概念
高爐高碳錳鐵:高爐法是高碳錳鐵生產最早採用的一種方法。該法以焦炭作為還原劑和熱源,白雲石或石灰作熔劑,用高爐生產高碳錳鐵。
高爐法是把錳礦、焦炭和石灰等料分別加入高爐內進行冶煉、得到含錳52%~76%/含磷0.4%~0.6的高爐錳鐵。由於高爐與電爐高碳錳鐵唯一的區別是熱源不同,所以兩者的爐體結構、幾何形狀及操作方法不一樣,但兩爐子冶煉高碳錳鐵的原理是相同的。
但是,兩種爐子使用同一種錳礦冶煉使得到的產品磷含量不一樣,高爐產品越高於電爐產品0.07%~0.11。這是由於高爐冶煉的爐料組成中的焦炭配量為電爐冶煉時的5~6陪,因此焦炭中有更多的磷轉入合金內,而且高爐冶煉時的爐膛溫度較低,因而冶煉過程中磷的揮發量較電爐低約10%
高碳錳鐵最早是採用高爐生產的,其產量高,成本低,目前國內外還在廣泛用。我國江西新余鐵合金廠、山西陽泉鐵合金廠為高爐生產高碳錳鐵的定點廠家。
用途
高爐高碳錳鐵:用於煉鋼作脫氧劑或合金元素添加劑。
牌號及化學成分表
類別 | 牌號 | 化學成分(%) | |||||
Mn | C | Si | P | S | |||
Ⅰ | Ⅱ | Ⅰ | Ⅱ | ||||
≤ | |||||||
高爐高彈錳鐵 | FeMn78 | 75.0~82.0 | 7.5 | 1 | 2 | 0.3 | 0.5 | 0.03 |
FeMn74 | 70.0~77.0 | 7 | 1 | 2 | 0.4 | 0.5 | 0.03 |
FeMn68 | 65.0~72.0 | 7 | 1 | 2.5 | 0.4 | 0.6 | 0.03 |
FeMn64 | 60.0~67.0 | 7 | 1 | 2.5 | 0.5 | 0.6 | 0.03 |
FeMn58 | 55.0~62.0 | 7 | 1 | 2.5 | 0.5 | 0.6 | 0.03 |
冶煉原料
高爐錳鐵冶煉用原料主要有錳礦、焦炭和熔劑。
錳 礦
高爐冶煉用的錳礦有氧化礦、碳酸鹽礦、焙燒礦和燒結礦。
礦石中的錳是高爐錳鐵冶煉中的主要回收元素。錳礦石含錳量的高低直接影響錳鐵冶煉技術經濟指標。高爐生產實踐表明,錳礦中含錳量波動1%,焦比波動50~80kg,產量波動3%~5%,因此對入爐礦中含錳量要求越高越好。
錳礦中SiO2的含量是影響渣量的主要因素。據分析,入爐錳礦中的m(SiO2)/m(Mn)波動10%,相當於含錳量波動1%,應當儘量選用m(SiO2)/m(Mn)低的礦石入爐。我國各廠家入爐混合礦的m(SiO )/m(Mn)一般控制在0.3~0.8。
錳礦中的m(Mn)/m(Fe)決定產品的含錳量,生產不同牌號的錳鐵,需用不同m(Mn)/m(Fe)比值的錳礦。
錳礦中的磷是高爐錳鐵生產中的控制元素,希望越低越好。磷在鋼鐵產品中大都屬有害元素。磷在高爐冶煉中理論上百分之百還原。因此錳鐵產品中的磷含量取決於礦石、焦炭中的含磷量。但在高爐冶煉中,Mn的回收率和錳礦石的品位會在較大範圍內變化,因此產品中的含磷量也隨之變化。
錳礦石中允許的含磷量按下式計算:
w(P礦)={[P]/np-(w′pK+w″pФ+w″pD)}÷H
式中 w(P礦)——入爐錳礦石的含磷量,%;
[P]——產品中允許含磷量上限,%;
np——磷在高爐中的還原率(理論上100%,實際上80%左右);
w′p,w″p,w″p——分別為焦炭,熔劑 和其他附加物的含磷量,%;
H,K,Ф,D——分別為冶煉每噸錳鐵所需礦石、焦炭、熔劑和其他附加物單耗,kg/t.
