能,在加工過程中能滿足工藝要求,減少刀具損耗,降低加工表面粗糙度,降低功率消耗,提高生產效率。同時應考慮使用的安定性。因此切削液的選用應遵循以下原則:
1、切削液應無刺激性氣味,不含對人體有害添加劑,確保使用者的安全。
2、切削液應滿足設備潤滑、防護管理的要求,即切削液應不腐蝕工具機的金屬部件,不損傷工具機密封件和油漆,不會在工具機導軌上殘留硬的膠狀沉澱物,確保使用設備的安全和正常工作。
3、切削液應滿足工件工序間的防鏽要求,不鏽蝕工件。加工銅合金時,不應選用含硫的切削液。加工鋁合金時,應選用PH值為中性的切削液。
4、切削液應具有優良的潤滑性和清洗性能。選擇最大無卡咬負荷值高、表面張力小的切削液,並經切削液試驗評定。
5、切削液應具有較長的使用壽命,這對加工中心尤為重要。
6、切削液應儘量適應多種加工方式和多種工件材料。
7、切削液應低污染,並有廢液處理方法。
8、切削液應價格便宜,配製方便。
適用領域
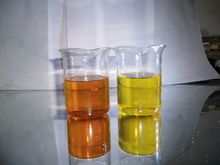
適用於鑄鐵、合金鋼、碳鋼、不鏽鋼、高鎳鋼、耐熱鋼、模具鋼等金屬製品的切削加工、高速切削及重負荷切削加工。包括車、銑、鏜、高速攻絲、鑽孔、鉸牙、拉削、滾齒等多種切削加工。一種特種潤滑油,由低粘度潤滑油基礎油加入部分動植物油脂及抗氧劑、抗磨劑、防鏽劑等經調合製得。有油型
和水型兩種。後者含水80%~95%,具有乳化能力,一般稱切削液。切削油在金屬切削加工過程中用於潤滑和冷卻加工工具和部件。
功能
在金屬切削加工中,切削每次都在新生面上進行,速度變化每分鐘數毫米至數百米,壓力高達2~3GPa。切削時除外摩擦外,還有刀具與切入金屬內部的分子內摩擦,切削區界面溫度可達600~800℃。這樣的高溫高壓會使刀具的強度和硬度降低,因此切削油必須兼具冷卻、潤滑、清洗和防鏽四個作用。
冷卻
表現在降低刀尖溫度、抑制被切削材料和刀具的熱膨脹,以提高操作性能和加工精度。水的熱導率和比熱容均比油大,粘度也比油小,故乳化液的冷卻性能遠比油好。
潤滑
減少前刀面與屑、後刀面與加工表面的摩擦,防止發生粘著、積瘤、鱗刺或冷焊,以減少功率消耗和刀具磨損,並得到較好的表面光潔度。
防鏽
為防止大氣中的水和氧氣對新加工表面的鏽蝕,在切削油中要加入防鏽劑,提高切削油的防鏽性能,以滿足工件在加工過程中短期防護之需。
清洗
利用液流衝去細小的切屑和粉末,防止粘結,以保證刀具和工件連續加工。在磨加工中,清洗性差的切削油會導致堵塞砂輪,使磨削區溫度升高和燒壞工件。使用低粘度油和加入表面活性劑能提高切削的清洗性。
除上述性能外,切削液還應具有乳液在加工過程中的穩定性、不分層、抗硬水和抗細菌污染變質的能力。
來源
眾所周知,切削液是金屬切削加工的重要配套材料。人類使用切削液的歷史可以追溯到遠古時代。人們在磨製石器、銅器和鐵器時,就知道澆水可以提高效率和質量。在古羅馬時代,車削活塞泵的鑄件時就使用橄欖油,16世紀使用牛脂和水溶劑來拋光金屬盔甲。從1775年英國的約翰·威爾金森(J.wilkinson)為了加工瓦特蒸汽機的汽缸而研製成功鏜床開始,伴隨出現了水和油在金屬切削加工中的套用。到1860年經歷了漫長發展後,車、銑、刨、磨、齒輪加工和螺紋加工等各種工具機相繼出現,也標誌著切削液開始較大規模的套用。
19世紀80年代,美國科學家就已首先進行了切削液的評價工作。 F·W·Taylor發現並闡明了使用泵供給碳酸鈉水溶液可使切削速度提高對30%~ 40%的現象和機理。針對當時使用的刀具材料是碳素工具鋼,切削液的主要作用是冷卻,故提出“冷卻劑”一詞。從那時起,人們把切削液稱為冷卻潤滑液。
切削液按油品化學組成分為非水溶性(油基)液和水溶性(水基)液兩大類。
水基的切削液可分為乳化液、半合成切削液和合成切削液。
乳化液的成分:礦物油50-80%,脂肪酸0-30%,乳化劑15-25%,防鏽劑0-5%,防腐劑<2%,消泡劑<1%
