簡介
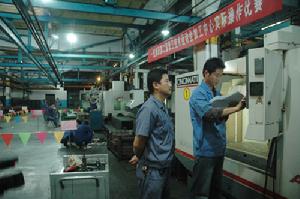
機械加工是一種用加工機械對工件的外形尺寸或性能進行改變的過程。按被加工的工件處於的溫度狀態﹐分為冷加工和熱加工。一般在常溫下加工,並且不引起工件的化學或物相變化﹐稱冷加工。一般在高於或低於常溫狀態的加工﹐會引起工件的化學或物相變化﹐稱熱加工。冷加工按加工方式的差別可分為切削加工和壓力加工。熱加工常見有熱處理﹐煅造﹐鑄造和焊接。 另外裝配時常常要用到冷熱處理。例如:軸承在裝配時往往將內圈放入液氮里冷卻使其尺寸收縮,將外圈適當加熱使其尺寸放大,然後再將其裝配在一起。火車的車輪外圈也是用加熱的方法將其套在基體上,冷卻時即可保證其結合的牢固性(此種方法現在不知道是否還有。
機械加工包括:雷射切割、重型加工、金屬粘結、金屬拉拔、等離子切割、精密焊接、輥軋成型、金屬板材彎曲成型、模鍛、水噴射切割、精密焊接等。
機械加工:廣意的機械加工就是凡能用機械手段製造產品的過程;狹意的是用車床、銑床、鑽床、磨床、衝壓機、壓鑄機等專用機械設備製作零件的過程。
加工工藝
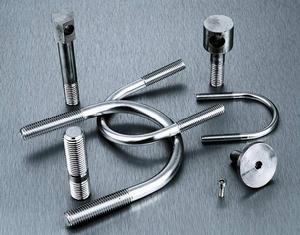
一、生產過程和工藝過程
生產過程是指從原材料(或半成品)製成產品的全部過程。對機器生產而言包括原材料的運輸和保存,生產的準備,毛坯的製造,零件的加工和熱處理,產品的裝配、及調試,油漆和包裝等內容。生產過程的內容十分廣泛,現代企業用系統工程學的原理和方法組織生產和指導生產,將生產過程看成是一個具有輸入和輸出的生產系統。能使企業的管理科學化,使企業更具應變力和競爭力。
在生產過程中,直接改變原材料(或毛坯)形狀、尺寸和性能,使之變為成品的過程,稱為工藝過程。它是生產過程的主要部分。例如毛坯的鑄造、鍛造和焊接;改變材料性能的熱處理;零件的機械加工等,都屬於工藝過程。工藝過程又是由一個或若干個順序排列的工序組成的。
工序是工藝過程的基本組成單位。所謂工序是指在一個工作地點,對一個或一組工件所連續完成的那部分工藝過程。構成一個工序的主要特點是不改變加工對象、設備和操作者,而且工序的內容是連續完成的。
二、生產類型
生產類型通常分為三類。
1.單件生產 單個地生產某個零件,很少重複地生產。
2.成批生產 成批地製造相同的零件的生產。
3.大量生產 當產品的製造數量很大,大多數工作地點經常是重複進行一種零件的某一工序的生產。
擬定零件的工藝過程時,由於零件的生產類型不同,所採用的加方法、工具機設備、工夾量具、毛坯及對工人的技術要求等,都有很大的不同。
三、加工餘量
為了加工出合格的零件,必須從毛坯上切去的那層金屬的厚度,稱為加工餘量。加工餘量又可分為工序餘量和總餘量。某工序中需要切除的那層金屬厚度,稱為該工序的加工餘量。從毛坯到成品總共需要切除的餘量,稱為總餘量,等於相應表面各工序餘量之和。
在工件上留加工餘量的目的是為了切除上一道工序所留下來的加工誤差和表面缺陷,如鑄件表面冷硬層、氣孔、夾砂層,鍛件表面的氧化皮、脫碳層、表面裂紋,切削加工後的內應力層和表面粗糙度等。從而提高工件的精度和表面粗糙度。
加工餘量的大小對加工質量和生產效率均有較大影響。加工餘量過大,不僅增加了機械加工的勞動量,降低了生產率,而且增加了材料、工具和電力消耗,提高了加工成本。若加工餘量過小,則既不能消除上道工序的各種缺陷和誤差,又不能補償本工序加工時的裝夾誤差,造成廢品。其選取原則是在保證質量的前提下,使餘量儘可能小。一般說來,越是精加工,工序餘量越小。
四、基準
機械零件是由若干個表面組成的,研究零件表面的相對關係,必須確定一個基準,基準是零件上用來確定其它點、線、面的位置所依據的點、線、面。根據基準的不同功能,基準可分為設計基準和工藝基準兩類。