某廠高爐錳鐵冶煉對入爐錳礦的m(Mn)/m(Fe)及m(P)/m(Mn)要求下見表。
牌號 | 錳鐵成分(%) | 對入爐錳礦要求 | ||||
Mn | P | M(Mn) | M(P)/m(Mn) | |||
Ⅰ | Ⅱ | M(Fe) | Ⅰ | Ⅱ | ||
≥ | ≤ | ≥ | ≤ | |||
FeMn78 | 78 | 0.33 | 0.5 | 6.22 | 0.00375 | 0.00493 |
FeMn74 | 74 | 0.38 | 0.5 | 4.68 | 0.00396 | 0.00521 |
FeMn68 | 68 | 0.4 | 0.6 | 3.59 | 0.00441 | 0.00662 |
FeMn64 | 64 | 0.4 | 0.6 | 2.9 | 0.00469 | 0.00703 |
FeMn58 | 58 | 0.5 | 0.6 | 2.38 | 0.00625 | 0.0075 |
錳礦中的鉛在冶煉時易還原也易揮發,還原後沉積在爐底,嚴重時會破壞爐底,爐溫高時易揮發,在高爐上部結瘤。一般為要求錳礦中Pb含量<0.1%。錳礦中的鋅易揮發在高爐上部沉積,對爐牆磚襯和爐殼有破壞作用,也可能和爐襯混合形成爐瘤。通常要求錳礦中Zn含量<0.2%。
錳礦石入爐粒度一般為5~60mm,含粉率要求小於5%。
焦 炭
焦炭在高爐冶煉中不但是還原劑和發熱劑,而且是整個高爐料柱的骨架。焦炭質量的好壞一方面要看其化學成分,另一方面要看其物理性能——粒度和強度。錳鐵高爐冶煉用焦炭主要有冶金焦、氣煤焦和土焦。不同焦炭質量差別較大,使用時應綜合考慮。
對焦炭的基本技術要求:
(l)高而穩定的固定碳含量。固定碳含量越高,作為還原劑和發熱劑的能力越大,對降低焦比,改善技術經濟指標有利。
(2)較低的灰分可以減少渣量及灰分帶入的磷含量。
(3)較高的機械強度,可防止和減輕焦炭在爐內下降過程中產生粉末、惡化料柱透氣性。揮發分低的焦炭機械強度比較好。
焦炭中的水分雖然對高爐冶煉過程無影響,但水分波動會影響配料的準確性。因此,希望焦炭水分穩定為好。焦炭入爐粒度一般為20~60mm。
熔 劑
高爐錳鐵冶煉所用熔劑為石灰石、生石灰、白雲石等。
對石灰石和生石灰要求CaO含量越高越好。CaO含量高,帶入的渣量相對減少。使用白雲石調節渣時,要求白雲石的MgO含量儘量高。
熔劑入爐粒度要求:石灰石和白雲石15~75mm,生石灰為20~l00mm,小高爐偏下限,中型高爐偏上限。
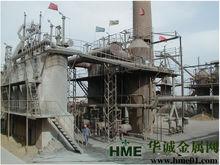
冶煉操作
錳鐵高爐冶煉操作與生鐵高爐相似,但錳鐵高爐具有以下不同特點:
①錳礦中MnO含量較鐵礦中FeO含量低,MnO較FeO難還原。冶煉過程中渣量大,錳的回收率較低。
②由於錳與氧的親和力比鐵強,還原MnO時需要較高的溫度和較大的能量,因此高爐錳鐵的冶煉焦比要比生鐵冶煉高得多,焦炭負荷輕。
③由於焦比高、焦炭負荷輕,焦炭和礦石之間粒度相差大。邊緣氣流易於發展,造成煤氣流紊亂,易產生偏行管道。