半合成:礦物油0-30%,脂肪酸5-30%,極壓劑0-20%,表面活性劑0-5%,防鏽劑0-10%
區別
油基切削液
油基切削液的潤滑性能較好,冷卻效果較差。水基切削液與油基切削液相比潤滑性能相對較差,冷卻效果較好。慢速切削要求切削液的潤滑性要強,一般來說,切削速度低於30m/min時使用切削油。
含有極壓添加劑的切削油,不論對任何材料的切削加工,當切削速度不超過60m/min時都是有效的。在高速切削時,由於發熱量大,油基切削液的傳熱效果差,會使切削區的溫度過高,導致切削油產生煙霧、起火等現象,並且由於工件溫度過高產生熱變形,影響工件加工精度,故多用水基切削液。
乳化液把油的潤滑性和防鏽性與水的極好冷卻性結合起來,同時具備較好的潤滑冷卻性,因而對於大量熱生成的高速低壓力的金屬切削加工很有效。與油基切削液相比,乳化液的優點在於較大的散熱性,清洗性,用水稀釋使用而帶來的經濟性以及有利於操作者的衛生和安全而使他們樂於使用。實際上除特別難加工的材料外,乳化液幾乎可以用於所有的輕、中等負荷的切削加工及大部分重負荷加工,乳化液還可用於除螺紋磨削、槽溝麻削等複雜磨削外的所有磨削加工,乳化液的缺點是容易使細菌、黴菌繁殖,使乳化液中的有效成分產生化學分解而發臭、變質,所以一般都應加入毒性小的有機殺菌劑。
化學合成切削液的優點在於經濟、散熱快、清洗性強和極好的工件可見性,易於控制加工尺寸,其穩定性和抗腐敗能力比乳化液強。潤滑性欠佳,這將引起工具機活動部件的粘著和磨損,而且,化學合成留下的粘稠狀殘留物會影響機器零件的運動,還會使這些零件的重疊面產生鏽蝕。
水基切削液
一般在下列的情況下應選用水基切削液:
對油基切削液潛在發生火災危險的場所;
高速和大進給量的切削,使切削區超於高溫,冒煙激烈,有火災危險的場合。
從前後工序的流程上考慮,要求使用水基切削液的場合。
希望減輕由於油的飛濺護油霧和擴散而引起工具機周圍污染和骯髒,從而保持操作環境清潔的場合。
從價格上考慮,對一些易加工材料護工件表面質量要求不高的切削加工,採用一般水基切削液已能滿足使用要求,又可大幅度降低切削液成本的場合。
當刀具的耐用度對切削的經濟性占有較大比重時(如刀具價格昂貴,刃磨刀具困難,裝卸輔助時間長等);工具機精密度高,絕對不允許有水混入(以免造成腐蝕)的場合;工具機的潤滑系統和冷卻系統容易串通的場合以及不具備廢液處理設備和條件的場合。均應考慮選用油基切削液。
參考配方
組份名稱 | 投料量(g/L) |
礦物油 | 8%~20% |
妥爾油 | 1~8% |
PEG600 | 4%~5% |
油酸三乙醇胺 | 5%~6% |
氯化石蠟 | 1~3% |
脂肪醇聚氧乙烯醚 | 3%~5% |
NP-10 | 3~5% |
乙二胺 四乙醇 | 1%~2% |
有機矽消泡劑 | 1~2% |
酒石酸鈉 | 1~2% |
石油磺酸鈉 | 4%~5% |
水 | 餘量 |
切削油(液)在使用過程中常出現的問題及解決措施
現象 | 原因 | 措施 |
摩擦磨損導致 刀具耐用度 降低( 後刀面 磨損急劇增大) | 由於刀尖處潤滑性不足產生 機械磨損 | 選用脂肪含量多的油性切削油 把活性切削油換成不活性 油基切削油 若 切削液 明顯 劣化 、應換用新液 增大供液量和供液壓力,直接向後刀面供液 使用水性切削液的場合,選用含有潤滑性優異的 極壓添加劑 的乳化型切削液,並在高濃度下使用 |
刀尖粘結, 積屑瘤 破碎 | 由於抗粘性能不佳,以至於積屑瘤異常增大;由於積屑瘤破碎引起刀刃損傷與剝落,由此產生摩擦磨損 | 換用活性強的 切削液 檢查 活性度 ,如果降低了,應補加添加劑(油性切削油) 將水性切削液換成油性切削油 |
過度發熱導致 刀具耐用度 降低(刀尖軟化、熔融、切屑變色) | 對於刀尖部分蓄熱的冷卻不充分 | 換油性切削油為水性切削液 增大供油量和供油壓力 保持切削油的溫度(不升高) |