1.設計基準
在零件圖上用以確定其它點、線、面位置的基準,稱為設計基準。
2.工藝基準
零件在加工和裝配過程中所使用的基準,稱為工藝基準。工藝基準按用途不同又分為裝配基準、測量基準及定位基準。
(1)裝配基準 裝配時用以確定零件在部件或產品中的位置的基準,稱為裝配基準。
(2)測量基準 用以檢驗已加工表面的尺寸及位置的基準,稱為測量基準。
(3)定位基準 加工時工件定位所用的基準,稱為定位基準。作為定位基準的表面(或線、點),在第一道工序中只能選擇未加工的毛坯表面,這種定位表面稱粗基準.在以後的各個工序中就可採用已加工表面作為定位基準,這種定位表面稱精基準。
五、擬定工藝路線的一般原則
機械加工工藝規程的制定,大體可分為兩個步驟。首先是擬定零件加工的工藝路線,然後再確定每一道工序的工序尺寸、所用設備和工藝裝備以及切削規範、工時定額等。這兩個步驟是互相聯繫的,應進行綜合分析。
工藝路線的擬定是制定工藝過程的總體布局,主要任務是選擇各個表面的加工方法,確定各個表面的加工順序,以及整個工藝過程中工序數目的多少等。
擬定工藝路線的一般原則如下。
1、先加工基準面
零件在加工過程中,作為定位基準的表面應首先加工出來,以便儘快為後續工序的加工提供精基準。稱為“基準先行”。
2、劃分加工階段
加工質量要求高的表面,都劃分加工階段,一般可分為粗加工、半精加工和精加工三個階段。主要是為了保證加工質量;有利於合理使用設備;便於安排熱處理工序;以及便於時發現毛坯缺陷等。
3、先孔後面
對於箱體、支架和連桿等零件應先加工平面後加工孔。這樣就可以以平面定位加工孔,保證平面和孔的位置精度,而且對平面上的孔的加工帶來方便。
4、主要表面的光整加工(如研磨、珩磨、精磨等),應放在工藝路線最後階段進行,以免光整加工的表面,由於工序間的轉運和安裝而受到損傷。
上述為工序安排的一般情況。有些具體情況可按下列原則處理。
(1)、為了保證加工精度,粗、精加工最好分開進行。因為粗加工時,切削量大,工件所受切削力、夾緊力大,發熱量多,以及加工表面有較顯著的加工硬化現象,工件內部存在著較大的內應力,如果粗、粗加工連續進行,則精加工後的零件精度會因為應力的重新分布而很快喪失。對於某些加工精度要求高的零件。在粗加工之後和精加工之前,還應安排低溫退火或時效處理工序來消除內應力。
(2)、合理地選用設備。粗加工主要是切掉大部分加工餘量,並不要求有較高的加工精度,所以粗加工應在功率較大、精度不太高的工具機上進行,精加工工序則要求用較高精度的工具機加工。粗、精加工分別在不同的工具機上加工,既能充分發揮設備能力,又能延長精密工具機的使用壽命。
(3)、在機械加工工藝路線中,常安排有熱處理工序。熱處理工序位置的安排如下:為改善金屬的切削加工性能,如退火、正火、調質等,一般安排在機械加工前進行。為消除內應力,如時效處理、調質處理等,一般安排在粗加工之後,精加工之前進行。為了提高零件的機械性能,如滲碳、淬火、回火等,一般安排在機械加工之後進行。
適用範圍
1、 各種金屬零
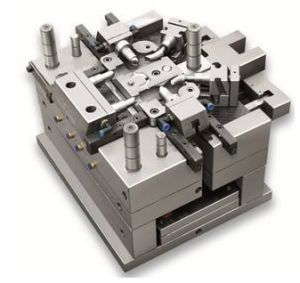
2、 鈑金、箱體、金屬結構;
3、 鈦合金、高溫合金、非金屬等機械加工;
4、 風洞燃燒室設計製造;
5、 非標設備設計製造。
6、 模具設計製造。
常用器械
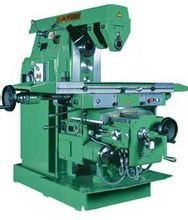
加工需要的機械由數顯銑床、數顯成型磨床、數顯車床、電火花機、萬能磨床、加工中心、雷射焊接、中走 絲、快走絲、慢走絲、外圓磨床、內圓磨床、精密車床等,可進行精密零件的車、銑、刨、磨等加工, 此類機械擅長精密零件的車、銑、刨、磨等加工,可以加工各種不規則形狀零件,加工精度可達2μm。