④錳鐵高爐煤氣量大,發熱值高,造成爐頂溫度高,煤氣含塵量大,淨化困難。
⑤爐襯侵蝕快,爐底易堆積,使得爐襯壽命低於生鐵高爐。
以上特點決定了錳鐵高爐的操作制度有別於生鐵高爐而具有自身的特點。
裝料制度
高爐錳鐵冶煉中原料、燃料及熔劑的裝入方法直接影響高爐斷面料層分布及上升煤氣流的分布,高爐裝料制度包括料線、料批、裝料順序和布料器工作制度。
(1)料線,即大鐘下降後的下沿至料面距離,根據錳礦粒度小、密度大、滾動性差,焦炭粒度大、滾動性好的特點,錳鐵高爐的料線選在碰焦點以下,通過反彈布料,使礦石布到邊緣,焦炭布到中心,有利於中心煤氣流的發展。
(2)批重,指每一批料礦石重量。小料批加重邊緣,大料批發展邊緣。根據錳鐵高爐的冶煉特點,一般採用小料批加重邊緣。
(3)裝料順序,指一批料中礦石、焦炭、熔劑裝入料斗的順序。礦石先裝為正裝(加重邊緣),焦炭先裝為倒裝(發展邊緣)。此外還有分裝、半正裝、半倒裝等。
(4)布料器工作制度,採用布料器是使爐料在高爐斷面分布均勻的一項措施,它還可用來糾正爐料下降和煤氣上升的不均勻。錳鐵高爐通常採用六點式布料器布料,即每批料旋轉60度。
生產實踐證明:錳鐵高爐採用深料線、較小料批、正裝或正分裝為主的裝料制度有利於爐況順行。
送風制度
錳鐵高爐的送風制度直接影響煤氣的初始分布及爐況。送風制度的確定體現為鼓風動能,即風壓、風量、風溫及風口尺寸等參數的選擇。
在原料強度好、粒度均勻且粉末少的情況下,可採用大風量及較小風速(大風口)。反之則採用小風量、較大風速(小風口)。高爐容積與鼓風動能成正比。即高爐容積越大、鼓風動能也越大。冶煉產品含Mn量越高,爐缸越易堆積,為此需要的鼓風動能也越大。
在高爐錳鐵冶煉中,為保爐缸活躍,要採取措施吹透中心。除力爭全風操作外,還應保持較高風速和較大的鼓風動能,以及調節風口長度和角度來實現這一目的。
熱制度
高爐錳鐵冶煉的熱制度是指冶煉中爐溫水平及維持手段。爐溫水平的確定應建立在保證錳的還原率及有利於降低焦比的基礎上。
爐溫的高低主要取決於焦炭負荷、風溫、煤氣熱能和化學能的利用情況。
焦炭負荷與礦石中的錳、鐵含量,冶煉中的渣量,熔劑消耗量以及風溫、高爐容積和工作狀態有關。在以上條件較穩定的前提下,應保持較合適而穩定的焦炭負荷。當以上條件變化時應根據變化相應調整焦炭負荷,以保證爐溫的穩定。
在高爐錳鐵冶煉中,熱風帶入的熱量是高爐熱量的主要來源之一。提高風溫可降低焦比,減少煤氣生成量,有利爐況順行。因此在設備條件許可下應儘量提高風溫。
造渣制度
高爐錳鐵造渣制度與原料條件有關。當錳礦品位高,Mn,Fe質量比高時,可採用無熔劑或少熔劑法生產高碳錳鐵,此時爐渣為低磷、低鐵富錳渣,可作為矽錳合金的原料。我國錳礦石含錳品位低,國內以熔劑法生產高碳錳鐵,以鹼性渣操作為主。生產實踐表明:渣中MgO含量由5%提高到8%時,渣中MnO由8%降至5%。為此,在高爐錳鐵冶煉中合適的爐渣成分為:CaO為30%~44%;SiO2為25%~30%;MgO為8%~12%;Al2O3為10%~15%,MnO為3%~7%。