鋼的脫氧反應
正文
減少鋼液中溶解氧量的化學反應。脫氧是保證鋼錠和鋼材質量的一項重要操作。煉鋼是一個氧化精煉過程,鋼液中不可避免地溶有一定量的氧。1600℃時,氧在鋼液中的溶解度可達 0.23%(見Fe-O 狀態圖)。氧化精煉末期,鋼液含氧量依煉鋼方法、鋼種規格而有所不同,一般約在0.02~0.08%範圍內,而氧在固態鐵中的溶解度卻很低(例如在δ-Fe中溶解度最大為 0.0082%)。在鋼液凝固過程中,氧以FeO形態析出,分布在晶界上,降低鋼的塑性。晶界上的FeO和 FeS還會形成低熔點(910℃)物質,使鋼在熱加工時發生熱脆。未充分脫氧的鋼液在鋼錠模內凝固過程中,由於固體鋼中溶解的氧很低,氧在鋼液內逐漸富集,超過碳氧平衡值的過剩氧將與碳繼續發生反應,生成CO氣體,使鋼錠內部產生氣泡,嚴重時會發生“冒漲”現象。因此,在煉鋼的最後階段必須脫氧。方法主要有三種:沉澱脫氧,擴散脫氧和真空脫氧。沉澱脫氧 向鋼液中加入對氧親合力比鐵大的元素(脫氧劑),使之與鋼中溶解的氧結合成不溶於鋼液的氧化物或複合氧化物而析出,其反應是:
(1)
沉澱脫氧產物如不及時排除,就會成為固態鋼中的非金屬夾雜物,影響鋼的質量。脫氧產物的密度(一般為3~5克/厘米3)比鋼液(7.1克/厘米3)小,可以上浮排除,其上浮速度v(厘米/秒)可按斯托克斯(Stokes)公式近似求得:
(2)
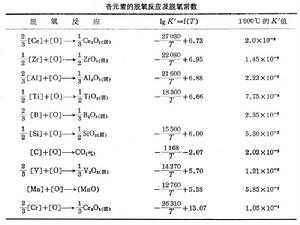
擴散脫氧 在電弧爐煉鋼還原期,渣中含FeO很少,鋼液中的氧會按下列反應進入渣中:
以上兩種脫氧方法各有利弊,為充分發揮它們各自的優點,還廣泛採用沉澱與擴散綜合脫氧。即在電爐還原期之初,先用沉澱脫氧迅速減少鋼液中氧含量。當稀薄渣形成後,再用擴散脫氧。在擴散脫氧期間,沉澱脫氧產物有充分時間上浮,最後在還原期末再插鋁脫氧。這樣既可提高鋼的質量,又縮短了冶煉時間。
真空脫氧 是在低壓下使鋼液中碳氧反應更加完全而進行的脫氧反應:
爐外精煉 用氬氣吹入鋼包使鋼液脫氧、脫碳、除氣及去夾雜物的工藝,是由於氬氣泡中CO分壓極低,促使碳氧反應進行得更完全,因而也能起到與真空脫氧相類似的作用(見真空冶金)。
參考書目
C.Bodsworth & H.B.Bell,Physical Chemistry of Iron and Steel Manufacture,2nd ed.,Longman,London,1972.