發展現狀
隨著現代機械加工的快速發展,機械加工技術快速發展,慢慢的湧現出了許多先進的機械加工技術方法,比如微型機械加工技術、快速成形技術、精密超精密加工技術等。
微型機械加工技術
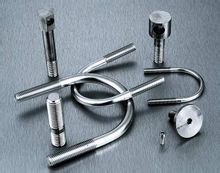
隨著微/納米科學與技術(Micro/Nano Science and Technology)的發展,以本身形狀尺寸微小或操作尺度極小為特徵的微機械已成為人們認識和改造微觀世界的一種高新科技。微機械由於具有能夠在狹小空間內進行作業,而又不擾亂工作環境和對象的特點,在航空航天、精密儀器、生物醫療等領域有著廣闊的套用潛力,並成為納米技術研究的重要手段,因而受到高度重視並被列為21世紀關鍵技術之首。
快速成形機械加工技術
快速成形技術是20世紀發展起來的,可根據CAD模型快速製造出樣件或者零件。它是一種材料累加加工製造方法,即通過材料的有序累加而完成三維成形的。快速成形技術集成了CNC技術、材料技術、雷射技術以及CAD技術等現代的科技成果,是現代先進機械加工技術的重要組成部分。
精密超精密機械加工技術
精密和超精密加工時現代機械加工製造技術的一個重要組成部分,是衡量一個國家高科技製造業水平高低的重要指標之一。20世紀60年代以來,隨著計算機及信息技術的發展,對製造技術提出了更高的要求,不僅要求獲得極高的尺寸、形位精度,而且要求獲得極高的表面質量。正是在這樣的市場需求下,超精密加工技術得到了迅速的發展,各種工藝、新方法不斷湧現。
政策支持
國務院通過的《裝備製造業調整與振興規劃》,提出依託高速鐵路、煤礦與金屬礦採掘、基礎設施、科技重大專項等十大領域重點工程,振興裝備製造業;抓住九大產業重點項目,實施裝備自主化;提升四大配套產品製造水平。政策措施包括加強投資項目的設備採購管理、鼓勵使用國產首台套裝備、推進企業兼併重組等。上述領域涉及了經濟建設中的關鍵部門,也是我國機械行業發展中亟待突破的領域,尤其是高檔數控工具機和礦用機械長期以來一直是我國製造領域的薄弱環節,與國外先進水平有明顯的差距。
安全知識
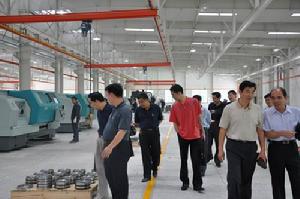
一、 加工畸形和偏心零件要注意哪些安全事項?
加工畸形和偏心零件,一般採用花盤裝卡對工件進行固定。因此首先要注意裝卡牢靠。卡爪、壓板不要伸出花盤直徑以外,最好加裝護罩。其次要注意偏心零件的配重。配重要適當。配重的內孔直徑與螺桿直徑間隙要小。工具機鏇轉速度不要太高,以防鏇轉時離心力作用將配重外移,與工具機導軌相碰,折斷螺絲,打傷操作者。
二、 工具機設備操縱系統應滿足哪些安全要求?
1、 便於操作,減少來回走動,避免不必要的彎腰、踮腳動作。
2、 定位準確可靠,防止稍有震動便產生誤動作。
3、 工具機設備操作件運動方向和被操作部件運動方向要符合規定,並有簡易符號標誌。
4、 安設必要的互鎖機構,防止操作件產生不協調動作,以及多人操作時不協調出現的事故。
5、 手柄、手輪、按鈕的結構和排列位置要符合規定。啟動按鈕應安設在機殼內或裝設防止意外觸動的護環。安裝在軸桿上的手輪、手柄,在自動進刀時,會隨軸轉動傷人,因此應安裝自動脫出裝置。
三、 預防切屑對人體傷害的安全措施有哪些?
1、 根據被加工材料性質,改變刀具角度或增加斷屑裝置,選用合適的進給量,將帶狀切屑斷成小段卷狀或塊狀切屑,加以清除。
2、 在刀具上安裝排屑器,或在工具機上安裝護罩、檔板,控制切屑流向,不致傷人。
3、 高速切削生鐵、銅、鋁材料,除在工具機上安裝護罩、檔板以外,操作者應配備防護眼鏡。
4、 使用工具及時清除工具機上和工作場所的鐵屑,防止傷手、腳,切忌用手去扒鐵屑。
四、 工具機設備配置哪四種安全裝置其作用是什麼?