加工精度 不好 | 冷卻不均或不充分 由於 積屑瘤 的附著導致過大切深 | 充分供油 保持切削溫度一定 換用抗粘性優異的油性切削油 補充 極壓添加劑 (油性切削油) |
從油性切削油換成水性 切削液 時, 刀具耐用度 降低 | 由於切削液種類固有的性能差別引起潤滑性不足 | 將含極壓劑的乳化型切削液在高濃度下使用 將水性切削液的原液向刀具噴霧供給 |
使用過程中刀具耐用度逐漸變短 | 由於漏洞混入引起添加劑濃度降低 由於只補給水造成濃度降低 | 換用新液 補充添加劑 採取防止漏油的措施 檢查使用液嘗試並補充原液 |
由於破損使 刀具耐用度 降低 | 由於斷續冷卻的熱沖產生破損 | 改善供液法,擴大供液範圍 換用冷卻性差的 切削液 硬質合金刀具斷續切削時不用切削液 |
已加工表面惡化(粗糙、撕裂、拉傷) | 由於潤滑不充分而附著 積屑瘤 切屑粘結引起拉傷(死加工) | 換用抗 粘結性 好的切削液 改善過濾方法以除去微細切屑 改善供液法以求不出現“斷油”現象 |
鑽孔、 鉸孔 、攻絲的粘結與破損 | 刀刃部產生斷油現象,潤滑不足 | 增大供液量 換用潤滑性和抗粘結性好的 切削液 在水性切削液的場合檢查稀釋倍率,並在高濃度下使用。 |
技術參數
型號 | 粘度@40℃ cSt | 閃點 | 顏色 | 適用材料 | 說明 |
| 15 | 170 | 棕色 | 鐵、合金鋼、不鏽鋼高鎳鋼、模具鋼等 黑色金屬 | 透明深棕色,含多量極壓添劑,低油霧、具良好滲透冷卻性。適用各種高硬度金屬於深孔鑚、槍鑚、 攻絲 、 拉削 等重負載及高速切削加工。該產品不適合銅加工。 |
| 32 | 196 | 深棕色 | 鐵、合金不鏽鋼、高 鎳鋼 、 耐熱鋼 等 黑色金屬 | 含多量高活性極壓劑,專用於難切削金屬的重負荷加工,提供極佳的產品 表面光潔度 ,延長刀具使用壽命。適合高硬度金屬的多工序加工,用於 自動車床 及 加工中心 。 |
| 17.5 | 185 | 淡黃透明 | 鑄鐵、不鏽鋼、合金鋼、高低碳鋼、高抗力鋼 | 是一種由深度精製基礎油調製而成的油性切削油,含有非 活性硫 及氯 極壓添加劑 ,適用與多種材料的 高速切削 ,鑚孔、 攻絲 、 拉削 、拉扎、滾齒及刨齒等加工。 |
| 31 | 198 | 淺黃透明 | 鑄鐵、不鏽鋼、合金鋼、高低碳鋼、高抗力鋼 | 是一種由精製礦物油及非 活性硫 、氯 極壓添加劑 調製而成的油性 切削液 ,適用於多種材料的攻絲、鑚削、 銑削 、 車削 、等加工。 |
| 22 | 183 | 淺黃 | 鐵、合金鋼系不鏽鋼、耐熱銅、 工具鋼 、 銅合金 、鋁合金、鋁等 | 淺黃色透明、低油霧、環保配方、不含硫/氯類添加劑,對有色金屬無腐蝕,並對鐵 類金屬 有1-3個月的防鏽。專利技術,對銅、鋁及不銹銅、碳銅均有極佳效果適中粘度,可同時用於液壓/道軌/齒輪潤滑,用途廣泛。 |
| 14 | 185 | 微黃 | 鎂、 鎂鋁合金 、鋁合金、 銅合金 、碳鋼 | 專為鎂鋁、銅等及有色金屬而設計的專用切削油,含特殊添加劑,杜絕鎂合金加工中的火災隱患,並防止有色金屬氧化。低氣味,低粘度,低油霧。 |
| 5 | 130 | 淺黃 | 鑄鐵、碳銅、合金鋼、黑色及有色金屬 | 不含硫和氯,極低粘度,快速散熱及沖洗功能,防止 鐵屑 粘附在砂輪上,並具有出色的防鏽功能。優異減磨性能,推薦用於多種材質的研磨和高精密度的研磨加工。 |
| 32 | 198 | 淺黃 | 所有金屬 | 新世紀最新科技,系採用納米技術合成的百分百耐極壓抗磨添加劑,淺黃透亮,無速激氣味。可與任何油品相溶。 不含硫、氯成份,對任何金屬無腐蝕,對人體無影響。 以1-10%的比例添加在切削油、 齒輪油 、發動機油、液壓等中,可以使油品的抗磨抗壓極壓性能成倍提高。 |