1、 防護裝置。用來使操作者和機器設備的轉動部分、帶電部分及加工過程中產生的有害物加以隔離。如皮帶罩、齒輪罩、電氣罩、鐵屑檔板、防護欄桿等。
2、 保險裝置。用來提高工具機設備工作可靠性。當某一零部件發生故障或出現超載時,保險裝置動作,迅速停止設備工作或轉入空載運行。如行程限位器、摩擦離合器等。
3、 聯鎖裝置。用於控制工具機設備操作順序,避免動作不協調而發生事故。如車床絲桿與光桿不能同時動作等,都要安裝電氣或機械的聯鎖裝置加以控制。
4、 信號裝置。用來指示機器設備運行情況,或者在機器設備運轉失常時,發出顏色、音響等信號,提醒操作者採取緊急措施加以處理。如指示燈、蜂鳴器、電鈴等。
五、 操作工具機要注意哪些安全事項?
1、 工作前穿好工作服,紮好袖口,戴好工作帽。嚴禁戴手套操作。
2、 認真檢查設備各部分及防護罩、限位塊、保險螺釘等安全裝置是否完好有效。
3、 設備必須牢固有效地接地接零,局部照明燈為36v電壓。
4、 工作前,在各油孔內加油潤滑,空轉試車確認無故障方可工作。
5、 工具機運轉時,不準用手檢查工件表面光潔度和測量工件尺寸。
6、 裝卡零部件時,板手要符合要求,不得加套管以增大力矩去擰緊螺母。
7、 不準用手纏繞砂布去打磨轉動零件。
8、 對高速轉動的偏心工件或畸形工件要加配重,並作平衡試驗,突出部分加護罩。
9、 更換齒輪、裝卸夾具必須切斷電源,停穩後才能進行
10、自動走刀前,調整和緊固行程限位器,並撥出進給手槍。
11、下班時,要將各種走刀手柄放在空檔設定,拉下電門,並擦試工具機打掃衛生。
擬定工藝路線的一般原則
機械加工工藝規程的制定,大體可分為兩個步驟。首先是擬定零件加工的工藝路線,然後再確定每一道工序的工序尺寸、所用設備和工藝裝備以及切削規範、工時定額等。這兩個步驟是互相聯繫的,應進行綜合分析。
工藝路線的擬定是制定工藝過程的總體布局,主要任務是選擇各個表面的加工方法,確定各個表面的加工順序,以及整個工藝過程中工序數目的多少等。
擬定工藝路線的一般原則
1、先加工基準面
零件在加工過程中,作為定位基準的表面應首先加工出來,以便儘快為後續工序的加工提供精基準。稱為“基準先行”。
2、劃分加工階段
加工質量要求高的表面,都劃分加工階段,一般可分為粗加工、半精加工和精加工三個階段。主要是為了保證加工質量;有利於合理使用設備;便於安排熱處理工序;以及便於時發現毛坯缺陷等。
3、先孔後面
對於箱體、支架和連桿等零件應先加工平面後加工孔。這樣就可以以平面定位加工孔,保證平面和孔的位置精度,而且對平面上的孔的加工帶來方便。
4、主要表面的光整加工(如研磨、珩磨、精磨等),應放在工藝路線最後階段進行,以免光整加工的表面,由於工序間的轉運和安裝而受到損傷。
上述為工序安排的一般情況。有些具體情況可按下列原則處理。
(1)、為了保證加工精度,粗、精加工最好分開進行。因為粗加工時,切削量大,工件所受切削力、夾緊力大,發熱量多,以及加工表面有較顯著的加工硬化現象,工件內部存在著較大的內應力,如果粗、粗加工連續進行,則精加工後的零件精度會因為應力的重新分布而很快喪失。對於某些加工精度要求高的零件。在粗加工之後和精加工之前,還應安排低溫退火或時效處理工序來消除內應力。
(2)、合理地選用設備。粗加工主要是切掉大部分加工餘量,並不要求有較高的加工精度,所以粗加工應在功率較大、精度不太高的工具機上進行,精加工工序則要求用較高精度的工具機加工。粗、精加工分別在不同的工具機上加工,既能充分發揮設備能力,又能延長精密工具機的使用壽命。
(3)、在機械加工工藝路線中,常安排有熱處理工序。熱處理工序位置的安排如下:為改善金屬的切削加工性能,如退火、正火、調質等,一般安排在機械加工前進行。為消除內應力,如時效處理、調質處理等,一般安排在粗加工之後,精加工之前進行。為了提高零件的機械性能,如滲碳、淬火、回火等,一般安排在機械加工之後進行。如熱處理後有較大的變形,還須安排最終加工工序
相關條目
工具機 機械 加工切削加工 電加工 五金工具 鑄造 鈑金 注塑 焊接 衝壓 模具加工 雷射加工